Clean Rooms
Clean rooms are specially designed enclosures that support sensitive research, manufacturing, and testing processes by minimizing airborne contaminants such as dust, moisture, and microbes. These controlled environments are essential in industries where even microscopic particles can compromise product quality or research integrity.
The cleanliness of a clean room is measured by the concentration of air pollutants in a given air sample. While some clean rooms require complete sterility, most focus on reducing dust particles to acceptable levels. Even the smallest disturbances, such as foot traffic, can stir up microscopic dust, which is measured in microns—each equal to one-millionth of a meter.
In industries like medical research and pharmaceuticals, sterility is a critical requirement. Procedures such as pharmacological studies, infectious disease testing, and other high-precision medical applications demand environments free of microbial contamination. Clean room classification is determined by the number of particles over 0.5 micrometers in size, ensuring compliance with strict industry standards for hygiene and precision.
Clean Room Applications
Clean room ceiling manufacturers design controlled environments where factors such as airborne dust, temperature fluctuations, air pressure, and moisture can be precisely regulated. These ceilings are integral to maintaining a stable workspace, ensuring that sensitive operations meet strict cleanliness and environmental standards.
Clean rooms come in various configurations, offering flexibility based on industry needs. Ranging from highly controlled Class 100 clean rooms to more adaptable portable and modular clean rooms, each setup is classified by its ability to eliminate contaminants. As the demand for clean room environments has grown, regulatory bodies have established clear classifications to define acceptable contamination levels.
For instance, Class 1,000 clean rooms require equipment that does not release fibrous contaminants, making them suitable for precision manufacturing. Class 10,000 clean rooms, while still controlled, allow for more flexibility, often incorporating soft walls and serving applications with less stringent requirements.
Clean rooms play a vital role in industries such as aerospace, semiconductors, pharmaceutical product manufacturing, medical device manufacturing, military contract manufacturing, nanotechnology, and scientific research. They are essential for ensuring product quality and compliance in highly sensitive applications.
Examples of clean room applications include:
- Pharmaceutical packaging rooms for sterile product handling
- Powder coating and painting enclosures to maintain finish consistency
- Plant cultivation rooms for controlled agricultural research
- Oil mist enclosures to prevent contamination in machining processes
- IV preparation rooms for sterile medical compounding
For businesses seeking clean room solutions, IQS Directory provides a comprehensive list of reputable suppliers offering tailored designs for a wide range of industry applications.
The History of Clean Rooms
The modern clean room was first developed in 1960 by American physicist Willis Whitfield while working at Sandia National Laboratories. His innovation was driven by the growing demands of the aerospace and microtechnology industries, which required highly controlled environments to prevent airborne contamination from disrupting production and research.
Before Whitfield’s invention, early clean room designs struggled with unpredictable airflow and insufficient particle control, making them unreliable for emerging high-tech fields such as biotechnology and medical research. As these disciplines advanced—and as products and research subjects became increasingly microscopic—contaminants posed a greater risk to precision work.
Whitfield’s clean room concept revolutionized contamination control by introducing constant, highly filtered airflows that flushed out impurities and maintained a stable environment. This breakthrough allowed industries to rigidly regulate air quality, temperature, and humidity, ensuring the success of sensitive manufacturing and research processes. Today, his innovation remains the foundation for modern clean room technology across a wide range of industries.
Clean Room Design
Clean rooms vary widely in size and configuration, depending on their intended application. Some clean rooms, especially those used in microelectronics, pharmaceuticals, and circuit manufacturing, can be as vast as warehouses, housing entire production facilities across multiple floors. These large-scale environments are often referred to as "ballrooms" due to their expansive, open-floor design.
At the other end of the spectrum, clean rooms can be compact enough to fit within a household oven, making them ideal for small-scale medical testing, precision manufacturing, specialized repairs, and controlled scientific experiments.
Permanent clean rooms are typically integrated into the infrastructure of the buildings they occupy, with environmental control systems built directly into the structure. Some of these rooms are enclosed by glass or clear plastic walls, providing a transparent barrier while maintaining controlled conditions.
For applications requiring lower levels of decontamination, soft-wall clean rooms—made from flexible acrylic or plastic—offer a cost-effective and adaptable alternative. These are often sourced from acrylic fabrication suppliers and plastic manufacturing and are particularly useful for industries with evolving clean room requirements.
Regardless of size or configuration, all clean room materials must be non-fibrous, non-static generating, and non-corrosive to prevent contamination. Every component, from walls to flooring, must be carefully selected to avoid releasing particles into the air. Even durable materials like stainless steel can corrode when exposed to certain disinfectants, such as bleach, which is sometimes used for sterilization. As a result, material selection is a critical factor in clean room construction, ensuring long-term performance and compliance with strict cleanliness standards.
Clean Room Features
Clean rooms maintain their controlled environments by filtering incoming air to remove contaminants such as dust and microorganisms. This is achieved through air filtration systems and high-efficiency fans that ensure a continuous flow of purified air. To maintain cleanliness, air is constantly recirculated using either HEPA Air Filter or a ULPA filter, both of which capture microscopic particles to prevent contamination.
A clean room facility relies on a combination of preventative devices and specialized equipment to maintain its sterile environment. These tools serve both personal protection and air purification functions. For example, airlocks at entry and exit points prevent outside contaminants from entering the space. Some clean rooms even incorporate air showers within these airlocks, where high-velocity air jets remove dust and particles from workers’ clothing before they enter the controlled area.
While features such as HEPA filters, air showers, and anti-static devices can be costly, they are essential for maintaining the integrity and performance of a clean room.
Clean rooms can be tailored to suit specific applications by incorporating features such as:
- Positive Pressure Systems – Used in environments where contamination prevention is critical, this feature ensures that if the clean room develops a leak, air flows outward rather than inward, preventing unfiltered air from entering.
- Temperature and Humidity Control – Systems can be adjusted to maintain specific climate conditions required for sensitive processes.
- Modular Room Divisions & Panels – Clean rooms can be designed with custom partitions, lighting fixtures, and furniture, allowing flexibility for different operations.
- Specialized Flooring & Anti-Static Features – To prevent static buildup, which can be harmful in electronics and semiconductor manufacturing, clean rooms can be equipped with ESD (Electrostatic Discharge) flooring and anti-static workstations.
By integrating these features, clean rooms can be fully optimized for pharmaceutical production, biotechnology, semiconductor manufacturing, aerospace engineering, and other precision-driven industries that demand strict environmental control.
Advantages of Clean Rooms
Clean rooms provide significant benefits to industries that require precision, sterility, and controlled environments.
One of the primary advantages of a clean room is its ability to protect highly sensitive technology and materials from contamination. By eliminating impurities such as dust and airborne particles, clean rooms enhance efficiency and accuracy, ensuring that delicate systems function optimally. This reduces the risk of malfunctions, breakdowns, or product defects, which can be costly in high-stakes industries like microelectronics, pharmaceuticals, and aerospace.
Another major advantage is the ability to create controlled micro-environments tailored to specific research or production needs. For example, clean rooms can be designed to prevent electrostatic discharge by maintaining low humidity or contain leaks using constant positive pressure, ensuring that any potential contamination flows outward rather than inward.
Beyond operational efficiency, clean rooms also increase profitability. By minimizing errors, defects, and downtime, businesses benefit from higher product yields, reduced waste, and improved compliance with industry regulations. This translates to substantial long-term cost savings and revenue growth, making clean rooms a crucial investment for industries that demand precision and reliability.
Clean Room Accessories
Clean rooms can be customized with a variety of accessories based on the materials being manufactured or researched. These additions help maintain strict contamination control, improve worker safety, and enhance operational efficiency.
- Furniture and Fixtures – Specialized tables, benches, pass-through cabinets, ceiling grids, and fume hoods (such as laminar flow hoods) are designed to minimize particle generation while providing necessary workspace functionality.
- Clean Room Foggers – These devices generate fog for airflow visualization in smoke studies, allowing researchers to analyze air movement patterns and turbulence to improve environmental control.
- Clean Room Suits – Workers must wear full-body protective gear, including hoods, face masks, boots, and coveralls, to prevent hair and skin particles from contaminating the environment. A single human hair is approximately 100 micrometers wide, and humans shed around 100,000 particles per minute even when standing still, making protective clothing essential.
Specialized Clean Room Equipment
Inside a clean room, only certified clean room supplies—such as buckets, mops, and cleaning tools—can be used. These items are designed to minimize particle release and comply with clean room standards. Additionally, clean room furniture is made from non-shedding, non-corrosive materials that are easy to clean and maintain, ensuring the highest level of cleanliness and contamination control.
By carefully selecting the right accessories and equipment, clean rooms can be fully optimized for precision manufacturing, scientific research, and critical medical applications, ensuring compliance with even the most stringent industry standards.
Clean Room Installation
Before installing a clean room, it is essential to double-check all dimensions to ensure a precise fit within your designated space. This applies whether you are retrofitting an existing facility or constructing a new space from the ground up. Proper planning helps avoid costly modifications and ensures a seamless installation process.
Prefabrication for Efficient Installation
The fastest and most efficient way to install a clean room is through pre-fabrication, where the manufacturer assembles as many components as possible at their facility before delivery. This approach offers several advantages:
- Faster assembly on-site, minimizing downtime
- Reduced construction debris and dust, maintaining a cleaner environment
- Fewer disruptions to ongoing operations in existing facilities
On-Site Assembly
For those who opt not to pre-fabricate, clean room installation will take longer but will still be executed with precision and attention to detail. Manufacturers will send skilled technicians to assemble the clean room on-site from disassembled components, ensuring compliance with all clean room classification standards and industry-specific requirements.
Regardless of the installation method, working with an experienced clean room manufacturer ensures a smooth process, allowing businesses to quickly begin operations in a fully functional, contamination-controlled environment.
Proper Care for Clean Rooms
Maintaining a clean room requires a combination of effective cleaning solutions and a high-efficiency air filtration system, such as HEPA filters, to remove airborne contaminants continuously. Regular cleaning ensures compliance with industry standards and extends the longevity of equipment and surfaces.
Selecting Cleaning Solutions and Supplies
When choosing a cleaning solution, ensure it is non-corrosive and non-reactive to avoid damaging surfaces or introducing contaminants. Different clean room classifications and industries require specific cleaning agents and procedures, so selecting the right products is essential.
A wide range of clean room supplies—including lint-free wipes, sterile mops, vacuum systems, and anti-static materials—are available to meet specific application needs. The type of supplies used will depend on the clean room’s classification and purpose.
Developing a Clean Room Cleaning System
To implement an effective cleaning regimen, consider the following:
- What needs to be cleaned? – Determine which surfaces, equipment, and air filtration components require routine maintenance.
- How is cleanliness measured? – Establish benchmarks based on ISO clean room classification requirements.
- What cleaning materials should be used? – Select the appropriate cleaning solutions and tools for your environment.
- When should cleaning occur? – Develop a schedule that aligns with operational needs and contamination risks.
- How often should cleaning be performed? – Cleaning frequency will depend on the level of contamination control required for your industry.
Compliance with Industry Standards
Clean room maintenance must align with ISO guidelines and industry-specific protocols. For up-to-date regulatory requirements, visit the ISO website to ensure compliance with the latest clean room cleaning standards. Proper care, maintenance, and adherence to regulations help sustain a contamination-free environment, ensuring product integrity, worker safety, and operational efficiency.
ISO Clean Room Standards
Clean rooms are classified based on their air cleanliness levels, with four major classification systems used worldwide:
- US FED STD 209E (United States Federal Standard)
- ISO 14644-1 (International Organization for Standardization)
- BS 5295 (British Standards)
- EMP EU (European Union GMP Standards)
Of these, US FED STD 209E and ISO 14644-1 are the most widely recognized standards for clean room classification.
US FED STD 209E Classification
This U.S. federal standard assigns a class number based on the number of 0.5-micrometer-sized particles per cubic foot of air. The lower the class number, the cleaner the environment:
- Class 1 – 1 particle per cubic foot
- Class 100 – 100 particles per cubic foot
- Class 10,000 – 10,000 particles per cubic foot
For reference, regular, unfiltered air would be equivalent to Class 1,000,000 under this classification.
ISO 14644-1 Clean Room Classification
ISO clean room standards classify environments based on the number of 0.1-micrometer-sized particles per cubic meter of air. There are nine ISO classes, with ISO Class 1 being the cleanest and ISO Class 9 being the least clean.
For example:
- ISO Class 3 allows a maximum of 1,000 particles per cubic meter, equivalent to a Class 1,000 clean room under US FED STD 209E.
- ISO Class 7 allows up to 352,000 particles per cubic meter, which is similar to a Class 10,000 clean room under US standards.
Key ISO Clean Room Standards
ISO provides detailed guidelines on various clean room aspects, including:
- Testing for Compliance – Ensuring clean rooms meet regulatory standards.
- Cleanliness Measurement Methods – Defining how to quantify contaminants.
- Design & Construction – Establishing best practices for building clean rooms.
- Operations & Maintenance – Ensuring optimal functionality and cleanliness.
- Molecular & Bio Contamination Control – Addressing airborne contaminants and biological threats.
British & European Standards
The British Standard (BS 5295) and European GMP (EMP EU) systems also classify clean rooms, using cubic meters instead of cubic feet for measurement. These standards are commonly followed in pharmaceutical and biotechnology industries.
Compliance & Effectiveness
To maintain compliance and operational efficiency, manufacturers should adhere to ISO and US FED STD 209E guidelines. Proper implementation of these standards ensures optimal contamination control, product safety, and regulatory compliance across various industries.
Things to Consider When It Comes to Clean Rooms
When investing in a new or refurbished clean room, several factors must be carefully evaluated to ensure it meets your operational needs. Considerations include project duration, required sterility levels, sensitivity of materials, available space, and environmental conditions (indoor vs. outdoor, new vs. existing structures).
Developing a Contamination Control Plan
To maintain a controlled environment, it’s essential to focus on clean room design, airflow management, filtration systems, and cleaning protocols.
Design and Airflow
Clean room architecture is carefully designed to optimize airflow and minimize contamination risks. The goal is to achieve a uniform laminar airflow, where air moves in parallel streams at a consistent velocity. Obstructions that disrupt airflow create turbulence, which can increase contamination risks.
ISO clean room standards emphasize the importance of an unrestricted airflow to maintain clean conditions. When designing a clean room, ensure that walls, equipment, and workstations do not interfere with air circulation.
Filtration System Manufacturers
Clean rooms rely on High-Efficiency Particulate Air (HEPA) filters, which remove airborne contaminants with 99.97% efficiency. These filters are standard in most clean room classifications, ensuring that even microscopic particles are effectively removed from the air.
For lower-grade clean rooms, such as Class 100 clean rooms, HVAC systems can sometimes be used as an alternative. However, alternative filtration options should be carefully evaluated for cost, efficiency, and installation feasibility before deviating from HEPA-based systems.
Cleaning
Maintaining strict cleanliness standards is critical for contamination control. Daily cleaning schedules, proper maintenance, and the use of certified clean room supplies help preserve air quality and sterility. When planning a clean room, establish clear protocols for cleaning procedures, material selection, and routine maintenance.
Additionally, all clean room materials and systems should be application-specific—meaning they must be compatible with your intended use and regulatory requirements.
Choosing the Right Clean Room Manufacturer
Selecting the right manufacturer is just as important as selecting the right clean room specifications. A reliable manufacturer will:
- Understand your requirements and provide tailored solutions
- Prioritize customer satisfaction and offer dedicated support
- Possess technical expertise in clean room design, airflow management, and contamination control
For businesses looking for trusted clean room manufacturers, refer to the supplier listings at the top of this page to find a manufacturer that meets your needs. Investing in the right clean room and the right partner ensures long-term efficiency, compliance, and performance in your controlled environment.
Clean Room Images and Illustrations
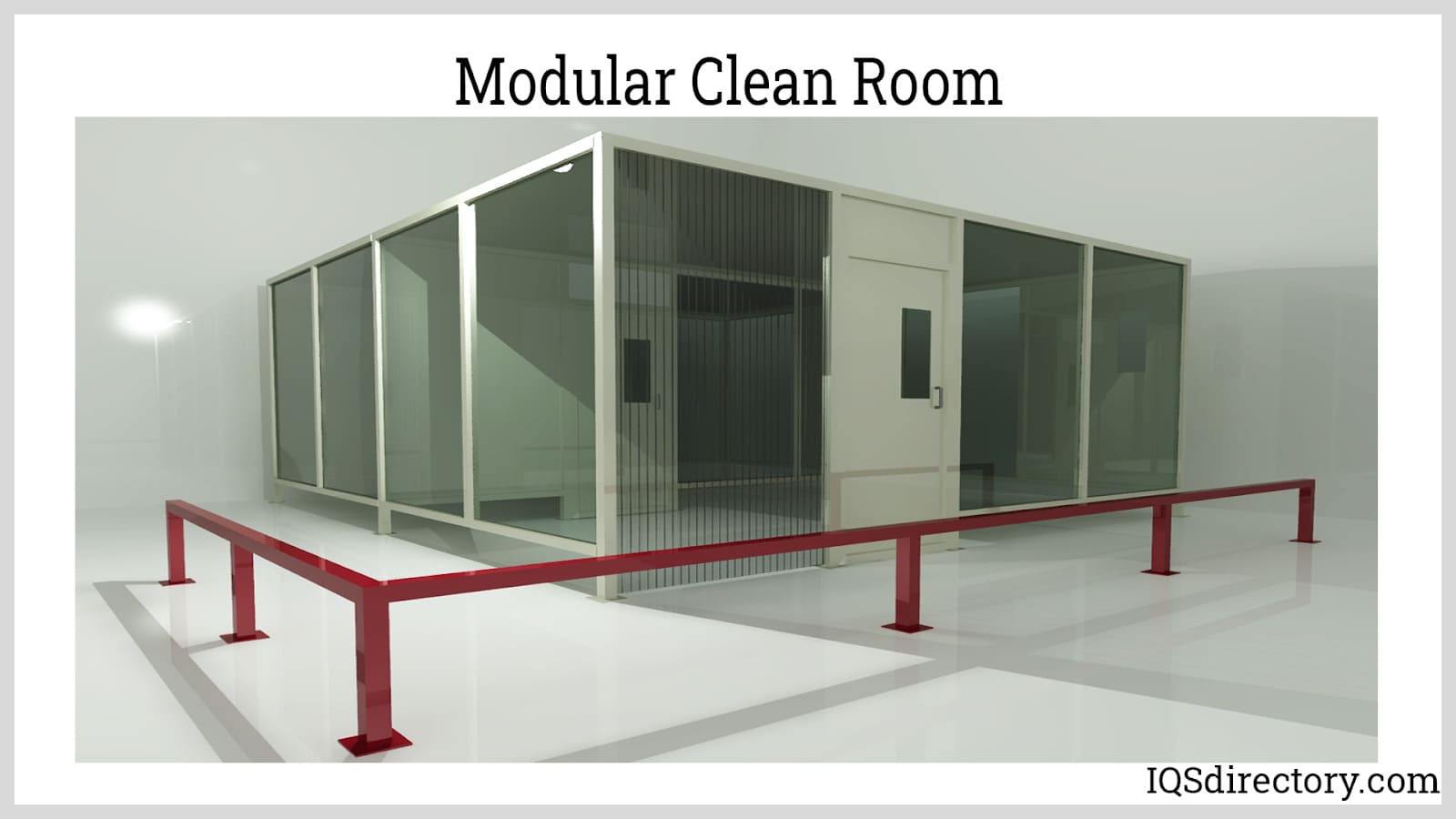
A prefabricated controlled environment that is constructed to limit the presence of sub-micron particulates.
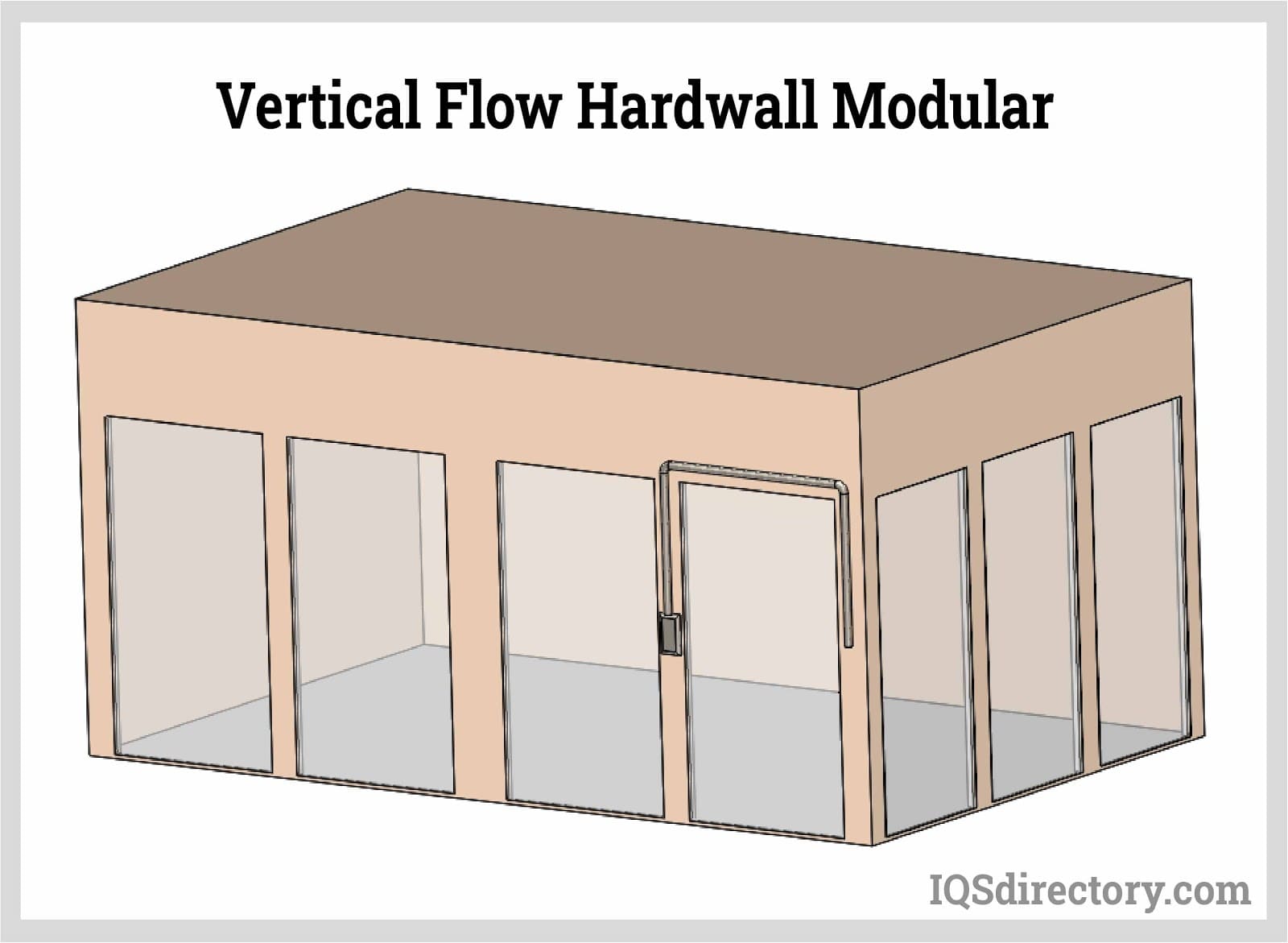
Modular cleanrooms with aluminum posts and rigid wall construction for increased air pressure.
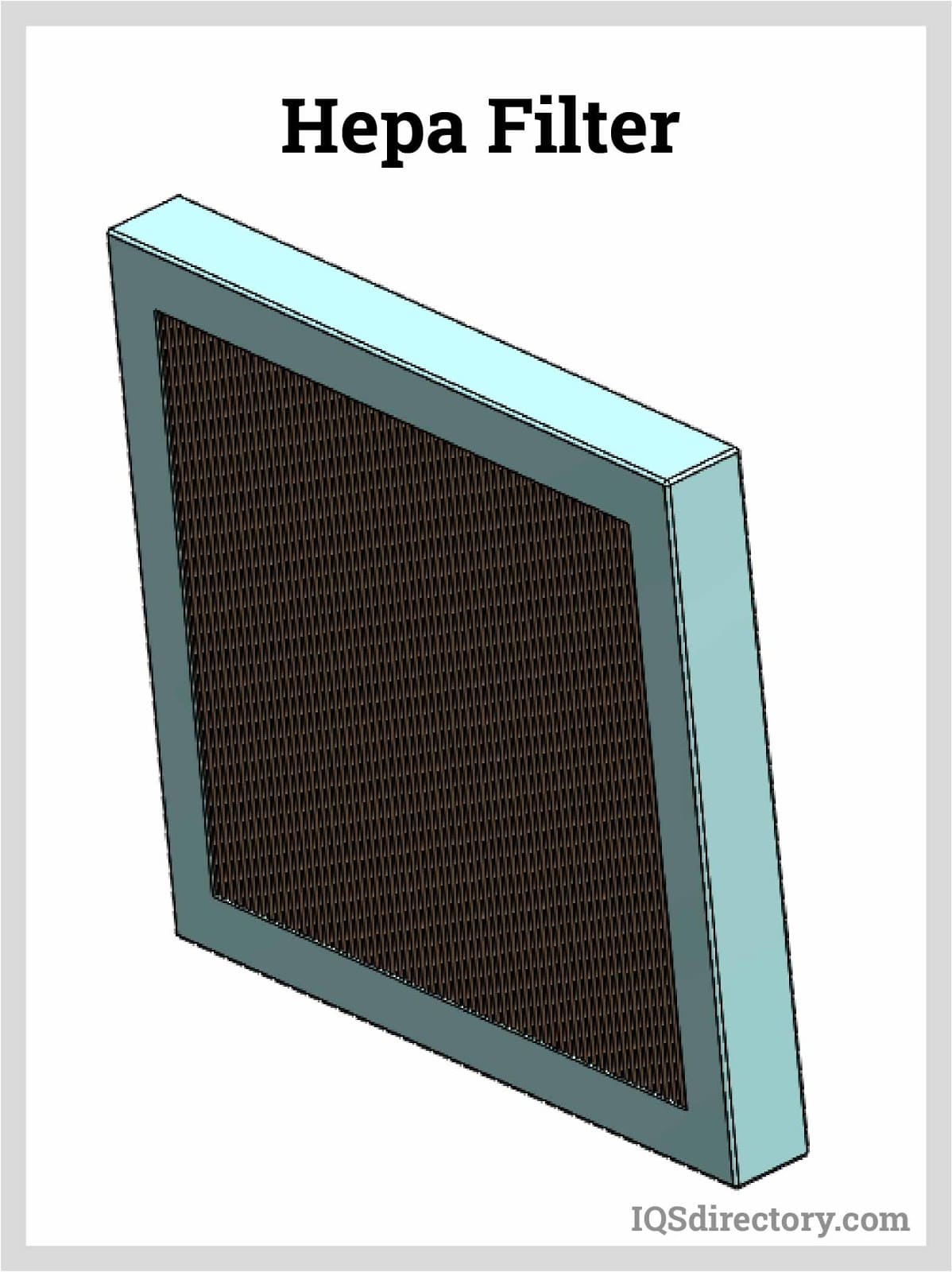
High efficiency air filters have tightly packed dense material to remove contaminants.
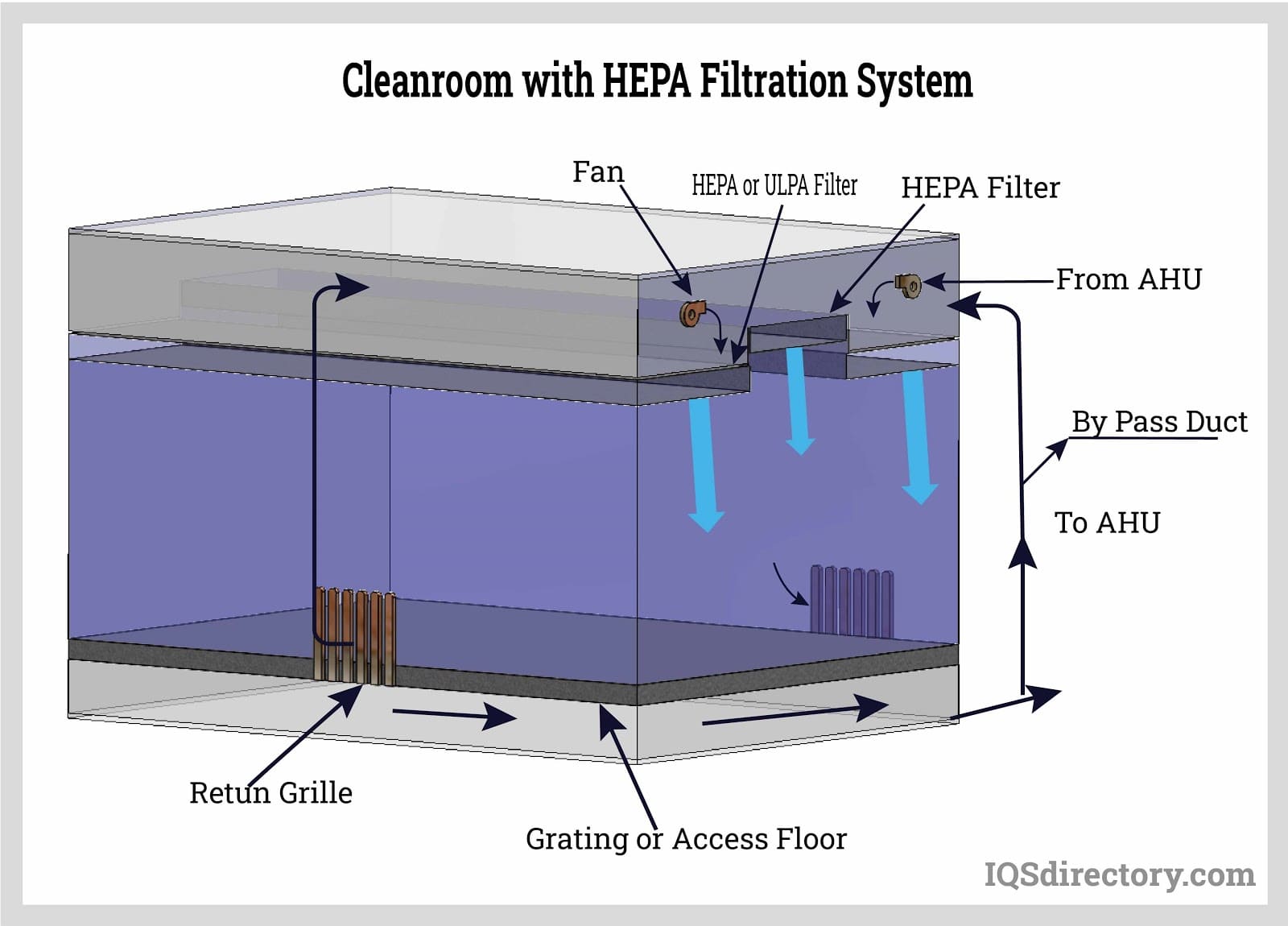
The multiple directions of the fibers of a HEPA filter are able to capture and trap microscopic particles.
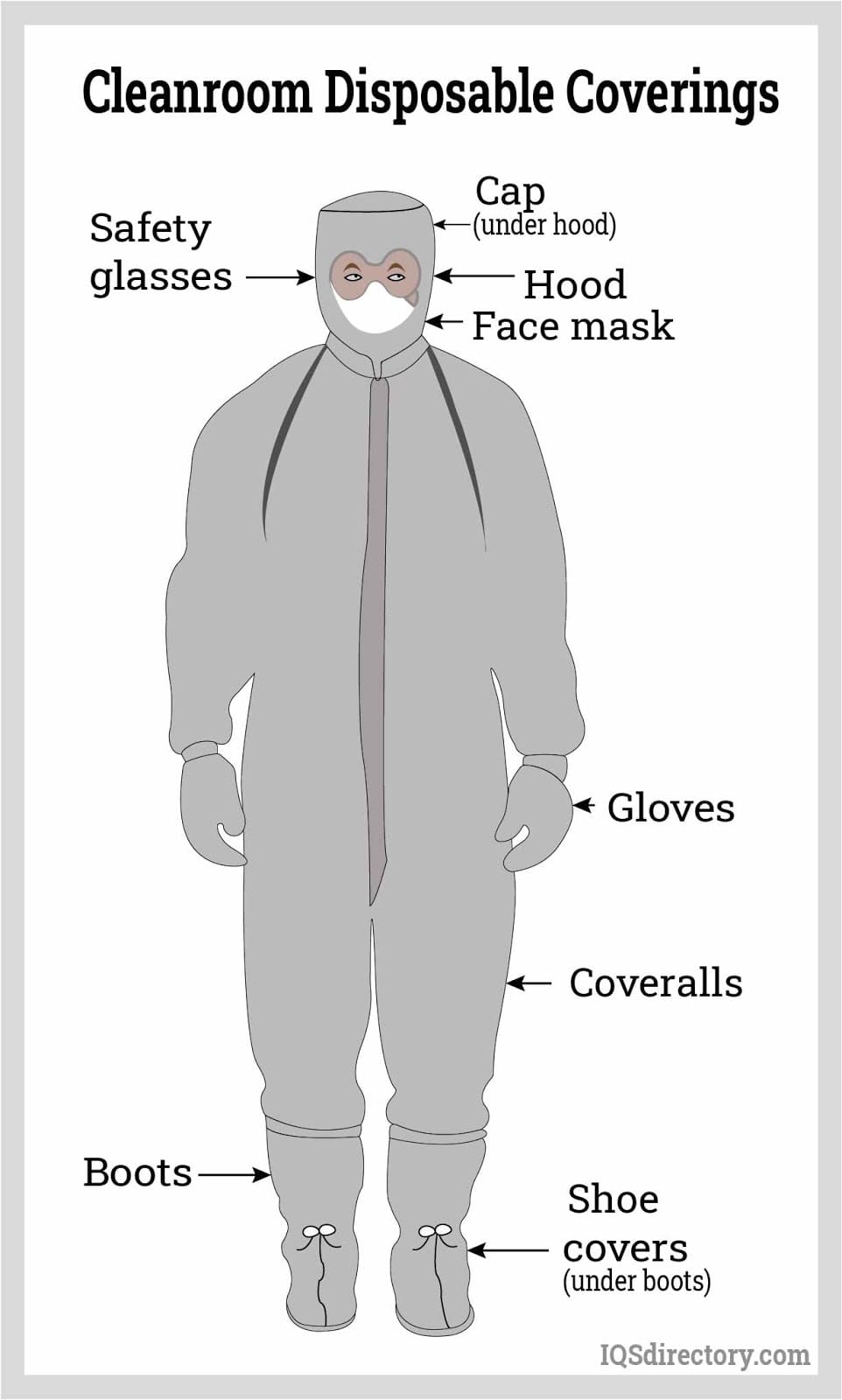
The required attire to enter a clean room.
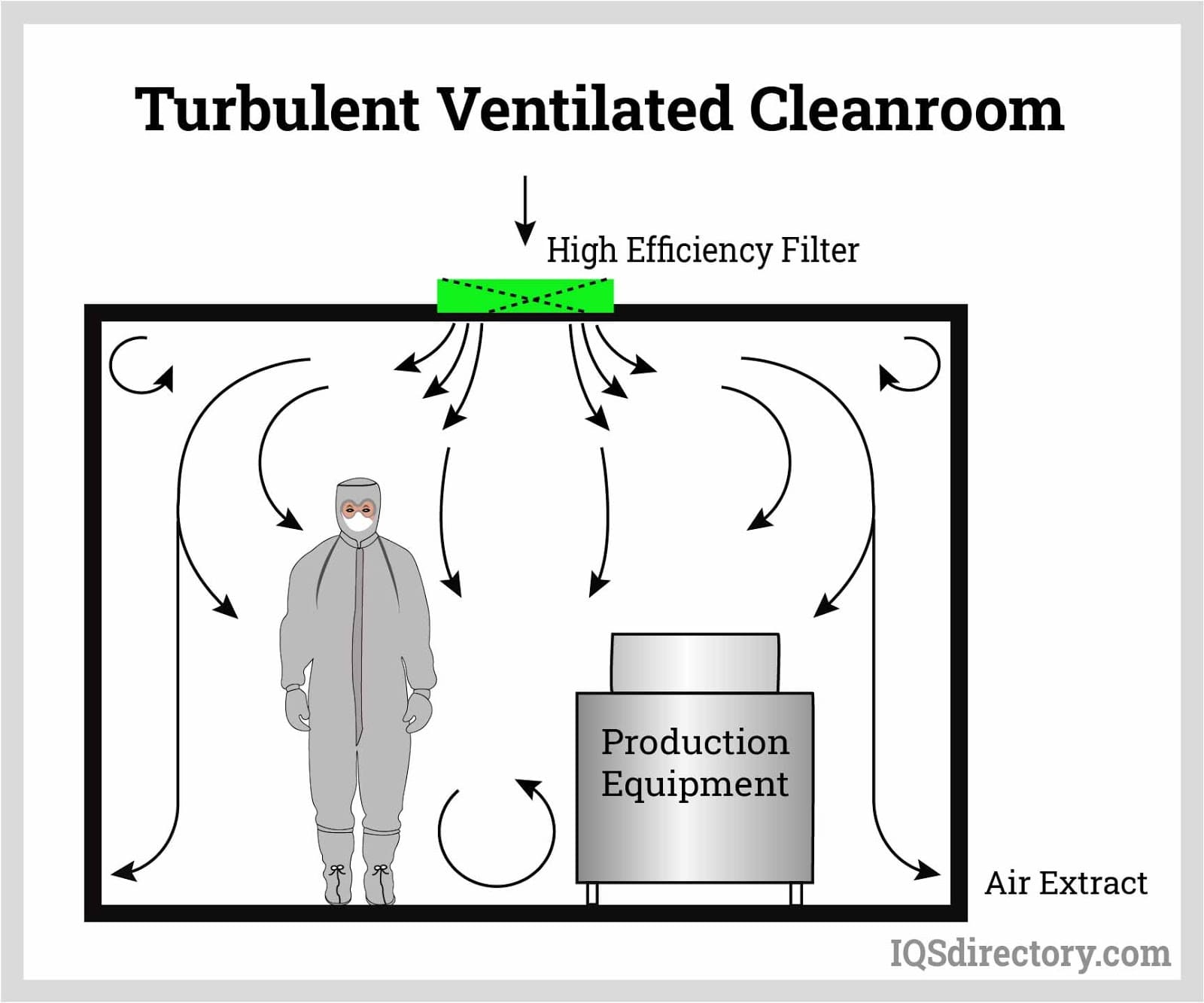
Turbulent ventilation are non-directional and unidirectional having air flow in one direction inside the clean room.
Clean Room Types
Clean rooms are classified based on function, construction, and adherence to industry standards. Different designs cater to various industries, from pharmaceuticals and electronics manufacturing to aerospace and biotechnology.
Ballrooms
Large-scale clean rooms designed to accommodate entire manufacturing floors.
Class 100 Clean Rooms
Federal Standard 209 regulated, never exceeding 100 particles per cubic foot of air.
Class 1000 Clean Rooms
Limited to 1,000 particles per cubic foot.
Class 10000 Clean Rooms
Limited to 10,000 particles per cubic foot.
Clean Room Equipment
Specialized tools, furniture, storage systems, and work surfaces made for clean room use.
Clean Room Systems
The complete set of components required for a fully functional clean room.
Clean Room Construction
Custom or pre-designed clean rooms built to meet industry-specific standards.
Clean Room Design
Includes conventional, portable, hard wall modular, and soft wall modular clean rooms.
Clean Room Supplies
Products essential for maintaining a sterile environment, such as anti-static garments, cleaning tools, and filters.
Clean Rooms
Controlled environments where air content, temperature, humidity, and pressure are strictly regulated.
Conventional Clean Rooms
Permanent and most commonly used in industrial settings.
Laminar Flow Clean Rooms
Feature filtration systems that regulate airflow and velocity, preventing airborne contaminants from coming into contact with sensitive materials.
Micro Environments
Small, highly controlled areas used for semiconductor fabrication or delicate manufacturing, focusing contamination control directly around the workpiece.
Mini Environments
Localized clean areas built around specific tools or components to prevent atmospheric exposure.
Modular Clean Rooms
Assembled on-site using pre-cut components such as walls and ceiling grids, providing flexibility in design.
Portable Clean Rooms
Self-contained, transportable clean rooms ideal for applications requiring mobility.
Softwall Clean Rooms
Constructed with fabric walls, either tightly stretched over a frame or made from free-hanging fabric strips, offering a cost-effective solution for applications with lower decontamination requirements.
Each clean room type serves a unique purpose, and selecting the right configuration depends on industry needs, contamination control requirements, and operational flexibility.
Clean Room Terms
Air Lock
A buffer room between a clean room and external areas, reducing contamination during material transfers.
Air Shower
A small chamber where high-velocity air jets remove contaminants from personnel before they enter the clean room.
Airborne Particulate Cleanliness Class Number
Indicates the number of 0.5-micron or larger particles per cubic foot of air; a lower class number signifies higher air purity.
Ceiling Grid System
The framework that holds lighting and filtration units in place
Clean Room Construction
Custom or pre-designed clean rooms that fit industry-specific standards and come in many different forms.
Clean Room Equipment
Includes furniture, storage, tools, and machinery specifically designed for use in controlled environments.
Clean Room Partitions
Internal walls that divide clean rooms into multiple classified areas.
Clean Room Pass Thrus
Small, enclosed transfer windows that allow materials to move in and out without human entry, reducing contamination risks.
Clean Room Suits
Full-body protective garments made from non-linting, anti-static fabric to prevent contamination.
Clean Room Tables
Work tables made from low-particulate materials, with either solid or perforated surfaces.
Contamination
Unwanted particles, microbes, or chemicals that compromise clean room air purity.
Electrostatic Discharge (ESD)
A static electricity shock that can damage semiconductor components.
Equipment Layout
The detailed design and arrangement of clean room furniture, machines, and workspaces to maintain optimal efficiency and airflow.
Federal Standard 209E
U.S. regulation outlining air cleanliness classifications for clean rooms.
Filter Module
A unit containing HEPA or ULPA filters, typically installed in ceilings or walls.
HEPA (High Efficiency Particulate Air) Filter
Captures 99.97% of particles at least 0.3 microns in size.
HVAC (Heating, Ventilation, and Air Conditioning) Systems
Regulate temperature, humidity, and air circulation in a clean room.
Laminar Flow
A uniform airflow pattern that moves at a constant speed and direction, minimizing turbulence and contamination.
Micron
Measurement unit equivalent to one-millionth of a meter.
Microbes
Microscopic living organisms, such as bacteria or fungi, that can be shed from human skin.
Particle Size
The measurement of a particle’s dimensions in microns.
Particle
Any solid or liquid object measuring between 0.001 and 1,000 microns.
Particulate
A collection of small particles, often airborne, that can contaminate a clean room.
Prefilters
Additional filters used before HEPA/ULPA filters to capture large particles and extend the lifespan of the primary filter.
Sealant
A plastic or silicone-based substance used to secure HEPA filters within ceiling grids.
Sticky Mat
Adhesive mats placed at clean room entrances to remove contaminants from shoes.
Testing/Certification Services
Professional services responsible for HEPA filter testing, particle count surveys, airflow consistency, and overall clean room maintenance.
Turbulent Flow
Air movement that is irregular and unpredictable, which can increase contamination risks.
ULPA (Ultra Low Particulate Air) Filter
Traps 99.9999% of particles as small as 0.12 microns, offering a higher level of filtration than HEPA.
Utility Matrix
A spreadsheet detailing all utility requirements for equipment within the clean room.
Wafer
A thin piece of silicon used as the base material for microchip production in semiconductor clean rooms.