Epoxy Adhesives
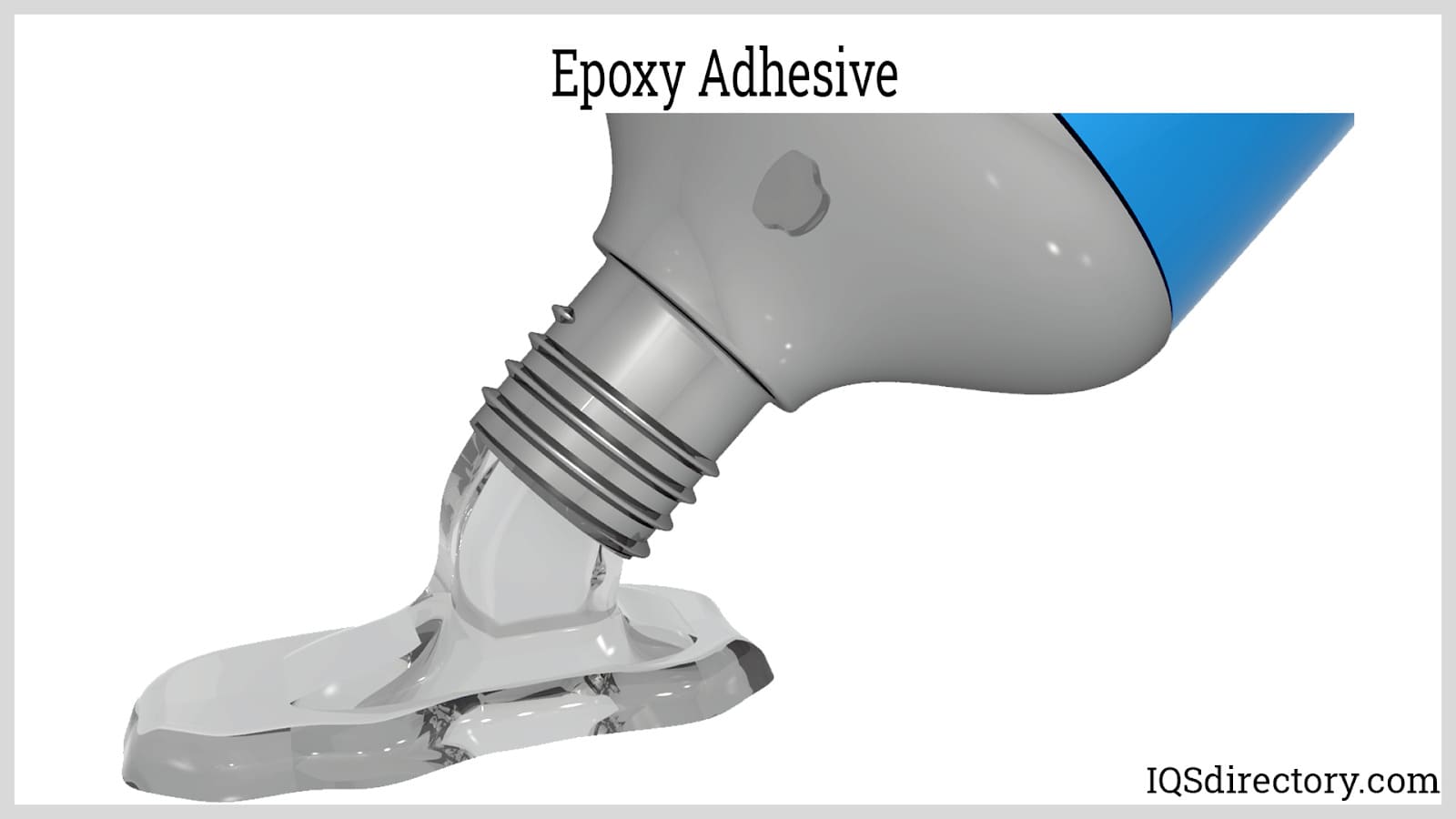
Adhesives and tapes, ceramics, glass and graphite are all materials used in industrial settings including, but not limited to:aerospace, automotive manufacturing, chemical processing, electronics, pharmaceuticals and wastewater. Adhesives, which include tape, can be generally defined as materials that bond surfaces together or unite them. The specific materials that can be used to serve this purpose are many, but among them are acrylic polymers, rubbers, epoxies like Bisphenol A and plastics, particularly those made from thermoplastic resins. Most typically, though, the adhesives used for industrial purposes are either plastic adhesives or epoxy adhesives. Adhesives can have a wide range of strengths, material compatibilities and physical features. Tape in particular can be manufactured with a wide range of widths, roll lengths and strengths. Some, for example, are made for use wi th fabrics and fabric-based items, like loudspeakers. Others are made to join or adhere to items permanently, necessitating that they must be especially strong. This is true of adhesives like duct tape. Because they are universally useful, adhesives and tapes are extremely popular in just about every industry under the sun.
Ceramics, glass and graphite are industrial materials with various levels of hardness and with a variety of different physical properties like electrical conductivity, corrosion resistance and thermal resistance. They are all made or derived from different naturally-occurring and synthetic materials. Ceramics, for example, may be made from more traditional materials like kaolinite or more modern materials like aluminum oxide (alumina), tungsten carbide and silicon carbide. Glass, on the other hand, is historically derived from silica, the main component of sand, but it can also composed of many other minerals and materials, like fluorspar, dolomite, limestone, fused quartz and more. Graphite is a bit more straightforward than its peers. It is a native mineral, meaning it can be found in nature, it can also be produced synthetically. Mostly, it is found naturally occurring in China, Canada, Brazil, India and North Korea. In general, all of the aforementioned industrial materials can be used in many different ways. They are often used to create different parts, both large and small, that contribute to applications like material handling, scientific research, machining, aircraft launching and more. In addition, all of these materials may be used in powder or grit form to perform abrasive media blasting. This is a process during which abrasive materials, like small glass beads, are forcibly projected in a stream towards a surface in order to smooth it, shape it, roughen it or clean it. As you may infer, ceramics, glass and graphite are all typically tough materials.
The manufacturers with whom IQS partner are all experienced and skilled, and they offer a wide range of services, sure to meet the needs of a customer. Find out more about the individual categories within the "Adhesives, Ceramics and Glass" industry and those companies that offer services in relation to them by scrolling down. Below you will find individual category descriptions and links to the external webpages of those manufacturers with whom we work.
Adhesives are substances that, when applied to one or both surfaces, binds two objects to each other and resists letting them separate. They can be used to bind objects either permanently or temporarily. Adhesives are used in just about every industry imaginable in some fashion or another, whether it be in arts and crafts or surgery. Therefore, it should come as no surprise that there are many different types of adhesives. Generally, adhesives are divided into type categories based on reactiveness, or lack thereof. Reactiveness of an adhesive is judged by whether or not it chemically reacts in order to harden.
Reactive adhesives are further divided into groups of multi-part and one-part adhesives. The former are adhesives that are made up of two or more components, while the latter only have one component. To work, multi-part adhesives harden via reaction with components with which they are mixed, while one-part adhesives harden when they chemically react with an external source like moisture or heat.
Non-reactive adhesives are divided into the following types: pressure-sensitive, drying, hot and contact. For the best results, select your adhesives based on: impact strength, shear strength, peel strength, cleavage strength, tensile strength, wet strength and fatigue strength. Learn more about adhesives.
Ceramic products are made from inorganic and metallic materials like tungsten carbide, silicon carbide, as well as, more traditionally, clay materials like kaolinite. They are Ceramics materials are valued for the many advantages they offer, such as their light weight, high melting points, high hardness levels, exceptional insulation properties, corrosion resistance and oxidation resistance.
They are also known for their extremely long service lifetime and superior heat protection. The many advantages of ceramic materials leads ceramic manufacturing to be popular with a wide variety of industries, particularly in the aerospace, automotive, food processing, medical and biomedical, military and defense and nuclear power industries. Ceramic products are usually divided into four main groups by type.
These are: structural, refractory, whiteware and technical. Structural ceramics include items like roof tiles, bricks, pipes, floor tiles and other products that help build or maintain a structure. Next, refractory ceramics are used in extremely high heat settings, most often kilns and furnaces. Examples of whiteware ceramic products include cookware, sanitary ware, tableware, wall tiles and pottery products. Finally, technical ceramics, are also known as fine, advanced, engineering or special ceramics, are used in technical applications. They include disc brakes, implants, missile nose cones and more. Learn more about ceramic manufacturers.
The term "glass" is somewhat broad, but usually, those glass products used in consumer, industrial and scientific applications alike are typically made of at least the three following ingredients: lime from limestone, sand and alkali-based sodium bicarbonate, which is also known as soda ash.
Each component offers something different. Lime, for example, has a high level of chemical stability and prevents glass from becoming water soluble. This can also be accomplished by aluminum oxide, which is even more chemically stable than lime. This addition is especially important when glass manufacturers include soda ash because soda ash, which is used to lower the initial melting point of the glass, also may make it water soluble. Other substances, like iron oxide (which creates a green tint) can also be used in order to create different colors and levels of shine or brilliance.
To create glass, manufacturers fuse these materials and others in a furnace reaching at least 2500?. Once it reaches this point of high heat, glass is cooled by several hundred degrees and shaped. Most often, shaping is done via drawing, pressing or blowing. The applications of glass are endless and diverse, from drinking glasses, to vacuum tubes, to fiber optics. Learn more about glass cutting.
Graphite is both a naturally occurring and synthetically manufacturable mineral that is used in a variety of applications that call for parts or materials with properties like: self-lubrication, dry-lubrication, corrosion resistance, strength and/or hardness. Examples of graphite products include bearings, brake linings, electrodes, batteries of all kinds, foundry facings, lubricants, pencils and neutron moderators.
Graphite may also be used in the service of: scanning probe microscopes, laptop cooling, vehicle heat resistance, steel making and refractories. Regardless of what product or part is made out of graphite, the machining processes used to process it must be heavy-duty. This is because graphite is incredible abrasive, making it tough on tools and difficult to fabricate. A polymorph of carbon, graphite is also the most stable form of carbon.
When found in nature, it may be grouped into three main categories: amorphous graphite, flake graphite and lump graphite. The first type, amorphous graphite, also known as meta-anthracite, is composed of exceptionally fine particles. The second type, flake graphite, is made of flat, isolated and plate-like particles. The third and last type, lump graphite, is also known as vein graphite. It is a compact, fibrous or crystalline aggregate that is found in fissure veins. Learn more about graphite machining.
Tape is an adhesive product used to bind and fasten. In general, tape consists of a backing material and an adhesive material that is coated on it. To create tape, tape suppliers use a process that reflects this; during the process called coating, manufacturers apply adhesive to the backing, or carrier, material. Typically, the backing material is a fairly thin and flexible one, like cloth, paper tissue, film or even metal foil.
To apply the coating, manufacturers use one of three common methods: hot-melt coating, water-based coating and solvent coating. During hot-melt coating, adhesive is heated to its melting point, then applied onto the backing material while it is still liquid. Once it has cooled, the coating process is done. Next, water-based coating uses solutions that are made when adhesive is mixed with water, forming small, suspended globs of one liquid inside the other (emulsions). To finish, the emulsion is coated on. During solvent coating, tape suppliers use a solvent to dissolve the adhesive and leave behind a relatively non-viscous liquid. Once they have done this, they coat the liquid onto the backing material. Then, to finish, they remove the solvent residue by sending the tape through a heated oven. Learn more about tape suppliers.