Air Filters
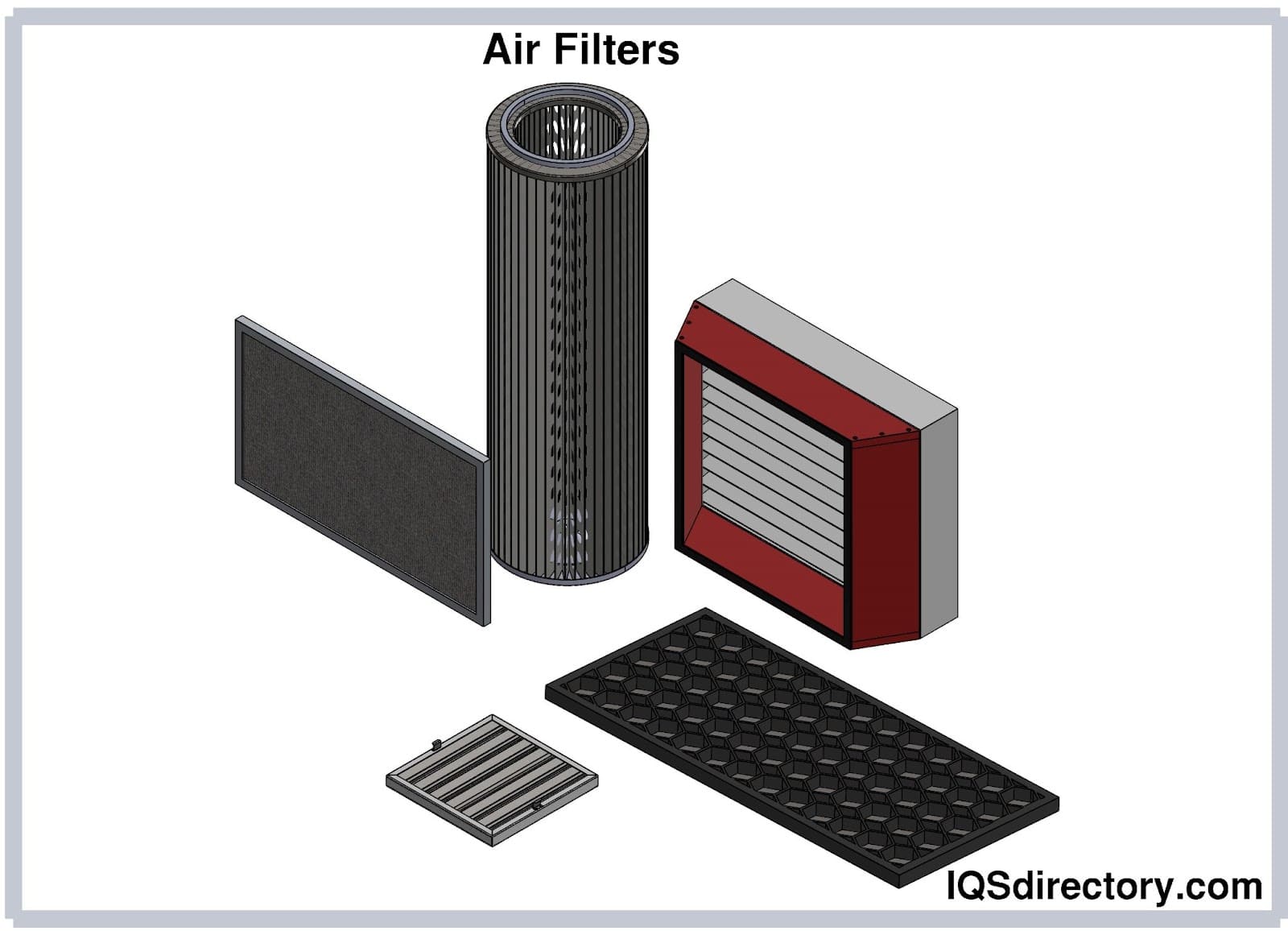
As technology has advanced and the need for filters for air, liquid, and assorted filtering systems has grown, a wide variety of filtering methods have developed, which include filters made of fabrics, electron filters, and natural methods such as bacteria and chemicals. The design and use of each type is dependent on what has to be removed as well as how pure the final result must be. In manufacturing and industrial complexes, there are contaminants that pollute the air and liquids that require a filtering system. To meet these needs, specific filters are designed to fit each application.
Though air filters are vital to industry, they are also valuable as a means of keeping air in a home clean. Their main purpose is to remove particulates from the air, which can include air from a ventilation system or air coming in from outside. In manufacturing, air filtering systems assist in improving the quality of the air in a facility for the protection of workers.
An important form of air filter is used for clean rooms, which have extremely high standards associated with air content that is measured in the number of particulates per cubic meter. The most common form of air filter for clear rooms is a HEPA, or high efficiency particulate air filter, that removes 99.9% of all pollutants. The measurements for these conditions are determined in microns or micrometers as symbolized by "µm".
Though air is the first consideration when discussing air filters, this type of filter is also used to purify gases for repurposing and reprocessing. Specially designed filters are designed to fit the specific application and meet quality requirements. When discussing filters, it is important to make a careful examination of the desired outcome as well as the conditions under which the filter will be used.
Another crucial form of filter is a water, or liquid filter, that comes in several forms depending on the type of liquid to be cleaned, which include oils, water, lubricants, and other manufacturing materials. As with air filters, each form of liquid requires a specific liquid filter with the correct fiber content and design to trap the materials to be removed.
The material for a fabric or solid filter can include wool, cloth, paper, fiberglass, or carbon. These types of filters are porous enough to allow acceptable substances to pass and block those that are unwanted. The principle of the system is to clean and clear materials such that the final product is free of contaminants. Most fabric or material filters have the substances to be cleansed passed through a series of filters to ensure complete particulate removal.
Electronic methods of filtration include the use of electrically charged ions. The ionic process uses voltage to trap particles using negatively charged ions, called anions. The charged ions attract particles as they pass through the system much like static electricity. When the anions connect with the particulate matter, they are deionized and fall out of the stream.
Some of the natural filtering systems are centrifugal and gravity. In a centrifugal system, air to be purified is passed through a rapidly rotating chamber where heavy particles are forced against the wall of the centrifuge and fall into a collector. The lighter cleaned air escapes for further processing or other uses.
Gravity filter systems are a practical filtering method that is inexpensive and does not require a power supply. It is applicable for liquids and granular materials. In a gravity system, there is a holding tank for the material to be cleaned. The contents of the holding tank are poured into a second tank with a filter that the holding tank material passes through before entering the second tank. In many cases, this process is repeated several times and may entail the changing of the second tank‘s filter.
Another natural method for removing contaminants is a biological system, which can be compared to a chemical filter. A biological filtering system uses bacteria to remove unwanted particles, usually from water. In nature, certain bacteria feed on contaminated substances and serve as a natural purification system. Filter manufacturers use the same principle when applying it to industrial filters. Biofiltration removes contaminants and pollutants by passing substances to be purified through a series of filters containing bacteria that live on the pollutants. The process can be used for natural and chemical materials.
Liquid and air filters, as well as filtering systems, are an essential part of meeting environmental standards and assisting industries maintain a safe workplace.
Air filters are devices used to minimize or remove unwanted particulates from the air. This may be air flowing within a ventilation system, or it might be air moving through an open indoor space. Industrial air filtration systems improve
indoor air quality and extend the working life of machinery, engines and appliances.
Types of spaces and products that air filters clean include in-home and commercial heating systems, ventilation systems, air conditioning systems, humidifiers, engine components, cars, and direct air machines. Particles that individual air filters remove fluctuate, but some include mold spores, animal dander, and dust and pollen. Learn more about air filters.
Filtration systems are used residentially, commercially, and industrially to physically remove contaminants from air, liquid, gas, or powdered substances. The process of separating a fluid substance into two or more distinct factions is often accomplished
through the use of a screen, film, or membrane. The fluid may be vacuum or pressure driven, or gravity fed through the filtration device to remove particles or contamination. Other methods of filtration include centrifugation, and chemical, biological, or electrical processing.
Air and water are the most common fluids to go through the filtration process. Other process fluids include food and beverage products, petrochemicals, paints, plating solutions, photographic solutions, pharmaceutical products, chemicals, lubricants, gases, fuels, coolant, and cosmetics.
There are several different manners in which filtration systems separate materials in a mixed process stream. Membrane filtration involves the use of media that trap contaminants. Foams and other materials employ similar techniques; additional filtration options include the use of gravity, centrifugal force, chemical solvents, biological agents and even electrically charged apparatus. Gravity and centrifugal force filters use hydrostatic or rotational pressures, which remove heavier particles from the flow line. Chemical filters function by either dissolving specific contaminants or attracting them and, through the use of gravity, pulling them from the system. Not as common, but thoroughly effective, biological filters use digestive microbes to remove unwanted organic compounds. There are two main types of filtration systems that depend upon the use of electrical charges to purify air and fluid supplies. Electrodialysis (ED) uses membranes that allow the passage of either positively or negatively charged ions while excluding the passage of the opposite. Because ED membranes are easily clogged, many filters are equipped with electrodialysis reversal (EDR) systems instead. It works in the same way as ED systems, but it periodically reverses the electrical current in order to exchange the fresh product flow. Reverse osmosis (RO), electrodeionization (EDI) and ultrafication (UF) processes are less common but equally efficient options. Each type has benefits and advantages particular to specific filtration applications. Learn more about filtration systems.
Liquid filters clean or purify liquids that run through them. All liquid filters operate by passing a liquid through a semi-permeable or porous substance, which allows the liquid molecules to pass through, but blocks large particulates and chemicals.
Note: The word "filter" actually refers to the housing or holding mechanism of a filtration system. "Filter media" refers to the porous barrier, chemical or mat clarifies the liquid. Learn more about liquid filters.