Magnetic Flow Meters
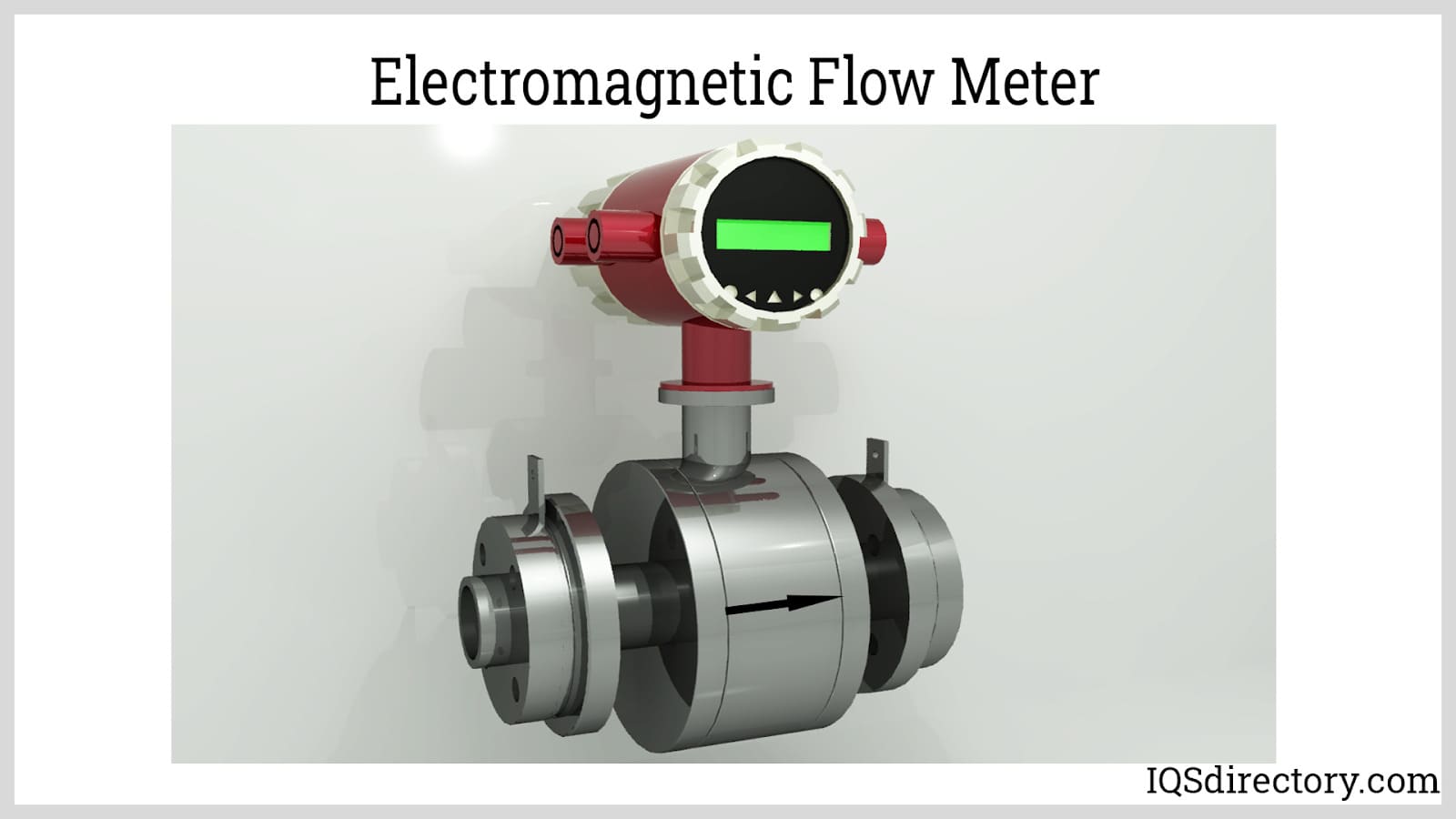
The determination to use a flow instrument is based on various factors beyond measuring the pressure and flow of liquids and gases. The main concerns for businesses are cost and efficiency to avoid waste by ensuring precision movement of materials. An accurate flow instrument can give production managers precise calculations relating to quantity, pressure, and flow.
The term flowmeter is an all-encompassing term used to describe a group of instruments used to measure the precision movement of liquids and gases. Though it is used as a generic term, it does not sufficiently describe the different types of instruments that are used to measure, regulate, and monitor material movement, which include flow gauges, flow indicators, and flow meters. The design and use of each form of device is specific to the types of readings that they take.
Flow gauges are designed to measure the rate of flow through a pipe or line such that it can be best adjusted to fit the application. They are commonly found in the regulation of fuel, chemicals, energy, and heating and cooling applications, which have a constant flow that has to be at an even controlled rate. Much like flow meters, flow gauges break into two groups, mass or volumetric.
Mass flow gauges are Coriolis or inertial and thermal. Coriolis flow gauges are named for the Coriolis effect, which is a vibrational force that is caused inside a flow tube by the tube‘s oscillation measured by sensors. The data from the sensors is used to calculate the mass flow. Unlike the Coriolis method, a thermal flow gauge measures heat transfer in a pipe or tube using the concept that faster moving flows have a cooling effect.
A flow indicator is a very basic type of flow measuring device. It uses empirical evidence to determine the rate of flow. Flow indicators do not take measurements, calculations, or readings to determine mass, speed, or flow rate. The design of a flow indicator allows the operator to look through a glass or plastic viewing window to observe the clarity, color, level, and movement of the flow.
The type of window for a flow indicator depends a great deal on the indicator design and the type of data that is to be gathered. In some cases, two windows are used where there is the threat of high pressure or corrosion that may impact mechanical performance. A flow indicator mechanism is attached to the flow pipe by threaded, flanged, or butt welded connections that are water and leak proof. In places where there is low visibility, a light may be installed to assist in viewing the flow. Flappers or propellers may be added to help in determining the direction of the flow.
Flow meters, the name that has been given to all flow measuring instruments, has several functions for collecting data, measuring flow, determining flow direction, and several other types of data. They are found in any industry that depends on raw material flow as an essential part of its operation.
There is an endless use for flow meters from ones that monitor volatile liquids as a safety measure to others that are designed to measure mass of a material and not its volume. The assortment of flow meter applications is the reason for their many varieties and types. The functions of flow meters include monitoring pressure, calculating fluctuations in temperature, and tracking the cleanliness of substances.
Any industry that works with fluids such as fuels, water, and chemicals as well as those that have gas as a central part of their operation uses either a flow gauge, flow indicator, or flow meter.
Flow gauges are devices used to measure the rate at which a liquid or gas is flowing through a system. They then relay this information to the operator who can make adjustments based on the readings or choose to continue to monitor the situation.
Flow gauges can be found in a wide range of applications and industries, as measuring the flow of fluid or gas can be a vital part of a lot of different products and systems.
Some examples of the industries and applications flow gauges are commonly found in include the medical industry for monitoring medical treatments and the energy industry for measuring fuel usage. In addition to these applications, flow gauges are an essential part of a lot of manufacturing processes as being able to monitor exact material feed values is a required part of the system. Learn more about flow gauges.
Flow indicators allow an operator to view the liquid as it moves through the pipes. These simple but important flow meters are often called sight flow indicators and are components of industrial process lines that require an instant and inside look of the flow inside the pipe.
Unlike ultrasonic flow meters or vortex flow meters, flow indicators do not take calculations or measurements regarding mass or speed. Flow indicators are the type of flow meters that monitor fluid clarity, level and color through a glass or plastic observation window of varying size. The window can be horizontally or vertically oriented. Learn more about flow indicators.
Flow meters are devices used to measure and monitor the flow of gases and liquids through various systems. These instruments are designed and manufactured for use in a multitude of different industries and applications. They can vary in construction, size, configuration, and measurement technique.
Some flow meters have to be built to operate effectively while exposed to volatile liquids, others have to handle a much larger volume of fluids, and still others have to measure mass instead of volume. All of these different factors contribute to the huge diversity in flow meter design. Other important factors include cleanliness, pressure, and operating temperature.
Manufacturers across practically all industries understand the importance of flow meters in everyday industrial processes. They are used to maintain efficiency and to help better understand profit gains and losses. The automotive, petroleum, HVAC, food and beverage, utility services, chemical, and many other industries all utilize flow meters extensively to monitor their operations. Learn more about flow meters.
Flow switches are used to monitor fluid or gas flow while it is passing through its valve body, then to send an electrical control sign if the flow rate is too high or too low. The signal is sent as a safety measure to another device, such as a pump, that will respond accordingly or to a switching unit within the valve body. This is an important safety feature because many processes will only operate within a certain range of flow rate, halting or becoming compromised if the flow rate exceeds or falls under that range.
Learn more about flow switches.