High Pressure Boilers
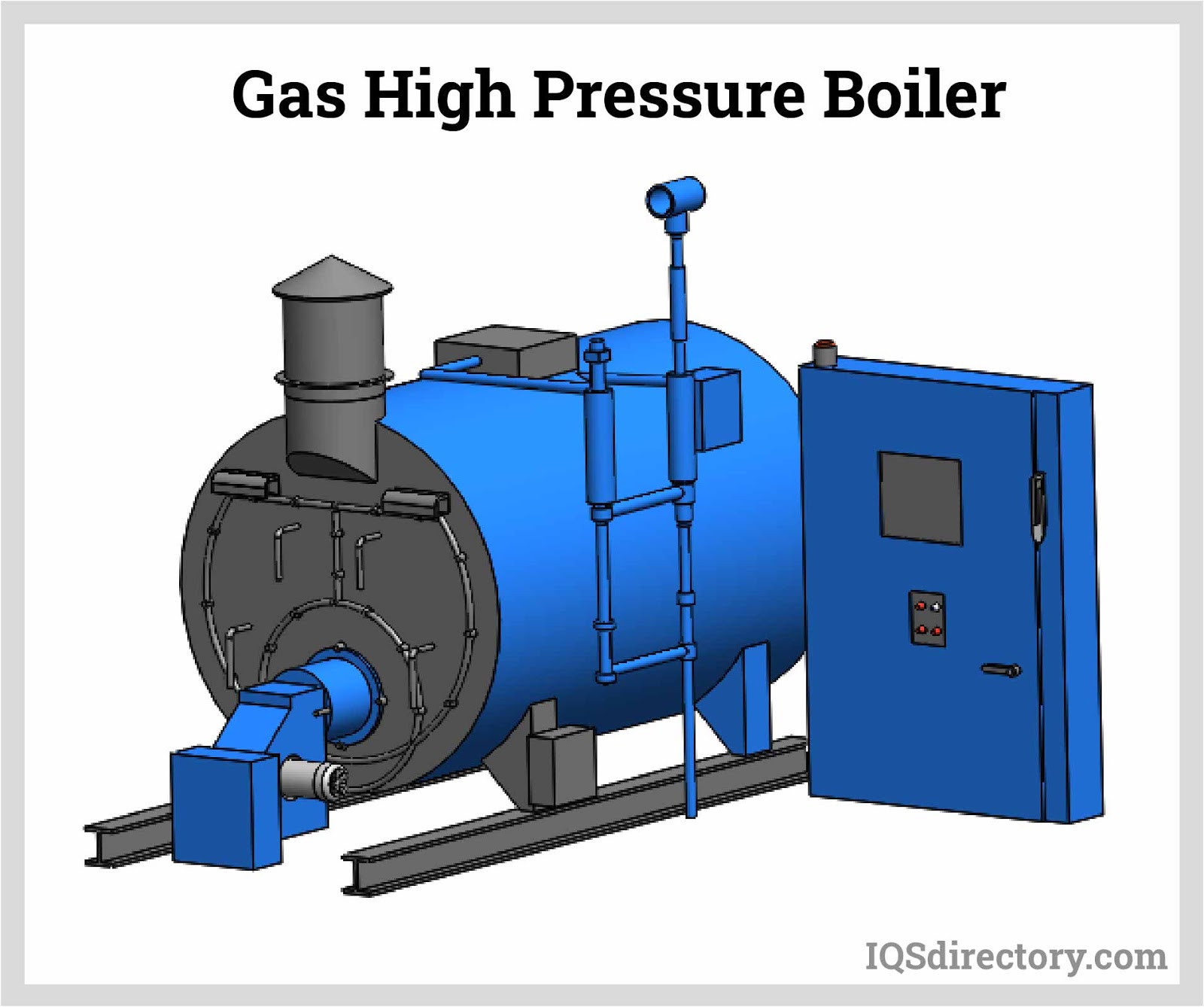
Heat transfer involves the movement of internal energy from one substance, material, or fluid to another, whether similar or different. It falls within the domain of thermodynamics, which explores the connection between heat and temperature. Understanding heat transfer is crucial for comprehending the operations of engines and pumps.
Energy is generated through the movement of atoms and molecules, transferring as heat between different bodies or systems. Heat transfer occurs in several ways: conduction, convection, and radiation. Conduction involves heat transfer through direct physical contact, while convection occurs through a fluid medium. Radiation, in contrast, requires no material medium for heat transfer.
Conduction is most efficient when surfaces are smooth and closely in contact. Gaps between materials reduce heat transfer efficiency. The interface where heat is exchanged is known as thermal contact. Insulation is designed to minimize thermal contact and restrict heat transfer.
Convective heat transfer involves two primary mechanisms: conduction and advection. Convection transfers heat to another substance, typically a liquid. This process commonly occurs between a heated surface and a fluid moving across it. When a fluid contacts a surface, it accelerates and heats up.
Radiative heat transfer occurs through electromagnetic waves, specifically in the infrared spectrum. Radiation is emitted when molecules undergo thermal activity. In industrial heating, radiation utilizes ultraviolet, infrared, microwaves, and short radio wavelengths. Unlike conduction and convection, radiation transfers heat without requiring material or contact.
Heat transfer equipment comes in two primary types: condensers and evaporators, each serving opposite purposes. Condensers cool refrigerant vapors to return them to a liquid state, while evaporators heat liquids until they vaporize. These systems circulate thermal fluid through processing equipment to maintain consistent temperatures. They comprise pipes, tanks, pumps, and heating/cooling methods that circulate water, steam, and oils. Heat is generated using fuels like gas, propane, or oil, as well as alternative sources such as solar power and electricity.
The most prevalent heat transfer system features small tubes carrying fluid, with a second liquid flowing over them within a shell. This configuration is common in oil refineries and chemical processing plants. Heat transfer equipment is ubiquitous, found everywhere from kitchen stoves to computer processors. It facilitates the transfer of thermal energy, underscoring its critical importance in daily life.
Boilers are enclosed containers designed to heat water or other fluids. In the United States, if the boiler's purpose isn't to boil water, it's often referred to as a furnace or, in household terms, a water heater. These devices are utilized across industrial, commercial, and residential settings to provide heated air, hot water, and steam for machinery powered by steam.
Learn more about boilers.
Liquid chillers rapidly cool large quantities of liquid refrigerant to extract heat from air or other liquids. Subsequently, they distribute the cooled liquid or air as required.
Learn more about chillers.
A cooling tower is a closed structure utilized in industrial plants to remove heat from water or other fluids. Despite varying designs, types, shapes, and sizes, cooling towers operate on the principle of evaporative cooling. Heat from water is transferred to the air through evaporation, effectively lowering the water temperature. Sometimes referred to as evaporative condensers or fluid coolers, cooling towers' efficiency is assessed based on the wet bulb temperature, which represents the lowest achievable temperature of the water in the system.
The rate of heat transfer required for water evaporation into the air serves as a performance indicator for cooling towers. The entering wet bulb temperature of the air is crucial in evaluating a cooling tower's effectiveness. Guidelines from industry bodies like the American Society of Mechanical Engineers (ASME) and the Cooling Technology Institute (CTI) recommend sizing and testing cooling towers based on entering wet bulb temperatures, measured using a psychrometer.
Learn more about cooling towers.
Industrial furnaces are enclosed chambers designed for high-temperature operations. They are utilized primarily with materials that have high melting points, such as steel, titanium, aluminum, alloys, glass, composite materials, and certain plastics. These furnaces are essential in various industries including glass fabrication, steel service centers, foundries, forgeries, metal recycling plants, and metallurgical processes where heat is used to modify, enhance, manufacture, or shape metals.
Furnaces designed for smaller production runs typically feature a single chamber and require manual loading and unloading. Various tools are used to handle crucibles filled with molten metal or heat-treated products. In contrast, furnaces designed for higher volumes come equipped with automated conveyor systems, allowing for the simultaneous treatment of numerous parts or products. These advanced furnaces can operate under controlled atmospheres, which may be oxidizing, inert, salt bath, or vacuum. They are predominantly used for heat treating glass and metal, a process that modifies or enhances the materials' properties through exposure to high temperatures followed by rapid cooling. Additionally, these furnaces are capable of aging, annealing, sterilizing, and sintering materials, as well as melting raw substances for molding or casting. Key specifications for furnaces include temperature requirements, pressure, internal dimensions (width, length, and height), and the type of heat source used.
Various furnace heat sources are available today, each with unique benefits, limitations, and applications. These sources include radiant, natural gas, induction, conduction, electrical, and dielectric methods.
Radiant heat furnaces operate similarly to wood stoves and portable heaters. They use a flame to heat an object, typically a ceramic plate, which then radiates heat throughout the area. Natural gas furnaces, burning natural gas or propane, are a cost-effective option for creating high-temperature environments and are widely used for their efficiency.
Induction furnaces heat metal parts through a combination of electrical resistance and hysteresis losses, generated by exposing the metal to a magnetic field around a coil carrying alternating current. These furnaces are preferred for metal melting applications, especially in iron foundries.
Electric furnaces, particularly electrical arc furnaces, are also popular for melting metal. They use high electrical currents that travel through a metal arc and conduct onto large quantities of scrap metal, heating it sufficiently to melt. These furnaces are primarily used for recycling metal parts into new products.
Learn more about furnaces.
Heat exchangers are devices made from thermally conductive materials designed to transfer heat between fluids. Depending on the model, these fluids can either be in direct contact or separated by a barrier. Heat exchangers are used to facilitate heat transfer for cooling or heating substances, which are then used in various other processes.
Heat exchangers are crucial in industrial processes involving the design, operation, and maintenance of heating systems, power generation, air-conditioning systems, chemical processing, engineering, and waste heat recovery systems. The fundamental principle of heat exchangers is also applied in the design of boilers, which heat large spaces by dispersing heat from a centralized source.
Learn more about heat exchangers.
Heat transfer equipment are devices used to transfer heat between mediums. Various types of heat transfer equipment offer distinct advantages and disadvantages. When selecting the appropriate equipment for an application, consider factors such as temperature range, thermal performance, fluid flow capacity, and pressure limits. Additionally, evaluate the potential need for future expansion of heat transfer equipment.
Maintenance requirements vary depending on the type of system, its layout configuration, and the materials used. Heat transfer equipment are essential in numerous industrial applications, including wastewater treatment, refrigeration, and petroleum refining, among others.
These products can be designed for air-to-air, water-to-air, water-to-water, oil cooling, flat plate heat transfer, waste heat recovery, and other configurations.
Learn more about heat transfer equipments.