Paper Tubes
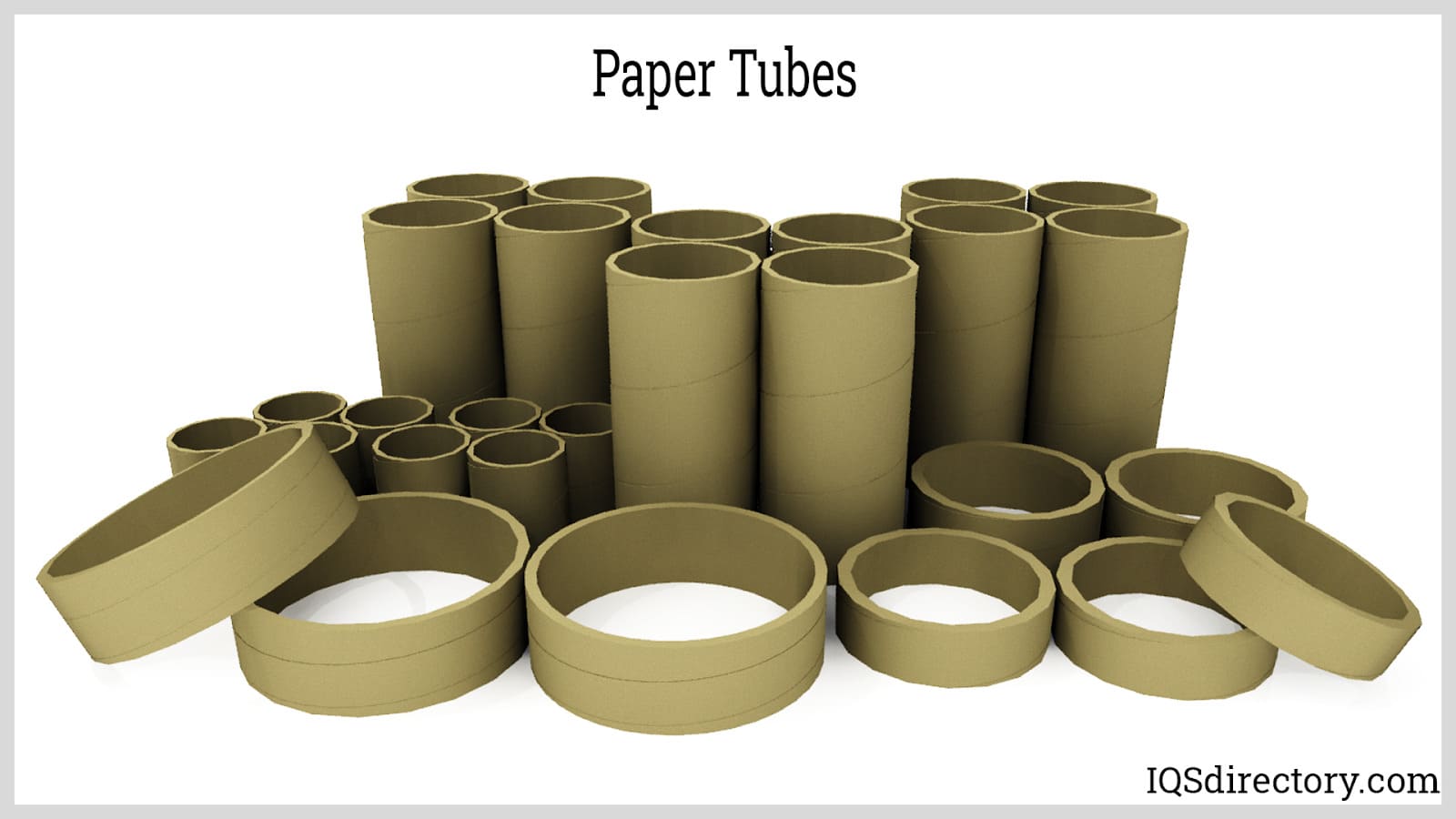
A fundamental aspect of the supply chain is having the proper equipment, materials, and protective devices to keep products and supplies safe during transport. This crucial part of product and tool movement depends on the design and planning of materials that exactly fit the requirements of each item to be shipped, a job that takes hours of planning and preparation.
The fundamental and most common type of shipping container is the pressed and glued corrugated box that has been a part of shipping for hundreds of years. Made in a variety of thicknesses for the shipping of huge equipment or small pieces of clothing, corrugated boxes have set the standard for how shipping containers should perform. Every part of delivery and product transport depends on the sturdiness and durability of corrugated boxes.
There are certain types of shipping that require specialized shapes to fit the needs of the product. This is true in the case of sending blueprints, posters, advertising materials, and pictures. Cardboard shipping tubes have been developed to meet the need of these specialty items. Using fiberboard, kraft paper, or paperboard, each tube is shaped to the proper length, diameter, and strength to meet the needs of the item to be shipped.
In the case of shipping technical instruments, computers, and delicate or intricate equipment, sturdier and more durable shipping cases are required that have specialized interior padding and coatings to prevent shocks or vibrations from damaging the equipment. These carrying cases are made from exceptionally durable molded plastics that have been tested to ensure that they can endure any type of shock or impact. When a piece of equipment has several components, compartments are placed in the container for added protection.
A key factor in the shipping industry is the ability to identify and catalogue the materials and items that are being shipped. One method for accomplishing this is through the use of dot peening that places permanent marks, numbers, descriptions, or short statements on materials as a means of identifying them. The nature of dot peening makes it an ideal solution for inventory purposes and providing the ability to locate stored materials and equipment.
To many people, labeling is the process of producing a paper label or tag to be affixed to an item for identification. Though this may be the first thing that comes to mind, the modern version of labeling is far more technical and advanced. Pre-glued paper labels are still used as a means of placing names and titles on folders and paperwork. The labeling industry has expanded into more modern methods that include sophisticated software and design features.
An activity that many employees have dreaded is the need to connect marking labels to inventory items. In the past, the process has been tedious and time consuming. With the use of technological advancements, the once tiresome task has been streamlined to quickly produce labels and attach them to any size item with ease and convenience. Included in the labeling advancements are hot stamping, plasma etching, laser marking, and dot peening, which are more efficient and permanent. These modern methods provide accurate control of inventory and easy location identification.
As with all industries, the packaging and supplies industry has been rapidly improving its processes with packaging equipment for enclosing, protecting, and storing of products supplies and inventory items. As an added benefit, the age old pallet has had its use maximized with the use of palletizers to assist in material movement and storage. Though corrugated boxes have become the staple for shipping, the need to protect the shipment of smaller items is fulfilled with versatile, resilient, and sturdy plastic bags.
Each of the many advancements in the development of shipping, packaging, and supplying raw materials as well as the storing of finished products has helped in the improvement of the quality of products delivered to manufacturers and the public.
Cardboard tubes, or paper tubes, are cylindrical products fabricated from wood pulp which has been made into different varieties of cardboard such as fiberboard, paperboard, kraft paper and paper-adhesive composites.
Cardboard tubes are used for a wide variety of functions in different industries and are typically fabricated from ribbons of cardboard wrapped around a mandrel in the desired dimensions.
Cardboard tubes can be made to fit a broad range of products, and are made in different levels of structural strength and thickness, depending on the level of protection required. Most commonly used for mailing tubes and shipping tubes, cardboard tubes are readily available for papers, posters, documents and pieces of artwork which are able to be rolled into a cylindrical shape. These poster tubes are able to withstand the pressure and stress that occurs during transit as they are formed from a material such as high quality kraft paper. Kraft tubes are strong and are often used in shipping and packaging. Other common uses for cardboard tubes include: paper cores providing structural strength to items such as rolls of fabric, paper towels or toilet paper, and electrical wires, coin banks for collecting money and donations, caulking tubes for construction projects, grease cartridges for use in the automotive and mechanical industry and paper cans which are used widely in packaging for foods, cosmetics and merchandise. Another specific use for cardboard tubing is by contractors and construction industries that use large, heavy duty and highly durable cardboard tubes, called Sonotubes®, for concrete pillar forming. You can find Sonotube® manufacturers and conctrete tube producers here on IQS Directory. Learn more about cardboard tubes.
It is hard to imagine the world without carrying cases. They are put to use every day in a massive variety of ways.
They get our stuff from point A to point B without damage. When they fail, we are at a loss, whether financial, material, or for kind words. With the ability to purchase or customize a quality case for nearly any purpose, getting things where they need to be, intact, is no longer a gamble.
Carrying cases come in many shapes, sizes, and compositions. They are often rectangular, sometimes with recesses or pockets to secure items. They may be tubes with sealed end caps and/ or hinged sides. They may be internally or externally shaped to the contours of the things inside. Carrying cases may be flame retardant, static free, resistant to electromagnetic interference, or waterproof. They may be hard or soft sided, single chambered or compartmentalized, and may have wheels for ease of movement.
More than just boxes and bags, custom carrying cases provide quality protection for the safe transport of delicate, sensitive, unruly, or potentially dangerous items, equipment, or materials. The case size, shape, and composition will be dependent upon the material in transit. Learn more about carrying cases.
Contract packaging is a service where a company will package products for another company.
Proper packaging is an essential step in the distributing process of any manufacturer and some industries have a number of very strict packaging requirements. For example the food/beverage and medical industries are required to comply with a set of regulations to ship their items. In some situations companies may not be able to properly equipped with the equipment to meet these requirements so a contract packaging company can then be utilized to adequately package the materials. Learn more about contract packaging.
Corrugated boxes are storage and shipping containers that are constructed of corrugated materials.
The term corrugated material refers to material (usually a type of paperboard) that is rippled, fluted or ridged. Corrugated containers are usually composed of a corrugated fiberboard, a common form of material that consists of a corrugated sheet sandwiched between layers of flat sheets. Despite the inaccuracy of the term, "cardboard box" is widely used to refer to this type of container.
Learn more about corrugated boxes.
Dot peen marking machines are a type of marking machine, which is a machine used to leave marks on the surface of objects and materials for the sake of identification, tracking, design or the impartation of other information.
Some other types of marking techniques include: embossing, engraving, etching, electrochemical etching, hot stamping, scribing, coining, abrasive blasting, laser marking, press rolling, rotary marking, roll marking, stylus marking and inkjet printing. Dot peen marking machines leave their mark using the process of dot peening. Dot peening is an impact marking technique that uses a multiple axis marker stylus in order to imprint identifying marks onto the surface of a material. Their primary function is to provide identifiers for products via marks including: bar codes, 2D codes, custom labels, custom graphics and alphanumeric characters. These marking machines are popular for use in a wide variety of industries, including aerospace, automotive, international transportation, manufacturing and medicine. In the aerospace and automotive industries, they are used to impact castings, metal tags and individual parts. In manufacturing, dot peen marking machines are often integrated into existing automatic and semi-automatic assembly lines, and they are also sometimes installed as a part of test stations. In the medical industry, dot peen markers are used to add identification to plastic molded parts and other products, such as surgical instruments. Of all of these industries, dot peening continues makes the greatest impact on aerospace, international travel and medicine, as product identification is of the utmost importance to them.
Dot peening marking systems participate in a process known as permanent direct marking (PDM), which is a process in which a marking machine leaves the material with a small depression in which color can later be added. To impart these depressions on a surface, or "peen" a surface, dot peening machines use a metal pin that is moved by air pressure. To work, air pressure drives the pin into the surface material, creating a small indentation, then quickly releases it, lets it move and then drives it into the material again. In this way, the dot peening machine, which is typically driven pneumatically, is able to create a series of closely spaced indents or dots. Dot peen marking machines can impart these depressions on all sorts of materials, including some hard woods and plastics. However, the process is most successful when used on metals with a hardness in the range of 62 on the Rockwell scale. Learn more about dot peen machines.
Labeling machinery is the term used to describe any equipment involved in the process of producing labels or affixing them to products. This equipment includes printers, applicators, dispensers and many other label making and applying systems.
Labeling machinery has applications in many industries, including, among others, agriculture, chemical and laboratory, electronics, food and beverage, home and office, pharmaceuticals, and packaging. Industries like these use both individual labeling components and fully integrated labeling systems. Labeling machinery may be as simple as handheld label or barcode printers, or as involved as systems that incorporate microprocessors and/or computer software. Learn more about labeling-machinery.
Marking machinery refers to a variety of machines that are used to implement images, logos, identification codes, part numbers, hazardous symbols and much more.
Marking machines are ideal for adding a uniform system to a workplace and there are several logistical benefits associated with marking machinery. These machines offer a number of different part marking styles such as hot stamping, plasma etching, laser marking, dot peen and more. The type of marking equipment that should be selected for a situation is based upon the surface type and application. Learn more about marking machinery.
Packaging equipment refers to the various types of machinery used in the process of enclosing or protecting products and materials for the purposes of storage, sale, distribution and use.
Also known as packaging machinery, packaging equipment is used to automate the packaging process, reducing labor time and cost as well as increasing process efficiency. Learn more about packaging equipment.
Packaging equipment refers to the various types of machinery used in the process of enclosing or protecting products and materials for the purposes of storage, sale, distribution and use.
Also known as packaging machinery, packaging equipment is used to automate the packaging process, reducing labor time and cost as well as increasing process efficiency. Learn more about palletizers.
Plastic bags are extremely versatile containers or carriers made of thin and often flexible polymeric films.
Used to store, transport, ship and package goods in a number of industrial, commercial and residential applications, baggies such as these prove very useful as they are most often waterproof and provide some degree of protection from the elements. Commonly referred to as poly bags, the containers are constructed of processed polymer resins. Learn more about plastic bags.
Sewing contractors manufacture products and provide services for a multitude of industries and applications.
This trade employs simple and complex machines that are capable of producing high quality custom embroidery and large-scale manufacturing. Companies contract production out to industrial sewers for a wide variety of products found in nearly every business or home. They manufacture a plethora of textiles including covers, fabric enclosures, uniforms, and carrying cases.
Many types of fabrics are used by sewing contractors. Vinyl-coated nylon is a lightweight, durable material that is a popular choice for bags, presentation cases and protective covers, as it is tough and weather resistant. Neoprene and Hypalon are chemical and abrasion resistant and are used in industrial applications. Canvas, which is comprised of twill, soft flannel and felt, is a breathable material used for bags and curtains, as well as many industrial applications. A sewing contractor uses a variety of anti-static materials for products in the computer and electronics industries. Other materials include suede, leather, felt, webbing, plastic, cotton and polyester. These fabrics are often custom embroidered, which is a decorative embellishment made by stitching thread by a needle. They are graphic or descriptive text and images, and they are often used by companies and businesses that want to print their logo on their products and employee uniforms. Clothing labels are attached inside of all garments, bedding, textiles and clothing that are sold commercially. These tags contain information that lets the consumer know where the product was made, the materials it is made out of, washing instructions, and they often have a brand name, logo and garment size. These tags may be woven, embroidered or printed and made of satin, damask or taffeta. Learn more about sewing contractors.
Tape, made of long strips of adhesive material, is primarily used for a wide range of binding and fastening applications, though it has several other applications as well. To make their product, tape suppliers engage is a fairly simple process called coating, wherein adhesive is applied to a carrier material. The carrier material may be any one of a collection of moderately thin and flexible materials, such as metal foils, paper tissues, cloth or films.
There are three main methods of coating: water-based coating, solvent coating and hot-melt coating. Water-based coating solutions are made by mixing the adhesive with water to form emulsions, or small, suspended globs of one of the liquids in the other. After the solution is made, it is simply coated on. In solvent coating, a solvent is used to dissolve the adhesive and thereby create a comparably non-viscous liquid, which is coated onto the carrier material. After the material has been coated, suppliers remove the solvent by passing the tape through a heated oven. The hot-melt coating process is performed in the way that its name suggests; the adhesive is heated until it reaches its melting point, and then it coats the carrier material as a hot liquid. After coating, the tape only need cool to become a finished product. Learn more about tape suppliers.