Ball Bearings
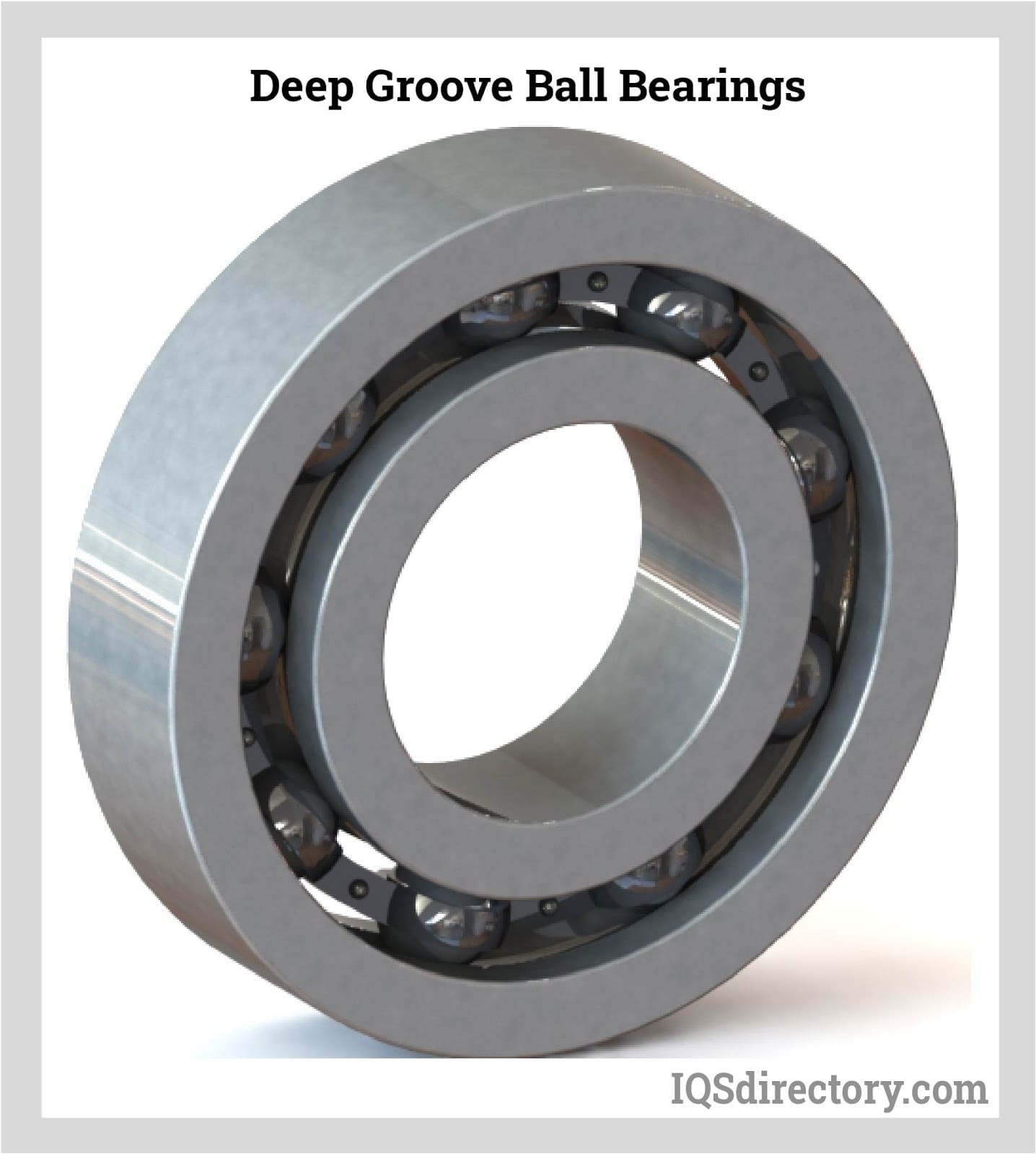
The purpose of power transmission is to move energy from its point of generation to a place where it can be applied for useful and productive work. This definition of power transmission may create visions of electricity passing through a wire. There are many forms of power transmission that do not include electricity or other forms of energy. The key is the concept of the transmission of power from one location to another.
Included in the broader definition of power transmission are conveyor belts, chains, pulleys, bushings, bearings, and linear actuators that redirect and guide various types of motion and energy. The rule for the manufacture of power transmission equipment is that they have to be sturdy and durable enough to withstand constant stress.
One of the most common forms of power transmission mechanisms is the ball bearing that allows for motion between two objects without creating friction. Ball bearings can move heavy objects and materials with less effort. The use of ball bearings is critical in the creation of smooth and uniform movement, which helps in avoiding damage to equipment and parts.
A fascinating mechanism that has a wide range of use is a ball screw device that changes rotational or circular motion into linear or straight motion. The transformation created by a ball screw is a crucial part of machines and mechanical movement. Ball screws can be found in nearly every form of manufacturing equipment since such conversion is a necessary part of heavy duty equipment operation.
For many years, the basic electric motor has been a reliable source of energy for manufacturing. Since electric motors can be designed in several different sizes, they can be applied to any form of machinery. The energy created by an electric motor is caused by the electromagnetic interaction between a coil and a set of magnets, which produces mechanical force. The types of energy from an electric motor can be direct or alternating depending on the requirements of the application.
Regardless of the type of energy or power being produced, there has to be some form of mechanism for stopping the flow of power. As demonstrated by the brakes on an automobile, this form of force is created by materials that create friction between surfaces. The purpose of friction materials is to control, slow, or inhibit motion. The main characteristic of friction materials is their high friction coefficient.
Much like ball screw devices, gears are a transfer mechanism used to change torque. They are composed of equally spaced teeth that come in a variety of designs and shapes that smoothly mesh. The various types of gears include spur, spline, and planetary, which are incorporated into a machine based on the type of torque required.
One of the simplest forms of power transmission devices is the quick release coupling that allows for easy and immediate connection or disconnection of fluid lines. The idea behind quick release couplings is to make the connection or disconnection with a minimum of effort and the least amount of process interruption. Normally, quick release couplings are designed to replace threaded or flanged connections for hydraulic tools.
A speed reducer works somewhat like a gear or ball screw device. The purpose of a speed reducer is to redirect the output of a high speed motor to a mechanism that operates at a lower speed. A set of gears in the speed reducer provide the necessary mechanism for the reduction in speed. The ratio of the input gear to the output gear is the reason for the exceptional performance of speed reducers.
A well-known form of power transmission mechanism is timing belts, which are used for power transmission where maintaining a drive ratio is important. Timing belts are the most widely used form of power transmission devices and are found in engines, large machinery, and stepper motors.
The safe and smooth transmission of power is an important part of the operation of machinery and vehicles. Power transmission devices provide the proper and safe ways to complete the exchange in an efficient and effective way.
Bearings are tools that allow for relative motion between objects that reduce the amount of friction between components in a system, which allows for heavier objects to be moved with less effort.
They provide smooth movement of parts or whole pieces of equipment; without these components, parts would wear out quicker and would require frequent maintenance or replacement.
Learn more about ball bearings.
Ball screws are products that are designed to convert rotational motion into linear motion.
This function allows for movement of parts and devices along a single axis. These come in different configurations such as ground ball screws, rolled ball screws, precision ball screws, and more. Learn more about ball screws.
Electric motors are used to convert electrical energy into mechanical energy. These motors are comprised of electric coils and magnets.
The electromagnetic interactions between the coils and magnets produce mechanical forces which can be utilized to power many different kinds of devices and machinery.
There are many different kinds of electric motors including DC motors, AC motors, universal motors, servo motors, stepper motors, linear motors, and many others. These different electric motors are used in a broad range of applications like in powering hard drives, household appliances, and power tools. Learn more about electric motors.
Friction materials are products used to slow or inhibit movement, and they are used in many different types of machinery to control or stop processes. The two main criteria for good friction materials are a high coefficient of friction and good energy absorption.
The coefficient of friction describes the roughness of a material, so a material with a high coefficient of friction is very rough and requires more energy to move along its surface. Frictional forces generate excessive heat, so it is also important that frictional materials be able to absorb this extra heat energy to prevent damage to the system. Friction materials are used extensively in braking and clutch systems which are essential in automotive equipment and industrial machinery. Learn more about friction materials.
Gears are devices used to transfer torque from one part of a mechanical system to another. Equally spaced teeth along the outside of the gear interlock with the teeth of other gears to transfer rotational motion.
There are many shapes, sizes, and types of gears, and each type serves different applications. Spur gears, splines, and planetary gears all utilize straight, axis-aligned teeth, while worm and helical gears have teeth that wrap around the axis like a screw. There are also conically shaped bevel gears which are frequently used as rear end gears in automobiles. Learn more about gears.
Quick release couplings are simple mechanical devices that permit easy and immediate connection or separation of fluid transmission lines with a minimum of stoppage time and spillage.
To make a complete coupling set, two parts must be used which are the male and the female connectors. Here the male connector fits perfectly into the female connector for a tight seal. Quick connectors or quick disconnects can also refer to couplings or fittings. Quick connect fittings replace threaded or flanged connections which require tools such as wrenches. Learn more about quick release couplings.
A shaft coupling is used to join two shafts together and to ensure that the two shafts rotate together.
Rigid couplings connect well-aligned shafts, while flexible shaft couplings are used to cancel out the misalignment between two shafts.
These components can also be used to absorb or reduce shock and vibrations. Some of the many different kinds of couplings include bellows couplings, flywheel couplings, jaw couplings, universal joints, fluid couplings, and torque limiters. Couplings are commonly used in power transmissions, generators, wheels, pumps, and turbines. Learn more about shaft couplings.
Speed reducers are used to redirect the output of a high-speed motor to another component at a lower speed. Gears within the speed reducer provide the mechanism for reducing the output speed of the motor.
The size ratio of the input gear to the output gear is directly related to the speed reduction, so different sized gears can be used to achieve different speeds. Speed reducers are know by many names and come in a variety of configurations. These include cyclo reducers, gear reducers, gearboxes, right angle gear boxes, and planetary gearboxes. Learn more about speed reducers.
Timing belts are used for power transmission or to interchange linear motion and rotary motion where maintaining a specific drive ratio or high loads are important.
They are most widely used in the regulation of internal combustion engine operation. Linear position systems are a common non-automotive application of timing belts.
In the context of internal combustion engines, timing belts are the component responsible for controlling the timing of an engine's valves. If tensioned properly, timing belts have no slippage and are used to transfer direct motion for timing or indexing purposes. Timing belts are utilized in the camshafts of automobiles and stepper motors. They began to replace engine timing chains in 1970s. One of the advantages of timing belts over timing chains and gears is that timing belts do not require lubrication. They are specially designed to precisely fit around the gears with which they operate. Their use helps to ensure the safe and efficient operation of important engine components. Though in recent years there has been a moderate resurgence of timing chains and other non-belting engine regulation components, timing belts continue to be the dominant utility for engine valve regulation.
In automotive applications, a timing belt is a reinforced rubber belt with square teeth driven by the crankshaft, which operates the camshaft. In some engine designs, timing belts are also used to drive other engine components such as the water pump and oil pump. Compared to a gear or chain system, rubber timing belts are more cost effective, quieter in their operation, and mechanically more efficient. Rubber timing belts can be made out of several different materials. Traditionally, rubber belts have been made out of natural rubber and integrated synthetic fibers for added strength. Natural rubber is not very heat resistant, though, and it can corrode in the presence of oil and other petrochemicals. For this reason, synthetic rubber materials like highly-saturated nitrile and other varieties have gained in popularity. Conveyor belt materials can be engineered to resist high heat and corrosion, which gives them a longer operating lifespan than natural rubber belts. Because of their importance in so many engine systems, timing belts are widely manufactured and are likely to continue to occupy a large percentage of all conveyor belt varieties produced annually. Learn more about timing belts.