Baler Machines
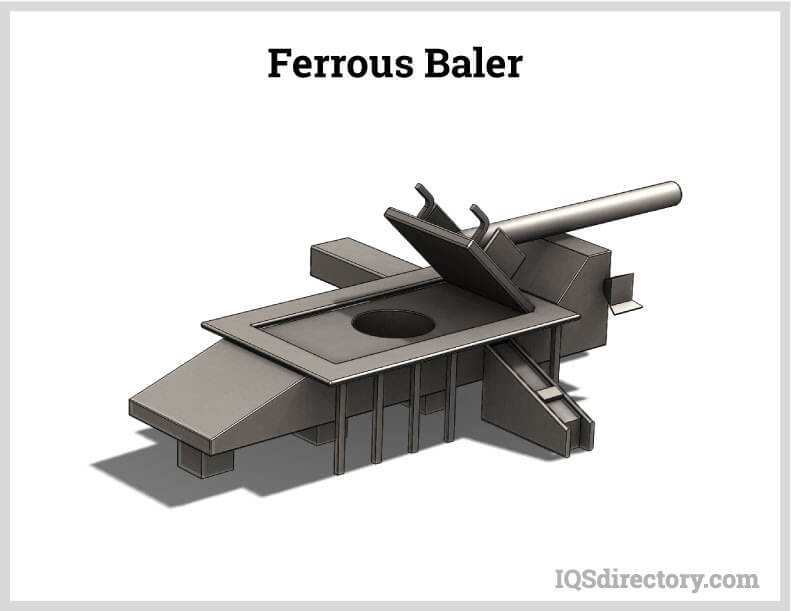
Keeping used materials out of landfills by repurposing them for new uses significantly reduces our environmental impact and conserves scarce resources. An efficient recycling process provides a streamlined solution for residential, commercial, and industrial locations to dispose of, sort, and reuse materials such as ferrous and non-ferrous metals, plastic and rubber, construction and demolition waste, wood, paper and cardboard, glass, and textiles.
The recycling journey begins with the collection of materials. Waste management companies gather recyclables from homes, dumpsters at commercial facilities like office buildings and warehouses, or industrial sites using specialized trucks. These collected items are then transported to a recovery center for further processing.
For larger recyclables, size reduction machines like shredders, pulverizers, and granulators break down materials into smaller, more manageable sizes. While some areas require pre-sorting of recyclables, many regions now accept unsorted materials to encourage recycling. Consequently, advanced separation technologies have been developed to ensure efficient and precise sorting. Vibratory feeders, for example, separate items based on weight, effectively removing heavier objects like metals and glass. Other separators, such as magnetic separators and screens, systematically sort materials into distinct groups.
By incorporating these processes, the recycling industry enhances the sustainability of material usage, fostering a greener future through innovative waste management strategies.
After the materials have been separated, additional processing is often required to prepare them for reuse. The next step involves putting these materials through a baling machine, which compresses them into manageable bales or blocks. These bales are then loaded onto trucks and shipped to factories where they are transformed into new products. For instance, a bale of crushed metal cans might be sent to a facility where the metal is melted down and molded into brand-new cans.
In mixed waste centers, waste must be separated from recoverable materials. Most facilities can recover about 30% of the material during this process, but the aim is always to increase that percentage.
When recycling industry experts refer to the "recovery rate," they mean the percentage of materials that can be recycled and kept out of landfills. While some waste will always be non-reusable, improving the recovery rate is essential for preserving the environment and conserving resources. Many people are unaware that plastic is a limited resource, despite its widespread use. This underscores the importance of recycling as much as possible to ensure sustainability.
Creating products from recycled materials consumes significantly less energy than producing them from raw materials. For example, manufacturing a plastic water bottle from recycled plastic requires 88% less energy compared to using entirely new plastic. Similar energy savings are seen with cardboard, wood, and glass products. Reusing materials is a straightforward and effective way to enhance efficiency and reduce greenhouse gas emissions.
In a single-stream recycling system, materials such as cardboard, glass, and plastic are collected together. This method is popular in residential recycling programs because it allows residents to mix their recyclables, eliminating the need for sorting at home. However, the challenge lies in sorting these mixed materials at the recycling facility. Due to the commingling of recyclables, efficient sorting and maximum material recovery become difficult. Studies have shown that single-stream recycling harms the environment by failing to leverage the efficiency of pre-sorted materials. As a result, many recyclables that could be processed end up as waste because the single waste stream is too complex to sort effectively.
To address this issue, many regions and facilities are adopting a dual-stream process. Dual-stream recycling involves keeping fiber components, such as paper and cardboard, separate from other recyclable materials. This method enhances the efficiency of the recycling process and ensures a higher recovery rate of recyclable materials.
The forefront of manufacturing and industrial operations today emphasizes investments in recycling equipment. With growing environmental awareness, an increasing number of producers are acquiring recycling equipment or seeking guidance from recycling equipment manufacturers. Industrial operations across various sectors are actively enhancing their environmental stewardship by developing processes and technologies aimed at the proper disposal of waste materials.
The rapidly expanding recycling industry continually refines and innovates new, more efficient processes for managing the millions of tons of waste generated by manufacturing and commercial activities. These methods are designed to efficiently reduce large volumes of waste into manageable sizes suitable for repurposing and reprocessing.
Central to waste management strategies is the initial reduction of waste using specialized equipment. Shredders, pulverizers, compactors, granulators, and balers employ hydraulic force to crush waste materials and eliminate air. This suite of equipment can effectively transform substantial volumes of trash and refuse into smaller, manageable particles and fragments.
The essence of recycling processes is to harvest waste materials and extract usable substances that can be reconstituted into raw materials for manufacturing. Achieving this involves a cohesive collaboration among recycling equipment components: breaking down waste, sorting reusable materials, and preparing them for shipment to be reincorporated into new products. Despite its apparent simplicity, this endeavor demands extensive engineering expertise at every phase.
The journey of recycling starts where waste originates—a familiar beginning for everyone: the moment waste is placed at curbsides for collection. However, this initial step represents only a fraction of the complete waste management cycle. Waste takes diverse forms, encompassing electronics, machinery, vehicles, appliances, textiles, paper, and aluminum cans, each presenting distinct challenges in the recycling process.
Certain types of waste, such as shredded plastic bottles, aluminum cans, clothing, and paper, are easily separated at disposal points and recycled. Public awareness of waste volume has grown recently, prompting manufacturers to comply with regulations by installing compactors and increasing collection frequency for efficiency. Post-collection, waste undergoes separation, starting with a vibrating conveyor line for smaller items and more intensive processing for larger materials.
Ferrous metals, heavier than other recyclables, are easily separated using large magnets positioned over vibrating conveyor feeders. Waste management engineers use this method to extract and process these metals into bales for further recycling.
As the recycling industry responds to increasing waste volumes and evolving product replacements, technological advancements in recycling methods have grown significantly. This trend is expected to continue, reflecting heightened industrial awareness of recycling benefits and driving ongoing improvements in recycling technology.
Balers compress materials to create uniform bales, facilitating efficient stacking and transportation. In recycling operations, sorted materials are fed into baling machines to form compact units. These bales, comprised of plastics or metals, are then shipped to manufacturers for melting and repurposing into new products.
Certain baling machines include a unique feature for moisture extraction, effectively eliminating any residual liquid traces. Materials like cardboard, plastics, and metals, which may have previously contained liquids, undergo thorough drying during recycling processes. This ensures that the bales exiting the facility are completely dry and ready for further processing.
To create a bale, a large volume of material is loaded into the machine's input area. From there, it enters a compression chamber where it undergoes crushing and shaping into a compact cube. While most balers operate on electricity, they harness hydraulic power for robust and consistent compression. Following compaction, wire or durable plastic ties secure the bale, ensuring structural integrity during handling. Certain balers offer flexibility to produce customized bale sizes. Due to their weight, forklifts are employed to lift and stack them or load them directly onto trucks for transport.
For manufacturers in industries reliant on recycled materials for new product creation, compact bales offer unparalleled convenience. These bundles can be stored for deferred processing and effortlessly transported throughout factories with the aid of forklifts. In the fast-paced environment of high-production facilities, the ability to melt substantial quantities of material at once optimizes operational efficiency to its fullest potential.
Learn more about balers.
There are several types of balers, including:
The vertical baler leverages a vertically oriented ram to meticulously compact recycled materials. Its design allows for versatile loading through a spacious front compartment that seals during operation, ensuring efficient use of space. Renowned for its compact footprint, this baler is not only cost-effective but also offers unparalleled flexibility. While it excels in cardboard baling, its capabilities extend to a wide array of recycled materials, customizable to meet precise specifications with ease.
Learn more about vertical balers.
Horizontal balers feature a horizontally moving compression ram, making them ideal for efficiently managing substantial quantities of materials. Unlike vertical balers, these machines excel in handling large volumes and can operate continuously, ensuring optimal throughput. They can be fed manually or integrated with automated systems like conveyors and feeders to maintain a steady flow of materials into the compression chamber.
Industries dealing with high-volume recyclables rely on horizontal balers for their superior material handling efficiency. These balers are versatile enough to handle a wide range of recycled materials, from paper to metals, meeting diverse recycling requirements effectively.
Learn more about horizontal balers.
A two ram baler revolutionizes horizontal baling with dual horizontally oriented rams instead of a single one. Featuring enlarged hoppers and robust feeding mechanisms, these balers ensure rapid material throughput into the compression chamber. The dual ram configuration efficiently compresses bulkier materials and larger volumes. In some applications, two ram balers eliminate the need for preliminary shredding or pulverizing. Overall, they enable recyclers to manage higher material capacities at faster speeds. It's important to consider that the dual ram design requires sufficient space and increased power.
Compactors streamline waste and scrap compression for easier transport and enhanced space efficiency. Industries like food processing, manufacturing, retail, and automotive sectors all realize environmental and economic advantages through reduced trash volume, cutting disposal costs and efforts.
Compactors play a crucial role in waste reduction, particularly for non-recyclable materials, aimed at conserving landfill space and optimizing trash disposal efficiency. They are typically smaller than industrial balers and produce tightly compacted waste bundles. Various types include residential, commercial, and industrial trash compactors, as well as those integrated into garbage trucks for space conservation, and specialized compactors for specific materials like textiles, food products, containers, metals, plastics, and fibrous materials. However, hazardous materials such as aerosol cans, batteries, and chemicals require specialized disposal methods. Compactors contribute significantly to reducing the carbon footprint of industrial operations, aligning with recycling efforts essential for sustainable manufacturing practices.
A compactor comprises a large chamber, an electric motor, and either a hydraulic or pneumatic press as its core components. Industrial models feature manual or automated loading systems with expansive input areas capable of handling large volumes of waste. Within the chamber, waste materials undergo compression under high pressure from the press. Hydraulic presses minimize energy loss and reduce machine heat during operation.
Industrial compactors typically produce compacted bales, while commercial or residential units often utilize bags or bins for storing compressed waste prior to disposal. Once compressed, materials are ready for transport to disposal sites or recycling facilities for reuse. Facilities such as factories, hotels, schools, medical centers, and manufacturing plants commonly integrate compactors onsite to streamline access and lower transport costs.
While initial costs for compactors may appear significant, their benefits are numerous. They mitigate odor and vermin issues, decrease the frequency of waste removal, prevent spills and leaks from overflowing containers, and enhance facility cleanliness standards.
Learn more about compactors.
Granulators are specialized machines designed to reduce substances into granules. What distinguishes granulators from other size reduction equipment like shredders or grinders is their capability to break down large components into much smaller particles than grinders can achieve. Typically, granulators feature an open rotor configuration that facilitates efficient air circulation for cooling the processed material. However, closed rotor granulators, operating at high speeds, are also available. The output from granulators is typically ground to a consistency resembling corn meal or finer, with grain sizes ranging between 0.2 and 4.0mm.
There are two primary methods of granulation: wet granulation and dry granulation. Wet granulation involves the formation of granules by pouring a granulating liquid onto a powder bed and mixing it using impellers, screws, or air agitation. This process combines the liquid and powder to form wet granules. Commonly used liquids include water, ethanol, and isopropanol, with aqueous solutions generally considered safer to handle compared to solvent-based solutions.
Dry granulation involves forming granules without using liquid, preferred for products sensitive to moisture and heat. This process utilizes a compactor to create granules without moisture. Granulators play a crucial role in recycling, particularly for lighter materials such as plastics and rubber, which do not grind effectively.
Learn more about granulators.
In recycling and recovery plants, scrap and waste materials are typically stored in large piles for future processing. Grapplers are widely utilized in these facilities to efficiently transfer these materials into processing equipment such as material separators, shredders, and balers. They excel in handling large quantities of scrap, facilitating seamless integration into the recycling and recovery processes.
A grappler is a versatile piece of material handling equipment designed for lifting and maneuvering large quantities of scrap materials. Typically attached to the extended boom or arm of heavy mobile machinery, such as a backhoe, grapplers come in various forms. One of the most prevalent types is the claw grappler, characterized by its curved metal arms resembling claws. Operated by a controller, the claw can be opened and closed to grasp and release loose materials. In recycling plants focusing on metal handling, it's common to employ a scrap handling magnet instead of a claw grappler, leveraging magnetic force to efficiently lift scrap metal.
Grapplers utilize hydraulic or electric power to operate their lifting mechanisms, requiring robust arms capable of securely grasping and lifting heavy materials commonly found in debris. They are typically available as attachments for backhoes or similar heavy equipment, offering flexibility that helps maintain cost efficiency for recycling facilities needing to manage large volumes of recycled materials. Alternatively, grapplers can be integrated into dedicated material handling vehicles designed by manufacturers specifically for use in recycling operations. These vehicles are equipped with stabilizers to ensure stability when lifting heavy loads, enhancing safety and operational effectiveness.
Learn more about grapplers.
Industrial metal shears are employed for cutting sizable metal pieces, especially sheet metal. These machines slice the metal into narrow strips as it is fed through, transforming it into numerous smaller pieces suitable for transportation, recycling, and reuse in manufacturing.
Some shearing machines operate through manual foot pedal pressure, while others use hydraulic or mechanical power. These machines feature sectional knives or sliding blades that effectively cut sheet metal by applying downward force. Cutting operations are not always conducted at perfect 90-degree angles, as diagonal cutting requires less force. Consequently, many metal shears are equipped with angled blades to optimize cutting efficiency.
Metal is fed into the shearing machine from the shear table, which serves as the machine's work surface. This table provides support as operators carefully feed the metal into the machine for cutting. While some metal shears are mobile for use in scrap yards or large recycling facilities, others are stationary and integrated into comprehensive recovery processes.
In metal fabrication shops, large sheet metal pieces are often sourced directly from suppliers who have reclaimed it or no longer require it themselves. Workers use metal shearing machines to trim edges and cut the metal to project specifications, a cost-effective alternative to purchasing new metal entirely for manufacturing purposes.
Certain metal shear machines are integrated into large industrial balers, enabling continuous shearing and baling on a large scale. This process ensures metals are consistently sized, ideal for creating uniformly shaped and sized units for efficient shipping.
Learn more about metal shears.
Material separation is a crucial initial stage in the recycling process. Efficiently recovering products from the waste stream and ensuring their correct categorization for recycling is challenging yet essential. Recycling facilities continually strive to increase their recovery rates to minimize landfill waste and reduce energy consumption through the production of new goods from recycled materials. Properly calibrated separation equipment tailored to specific applications significantly enhances recovery rates. While manual separation by workers is possible for some materials, machine-assisted separation proves far more effective, especially when managing large volumes of materials.
As technology advances and recovery centers prioritize increasing their recovery rates, more materials are being diverted from the waste stream for repurposing. This reduces landfill impact and promotes a more sustainable approach to environmental stewardship. Material separation equipment plays a pivotal role in optimizing the efficiency and effectiveness of this process.
Technology has led to many innovative separation tools and techniques, but here are the main tools:
Magnetic separators separate ferrous materials from non-ferrous substances by subjecting unsorted material to a powerful magnet mounted over a conveyor belt or within a chamber. The magnet attracts ferrous metals, which are then extracted, leaving the remaining materials unaffected. This equipment is highly advantageous in metal recycling facilities, ensuring continuous material flow in scrap yards and other high-volume environments.
Learn more about magnetic separators.
An air separation unit efficiently extracts lightweight debris and low-value materials from a recyclable waste stream. Typically, high-pressure air is directed over the conveyor's drop-off point, causing heavier materials to drop onto the next conveyor, while lighter materials are directed into a designated bin or repository. Alternatively, some units employ vacuum or cyclone technology to extract lightweight, non-metallic materials from the waste stream.
An eddy current separator is a sophisticated piece of equipment designed to extract non-ferrous metals such as aluminum and copper from waste streams. Using a powerful magnetic field, it induces an opposing magnetic field in non-ferrous metals, repelling them from the waste stream. Unlike magnetic separators that attract ferrous materials, the eddy current separator is placed at the end of a conveyor to divert non-ferrous metals into a dedicated bin, while other materials continue onto a separate path. It is crucial to remove all ferrous metals from the waste stream before using the eddy current separator to prevent operational issues.
A scrap handling magnet functions like a grappler but employs electromagnetic force to attract and secure objects rather than mechanical force. It consists of an electromagnet attached to a chain at the end of a hydraulic arm for maneuverability. Typically round in shape, these magnets vary in size and are encased in a robust metal body for protection and stability during operation. Capable of lifting thousands of pounds, they are essential in metal recovery facilities.
Screeners provide a meticulous method for sorting mixed recyclables, operating through various types of screens. Unlike other separators, they rely on mechanical means for material separation. Available in diverse styles and sizes tailored to specific applications, screeners play a crucial role in recycling. Below are several types commonly used:
A widely used screening device is the vibratory screener. Recyclable materials are introduced onto the screen surface of the machine, where continuous vibrations agitate them. This agitation effectively separates smaller components from the main bulk of recyclables, allowing them to pass through the screen into designated bins or continue through the recycling process. This method is highly efficient for size-based material separation, reducing processing time and energy consumption by isolating smaller pieces that require less handling.
Learn more about vibratory separators
Rod deck recycling screens are a specialized variant of vibratory screeners, featuring multiple rows of rods instead of a traditional grid screen. Similar to standard vibratory screens, these machines utilize vibrations to agitate materials fed onto the rod deck, facilitating the separation of smaller particles from larger ones. However, rod decks excel in handling wet, abrasive, heavy, and challenging materials due to their design. The flexibility and reduced surface area of the rods prevent material adhesion and blockages, enhancing operational efficiency in various recycling applications.
A disc screener consists of rotating discs arranged along a rod. Materials pass over these discs, allowing smaller particles to fall through the gaps. The rotation ensures that smaller bits fall through after traveling a short distance. This setup is especially effective in recycling plants where disc sizes can be tailored to specific materials, enhancing recovery rates.
A star screener operates like a disc screener, but uses star-shaped components instead of discs to screen materials. These stars, mounted horizontally, efficiently pull in and separate fractured, damp, and cohesive materials. The screen's rotation speed can be adjusted depending on the specific materials processed at the recycling facility.
Shredding equipment is indispensable in recycling operations, effectively reducing tough materials into smaller fragments before they are baled or transformed for reuse. Shredders are diverse, designed for various materials like rubber, plastic, and metal, each necessitating specific sizes and types of machinery. Manufacturers cater to different industries by creating shredders tailored to their unique requirements; for instance, document destruction demands lighter-duty machines compared to heavy-duty models used in metal processing. The recycling of electronic scrap has surged due to the proliferation of obsolete electronic devices, highlighting the need to dismantle and recycle their components efficiently.
Shredders operate similarly despite variations in design. They consist of interlocking metal shafts fitted with discs bearing sharp teeth at regular intervals. Positioned at the bottom of a hopper, these shafts are powered by a motor to rotate. As objects are fed into the shredder, the teeth on the discs grab and pull them between the shafts, breaking them into small pieces. The shredded materials exit at the bottom into a bin or onto the facility floor for further processing or disposal.
Shredders vary in design to accommodate different tasks: single-shaft models handle smaller materials and light duty tasks, while models with up to four shafts tackle heavy duty applications such as shredding tires. This capability enhances recycling efficiency and reduces costs by breaking down bulky materials quickly. Shredders play a crucial role in recycling processes, enabling the reuse of materials that would otherwise be difficult to process. Explore more about industrial shredders for further insights.
Size reduction equipment encompasses a range of machinery designed to decrease the dimensions of materials. This technology has a rich historical lineage, originating from ancient times when rudimentary tools such as stones were employed to fragment large substances into smaller units. Over time, these devices have evolved significantly, becoming integral to modern industries including mining, food processing, and chemical manufacturing.
Learn more about size reduction equipment.
A vibratory feeder, also known as a vibratory conveyor, is specialized equipment designed to transport bulk materials through various stages of a process such as packaging, recycling, or finishing using controlled vibrations. Unlike traditional belt, screw, and pneumatic conveyors, vibratory conveying is particularly suitable for handling sticky or delicate materials without causing damage or liquefaction.
Vibratory feeders are highly advantageous for material handling due to their low-maintenance nature. They feature minimal moving parts, with the vibrating drive situated beneath the feeder pan to avoid interference with the materials being transported. Other components of a vibratory feeder are both cost-effective and easy to replace.
These feeders can be powered either electromagnetically or electromechanically. Electromechanical vibratory feeders utilize a motor supported by eccentric weights or an eccentric crank to generate the necessary vibrations for material movement.
Several main types of vibratory feeders exist. Vibratory bowl feeders, also known as centrifugal feeders or vibratory bowls, align finished or semi-finished parts for packaging in parts manufacturing. Vibratory conveyors cover a broader range, including troughs, trommel screens, and vibrating screens, designed to convey and sort bulk materials. Rotary feeders, also known as rotary valves or rotary airlocks, transfer airtight bulk material to vibratory or screw conveyors. Linear feeders, or inline feeders, transport parts from bowl feeders in a vibratory linear motion over short or long distances.
Vibratory bowl feeders are used by small parts manufacturers to efficiently orient products for distribution or subsequent finishing processes. Initially developed by pharmaceutical companies for sorting, counting, and organizing pills, these feeders have evolved to handle a diverse range of items including toothpaste caps, molded rubber parts, o-rings, ammunition, and fasteners.
Many industries, including food processing, agriculture, and pharmaceuticals, actively utilize vibratory conveyors, screens, and trommels to handle bulk and powder materials. Recycling industries rely on vibratory conveyors to sort and convey materials such as metals, crushed cement, wood, and plastic. Mining, pulp, sand and gravel, and fertilizer companies employ vibrating screens and trommel screens to sort, sift, and convey their materials. The mining industry predominantly uses grizzly screens, which are powerful types of vibrating screens. Vibratory conveyor systems often collaborate with rotary airlock feeders for conveying powder bulk solids. Additionally, in dust reclamation or collection processes, rotary feeders and dust collecting systems work together effectively.
Bowl feeders, similar to vibratory finishing bowls, are typically made of plastic, silicone, or metal. These machines feature a vibrating drive mounted at the base of the bowl. A ramped ridge, specifically designed for a particular part, guides it towards the outfeed area in a spiral along the bowl's edge. The bowl vibrates in a circular motion, moving the parts up the spiral ridge. As parts reach the output area, the ridge narrows, ensuring they form a single-file line. Small items like coins, LEGO bricks, O-rings, and washers can be easily aligned for packaging and counting when placed into the center of the bowl feeder.
Vibratory conveyors use directional vibrations to move heterogeneous mixtures or powdered bulk solids between equipment pieces. Some variants of these conveyors feature ultra-low vibrations, making them suitable for handling sticky, delicate, or easily liquefiable solids like lettuce or gummy bears. Trommels, also known as trommel screens, vibrate to separate small and large particles effectively. They find applications in recycling and gravel processing. Trommel magnets assist in separating ferrous from non-ferrous materials, commonly alongside rotary trommels in metal recycling operations. Continuous flatbed trommels incorporate filtering devices or screens to sort particles by size. They direct larger particles for further processing or containment as needed.
Learn more about vibratory feeders.
A commonly used screening apparatus is the vibratory screener. Recyclable materials are introduced into the screener and pass over a vibrating screen. The machine continuously generates vibrations within the screen, causing the recyclables to agitate. This agitation dislodges smaller components from the bulk of recyclable material. These smaller components either pass through the screen into a designated bin or proceed further in the recycling process. Such screeners are highly effective for segregating materials by size. By isolating smaller pieces early on, which typically require less processing compared to larger materials, this method conserves both time and energy in the recycling process.