Noise Control Products
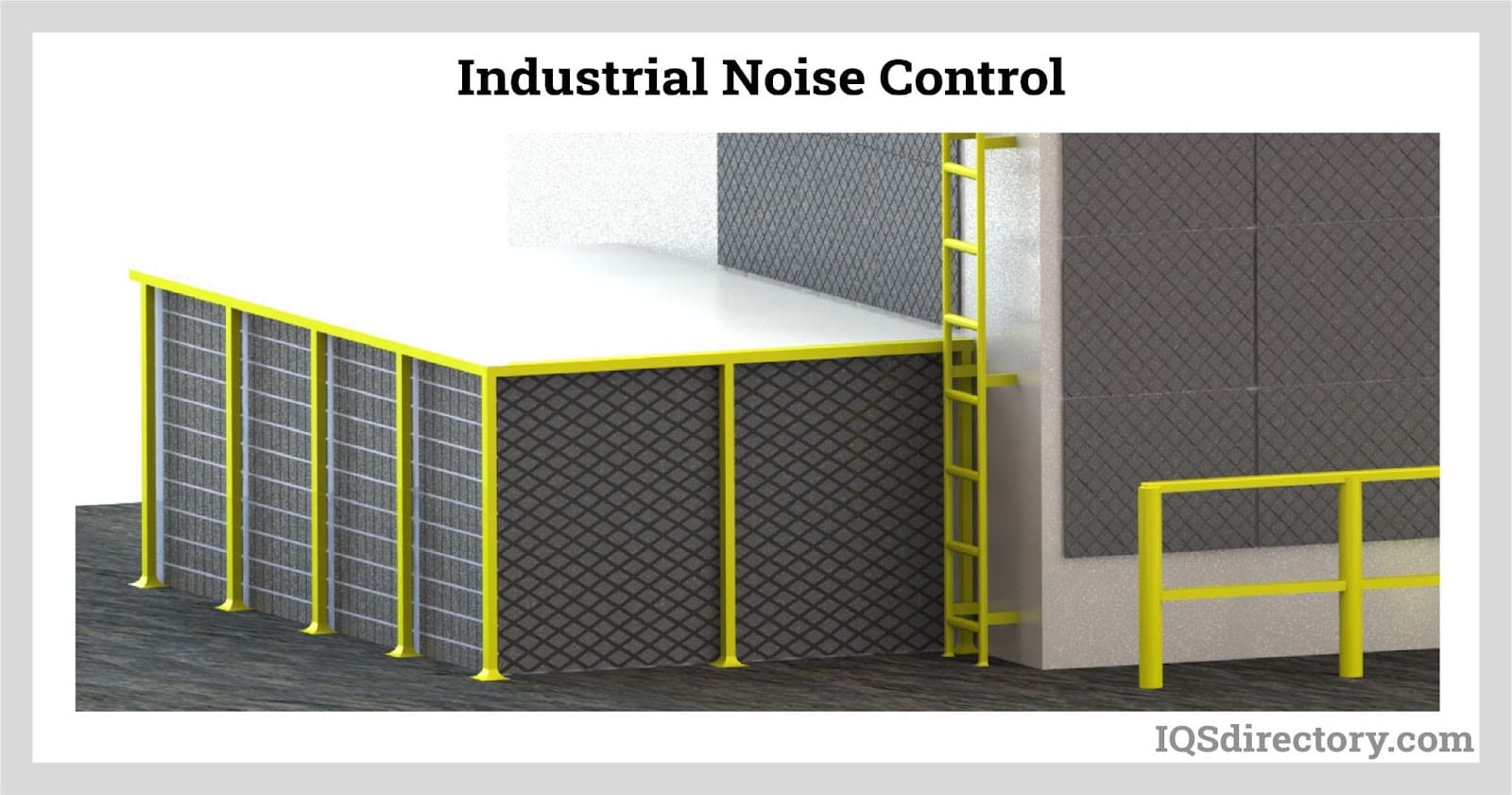
A primary responsibility of any industry is to ensure the safety and welfare of their employees. Though there are laws to protect workers, the main reason to keep employees safe is to be able to maintain production and avoid the need for constant retraining. Research has proven that keeping employees safe and happy enhances their performance and leads to greater productivity.
There are several measures available for companies to guarantee a safe and protected workforce from creating the right atmosphere to cleaning measures and protective guards. Each piece of safety equipment is devised and designed to fit the conditions and offer peace of mind as well as build worker confidence.
Many members of the American workforce are exposed to potentially damaging noise levels each year. This can be in a factory, group work, at an airport, or using various types of equipment. In the majority of cases, these harmful sounds can be controlled with various forms of soundproofing, which act as a silencer, muffler, and insultation.
Sound suppressing materials can be installed in any type of conditions where excessive noise is present. Acoustic or sound insulation is flexible enough to be placed in any space for blocking and suppressing unwanted noise. When a pump is producing too much noise and interrupting operations, acoustic insulation can be formed, shaped, and configured to control and block the noise.
What may be considered to be normal and acceptable levels of noise may be irritating and cause discomfort. The determining factor regarding the need for soundproofing is the level of decibels (dB) that the noise produces. Decibels levels between 85 dB to over 140 dB need to be controlled and suppressed with soundproofing materials.
Since the beginning of the industrial revolution in the 19th Century, there has been a continuing effort to provide protective guards for equipment for machines and workers. Though the main function of machine guards is to keep workers from harm, they also serve a secondary function of protecting equipment from damage from passing vehicles or falling materials.
Machine guards can be shaped to fit any type of equipment from small floor motors to large cranes. The design and shape of machine guards is dependent on the type of machine. Engineers and designers are continually perfecting and developing materials and configuration for every industry.
As with other forms of safety equipment, machine guards serve several purposes aside from their primary function for protecting workers. Having a machine enclosed with rails, coverings, and shelters offers peace of mind to the operators so that they can perform their duties with ease.
One of the problems for industries that install fasteners where there are significant vibrations is the fasteners coming loose, which can be unsafe and hazardous. In an effort to prevent loosening, designers have developed safety cables that connect the fasteners and keep them in place. These safety cables can be connected by being wound around the fastener or threaded through holes in it.
Industries that rely on safety cables are the aerospace and aircraft industries where engines produce significant long term vibrations. Though the first efforts designed for safety cable installation were not completely successful, manufacturers have improved their methods to provide materials and connectors that secure fasteners and prevent hazardous conditions.
The importance of safety equipment has been a growing concern since the industrial revolution. Manufacturers and designers are constantly developing new methods to protect equipment, secure devices, and create a pleasant and safe working environment.
Soundproofing is the process of reducing unwanted noise and noise pollution, and in preventing noise from entering or leaving specific areas.
Soundproofing materials and products act as silencers, mufflers and insulation, absorbing the excess sound level in rooms, chambers and around pieces of equipment in order to create quieter environments for the purposes of worker safety, product testing, audio mixing and research etc.
Learn more about soundproofing.
Machine guards are mechanisms that act as safety barriers between workers and machines used in factories, manufacturing facilities, warehouses and plants.
In addition, machine guards control traffic, keeps vehicles out of certain areas and contain flying debris.
Almost all machines need safety guards. Any type of machine that shears or impacts, has meshing gears, rotating parts, reciprocating arms, cutting teeth or moving belts, or has the potential to be hazardous must have a safety barrier of some kind.
Presses, milling machines, automated assembly line machinery, roll form machines, robotics, saws and feeders, among others, have potentially dangerous components that require a machine guard to operate safely. Machine safeguards are crucial to these types of machines because they prevent crushed fingers or hands, loss of limbs, burning, blindness, or death. More and more often, machines are manufactured with integral machine guards, but some need to be analyzed before the proper user-built guard can be installed on the point of operation. Robots also need proper machine guarding. Learn more about machine guards.
One of the problems in the operation of equipment in the aerospace and aircraft industries is vibrations that can loosen fasteners, which can be a severe safety hazard.
Although fasteners may be mechanically tightened to ensure they are held in place, there is always, especially with the stress that aircraft has to endure, the chance of a connector coming loose.
The first attempts to prevent the loosening of fasteners was the installation of safety wires. Several problems arose from this method, which included the wires breaking or being unable to keep the fasteners secure enough to stop them from loosening. The wires had to be constantly inspected and changed multiple times causing delays and unnecessary repairs. Learn more about safety cables.
Sewing contractors manufacture products and provide services for a multitude of industries and applications.
This trade employs simple and complex machines that are capable of producing high quality custom embroidery and large-scale manufacturing. Companies contract production out to industrial sewers for a wide variety of products found in nearly every business or home. They manufacture a plethora of textiles including covers, fabric enclosures, uniforms, and carrying cases.
Many types of fabrics are used by sewing contractors. Vinyl-coated nylon is a lightweight, durable material that is a popular choice for bags, presentation cases and protective covers, as it is tough and weather resistant. Neoprene and Hypalon are chemical and abrasion resistant and are used in industrial applications. Canvas, which is comprised of twill, soft flannel and felt, is a breathable material used for bags and curtains, as well as many industrial applications. A sewing contractor uses a variety of anti-static materials for products in the computer and electronics industries. Other materials include suede, leather, felt, webbing, plastic, cotton and polyester. These fabrics are often custom embroidered, which is a decorative embellishment made by stitching thread by a needle. They are graphic or descriptive text and images, and they are often used by companies and businesses that want to print their logo on their products and employee uniforms. Clothing labels are attached inside of all garments, bedding, textiles and clothing that are sold commercially. These tags contain information that lets the consumer know where the product was made, the materials it is made out of, washing instructions, and they often have a brand name, logo and garment size. These tags may be woven, embroidered or printed and made of satin, damask or taffeta.
Sewing contractors offer different services, such as free prototypes, custom fitting, custom embroidery and producing and attaching clothing labels to commercially-sold products. A variety of fabric products are produced by sewing contractors, including custom bags such as canvas bags or pouches, soft luggage and protective covers such as tarps. Many sewing contractors manufacture items for the aircraft industry such as seating, carpet, blankets and ground service covers. Banks, retail stores, amusement parks and insurance businesses use security, transit and courier bags; restaurants use umbrellas, slip covers, window treatments and booth cushions; and contract sewing is also used by the military, hospitality, transportation, casino and healthcare industries. Equipment used in contract sewing ranges from single needles to computer programmable machines. Auxiliary equipment includes riveters, stud setters, zipper fabricators, grometters, strip cutters, snap setters and heat and bag sealers. Learn more about sewing contractors.