Metal Moulding
Moulding, in its simplest terms, is creating an object out of a malleable material. The moulding technique is not a modern invention. While looking at the history of the moulding process, we can see that the Greeks were the first civilization to use architectural wood mouldings to accentuate their buildings solely for aesthetic reasons. The use of metal in the moulding process has been one of the big leaps of modern development as this process has led to the creation of unique and critical products. Since this process is relatively easy and waste-free, metal moulding has been employed to create items ranging from decorative ornamentation to a variety of critical items that society relies on every day such as various medical equipment and automotive components.
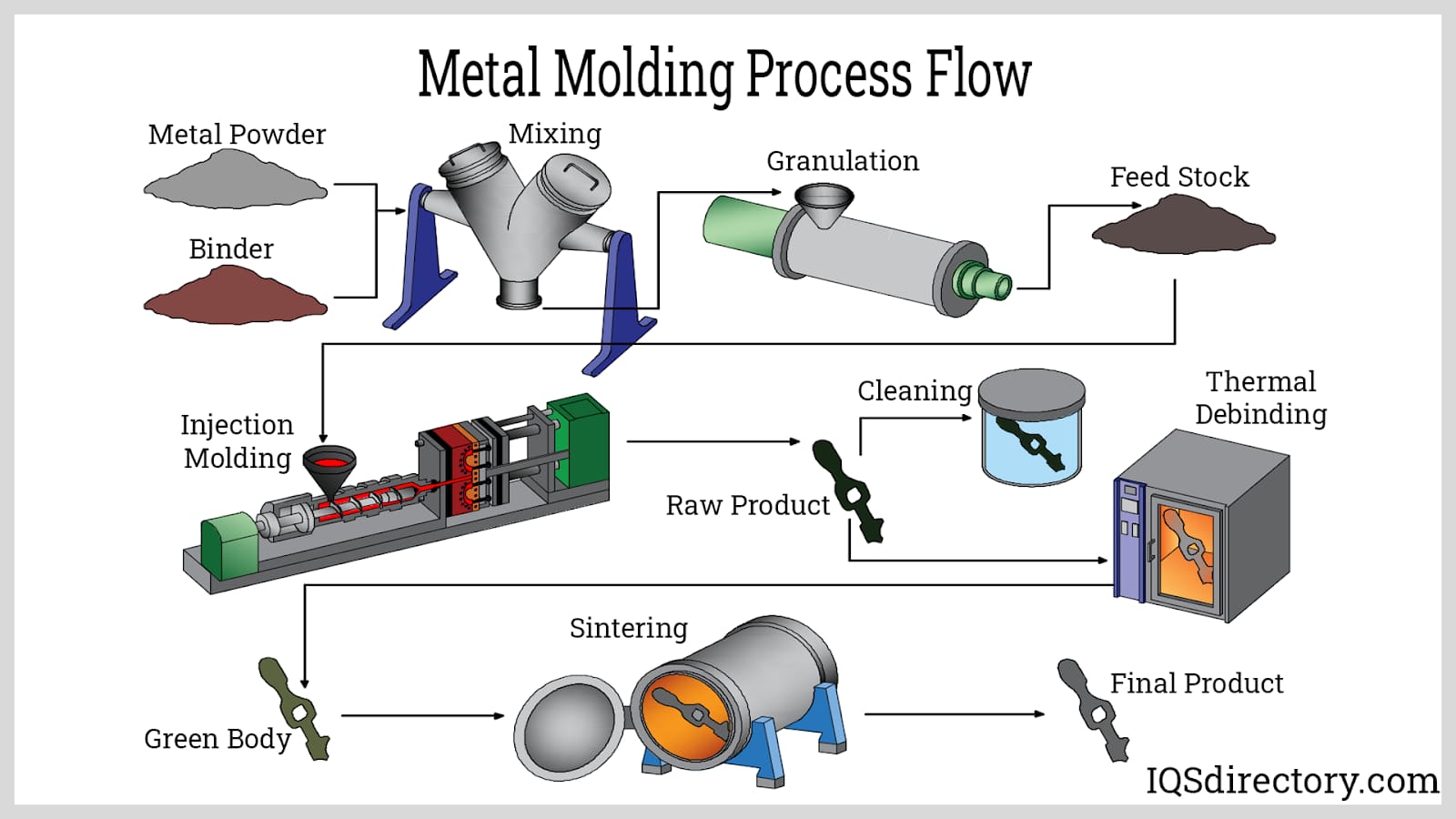
Quick links to Metal Moulding Information
What is Metal Moulding?
Metal moulding is a variation of conventional plastic injection moulding that makes it possible to fabricate solid metal pieces. The feedstock, or raw material, in this process, is a metal and polymer powder mixture. Because of this, metal moulding is also known as powder injection molding (PIM). The powder is first melted and then injected into a mould using a typical injection moulding process, where it cools and hardens into the shape of the desired object. After additional heating procedures are used to remove any remaining undesired polymer binding, a high-density metal component is created.
Only weights of 100 grams (less than a quarter pound) or less are allowed to be inserted into a mould at a time when the products are being made, though each "shot" may go into more than one cavity. As a result, the cost of producing each small item is reduced because large quantities of small objects can be produced at once.
Types of Metal Moulding
There are three categories of metal moulding based on the type of mould being employed for the process:
Permanent Mould:
Permanent metal moulding, also known as non-expendable mould casting, makes use of permanent moulds that are utilized throughout the course of production. Permanent mould casting can only make simple castings because the mould needs to be opened in order to remove the castings, even though it generates repeatable parts because the same mould is reused.
Expendable Mould:
When using an expendable mould, the foundry breaks the mould to release the casting, producing the finished item in its place. These moulds are frequently made from materials like sand, clay, and plaster. Binders, referred to as bonding agents, are frequently used to enhance the properties of disposable moulds. Casting with disposable moulds is used to create intricate, complicated shapes.
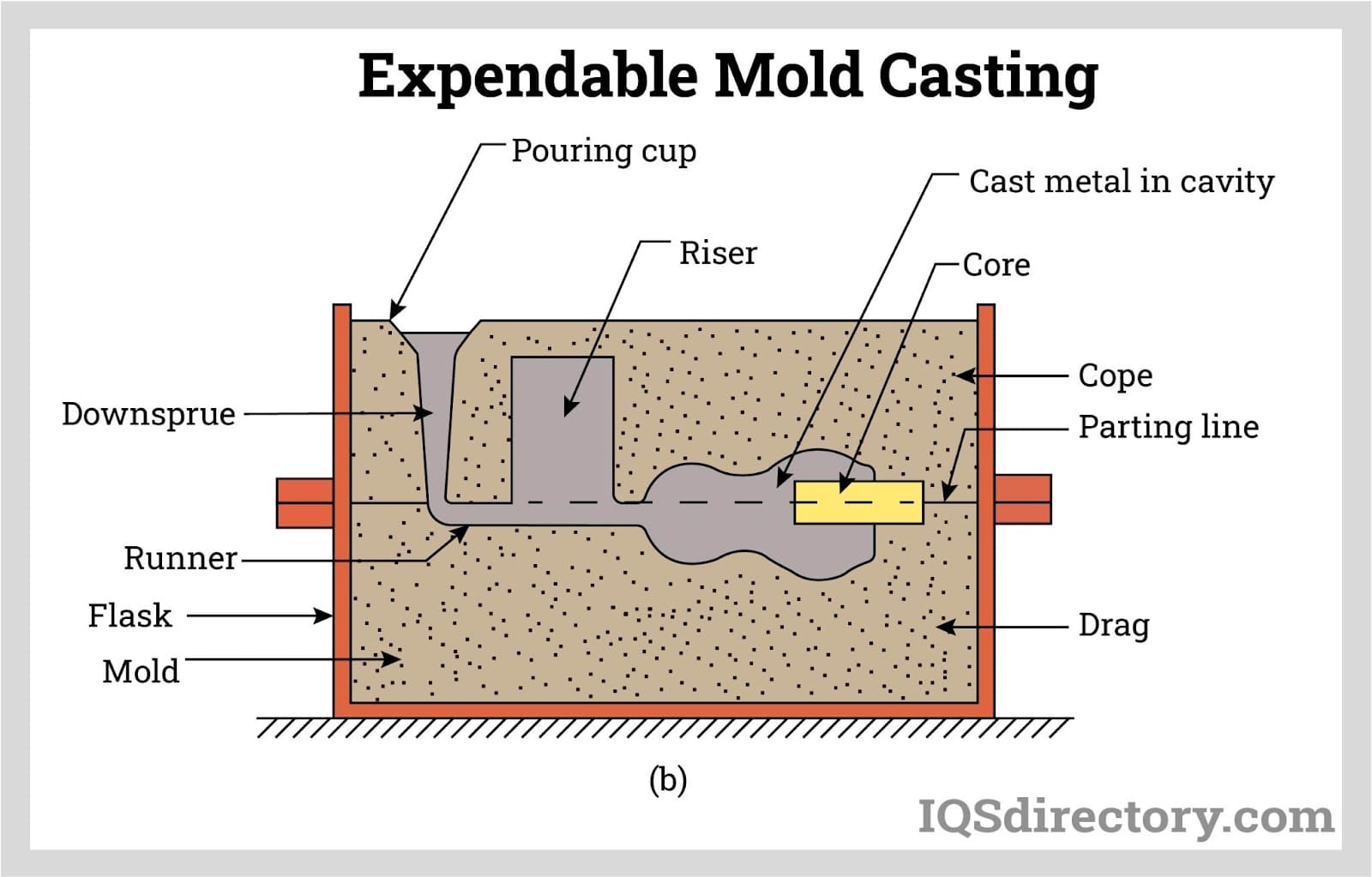
Composite Mould:
As the name implies, these castings use both disposable and recyclable moulds. These moulds frequently consist of substances like sand, wood, metal, and graphite.
Important Considerations in the Metal Moulding Process
Even though the metal moulding process is similar to the plastic moulding process, there are still some important factors to consider, including:
Wall Thickness:
Wall thickness should be kept to a minimum and consistent throughout the product, just like with plastic injection moulding. It is important to remember that in the MIM process, reducing wall thickness not only cuts down on material volume and cycle time, but also cuts down on the time needed for debinding, where any remaining material used to bind the metal powder together is removed, and sintering, where the metal mixture is heated to form a solid material.
Support in Sintering:
Metal moulding components must be adequately supported during sintering to prevent distortion from the resulting shrinkage process. Standard flat support trays can be used if parts are designed with flat surfaces that are all on the same plane. If not, more costly specialized support might be needed.