Multistage Exhausters
Maintaining a clean air environment is crucial for workers' health. To ensure these proper conditions, exhaust systems are used to remove unpleasant odors, vapors, and chemicals. The central feature of an exhaust system is a multistage exhauster designed to remove contaminated air. Exhausters can be simple devices with a single impeller capable of moving a limited volume of air. For larger volumes of air, complex exhausters have multiple impellers and a sophisticated structure.

Industrial multistage exhausters operate like multistage blowers and are designed to move and remove air and gasses and assist in various manufacturing processes. The inlet of a multistage exhauster draws in air or gasses and passes it on to the first stage of the multistage exhauster system, which consists of an impeller.
The popularity of multistage exhausters is due to their reliability, toughness, and ability to operate in all types of conditions. Unlike multistage blowers, multistage exhausters perform the function of a vacuum that cleans the air or removes unwanted contaminants.
Quick links to Multistage Exhausters Information
Components of Multistage Exhausters
The main components of a multistage exhauster are its inlet, outlet, motor, and impellers. How these pieces are assembled depends on the manufacturer and the size of the exhauster. In all cases, the purpose of a multistage exhauster is to remove contaminated gasses and air or separate desired gasses.
Benefits of Multistage Exhausters
Multistage exhausters are necessary for industries that produce significant quantities of toxic, harmful gasses and air. For example, in the production of biogas, they are used to extract gas from sludge such that it can be purified and turned into biogas. Multistage exhausters can have a pressure rating of up to 1.7 bar or 25 psig with a flow rate of 68,000 m3 per hour. A wide assortment of industrial and commercial operations depend on multistage exhausters as an essential part of their applications.
Safety
Multistage exhausters can operate at 120 °F (50 °C). They have high-quality and durable stainless steel shafts with housing or casings made of iron coated for protection against corrosion and atmospheric dust.
Efficiency
The major selling point for multistage exhausters is their efficiency. Their simple mechanism requires little maintenance, making them capable of continuous operation. This particular factor limits repairs and lowers operational costs.
Reliability
In most cases, multistage exhausts must operate in harsh and risky conditions. However, the well-engineered components of multistage exhausters make them capable of enduring the most hostile environments.
Flexibility
The adaptability of multistage exhausters makes them able to be designed, engineered, and configured to fit the needs of any operation. From exhausters with two impellers up to ones with ten impellers, multistage exhausters can be manufactured to meet any industrial conditions.
Cost Savings
Although safety is a major concern for industrial equipment, the first consideration during the planning phase is cost, which limits the available choices. For example, the initial cost of a multistage exhauster may be high. However, cost savings are realized during its operation, which can be continuous for hours over the years with little maintenance.
Impellers
One of the main characteristics of a multistage exhauster is the number of its impellers, which can be from two to ten. The multiple impellers allow a multistage exhauster to have higher pressure capabilities.
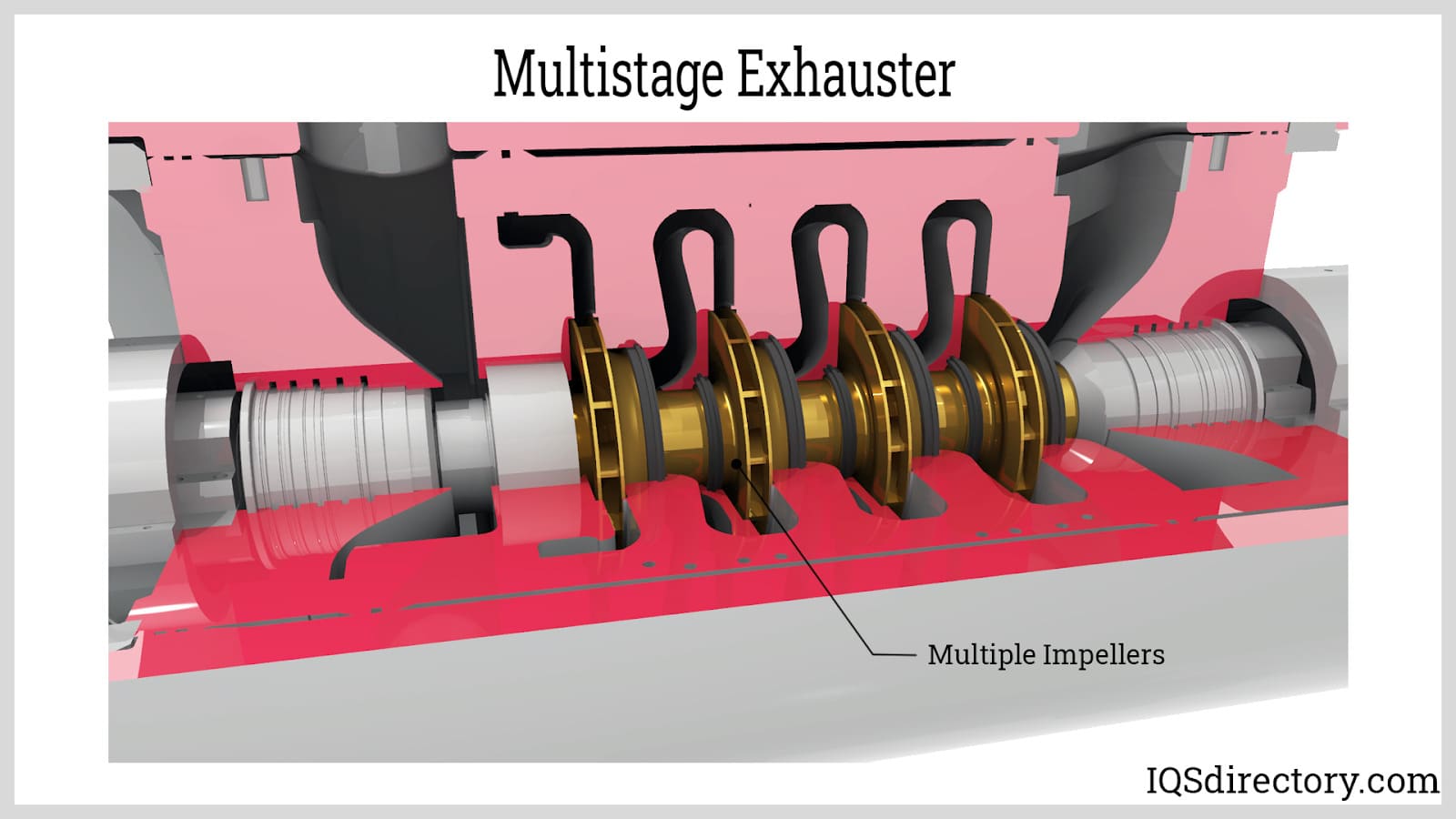
The types of impellers are open, semi-open, closed, vortex, and cutter. Closed impellers or shrouded impellers have their blades covered on both sides. They are the most common type of impeller used in multistage exhausters because they can withstand high pressure and constant use.
Casing
The casing is the housing for a multistage exhauster. It encloses the impellers and the shaft and protects it from the elements. Casings are tightly sealed to prevent contaminants from entering the exhauster and interfering with its operation. It is essential that the casing be able to withstand the pressure created by the motion of the impellers. Most casings are cast iron with steel rods connecting the various sections.
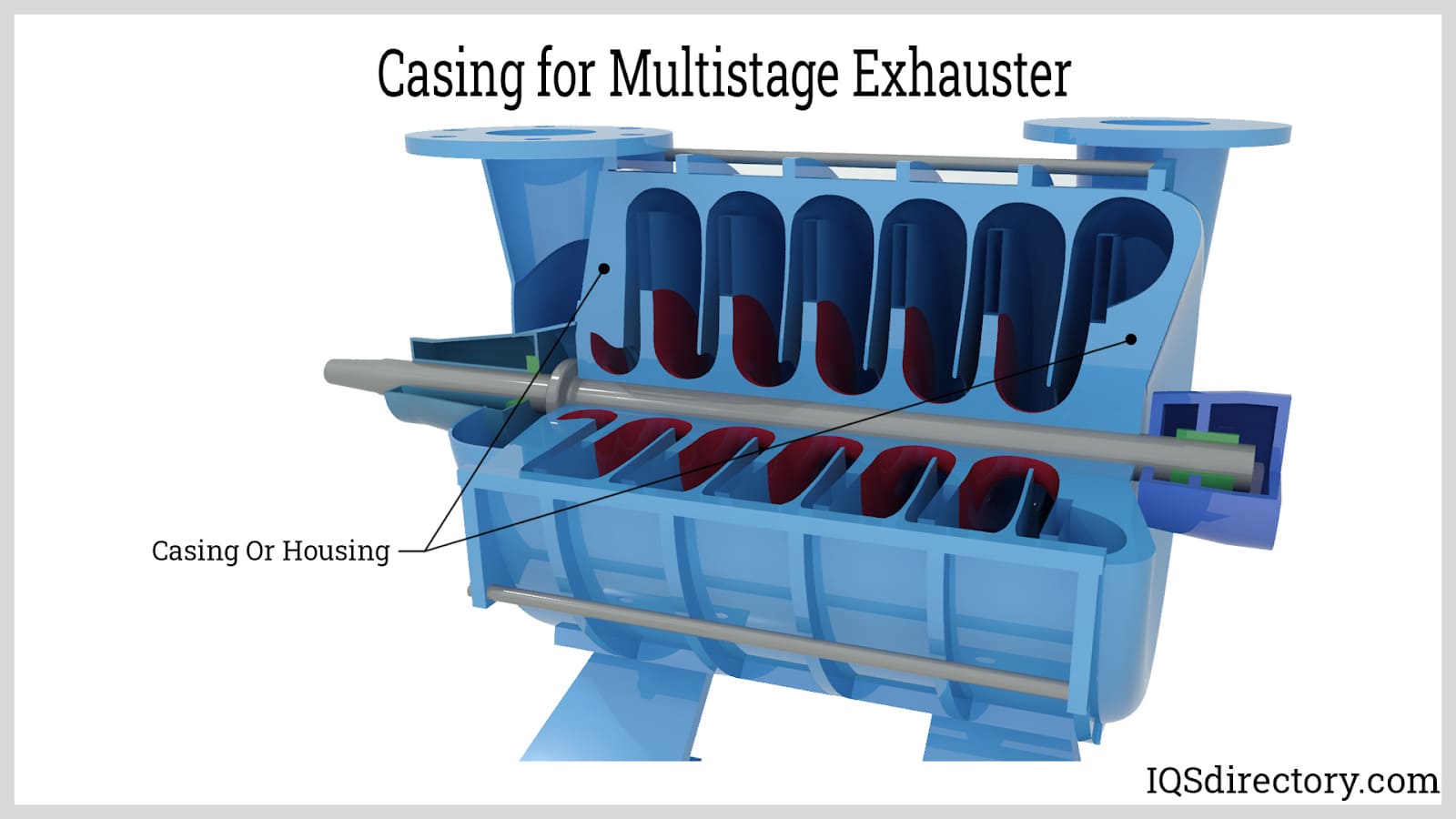
Shaft
The shaft runs the full length of the multistage exhauster housing and holds the impellers in place. It is made of steel or stainless steel and has to be sized properly to avoid vibrations, bearing wear, breakage, and repairs. A part of the shaft is the shaft sleeve that slides or screws onto the shaft. The shaft sleeve assists in positioning the impellers properly and protects the shaft.
Motor
Power for a multistage exhauster is provided by an electric motor that can be direct drive or indirect drive. Manufacturers size their motors according to the demands of the exhauster, typical operation, and if the exhauster will be operated at variable frequency drive (VFD).
Direct drive motors are connected to the shaft, while indirect drive motors are connected to the shaft by a belt. Each type of drive has advantages and disadvantages, with indirect drive motors able to adjust their speed and operate quieter.
Inlet and Outlet
The inlet and outlet are where the air or gas enters and exits the multistage exhauster, with the inlet located at the bottom of the casing while the outlet is located at the top. The outlet exhausts the air or gas that has advanced through the stages of the impellers and has achieved the proper pressure.