Palletizers
Palletizers are material handling machines used for loading and unloading pallets before and after shipping, as well as during storage. Pallet loads are frequently used for mass shipping and distribution, providing a convenient method for consolidating smaller units into one larger, more manageable package.
Many manufacturing and distribution plants utilize automated palletizers, palletizing systems and robotic palletizers for pallet loading and unloading. Automated conveyor palletizers can be low-level palletizers, which load packaged units from the floor level, or high-level palletizers, which move packaged units on an elevated platform. Palletizing machines may be designed for specific products, such as bag palletizers, case palletizers, drum palletizers, and bottle palletizers, or they may handle multiple types of packages. Large-scale distribution centers and manufacturing facilities often use depalletizers to unload packaged units, and palletizing equipment accessories like pallet dispensers and load transfer stations assist in managing both pallets and loads. Some refer to palletizers as case pickers, though the terms "case picking" and "palletizing" are sometimes used interchangeably. However, case picking often specifically refers to the picking of individual products by warehouse staff in distribution operations.
There are three main types of palletizers: robotic palletizers, low-level palletizers, and high-level palletizers. Robotic palletizers are typically positioned between a conveyor line of incoming product units and a pallet dispenser. A hydraulic robotic arm lifts cases, bottles, bags, or drums using flat pincer arms or suction cup arms, arranging them in precise rows onto a pallet. These machines are highly versatile, capable of handling different product units, especially fragile or heavy items. Despite moving one object at a time, robotic palletizers are still significantly faster than human operators and can work continuously without fatigue or risk of injury. Low-level and high-level palletizers are conveyorized systems with a feed area where goods are received for palletizing. In low-level palletizers (also called floor-entry palletizers), products are loaded from the ground level, while high-level palletizers load from above. The packaged units are conveyed using roller conveyors, which automatically sort and transfer the goods to the pallets, providing higher packaging speeds than robotic systems. These systems can be fully automatic, requiring no manual intervention, or semi-automatic, where loads need to be manually connected and disconnected.
Robotic and automatic palletizers offer numerous advantages over manual pallet loading, such as precision, load stability, and a reduction in worker injury frequency. These machines can work faster and more consistently than human operators. The repeated physical movements involved in manual loading—like lifting, rotating, and wrenching—are strenuous and can lead to worker injuries. Reduced employee injury risk not only creates a more pleasant work environment but also boosts productivity and efficiency. Fewer injuries result in lower workplace health coverage costs. The Occupational Safety and Health Administration (OSHA) has proposed significant fines for companies failing to adequately safeguard employee well-being, encouraging many businesses to look for creative solutions to minimize hazards. Palletizers serve as an investment in both productivity and employee safety. Many models come equipped with QuickSTOP collision sensors and Smartscan work cell perimeter guards. QuickSTOP sensors detect equipment damage and automatically shut the machine down to prevent further damage or product loss. Smartscan systems detect when a human worker is too close to the palletizer, automatically halting the machine to avoid injury.
The automation provided by palletizers is crucial to improving operational efficiency and safety. A well-chosen, properly installed, and maintained palletizer can significantly increase productivity. Human errors in materials handling, which often result in product loss, are eliminated when palletizers are used. These systems can operate faster and more consistently than a human using a manual pallet jack or forklift. They are not subject to distractions, and the precise repeatability of their movements guarantees consistent, careful loading and unloading. Though the initial investment in a palletizing machine can be substantial, most operations recoup that investment many times over during the palletizer’s lifespan. Workplace injuries can be costly, but by eliminating the possibility of injury, palletizers contribute to healthier and more productive workplaces.
The History of Palletizers
Since the inception of production lines, cases were traditionally stacked by hand. However, as production rates grew to around 20 or more cases per minute, manual stacking became insufficient, prompting the need for automatic stacking systems. This challenge was addressed through the development of the palletizer.
The first automatic palletizer was designed and built by Lamson Corp in 1948. Lamson was later acquired by ARPAC, a company that now manufactures both mechanical and robotic palletizing machines, producing complete end-of-line packaging systems.
In 1950, row-forming automatic palletizers were introduced in industries and warehouses. The palletizer arranged goods into a row-forming area, and then pushed them into a layer forming area. This process repeated until a complete layer of goods was created, which was then placed onto a pallet. Once the pallet was full, it was removed, and a new one was brought in.
By 1970, the demand for higher speed palletizing led manufacturers to develop in-line, continuous motion palletizers. These machines used a continuous flow to guide products into the desired position on the layer forming segment. Once the layer was complete, it was placed onto a pallet.
In the 1980s, robotic palletizers were introduced. These machines utilized end-of-arm grippers or tools to pick goods from a layer table or conveyor and place them on a pallet. Both conventional and robotic palletizers are capable of handling products at high elevations (up to 124 inches) or at a low floor level (down to 36 inches).
Palletizer Advantages and Disadvantages
Palletizer Advantages
With the growing need to cut costs and reduce processing times in manufacturing, automation has been integrated into nearly every stage of production. Whether it's feeding, washing, assembling, or packing, various machines have been automated to work with minimal operator assistance.
In the packing process, which involves tasks such as selecting, transporting, orienting, counting, and stacking, palletizers play a crucial role by automating these steps, making the process faster and more efficient. Palletizers are also known as load transfer stations and pallet stackers.
To simplify the palletizing process, early palletizing equipment was designed with lifts and platens. Lifts help elevate the station to conveyor belt height, allowing for easier operation, while platens help rotate the palletizing station manually to handle different angles. The use of the platen reduces the need for bending motion, thus minimizing the risk of injuries caused by repetitive motion.
Palletizer Disadvantages
Despite their advantages, palletizers are more complex than simple palletizing equipment, performing a variety of functions, including metering incoming loads, orienting loads, dispensing pallets, forming layers, and more.
Depending on the feeding level, palletizers can be categorized into floor-level in-feed and high-level in-feed types.
Conventional and Robotic Palletizers
The market for palletizers has expanded with a variety of options, from conventional conveyor-based designs to more sophisticated robotic palletizers. However, each type has its own set of disadvantages. To overcome these shortcomings, hybrid palletizers have been developed. These combine the high stacking rates of conventional designs with the flexibility of robotic systems, taking the best features of both. Hybrid designs allow for the palletizing of multiple loads simultaneously.
Hybrid palletizers can easily handle finished products from multiple production lines while occupying less space than alternative systems. They are designed to be adaptable, allowing for the addition of further palletizing equipment if necessary, providing buyers with the option to upgrade the system even after installation.
There are generally three types of hybrid palletizers available: shuttle cars, rotary tables, and robotic arms.
Shuttle Cars
In the shuttle car design, pallets are moved along a track or chain-type conveyor. Shuttle cars carry the pallets and are used in the layer forming section. Instead of individually orienting each product, the hybrid palletizer aggregates products, and once enough products are accumulated, they are fed into the layer forming section. After a layer is formed, it is transferred to a pallet, similar to conventional palletizers. As one pallet fills, another takes its place as they move along the tracks. Pallet dispensers feed the system with empty pallets, automating the process and improving efficiency. Once a pallet is loaded, it is transported to the unloading area via a conveyor. A barcode reader is used for monitoring and metering purposes.
Rotary Tables
The rotary table hybrid palletizer works similarly to the shuttle car design but uses rotating tables instead of shuttle cars moving on chains or tracks. While this design doesn't offer distinct advantages over the shuttle car design, some buyers prefer rotary tables based on the type of cases they need to handle.
Robotic Arms
The robotic arm hybrid palletizer combines the shuttle design with a single robotic arm operation. A robotic arm with three jointed points picks and stacks products in coordination with shuttle cars. As in the shuttle system, products accumulate on the in-feeding conveyor, and the robotic arm picks and stacks them according to its programming. A barcode helps the robotic arm identify and stack the different cases onto an empty pallet attached to the shuttle. The robotic arm can also handle tie and slip sheets when needed. This design offers the flexibility of robotic operation combined with the speed of the shuttle design, managing multiple feeding conveyors. The finished pallet is then delivered to the transportation point. When the pallet is moved, empty pallets are fed back into the system via a pallet positioning system.
While hybrid palletizers can be expensive, they are typically used in facilities with multiple product manufacturing needs. Their flexibility, speed, and efficiency make them suitable for high-output environments.
Palletizer Images, Diagrams and Visual Concepts
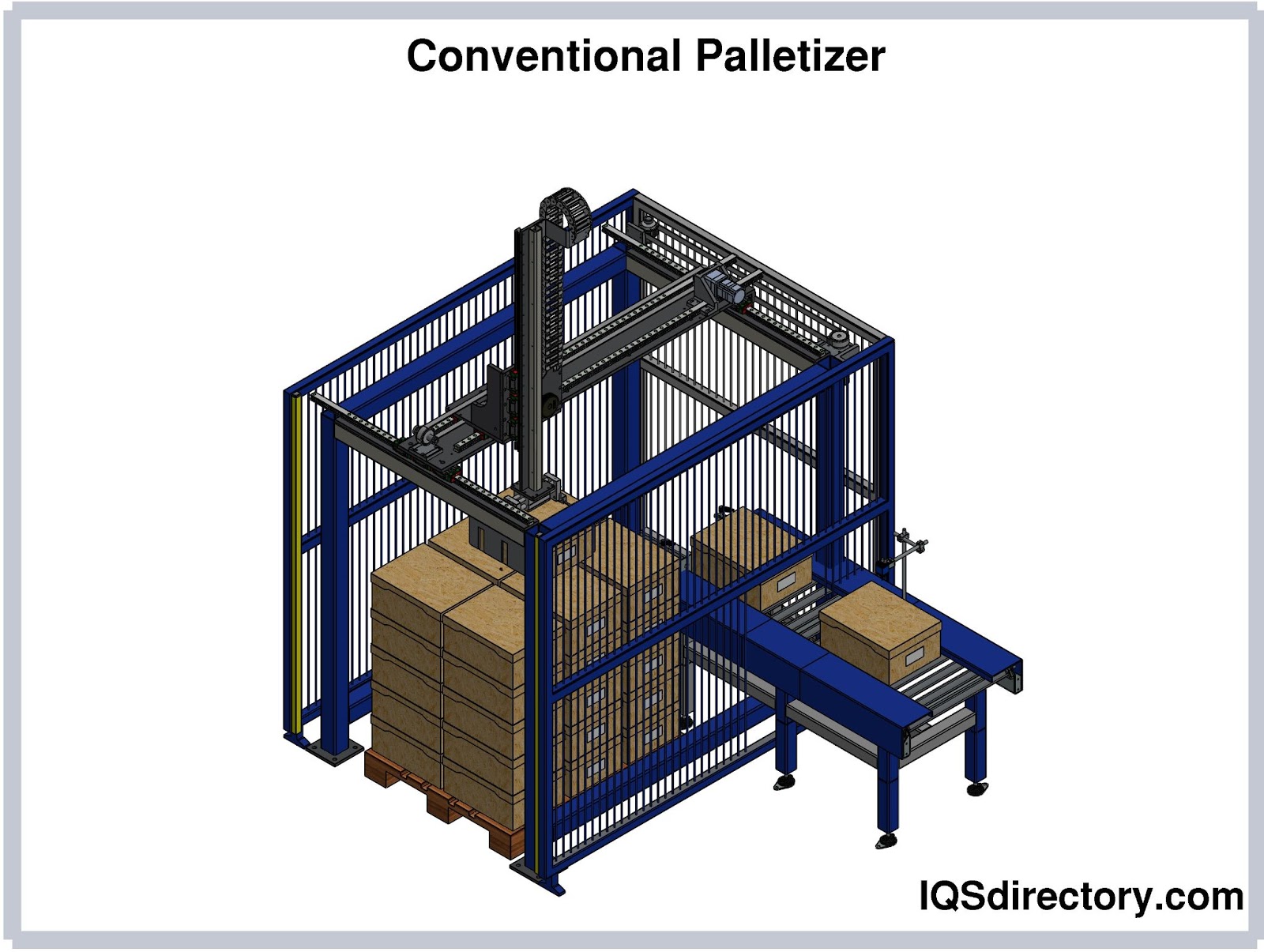
Palletizer, an automated material handling machine used to stack and arrange individual products into a single load.
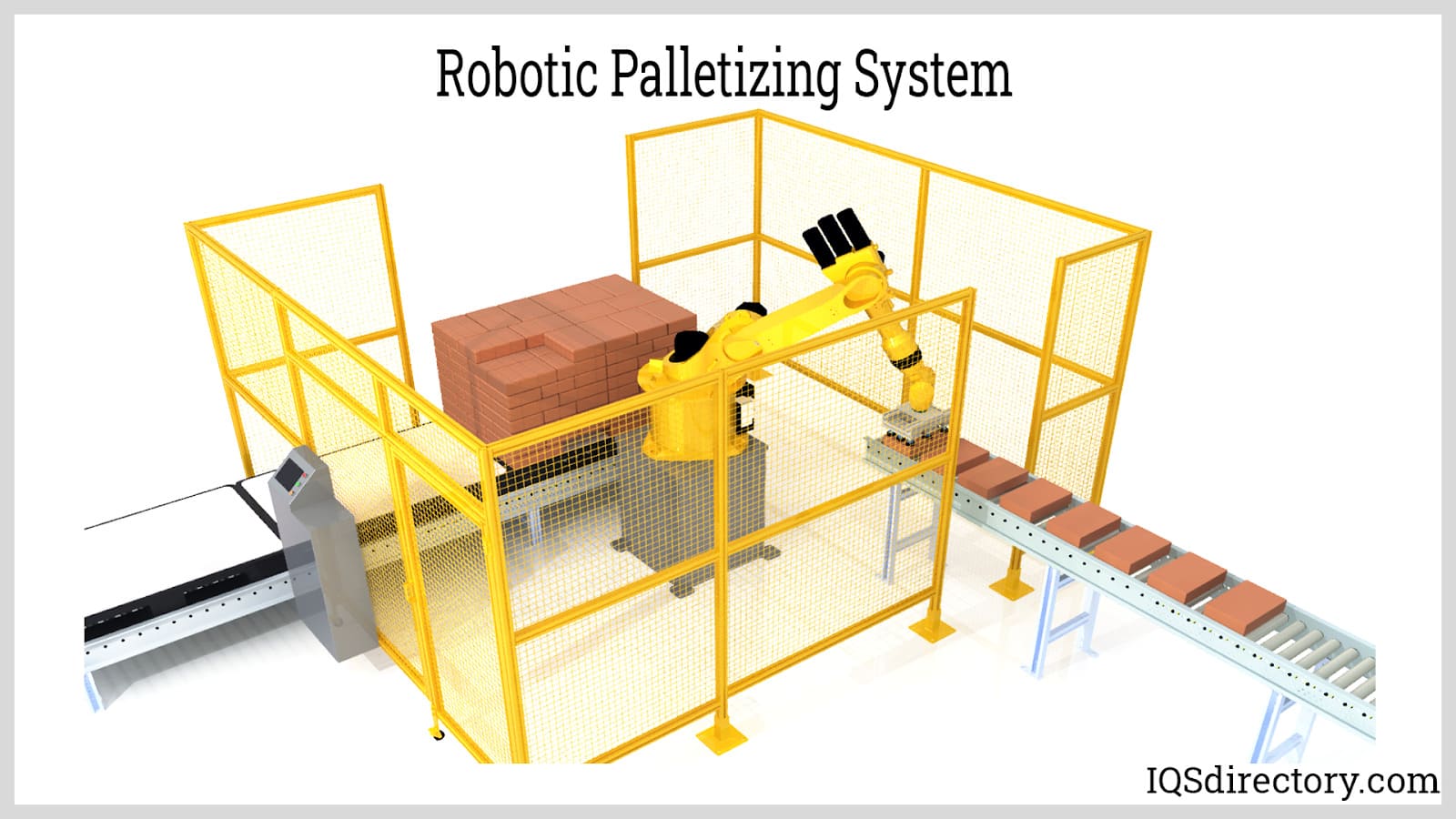
Robotic palletizer, a type of palletizer that uses a robotic arm to lift, place, and arrange individual products into a single load.
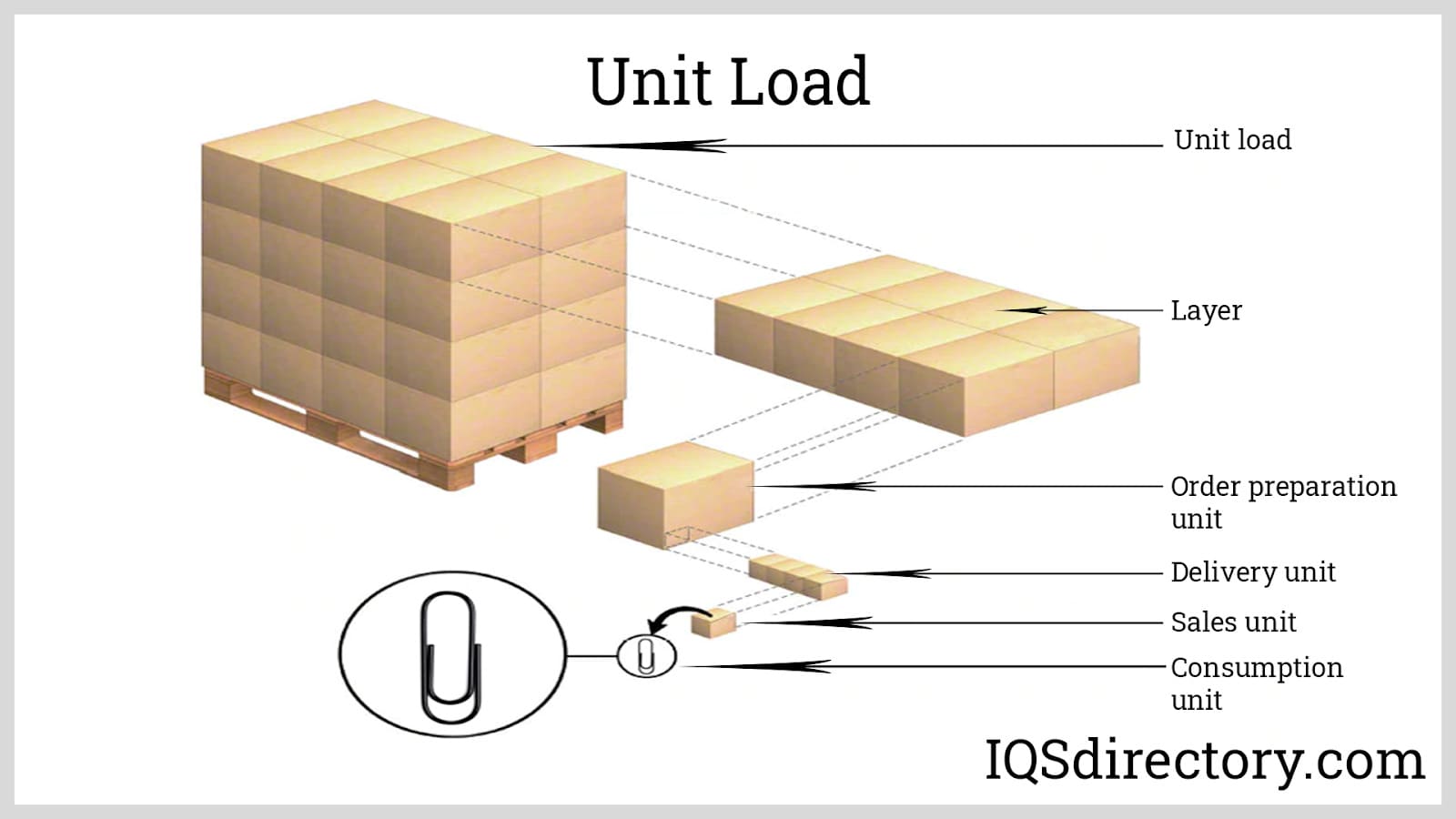
Unit load refers to the assembly of materials combined for efficient handling making it faster and more economical to move large single unit.
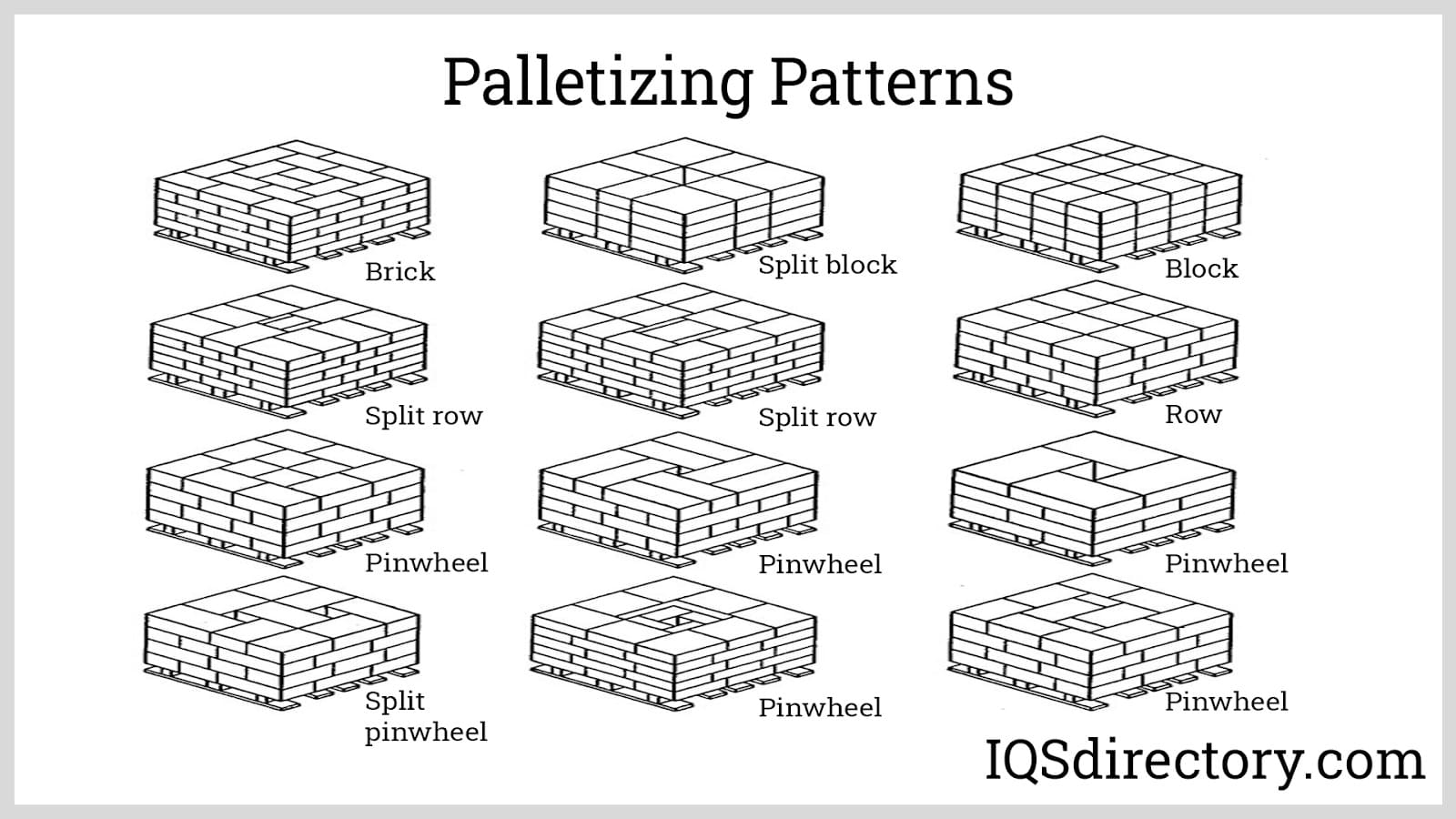
Pallets are designed to be flat, stable structures made of wood, plastic, paper, or steel.
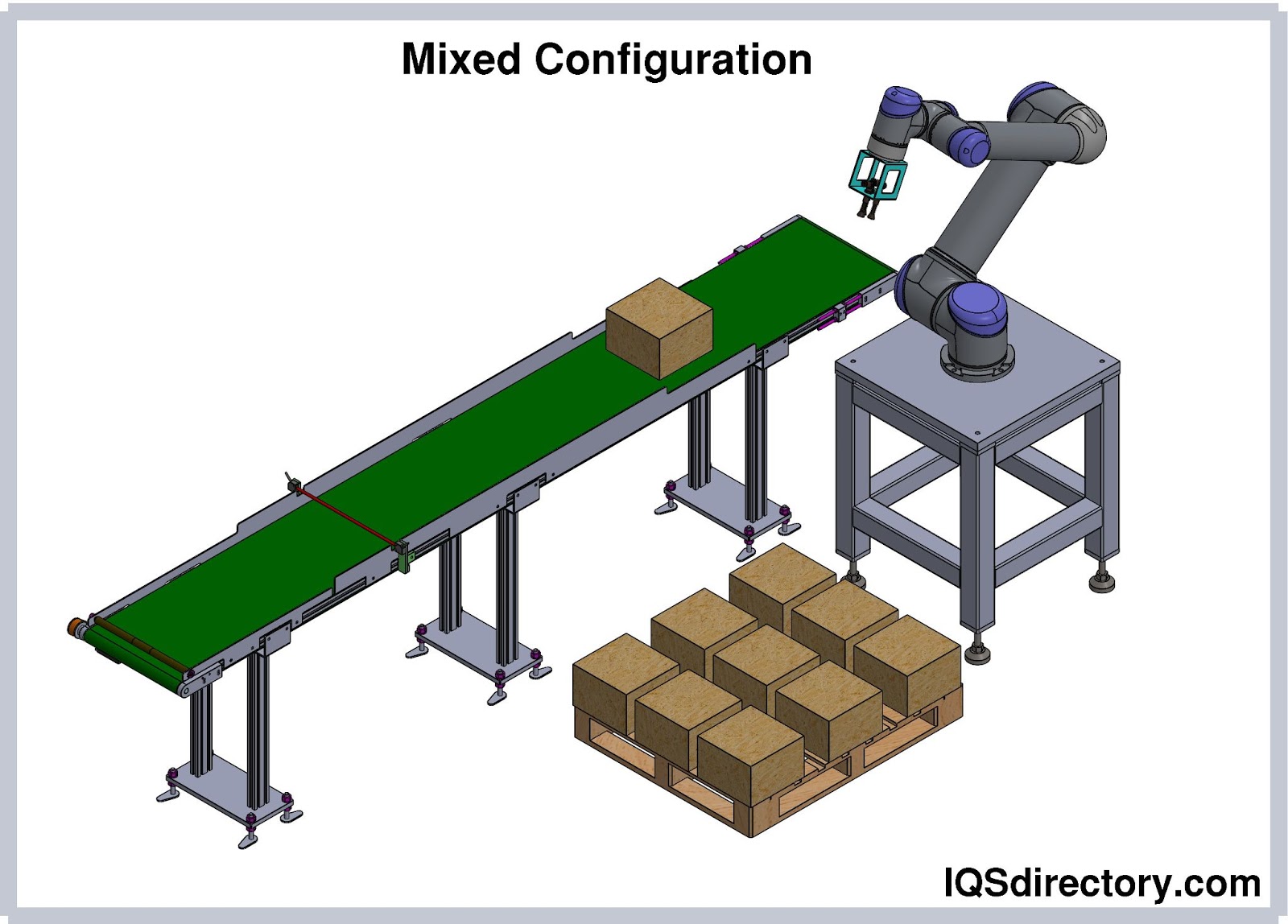
Mixed palletizing refers to the ability of robotic palletizers to accept different products and unitize them into a single pallet.
Palletizer Types
Articulated Arm Palletizers
In articulated robot palletizers, a robotic arm with three rotary joints is installed on the floor, pedestal, or roof, depending on the needs. To operate, additional palletizing equipment such as a conveyor belt is required to bring finished products to the robot. Based on the requirement, articulated robot palletizers can pick single or multiple products from the conveyor and place them onto the pallet. In some designs, the pallet is fed into the palletizer, but in most cases, the robotic arm lifts the pallet when needed. More advanced systems may incorporate a slip sheet to reduce arm movement and increase efficiency.
Palletizers that do not use robotic arms stack products using a combination of conveyor belts and are further divided into floor-level in-feed palletizers and high-level in-feed palletizers.
Automatic Palletizers
Automatic palletizers assemble products on pallets either autonomously or with minimal assistance and are often part of a larger shipping system.
Bag Palletizers
These palletizers are specifically designed to handle bags, either by placing them onto pallets or unloading bags from pallets.
Can Palletizers
Used for arranging filled or empty cans onto pallets for shipping or movement.
Case Palletizers
These machines lift cases from tables and place them onto a pallet or a previous layer of product.
Case Picking
Refers to the movement of products in a warehouse either in preparation for shipment or during organization. It can involve palletized bulk quantities or individual products.
Depalletizers
These machines remove products from pallets, either layer by layer, for leveling or stocking purposes.
Drum Palletizers
Used for moving filled or empty drums onto pallets for shipping or transport.
Floor Level Infeed Palletizers
Also known as low-level palletizers, these palletizers are installed in the production area at the same level as the production equipment. They are advantageous in many industrial applications due to their smaller footprint. They operate by organizing the pallet on the bed and either raising or lowering it to feed it into the stationary pallet. After forming a layer, the palletizer forms another layer until the pallet is complete.
Gantry Palletizers
Gantry palletizers use a robotic arm that can move in three dimensions. These systems work without assistance and are used when a centralized station receives different types of products to be placed onto pallets. The movement of the robotic arm is pre-programmed and occurs within the platform.
High Level Palletizers
High-level palletizers load or unload pallets at an elevated position. The product is received from an accumulation station and placed into the palletizer. The goods are arranged into a single tier above the pallet, which is then lowered layer by layer as new tiers are formed.
High Level In-Feed Palletizers
These palletizers receive products at elevated heights, typically around nine feet, and require operators to work on elevated platforms. Some designs have a controlling area on the ground, although this makes the system more costly. These palletizers help keep the production area clear and make the movement of forks easier.
In-Line Palletizers Systems
These systems are capable of stacking complete layers of products, such as cartons or bags, all at once.
Load Transfer Stations
These palletizing systems transfer loads from one pallet to another without disassembling the contents.
Low Level Palletizers
Also known as floor-level palletizers, these machines are a type of automated conveyor palletizer that can load packaged units from the ground level.
Manual Palletizers
Manually-operated machines used for moving products on and off pallets.
Pail Palletizers
Designed specifically for arranging pails on pallets for shipping or transport.
Pallet Dispensers
Also known as pallet feeders, these devices feed empty pallets to conveyors in larger palletizing systems.
Palletizing Equipment
Refers to the various machines used to pack and transport pallets.
Palletizing Machines
Automated machines or conveyor systems that arrange a maximum load of packaged products onto a pallet for distribution.
Palletizing Systems
Material handling systems that arrange packaged product units onto a pallet for distribution.
Robotic Palletizers
Automated systems that lift and move goods onto pallets, either fully automatically or semi-automatically, to relieve workers of heavy, repetitive lifting tasks.
Row Stripper Palletizers
A type of in-line palletizer that organizes rows and pushes them aside until a new row is formed, which is placed on top of the previous row until the pallet is complete.
Selective Compliant Articulated Robot Arm Palletizers
A type of robotic palletizer that uses a mast and cross arm to place products.
Semi-Automatic Palletizers
These systems allow an operator to stack layers of heavy products without manual lifting.
Vacuum-Head Unit
A type of in-line palletizer that uses air-powered suction cups to grip products and place them onto pallets.
Palletizer Characteristics
Palletizers are used to automate the stacking process in manufacturing, helping to load and unload goods efficiently. These machines are designed to count, orient, and arrange incoming loads into rows and layers. The process is akin to an assembly line, where different types of conveyors are integrated to work together and ensure effective stacking.
Standard palletizers include several operations. Initially, the machine counts or meters products as they move on the in-feed conveyor. The product is then rotated or oriented to the desired position, before being placed in a designated spot to form a row or layer. After the layer is formed, a layer compression device ensures that the products are tightly packed. The formed layer is then moved to a load hoist by a layer stripper. Once the pallet is created, forklifts remove it, and pallet dispensers automatically replace the empty pallet.
There are two main types of palletizers: those that do not use robotic arms and those that do.
Both articulated and gantry arm palletizer machines are considered pick-and-place units. These machines are designed to pick cases from various locations and place them on the pallet at designated spots. Equipped with basic computing features and sensors, they can distinguish between different cases and separate a wide variety of package types.
Unlike low-level and high-level palletizers, robots can automate multiple production lines with a single machine. Goods from various production lines only need to be placed near the robot, which then identifies and places the cases in the correct position.
These palletizers can produce multiple pallet loads depending on the size, shape, and other characteristics that the machine is programmed to detect. They are often referred to as end-of-arm palletizers because of their rotating arms, which enable them to pick cases from different parts of the production area. This rotation sets them apart from traditional stationary units, though they are relatively slow, handling up to thirty cases per minute.
Robotic palletizers are named based on the type of arm they use. Lighter applications require an articulated arm designed with multiple axes for flexibility, while gantry palletizers are needed for heavy-duty applications. However, gantry palletizers are less flexible than articulated arm palletizers. The distinction between the two is not absolute, and there are hybrid models that combine features of both.
Data Collection in Palletizer Machines
These computerized controls provide the ability to collect and report data, making the machines more efficient and insightful. Various manufacturing companies equip their machines with real-time reporting features, including alarm and downtime alerts, production tracking, and more. The data gathered helps businesses optimize their supply chains and improve operational efficiency.
The manufacturers also provide these machines with schematics and manuals, enabling industries to carry out repairs independently without needing to call in the manufacturer. The user-friendly computer interface guides operators through routine maintenance tasks and troubleshooting, reducing downtime and maintenance costs. These interfaces have also played a key role in the development of high-speed machines that can handle smaller case sizes efficiently.
As more retailers shift toward smaller-sized packaging, the demands on handling have increased. This shift has been driven by suppliers and retailers aiming to minimize waste while maximizing the quantity delivered with fewer packages.
Palletizer Versatility
HMIs (Human-Machine Interfaces) are being used to upgrade palletizer machines, making them more adaptable and efficient. For example, robotic palletizers have shown remarkable flexibility in handling various product types, with the capability to manage up to five production lines simultaneously.
Gantry palletizers, known for handling heavy-duty applications, are being increasingly utilized in distribution centers to manage numerous production lines. These machines can create a "layered rainbow pallet," where each layer consists of different product types, making them ideal for applications like palletizing soft drinks, where various flavors are organized in separate layers for transport to different retail locations.
For smaller suppliers, palletizer machines have brought significant improvements in ergonomics. The rotation, repetitive motion, and lifting involved in manually placing goods on pallets are minimized, reducing strain and increasing efficiency.
Palletizer units continue to evolve, with engineers collaborating with suppliers to enhance their convenience and functionality. These machines are now designed to organize goods at the case level, placing them at the core of production processes. While this technology is still undergoing refinement, palletizer machines are addressing the growing demand for speed and precision in modern manufacturing.
Custom Designs of a Palletizer
When requesting custom palletizers for specific applications, companies often provide clients with the opportunity to review their CAD designs. Engineers, in particular, can collaborate with the manufacturer to refine the design and ensure it meets their unique requirements.
Custom palletizers are designed to handle specialized materials. Among the most common is the bulk palletizer, which is frequently used in can manufacturing plants. This unit is used to load and unload cans made from various materials. The cans are stacked in layers on the pallet, with slip sheets placed in between to protect the products. To ensure security during transport, the load is typically banded.
Specialized palletizer machines are also available, including bag palletizers, case palletizers, and drum palletizers, each designed to meet specific needs as indicated by their names.
Hybrid Palletizer
The growing demand to reduce secondary packaging has driven the design of hybrid palletizers, combining robotics with traditional technology. This integration allows for simultaneous operations, where a palletizer can palletize and stretch-wrap products in one seamless process. Automated palletizers are increasingly sought after due to their flexibility, allowing businesses to handle various packaging requirements with ease.
Things to Consider When Purchasing a Palletizer
Future Needs
Returns on investment tend to be higher with conventional palletizer machines. However, robotic systems have the advantage of being able to handle various packages and can even process up to 60 cases per minute in some applications. The industry must determine the most suitable design based on specific needs. For example, a bottler might opt for robotic palletizers due to their ability to handle products gently.
Safety Standards
Suppliers and palletizer manufacturers are placing significant emphasis on using safety-rated devices, such as PLCs, automatic air dumps, and VFDs. Wider palletizer equipment is being phased out in favor of more ergonomic and convenient designs. When requesting a custom machine, safety should always be the top priority.
Consumer Level Developments
Pallet loads designed for display are becoming increasingly common, which has led to a need for graphics-oriented pallet placement. This requires the use of tier sheets between layers. The decision to use hooding or stretch wrapping depends on convenience and applicability.
Shrink-Wrapping
Shrink-wrapped loads require specialized handling within the palletizer compared to paperboard or corrugated cases. When handling either very small or large loads, a highly flexible palletizer is necessary to manage the variation in size.
Costs and Complexity
The demand for speed and flexibility, coupled with the trend toward lightweight packaging, is driving up the cost and complexity of palletizer machines. This shift has also led to increased use of robotic technology to meet these evolving needs.
Risk Assessments and Controls
As the complexity of palletizer systems grows, it is essential that users have access to machines that are not only easy to operate but also safe. Manufacturers must provide risk assessments to users, and at a minimum, this information should be disclosed to OSHA to ensure compliance with safety regulations.
Choosing the Right Palletizer Manufacturer
There are numerous companies that design and produce palletizer machines. The right manufacturer will allow clients to specify important features such as size, weight, power, and other technical details when requesting a palletizer. Some manufacturers even offer CAD software to showcase the modular design before production, providing clients with a visual preview of the machine. While many companies do not offer fully custom machines, most provide a wide range of machines, making it easier for consumers to select one that fits their needs. The cost of palletizer machines depends on the type and features, but the price tends to be similar across manufacturers for the same type of machine. Manufacturers that place more emphasis on safety features for industrial applications are often preferred by buyers.
In addition to palletizer machines, some manufacturers also offer pallets designed to work seamlessly with their palletizing systems. While most pallets are made of plastic, some are constructed from wood or metal, providing a variety of options to suit different applications and requirements.
Palletizer Accessories
Most palletizer machines are offered as complete units with no need for additional accessories. However, in some cases, the units may require accessories to optimize performance and enhance speed. These accessories include:
- Pallet Dispenser
- Sheet Dispenser
- Turning Devices
These accessories are designed to customize the palletizer machine to suit specific operational needs. While they can be purchased directly from the palletizer manufacturer, they are also widely available from other suppliers.
Palletizer Terms
Captive Pallet
A pallet that stays within a facility and is not exchanged, traded, or delivered off-site.
Deck
The top or bottom surface of the pallet.
Deflection
The amount of bending in a pallet or one of its components when under a load.
Fork Entry
The place for forks to enter and move the pallet, usually between decks or under the top deck.
Line Load
The weight of a unit load concentrated across the entire length or width of the pallet or along a narrow area.
Load Bearing Surface
The area of material that is in contact with and is supporting a unit load.
Mast-Equipped Automatic Guided Vehicles (AGVs)
Vehicles that move unit loads and store or retrieve pallets and unit loads.
Pallets
Platforms used to stack goods on for shipping, storing, or moving. They can have two-way or four-way entry by fork trucks.
Pallet Conveyors
Industrial equipment used to more efficiently transport goods loaded on pallets through a factory or manufacturing plant.
Pallet Design System (PDS)
A computer-aided design program that helps determine safe load-carrying capacities, performance, life, and economy of wooden pallets.
Pallet Jack
A manual wheeled platform used for lifting palletized unit loads.
Pallet Inverters
Used to turn heavy loads of merchandise 180 degrees to exchange one pallet for another with as little hassle as possible. Pallet inverters are usually used on their own and utilize a rotating frame to transfer pallets or stack them in a warehouse, or move them to a shipping container.
Raked Across Deck Boards
The maximum load carrying capacity and deflection of a pallet where, at the ends of the deck boards, the rack frame sustains the pallet.
Racked Across Stringers
The maximum carrying capacity of a pallet where, only at the ends of the stringers or stringer boards, the rack frame sustains the pallet.
Slave Pallet
A panel used to support the base of a palletized load in rack-storage facilities.
Strapping
Bands that secure the goods or load to the pallet.
Throughput
The amount of output or production in a given period of time.
Top Cap
Panel placed on top of goods on a pallet that protects them from damage when strapping occurs.
Unit Load
The collecting of goods to be moved or shipped onto a pallet.
More Palletizers
More Bulk Material Handling Equipment