Plastic Containers
Plastics are a defining product of the modern age. The evolution of plastic, as detailed on this site, reflects a story of innovation and industrial growth. The rise of plastic storage solutions, along with the rise of mass production, played a crucial role in driving America's post-war economic expansion. Among the many transformative products made from this groundbreaking material, plastic containers stand out as some of the most practical and essential items.
Plastic containers are versatile enclosures made from plastic, designed to hold or store various items. These containers differ from one another based on their size, shape, function, and intended use. While it's easy to visualize plastic boxes or containers, capturing them within a single, universal description is challenging due to the vast array of types available. There are simply too many different kinds of plastic containers to define them all with one simple explanation.
The History of Plastic
From the outset, the development of plastic has been driven by commercial interest. Manufacturing for consumer production continues to be a primary catalyst for the many forms plastic has taken over time.
The fascination with plastic began in the 19th century as a substitute for increasingly scarce materials like shell, bone, and ivory. One of the earliest applications of plastic was the use of natural cellulose from plants and trees. By heating it and adding chemical agents, a new, durable, and versatile substance was created.
In 1839, Charles Goodyear made a groundbreaking discovery when he accidentally found how sulfur reacted with raw rubber in a process known as vulcanization, resulting in a more durable form of rubber. In 1870, John Hyatt developed celluloid, marking another milestone. Then, in 1909, chemist Leo Baekeland formulated Bakelite. These innovations, alongside the creation of nylon in the 1930s, sparked an era of commercial experimentation and opened up a new world of plastic materials.
Advantages and Disadvantages of Plastic Containers
Plastic containers can be crafted to meet nearly any specification required by designers and customers. The material is both lightweight and durable, offering a wide range of colors, textures, and shapes.
By adjusting the formulations of plastic, manufacturers can create containers with specific properties like food safety, water resistance, sterility, heat resistance, and microwave compatibility.
Another significant advantage of plastic is its cost-effectiveness, mainly because of its ease of mass production. Furthermore, plastic is evolving to become more sustainable with the introduction of biodegradable products. These innovations, along with advances addressing concerns such as BPA emissions, contribute to the growing appeal of plastic containers.
Applications of Plastic
Plastic is defined as any material that can be shaped or molded, which includes products like fiberglass. The variety of chemically-made plastic products is vast, ranging from food-grade bottles to Lego toys, car bumpers, and even bubble gum. It plays a crucial role in industries such as electronics, plumbing, construction, and healthcare.
Plastic can be engineered to be chemically inert and food-safe, making it ideal for packaging materials. It is also highly durable and resistant to chemicals, allowing for the creation of storage containers designed to hold substances like water, juice, bleach, gasoline, soap, alcohol, and even acid.
The versatility of plastic manufacturing has led to the production of a wide range of lightweight, strong, and flexible products. Plastic is used in a variety of forms, including food bins, bulk containers, ropes, filaments, glues, paints, sheets, pipes, and bottles. Over time, plastic has replaced older materials such as leather, horn, stone, wood, metal, and glass.
One of the most popular uses for plastic is in container manufacturing. Today, there is a vast selection of plastic containers available, including food packaging and food-grade containers in nearly any shape, color, or size.
Industries that Use Plastic Containers
Plastic containers are not just popular with consumers; they are also a vital component in numerous industries. Plastic containers are widely used for packaging and storage in nearly every sector of business, from manufacturing to logistics, and are indispensable for operations across the globe.
Countries at every level of economic development depend on plastic containers. Whether in developed nations or regions facing resource scarcity, plastic containers are everywhere. In wealthier countries, plastic packaging is ubiquitous—few food items, for instance, are not packaged in plastic, and it would be challenging to find peanut butter in a glass jar in the United States. In developing nations, plastic containers, such as water bottles, are essential, particularly where municipal water systems are lacking. The demand for portable water containers is immense in these regions.
In addition to household and retail uses, industries of all kinds rely heavily on plastic containers. Warehouses store and transport goods in plastic totes and bins, while factories use plastic tubs to collect products as they exit production lines. Landscaping companies, municipalities, and consumers use plastic catch basins to manage rainwater runoff and prevent water pollution. Even recycling containers for plastic waste are made from plastic. The popularity of plastic is due to its durability, flexibility, low manufacturing cost, and ability to be molded into virtually any shape.
In construction, plumbing, healthcare, and even finance, plastic storage and containment solutions are a critical part of everyday operations. From crates and boxes to jars and specialized containers, plastic is an essential material for businesses around the world.
Making Plastics
Plastic is a versatile, lightweight, strong, and cost-effective material, offering excellent electrical and thermal insulation. It is resistant to corrosion and can even be made sufficiently transparent for optical devices.
Plastic Composition
Plastics are primarily composed of synthetic and semi-synthetic organic polymers, mostly derived from petrochemicals, although renewable sources like corn and cotton are increasingly being used. Initially, natural materials such as rubberwere the first useful plastics.
Chemists can combine different monomers in various ways to create an impressive array of products. Plastic containers, for example, can be made in varying sizes and designed to withstand different pressures and temperatures.
Plastics are predominantly based on carbon atoms, except for a few exceptions like silicone. The chemistry behind plastic is complex, but the concept revolves around chains of molecules, known as polymers. Many types of plastics have names that begin with "poly," such as polyethylene, polystyrene, and polypropylene. These polymers can be found by checking companies listed on IQS Directory.
Most plastics are refined and processed hydrocarbons, although there are biodegradable options made from processed corn. The majority, however, are petrochemical derivatives, starting as crude oil and natural gas. Through refinement, these raw materials are transformed into chemicals like styrene, ethylene glycol, and vinyl chloride, which are the primary components of thermoplastics. Thermoplastics, under specific conditions, can be molded into useful products. Thermosets, another category of plastic, are less commonly produced and cannot be remolded after setting. Common processes used to create plastic containers include injection molding and blow molding. In these methods, raw plastic material is fed into a conveyance channel, where it is heated and liquefied by friction and pressure from a rotating screw. In injection molding, the molten plastic is forced into a mold to form a shape. In blow molding, compressed air is injected into the mold to shape the plastic further, creating hollow sections. Sometimes, both techniques are combined for complex shapes. Once molded, the plastic cools, hardens, and is ejected from the mold.
Additives and Plastics
Additives are chemicals or substances mixed with plastic to improve its performance or achieve a desired aesthetic. Inorganic fillers, like carbon, strengthen plastic, while thermal stabilizers are used for high-temperature processing. Plasticizers make the material more pliable, and fire retardant additives help prevent ignition. UV stabilizers slow down degradation caused by sunlight. Other additives can alter the color, texture, or finish of the plastic. The malleability of plastic allows it to be securely combined with various substances like stainless steel or glass.
Plastic Container Production
Plastic poses unique challenges to engineers due to its semi-liquid state during processing, which requires specific knowledge and experimental testing. The adaptability of plastic means it can be processed in many different ways. Plastic storage containers are typically made through methods like injection molding, extrusion, rotational molding, and blow molding.
Injection molding, one of the most common techniques for making plastic containers, involves injecting molten plastic into a mold. Extrusion, a similar process, involves melting and cooling plastic into a desired shape. There are several variations of these techniques, including rotational and blow molding, and often combinations of methods are used to achieve specific characteristics in the final product.
Chemical Characteristics and Features of Plastic
An essential distinction in plastic types is whether it is classified as a Thermoset or Thermoplastic. Some plastics, such as Bisphenol A (BPA), can be formulated as either of these types. BPA and BPA-based products are widely used in the consumer market.
A Thermoset plastic polymer can only be shaped once, as the material undergoes irreversible changes when heated. Once shaped, it cannot be remelted or reformed. Common applications of Thermoset plastics include housing insulation, bathtubs, plywood, and computer components. These plastics are valued for their strength, durability, and versatility, and they can be produced in various sizes, including both small and large plastic containers.
On the other hand, Thermoplastics are also plastic polymers that soften when heated, but unlike Thermosets, they can return to their original state when cooled. Thermoplastics are extremely versatile and used in a wide range of applications, including packaging, films, siding, and floor and wall coverings. This type of plastic is common for both small and large plastic storage containers, as well as their lids. BPA products can also be made from Thermoplastics.
Many food-grade containers are made from Thermoplastics like High-Density Polyethylene (HDPE) or the more flexible Low-Density Polyethylene (LDPE). Polyvinyl Chloride (PVC) is another common thermoplastic used for containers. BPA-containing plastics have faced scrutiny due to concerns about BPA emissions. Environmental issues surrounding BPA have raised caution, though the pervasive use of BPA products makes it nearly impossible to completely avoid exposure.
Plastic Container Images, Diagrams and Visual Concepts
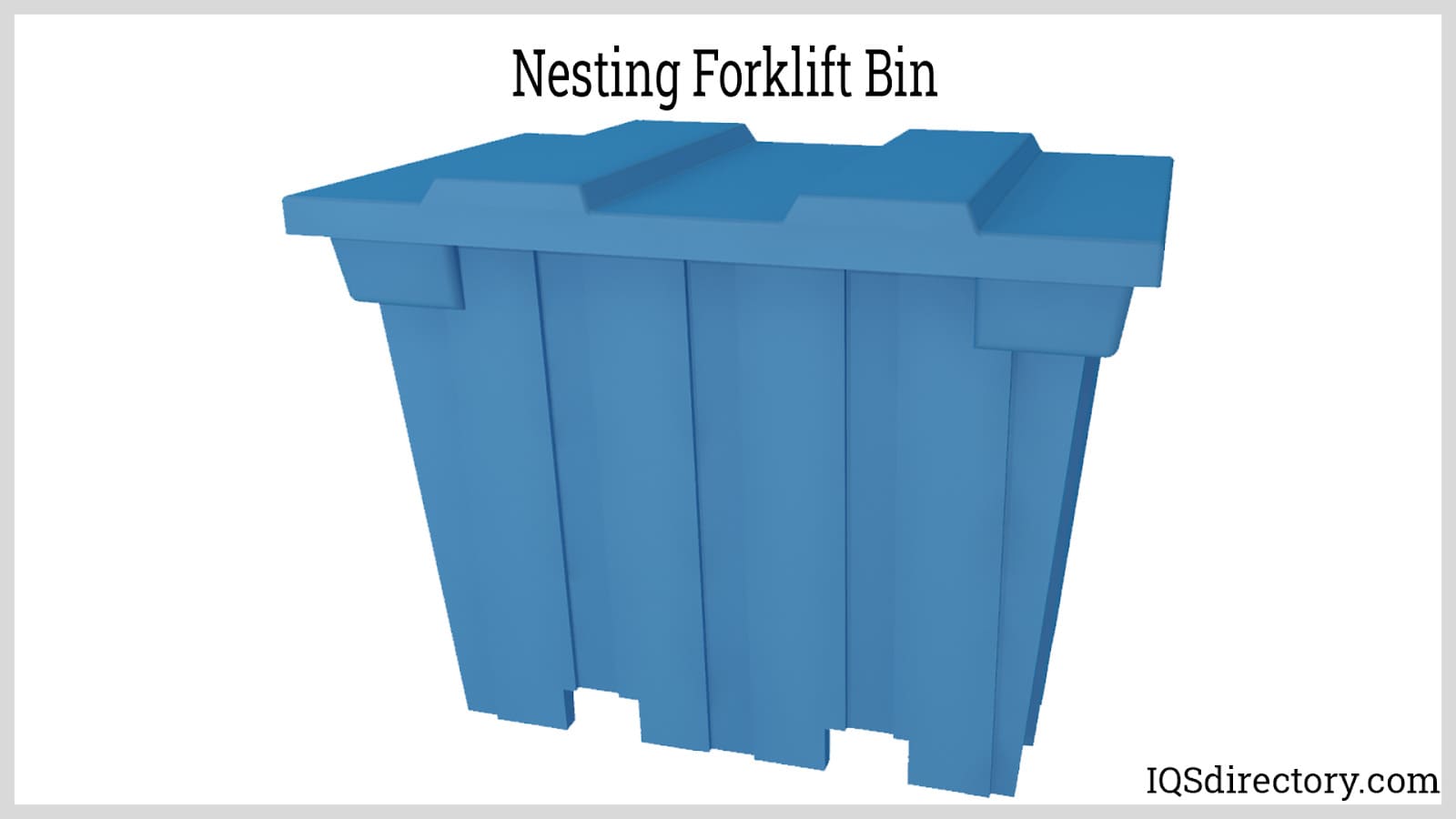
Plastic containers are storage units fabricated from various forms of polymers produced from crude oil or natural gas.
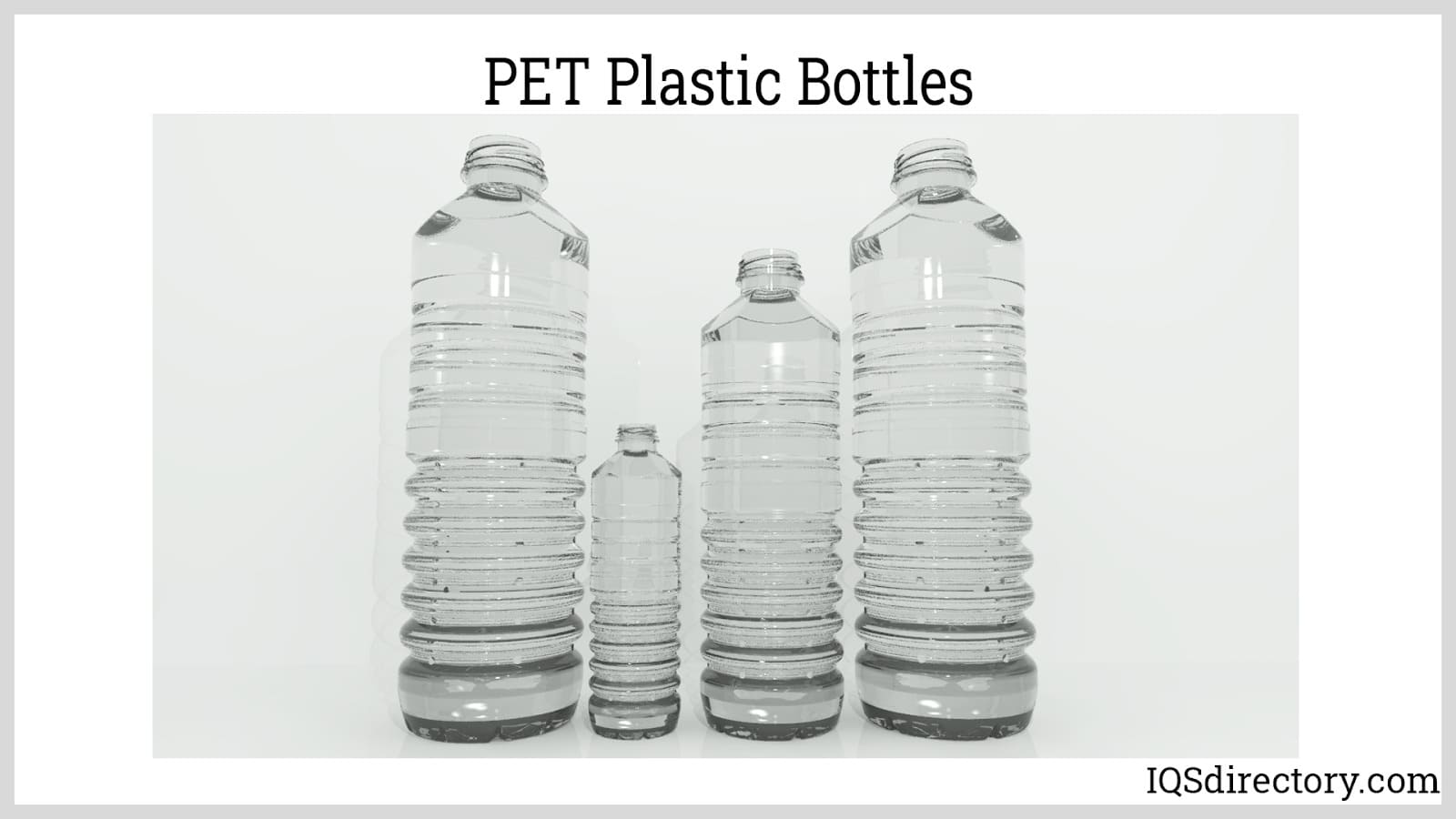
Polyethylene Terephthalate (PET) is the most used plastic material for plastic containers and is known for its low permeability to carbon dioxide.
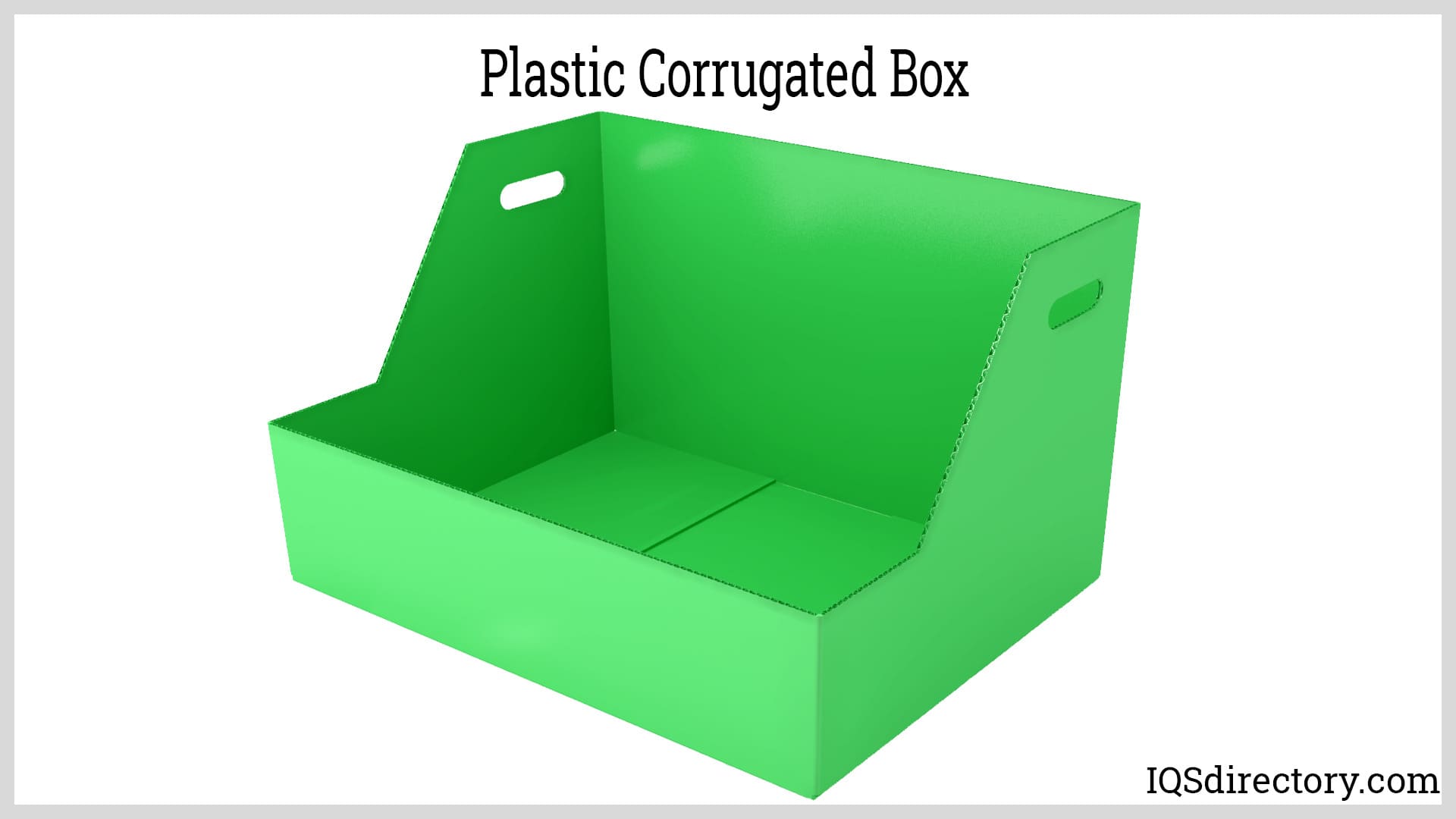
A disposable container with three layers of material consisting of an inner, outer, and middle layer on its sides.
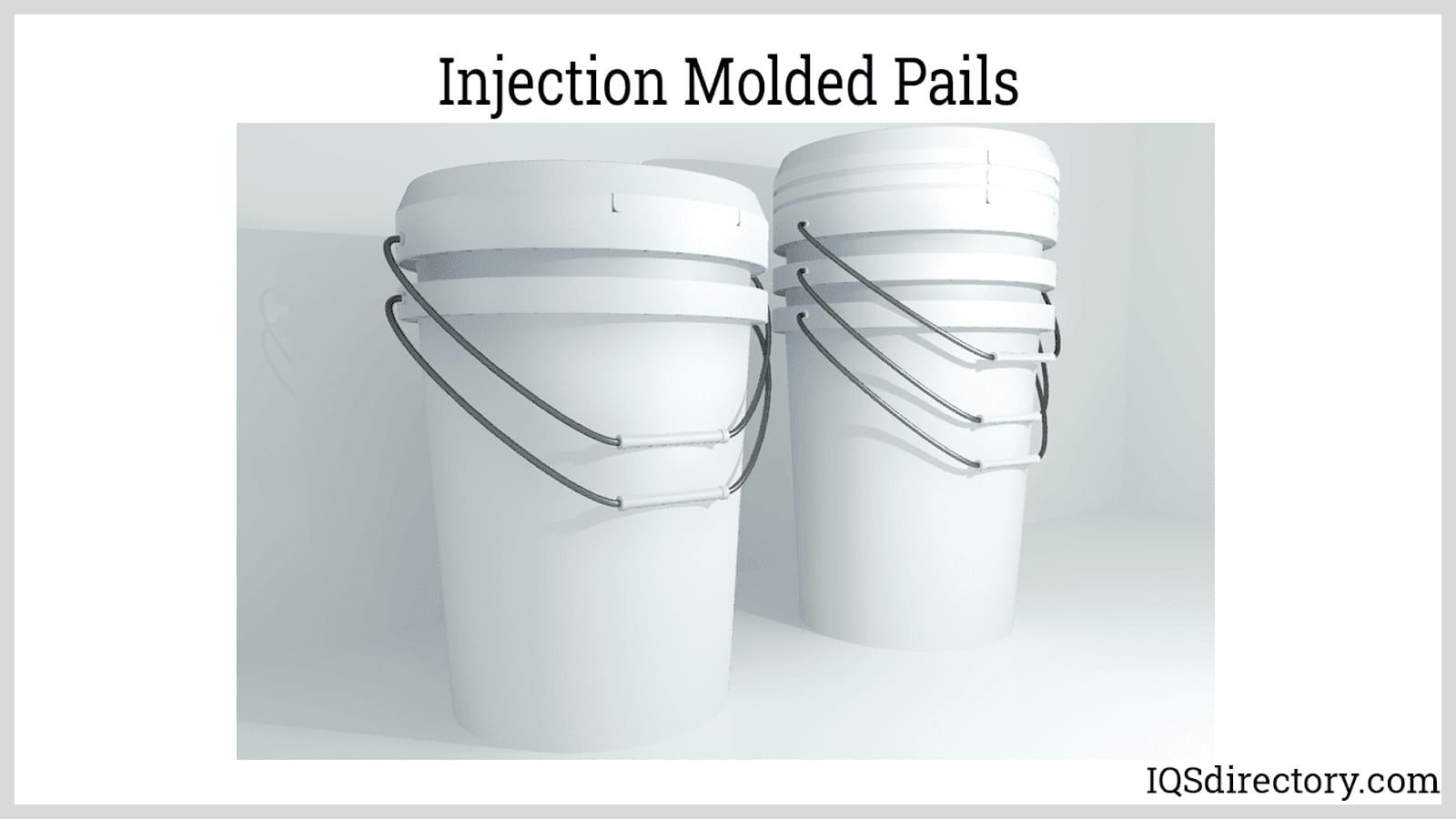
Injection molding is limited to producing containers that are open on one side.
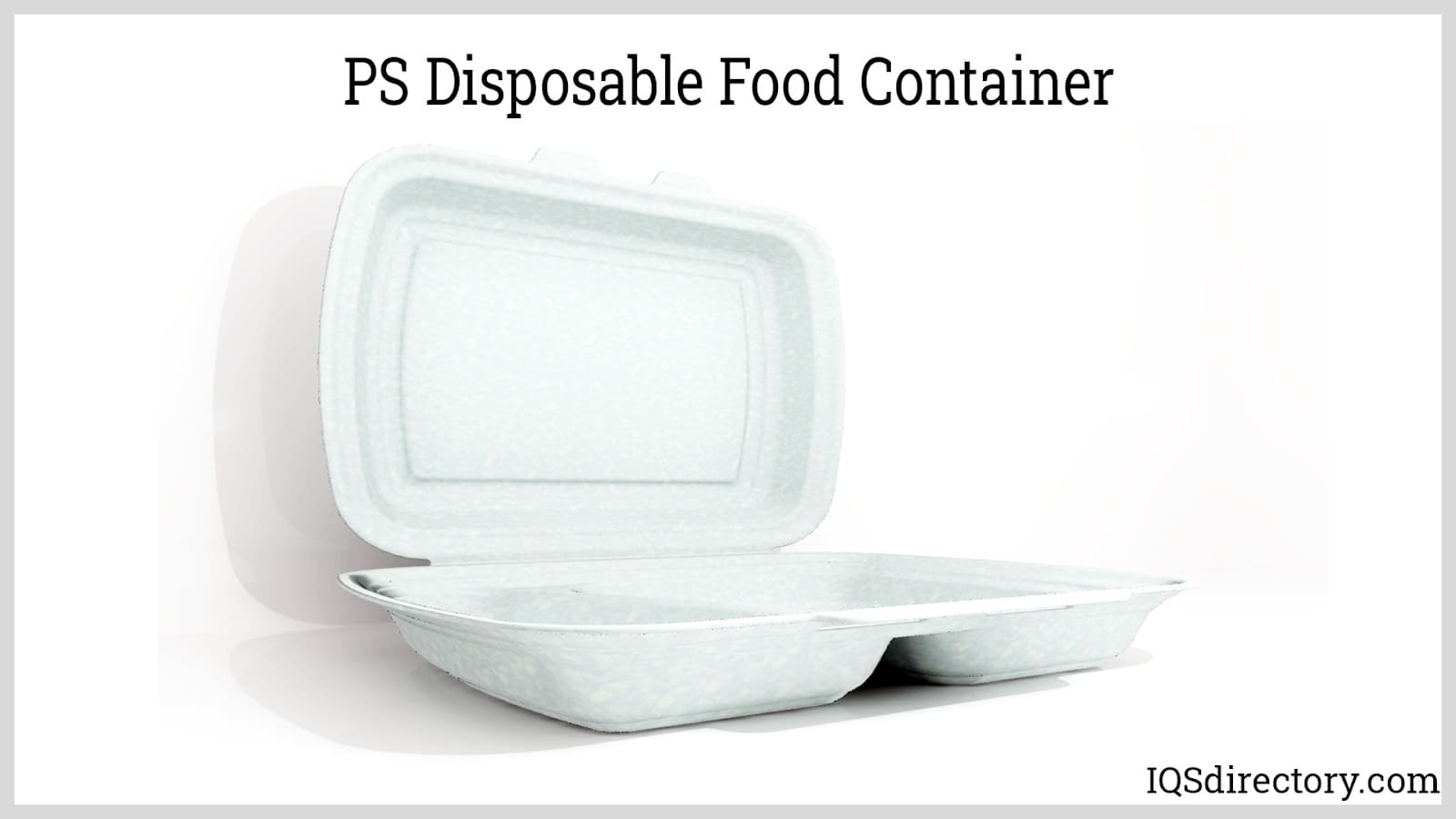
Polystyrene is a versatile plastic modified by copolymerization and the addition of additives, made to be flexible, rigid, or cellular (foam) plastic forms.
Plastic Container Types
Attached Lid Containers
Containers with lids attached, typically by hinges, to provide product protection and prevent the lid from being lost.
Bottom-Hinged Containers
Containers with openings at both the top and bottom. The bottom opening is typically lockable for easy product removal.
Bulk Containers
Containers designed to hold, transport, and ship large quantities of products together.
Catch Basins
Cisterns located at the end of gutters to collect rainwater.
Drum Containers
Containers used to hold bulk products, including food, liquids, wine, water, parts, and various other materials, available in various sizes.
Holding Tanks
Tanks designed similarly to septic tanks, used to contain wastewater until it can be removed for treatment and disposal.
Hopper Containers
Containers designed for short-term storage, with a design that allows for easy disposal of stored material.
Lockers
Secure, private storage units typically used for clothes or valuables, most commonly found in changing rooms. They come in various sizes and styles.
Nestable Containers
Containers designed to fit together or inside one another for easy storage.
Neutralization Tanks
Containers designed to collect and neutralize acidic and basic wastewater, making it safe for removal.
Open Head Containers
Containers with a removable top or cover.
Overpack Containers
Containers used for damaged or leaking drums, often containing hazardous materials.
Packaging Containers
Commercial containers, often custom-designed, intended for easy use and presentation depending on the product inside.
Plastic Bins
Storage boxes made from various types of plastic materials.
Plastic Bottles
Small containers designed for the transportation, storage, and distribution of products in small quantities.
Plastic Boxes
Storage containers made from plastic materials for various uses.
Plastic Buckets
Smaller, round plastic containers used for storage, distribution, and various other applications.
Plastic Crates
Containers of varying sizes and constructions used for storage and distribution.
Plastic Food Containers
Typically made of polypropylene, available in various shapes and sizes to accommodate different quantities of food.
Plastic Jars
Small plastic containers used for distributing consumer products in small quantities.
Plastic Shipping Containers
Containers made from plastic designed for shipping products.
Plastic Storage Containers
Stackable containers used for storing various goods.
Plastic Totes
Plastic baskets with handles, designed to hold or carry products/materials.
Plastic Tubs
Storage or distribution containers used in commercial and industrial applications.
Reusable Containers
Containers designed to be reprocessed and used multiple times.
Stackable Containers
Containers designed to stack easily without damaging the product or other containers, sometimes with interlocking features.
Tank Containers
Containers used for storage, transport, and dispensing of liquids, typically in bulk or heavy quantities.
Tighthead Containers
Containers with non-removable, attached tops or covers. Tooling boxes are specialized plastic cases with compartments to store punches and dies, available in various sizes and capacities.
Customization of Plastic Containers
Plastic containers can be tailored to virtually any size, shape, or color. Their durability, transparency, and temperature resistance can be engineered to create specialized boxes, jars, and bottles. In the consumer market, plastic containers can also be made food-safe, sterile, waterproof, or designed for microwave use.
Improving Usage of Plastic Containers
A long-term concern with plastic is its increasing brittleness. While some materials offer more resistance, many plastics tend to become brittle over time, making them more prone to breakage.
It’s important to periodically check for cracks or signs of wear. Remember that a plastic container may gradually lose its ability to safely serve its intended purpose.
Microwaving can shorten the lifespan of plastic containers. Whenever possible, transfer food to a microwave-safe dish before heating. If that’s not feasible, try to reduce the microwave time.
Lastly, avoid microwaving plastic lids. Doing so will likely cause them to warp, rendering them unusable.
Standards and Specifications for Plastic Containers
Plastic materials are regulated for food safety, handling, and packaging, with various federal, state, and other organizations establishing regulatory requirements for manufacturers. The following are major organizations that set standards for plastic products or components:
FDA
The Food and Drug Administration (FDA) oversees materials that come into contact with food products, ensuring they are safe for use.
USDA
The U.S. Department of Agriculture (USDA) Food Safety and Inspection Service sets policies for the agricultural food industry. The USDA requires certification of compliance for materials used in food-related applications.
UL
Underwriters Laboratories (UL) is an independent, nonprofit organization. One of their most recognized services is “listing,” which means product samples have been evaluated and meet UL’s established safety standards.
3A-DAIRY
To display the official 3A-Dairy symbol on a storage container, manufacturers must use plastic materials that are formally approved by 3A-Dairy.
NSF
NSF International sets standards for materials used in drinkable water additives, both direct and indirect. Products bearing the NSF symbol indicate that the equipment has been approved by NSF.
USP CLASS VI
The U.S. Pharmacopeia (USP) establishes official standards for health-related products in the U.S., including plastics used to manufacture pharmaceutical containers.
ASTM
The American Society for Testing and Materials (ASTM) provides forums for manufacturers, producers, and consumers to discuss and establish standards.
CANADA AG
Agriculture and Agri-Food Canada and Health Canada serve as counterparts to the USDA and FDA, respectively. Unlike the FDA and USDA, materials in Canada cannot be self-certified by manufacturers without prior agency review and approval.
Proper Care of Plastic Containers
Plastic containers are designed to be durable and safe, but understanding the best care practices can help prolong their life.
Hand washing plastic containers is usually safe, as tap water isn’t hot enough to cause warping. However, heat can damage plastic, and different types of plastic have varying resistance to higher temperatures. Vinyl and film plastics, in particular, are sensitive to heat and may warp easily.
Each type of plastic material responds differently to solvents, including water. It’s important to ensure that only substances compatible with the material come into contact with your container.
Proper handling is essential for maintaining the container’s intended use and appearance. Even harder plastics can scratch easily, so avoid rough handling.
If you’re using a dishwasher, place plastic containers on the bottom rack to minimize exposure to high temperatures. Always remember that excessive heat can damage the plastic.
In some cases, plastic containers may develop stubborn stains that regular washing can’t remove. A simple solution is to mix warm water and baking soda into a paste and leave it in the container overnight to lift the stains.
Odors can also be an issue, but rinsing the container with vinegar for a few minutes will help eliminate most unwanted smells.
How to Choose the Right Plastic Container Manufacturer
Plastic products are in high demand, especially plastic storage containers, with a strong, growing market. Building a reliable relationship with a competent plastic manufacturer is crucial for any business. As a purchaser, you understand the significance of securing high-quality products promptly and at an affordable price.
With hundreds of commercial plastic containers available, it’s essential to find a manufacturer that aligns with your specific needs. Even a good manufacturer may not always be the best fit for your requirements—what matters most is whether they can meet your precise specifications.
Check if the manufacturer offers containers in the desired shapes and if they can accommodate additional processing needs like folding or stamping.
If you're looking for a custom design, ensure that the manufacturer has the expertise to transform your concept into a functional, cost-effective solution. Can they provide supplementary services, such as project design, packaging, and implementation?
Location is often a key factor, and pricing should always be considered when choosing a manufacturer.
Ensure the manufacturer adheres to the regulatory standards relevant to your needs.
The manufacturer’s reputation plays a vital role in evaluating their performance. Look for one with a strong track record of reliability and delivery, and credibility within the industry.
Plastic Container Terms
Blow Mold
A method of creating hollow objects by extruding plastic into a chamber, where air is blown to expand the plastic, taking the shape of the mold cavity.
British Thermal Unit (BTU)
The amount of heat required to raise the temperature of one pound of water by one degree Fahrenheit.
Coextrusion
A manufacturing technique in which plastic containers are created with walls consisting of two or more layers made from different materials. This process often incorporates recycled plastics.
Extrusion
A widely-used plastic container processing technique where plastic resins are melted, heated, and pumped through a system for shaping into containers.
HazMat
Hazardous materials, with standards set by the Environmental Protection Agency (EPA) regarding the ability of plastics to handle certain hazardous substances.
High Density Polyethylene (HDPE) Colored (Pigmented)
Used in packaging products such as bleach, liquid detergents, motor oil, and other household and automotive items. These containers typically bear the number "2" in the recycling symbol.
High Density Polyethylene (HDPE) Natural (Non-pigmented)
Often used for containers holding dairy products, juices, and other household goods. These containers are also marked with the recycling number "2."
High Density Polyethylene (HDPE) Wide
These containers, available in both natural and pigmented versions, are used for items like butter, food products, medicine bottles, and 5-gallon buckets. They usually feature the recycling symbol with the number "2."
Injection Mold
A process where heated plastic granules are injected under pressure into a mold, where the molten plastic hardens to form the container shape.
In-line Fluorinated
Describes the chemical modification of HDPE containers' interiors with fluorine gas during production, creating a solvent-resistant barrier, ideal for packaging janitorial, industrial, and consumer products.
ISO Container
Intermodal shipping containers used for transporting freight across various transport modes like rail and ship. Typical sizes include 20 and 40 feet, with standard widths of 8 feet and standard heights of 8 feet 6 inches or 9 feet 6 inches.
Low Density Polyethylene (LDPE)
Commonly used for plastic shrink-wrap, bags, garment bags, dry cleaning bags, and squeezable plastic food bottles.
Monomer
A simple compound that can chemically bond to form a polymer, which is the core building block of plastic containers.
Polyethylene Terephthalate (PET) Slim
Used for clear or colored containers for cosmetics, water, salad dressings, and cleaners. These containers typically display the recycling number "1."
Polymer
A natural or synthetic compound made up of repeated small units, forming the structure of materials like rubber and plastics.
Polypropylene (PP)
Common in plastic food containers, including margarine and yogurt containers, caps for bottles, and wrappers that replace cellophane.
Polystyrene (PS)
Used for products like egg cartons, fast food trays, disposable cutlery, cups, and compact disc cases.
Polyvinyl Chloride (PVC)
Found in containers such as food wrap, vegetable oil bottles, and blister packaging.
Recycling
The process of collecting, sorting, processing, and converting discarded materials back into raw materials, which are then used in the production of new plastic containers.
Resin
Polymers that are organic and either naturally occurring or synthetically made, with high molecular weight and no definitive melting point, commonly used in plastic container manufacturing.
Rigid Plastic Containers
Plastic containers that maintain their shape when filled or empty, including molded plastic containers, but excluding plastic storage bottles.
Rotational Molding
A method where hollow molds are filled with powdered resin, and the mold is rotated inside a furnace, causing the powder to stick to the mold. The mold is cooled with water as the plastic hardens into a hollow shape.
Tare Weight
The weight of an empty plastic container before it is filled with product.
Thermoforming
The process of heating a thermoplastic sheet and forming it into the desired container shape using heat or pressure.
More Plastic Containers Information