Plastic Tubing
Plastic tubing encompasses a wide range of tubes and pipes made from plastic materials.
Its adaptability has made plastic tubing essential across numerous industries, including medical, aerospace, and beverage sectors.
Applications of Plastic Tubing
The uses for plastic tubing are vast, but they typically revolve around transferring fluids, gases, or certain solids from one location to another.
Plastic tubing is often preferred over alternatives like steel due to several key factors. First, it can be designed to be more flexible than other types of tubes and pipes. Second, plastic offers a broad selection of material choices, enabling manufacturers to produce tubing that can handle extreme industrial conditions, including high temperatures and pressures, as well as everyday applications. Additionally, plastic tubing is generally more cost-effective than comparable options.
Plastic tubing is utilized across nearly every industry that requires the conveyance of materials. It's a go-to solution for any process that involves moving fluids, gases, or solids from one place to another. Some of the key industries that rely on plastic tubing include:
- Medicine and Pharmaceuticals: Used for intravenous drug delivery, blood transfusions, and numerous other medical applications.
- Aerospace Engineering: Employed in fuel systems, hydraulics, and other fluid transfers, with similar uses in automobiles and mechanical devices.
- Water Management: Essential for plumbing, water treatment, irrigation, and drainage systems.
- Agriculture: Used extensively on farms for transferring liquids, bulk solids, and other materials.
- Fuel: Integral to piping systems for liquid and gaseous fuels, such as gasoline, natural gas, and butane.
History of Plastic Tubing
The history of plastic tubing closely mirrors the broader history of plastic itself.
While pinpointing the exact inventor of the first plastic tubes is difficult, the creation of parkesine in 1856 marks the birth of the first man-made plastic. Over the next century, various forms and applications of plastics were developed, with chemical breakthroughs during World War I fueling a surge in usage and innovation by the 1940s and 1950s. As new technologies emerged, plastic tubes began to replace older materials in many industries. For example, plastic catheters for intravenous delivery were first used in medicine in 1945.
Today, plastic tubing is an essential and widely used component in virtually every industry and field across the globe.
Plastic Tubing Production Methods
There are two primary methods for manufacturing plastic tubes, each with its own advantages and drawbacks. These methods are plastic pultrusion, where material is pulled through a die, and plastic extrusion, where material is pushed through a die.
Pultrusion is a process where fibers are pulled through a shaped die while resin is simultaneously injected, resulting in plastic tubing with fibers oriented along the tube's length. This gives the tubing exceptional strength for bending and pulling applications. However, this orientation of fibers makes pultruded plastic tubing less suitable for applications that involve torque or crushing forces, as it doesn't offer the same level of strength in those areas.
Extrusion, in contrast, allows for a much wider range of material properties and can be performed at high speeds with high production volumes, while keeping costs relatively low. The extrusion process involves melting raw plastic and forcing it through a shaped die, creating a consistent cross-section or profile.
Materials Used to Produce Plastic Tubing
Plastic tubing can be made from a wide range of materials, each offering unique properties suited to specific applications. Below are some common materials used for manufacturing plastic tubing:
Acrylic
Acrylic tubing is well-known for its excellent optical clarity, making it ideal for applications where visibility inside the tube is essential. It is commonly used in lighting, aquariums, storage, and industrial settings. Acrylic tubing is typically created through a casting process and offers durability and versatility.
Cast Acrylic
A highly durable thermoplastic with glass-like properties, cast acrylic tubing is stable in various environments and offers resistance to wear and corrosion. It is lightweight and shatter-resistant.
PVC
PVC tubing is valued for its corrosion resistance, flexibility, flame retardancy, and immunity to heat shrinking. It provides excellent physical and electrical properties and is commonly used in plumbing, electrical, and construction applications.
Latex
Latex tubing is known for its ability to return to its original shape after being stretched. It maintains flexibility in low temperatures and has high holding strength, making it suitable for applications requiring elasticity.
CPVC
CPVC is similar to PVC but with enhanced resistance to corrosion at higher temperatures, making it suitable for hot water piping and other demanding applications.
Fiberglass
Fiberglass tubing is used in high-temperature applications and in areas requiring abrasion resistance. It is naturally RF transparent and non-conductive, making it ideal for radome and communication applications where electrical conductivity is a concern.
Nylon
Nylon tubing is strong and abrasion-resistant, making it ideal for high-pressure and high-temperature applications. It resists corrosion from chemical solutions and is highly versatile for use in hydraulic hoses, vacuum lines, fuel lines, and more.
Polycarbonate
Polycarbonate tubing offers a strong, lightweight solution that balances transparency and durability. It is commonly used in industrial and medical applications due to its flame and impact resistance, with customizable thickness options available.
Polyethylene
Polyethylene tubing, offers a strong, lightweight solution that balances transparency and durability. It is commonly used in industrial and medical applications due to its flame and impact resistance, with customizable thickness options available.
Polystyrene
Polystyrene tubing is lightweight, flexible, and durable. It is often used for transferring fluids and gases and has excellent resistance to vapor and moisture. It can handle a variety of chemical compounds.
Silicone
Silicone tubing, which is rubber-like, is non-toxic, versatile, and resistant to extreme temperatures. It is widely used in medical applications due to its cleanliness and inertness.
Vinyl
Vinyl tubing is versatile, offering chemical resistance, low weight, high strength, non-toxicity, and transparency. It is used in a wide range of applications across various industries.
Polypropylene
Polypropylene tubing can be produced in an optically clear form and offers a higher melting point than polyethylene, making it suitable for more demanding applications.
HDPE or High Density Polyethylene
HDPE tubing is popular in industrial and infrastructure applications due to its high strength-to-density ratio and resistance to shattering, corrosion, and failure compared to materials like steel and PVC.
PTFE
Also known as Teflon tubing, PTFE is highly flexible, with excellent resistance to corrosive liquids and gases. It has a broad temperature range and is used in laboratories, chemical processes, and high-temperature environments.
XLPE High-Density Cross-Linked Polyethylene
XLPE tubing is used in chemical applications where standard HDPE is insufficient. It offers enhanced properties for demanding environments.
Plastic Tubing Design Factors
When selecting the ideal tubing for an application, several design factors must be taken into account. These include, but are not limited to:
- Strength
- Diameters
- Wall thickness
- Flexibility
- Cost
- Fittings
- Load capacity
- Color
- Length
- Performance characteristics
- Stretchability
- Corrosion resistance
- Coatings
- Microbial properties
- Toxicity concerns
- Maintenance requirements
Characteristics of Plastic Tubing
Plastic tubing is a versatile product used in a wide range of applications. Often, its effectiveness depends more on the fittings and devices connected to the tube than the tube itself.
In certain cases, like drainage systems, the tubing serves the purpose of providing a clear path for fluid flow. For instance, a corrugated tube placed correctly in a yard can help prevent puddles, erosion, or flooding in basements without requiring additional components.
The characteristics of plastic tubing can also vary greatly depending on the material used and the production method employed.
Advantages of Plastic Tubing
The versatility of plastic is what makes plastic tubing indispensable across numerous industries. It can be engineered to be as rigid and strong as metal tubing or as flexible as needed, while also being capable of withstanding extreme temperatures, pressures, and corrosive environments. These qualities can be achieved through the use of appropriate materials and manufacturing techniques. Ultimately, the effectiveness of plastic tubing depends on the expertise of the manufacturer you choose. When in the right hands, plastic tubing can provide highly effective and cost-efficient solutions for nearly any application.
Plastic Tubing Accessories
Plastic tubing is seldom effective on its own without the proper fixtures and connectors to ensure secure, reliable seals. When considering plastic tubing for a particular application, it's important to factor in the necessary fittings and how they will integrate with the tubing.
Some accessories you might need to take into account include:
- Fittings
- Valves
- Connectors
- Couplings
- Inserts
- Joints
Proper Care of Plastic Tubing
When maintaining plastic tubing, it's important to keep the properties of the materials in mind at all times. Regularly check for signs of corrosion, cracks, tears, and leaks based on your application needs. While many types of plastic tubing are designed with fail-safes in place, others may be more prone to shattering or catastrophic failure. For these, stay especially vigilant and address any issues promptly to prevent further damage.
If you're unsure how to properly care for a specific type of plastic tubing, it's a good idea to consult with your engineers or manufacturer for advice. This can help prevent costly or hazardous mistakes in the future.
Plastic Tubing Compliance and Standards
Various industries have specific recommendations or strict regulations regarding the materials and specifications for plastic tubing used in certain applications. For instance, surgical tubing and drinking straws must adhere to safety and non-toxicity standards. Fuel piping systems require tubing that is both reliable and secure, while industrial tubing must be designed to withstand the particular environmental challenges of that industry.
Given the wide range of uses for plastic tubing, there is no one-size-fits-all standard. It’s important to research the standards and compliance requirements for your specific application beforehand. Alternatively, partnering with a plastic tubing manufacturer who is knowledgeable about compliance can ensure the correct standards are met for your needs.
Choosing the Right Plastic Tubing Manufacturer
With the wide variety of plastic tubing options and applications available, it's crucial that your manufacturer meets your specific needs rather than adhering to an idealized standard.
Ideally, you should choose a manufacturer with experience in producing plastic tubing for your particular industry or a similar application. If you're dealing with a highly specialized or unique application and can't find a manufacturer with directly relevant experience, look for one with a solid track record in custom plastic tubing production.
For industries with strict compliance requirements, it's even more critical to select a manufacturer carefully. A reputable contract manufacturer can help ensure compliance, especially if you're not familiar with the specific regulations for your application.
In addition to specific experience, prioritize manufacturers who have strong customer feedback, offer ample references, communicate effectively, and provide transparent pricing and cost breakdowns.
Plastic Tubing Images, Diagrams and Visual Concepts
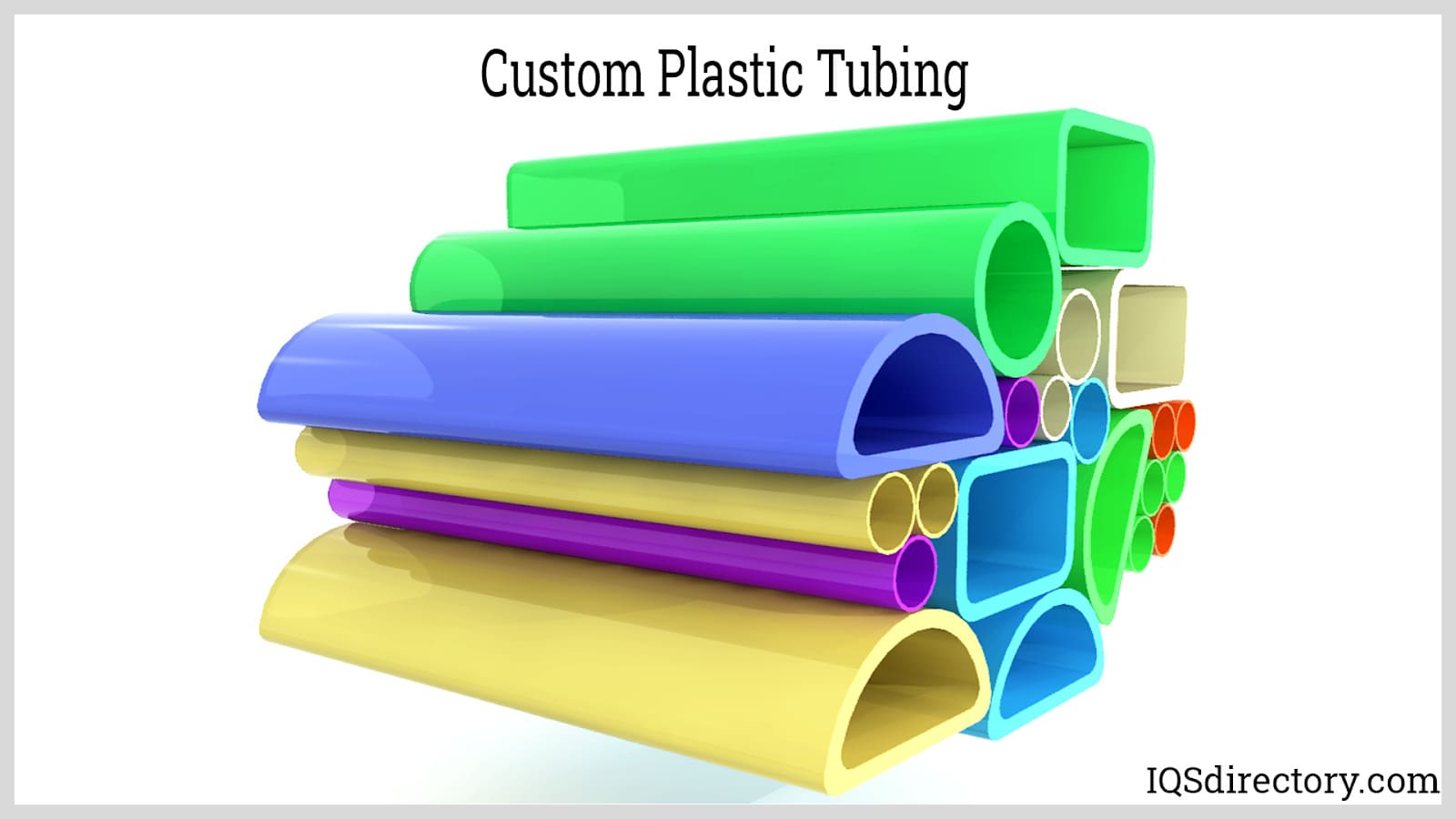
Plastic tubing can be made into many different forms and can serve a variety of proposes.
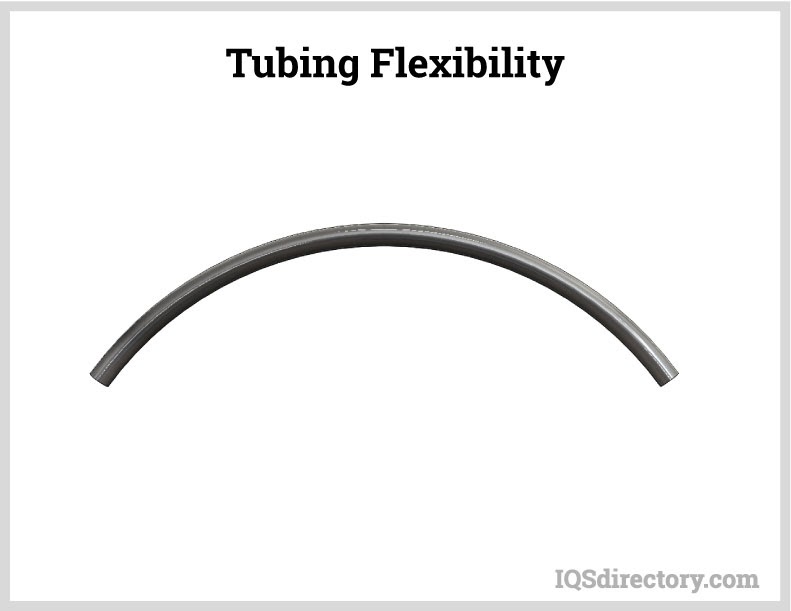
The flexibility of the plastic tube are determined by the material used in manufacturing, which different material are more flexible.
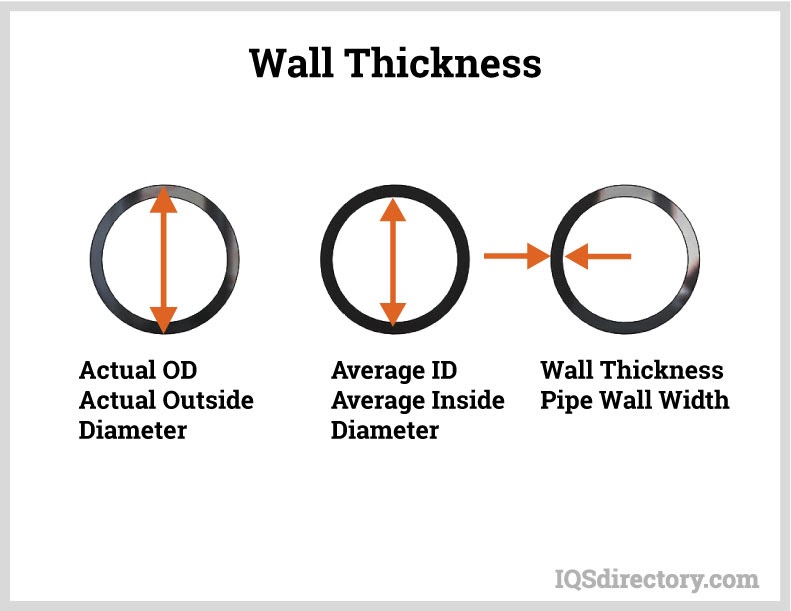
Determining the wall thickness of the plastic tube influences what the tube can be used for.
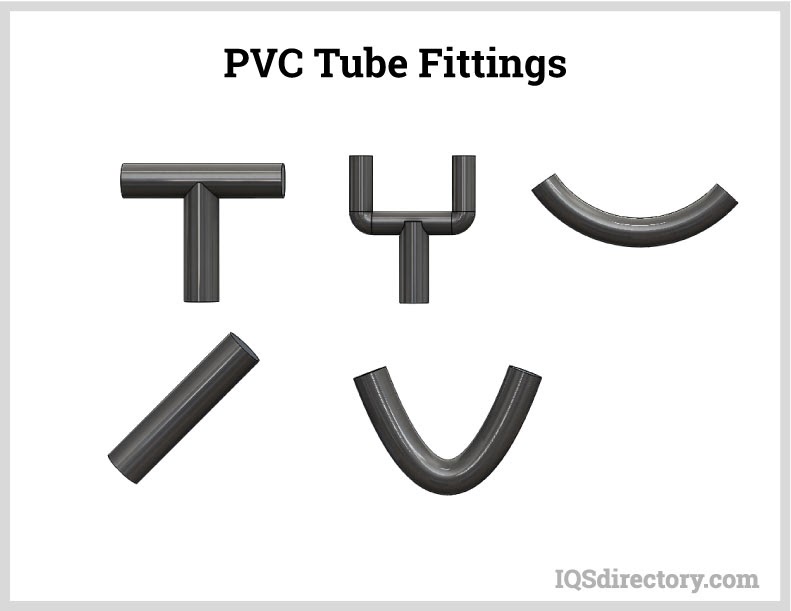
There are a variety of fittings include compression, push to connect, quick turn, threaded, barbed, socket, and flanged. The type of fitting is determined by the usage of the tube.
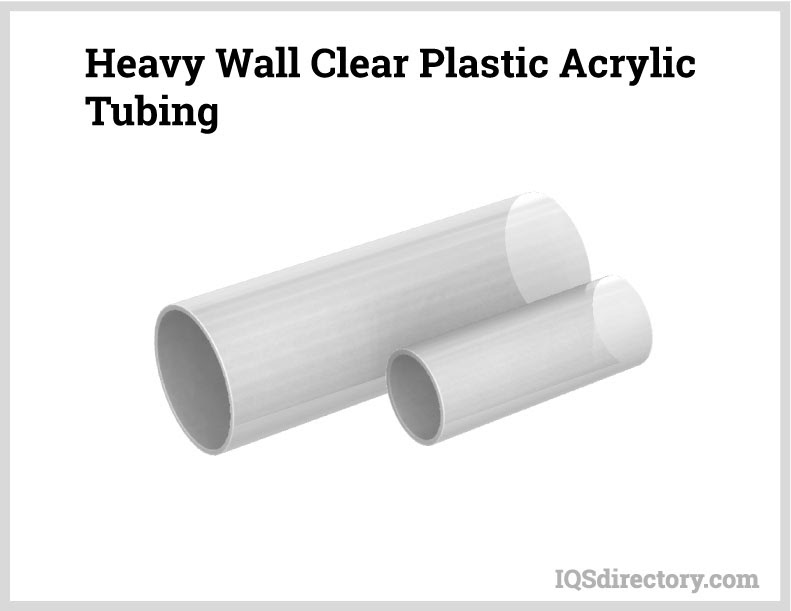
Plastic tubing does not have the same durability of steel, however plastic is able withstand daily wear.
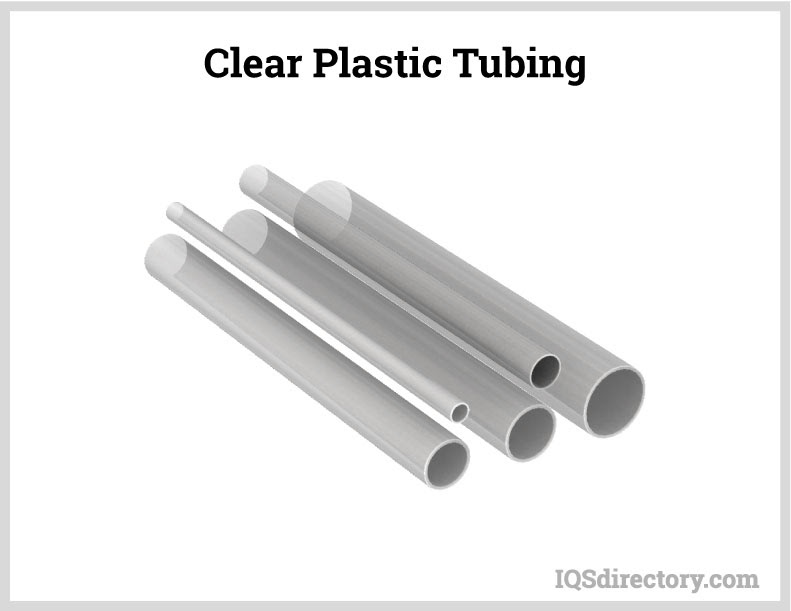
Produced with the same clarity as glass without being fragile with greater strength and endurance.
Plastic Tubing Types
The versatility of plastic tubing has led to a wide array of types and categories, each with distinct functions. Some overlap in design or purpose, while others stand out as unique forms of plastic tubing. Here are some common types of plastic tubing you may encounter:
Corrugated Tubes
These tubes feature ridges and valleys running perpendicular to the length of the tube, offering increased strength but reduced flow. Made from materials like nylon, polyurethane, polyethylene, PVC, and other low-density plastics, corrugated tubing can be customized in various sizes, with 10mm being a standard. It's often used in medical applications, such as anesthesia and respiratory ventilators, and can be either disposable or reusable.
Clear Plastic Tubing
This refers to any plastic tubing made from transparent materials, allowing visibility of the contents inside.
Heat Shrinkable Tubes
These are designed to shrink when heated, forming a tightly fitting protective covering that provides insulation.
Medical Tubing
Plastic tubing used in medical applications, such as catheters, IV lines, and other surgical equipment.
Plastic Pipes
Typically rigid plastic tubes, these are often defined by their inner diameter and used in plumbing and various other industrial applications.
Pultruded
Any tubing created through the pultrusion process, where materials are pulled through a die to form a specific shape.
Square Plastic Tubing
Tubing designed with a square cross-section, as opposed to the typical circular shape.
Surgical Tubes
These are specialized plastic tubes used for medical procedures, including those for intravenous lines and surgical applications.
Hard Plastic Tubes
Rigid and inflexible tubes, though not as stiff as pipes, made from materials like acrylic and polycarbonate. These tubes are resistant to kinks and abrasions, providing strength and durability in various applications.
Small Diameter Tubes
Plastic tubing with diameters less than 3mm, often smaller than 1mm, and typically used in medical applications. While flexible and weak, they are essential in situations where precision is needed, though they are less durable than larger tubes..
Mini Tubes
These small plastic tubes, made from materials such as polycarbonate, polypropylene, polyethylene, polystyrene, and PVC, are used in a variety of industries, including electronics, medical products, and swab sticks. Mini tubes can be custom-made for clients or purchased in bulk.
Rigid Plastic Tubing
This type of tubing is stiff and unbendable, used in applications requiring strength and stability without the need for flexibility.
Centrifuge Tubes
Custom-made tubes for use in laboratory centrifuges, typically made from high-purity resins or polypropylene. These tubes must be precise to withstand high-speed spinning in laboratories.
Vinyl Tubing
Hollow channels primarily or entirely made from vinyl plastic, a material derived from the vinyl group of chemicals, known for its durability and flexibility in various applications.
Plastic Tubing Terms
Crazing
Small surface cracks that appear on plastic tubing, usually close to the surface.
Brew Tube
A specialized type of tubing used primarily in beer and coffee brewing, designed for the unique needs of these processes.
Ductility
The ability of plastic tubing to withstand strain before breaking or failing.
Expansion
A process where the diameter of a plastic tube increases while its wall thickness decreases. This technique is commonly used to create heat shrinkable tubing.
Extrusion
A process in which solid plastic resin is melted and pushed through a heating chamber by a screw to form plastic products.
Fish Eyes
Small, irregular masses found in transparent plastic tubing, caused by incomplete blending during the manufacturing process.
Flaring
A method of increasing the diameter of a plastic tube by applying mechanical pressure from the inside.
Jacket
The outer layer of a dual-wall heat shrinkable tube.
Latex
A polymer solution, often referred to as rubber, consisting of water and polymer.
Liner
The inner part of a dual-wall heat shrinkable tube.all.
Polymerization
A chemical process, often catalyzed, where simple molecules combine to form more complex, chain-like compounds (polymers).
Polystyrene
A transparent, flammable plastic that is known for its excellent electrical and thermal insulating properties, high strength, and impact resistance.
Polyurethane
A versatile class of thermoplastic polymers that offer good resistance to solvents and abrasion and can be found in either solid or foam forms.
Pultrusion
A manufacturing process that creates reinforced plastic shapes with consistent cross-sections by pulling resin-wetted reinforcing fibers through a heated steel die.
Plexiglass Tubes
Transparent thermoplastic, also known as acrylic, often used as an alternative to glass due to its high optical clarity, strength, light transmission properties, and affordability.
Shore Hardness
A scale used to measure the hardness of materials, with the "A" scale being used for plastic tubing. Higher numbers indicate harder materials.
Strain Relief
A technique in which plastic tubing is used to cover an object, reducing stress on the object by adding extra support and stiffness.
Stress Cracks
Small cracks, typically found in clusters, which occur in plastic tubing due to mechanical stress.
Thermoset
A type of material that becomes permanently hardened after undergoing a chemical reaction and cannot be reshaped even when reheated.
VW 1
A type of material that becomes permanently hardened after undergoing a chemical reaction and cannot be reshaped even when reheated.
More Plastic Tubing Information