Plastic Materials
“Plastics” refers to a broad group of materials and products created by processing polymer resins. These large molecules, called macromolecules, are made up of repeating smaller units known as monomers, linked by covalent bonds. This basic structure results in a wide variety of plastics, each with unique chemical properties, producing numerous types such as acrylics and polystyrene products. Plastics are recognized for their distinct features, including tensile strength, chemical and wear resistance, dimensional stability, machinability, thermal and impact resistance, optical clarity, moisture absorption, and electrical insulation.
Quick links to Plastic Material Information
The History of Plastics
Early Use of Plastics
Plastics have a history that extends thousands of years. Early forms of plastics were sourced from natural, organic polymers such as proteins found in eggs and blood. As early as 1600 BC, Mesoamerican civilizations used natural rubber to create objects like figurines, bands, and balls. In the Middle Ages, treated cattle horn—using casein from milk proteins—was an early example of plastic material.
Plastics in the 1800s
The era of synthetic plastics began in the 1800s. Charles Goodyear’s discovery of vulcanization was a key breakthrough, demonstrating natural rubber could be thermoset. The first synthetic plastic, nitrocellulose (Parkesine), was made by treating cellulose with nitric acid and dissolving it in alcohol, then hardening it into a moldable, elastic, transparent material that could be colored. Patented by Alexander Parkes in Birmingham, England in 1856, Parkesine was presented at the 1862 Great International Exhibition, winning a bronze medal. In 1868, John Wesley Hyatt developed celluloid, a similar material, as a substitute for ivory in billiard balls. In 1897, Germans invented casein plastics from milk proteins and formaldehyde. Arthur Smith patented a formaldehyde resin process in 1899, which was later improved by Leo Hendrik Baekeland in 1907 with the invention of Bakelite—the first fully synthetic, commercially successful plastic.
Plastics in the 1900s
In 1908, Jacques E. Brandenberger invented cellophane, a clear, flexible film first designed for waterproofing fabric. Although not used for its original purpose, cellophane became popular as a packaging material, notably for candy. After World War I, advancements in chemistry spurred rapid growth in plastic development. During World War II, plastics were mass-produced, including polystyrene (PS), polyvinyl chloride (PVC), polyethylene, and polyethylene terephthalate (PET). The 1950s saw innovations like expanded polystyrene from Dow Chemical, used for cups, packaging, and insulation, and polypropylene entered mass production in 1957, three years after its discovery.
After the 1950s, the plastics industry continued to diversify, with more precise manufacturing methods. More recently, efforts have focused on sustainable polymers due to environmental issues with non-biodegradable plastics. Bioplastics made from sugarcane-derived ethanol are being developed. Until bioplastics become widely available, recycling thermoplastics is recommended for reuse. Companies working on sustainable thermoplastics can be found through IQS Directory’s listings.
The Benefits of Plastic
While recycling is essential, plastics provide many significant benefits. Their versatility allows for easy shaping, coloring, and texturing to meet exact needs, and they can be engineered to deliver a wide range of characteristics. Plastics are lightweight, strong, cost-effective, and easy to process. Their ability to be recycled adds to their environmental value.
Plastic Production Process
Raw Material Production
The creation of plastics involves many production techniques. Methods such as suspension, emulsion/dispersion, mechanical mixing, solution, and bulk processes are used to produce resins, powders, gels, and liquids. Thermosetting plastics are generally processed just once, while thermoplastics are often provided in pre-formed solid shapes for ease of handling or direct use.
Plastic manufacturers may also incorporate additives like heat stabilizers, lubricants, fillers, and plasticizers to customize materials for specific applications, affecting properties such as color, strength, density, temperature performance, durability, and resistance to various conditions.
Thermoplastics vs. Thermosetting Plastics
Plastics, whether derived from synthetic, natural, or organic sources, are divided into two main types: thermoplastics and thermosetting plastics. Understanding the distinction is important for selecting materials. Thermoplastics can be melted and reshaped repeatedly, becoming soft with heat and rigid when cooled, though they may turn brittle in low temperatures. Thermosetting plastics, on the other hand, are ideal for cold environments but cannot tolerate high heat and cannot be remolded after curing. Delivered as two-part liquids or premixed solids, thermosets have more limited uses and are provided as raw materials or finished products. Cure methods include air setting, film drying, anaerobic curing, hot melt, cross-linking, room temperature curing, and vulcanization, selected based on the product requirements and manufacturing processes.
Manufacturing Processes
Common plastic shapes such as sheets, pipes, profiles, and rods are typically produced using plastic injection molding or extrusion. Films are made through blown film extrusion, where the material is stretched to precise dimensions. Other manufacturing techniques include foam extrusion, rotational molding, machining, vacuum and pressure forming, thermoforming, casting, pultrusion, welding, and grinding. These methods apply heat and pressure, then cool the material to achieve the desired shape.
Plastic Images, Diagrams and Visual Concepts
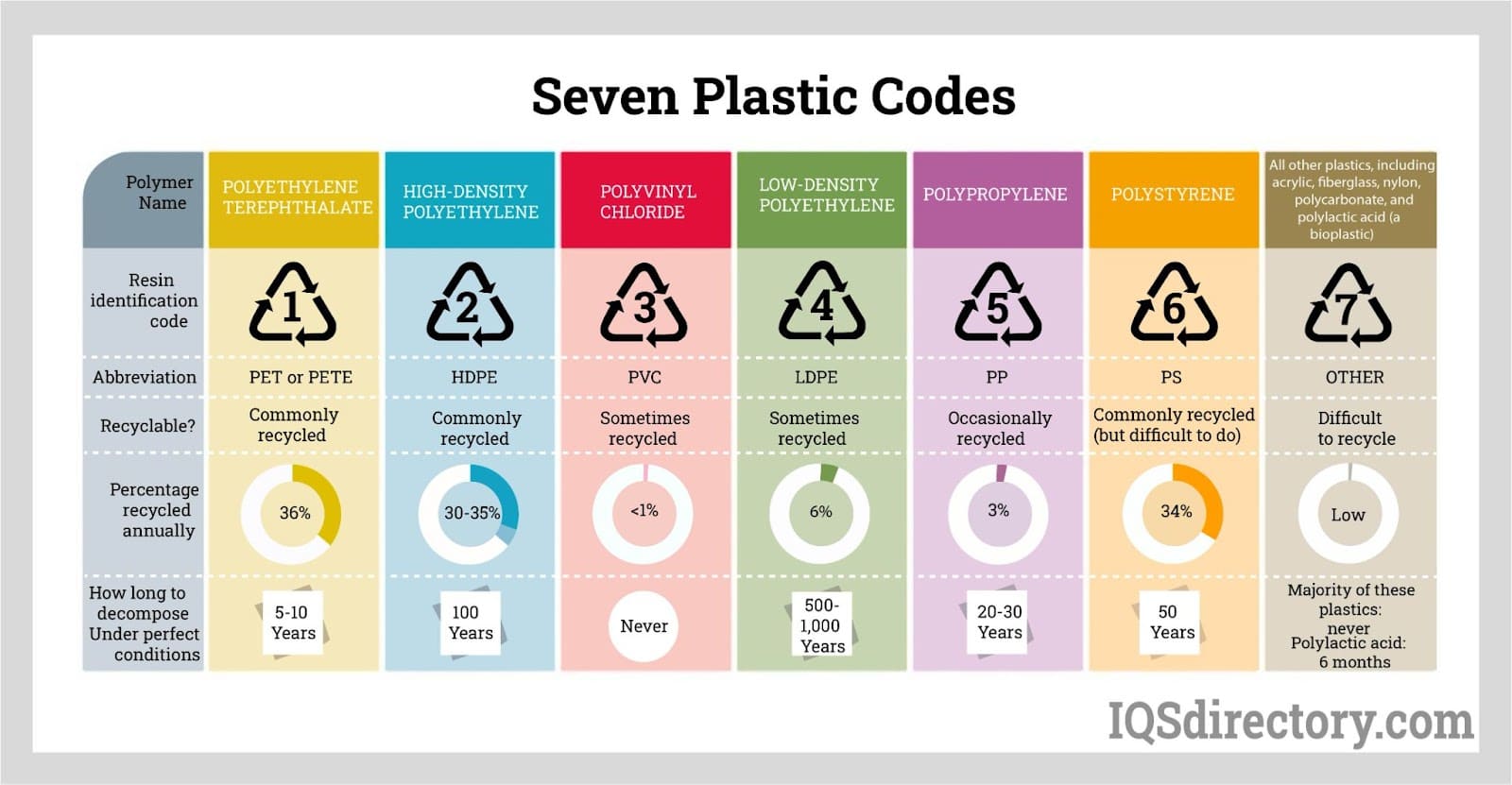
The seven main types of plastics classified for manufacturing and recycling.
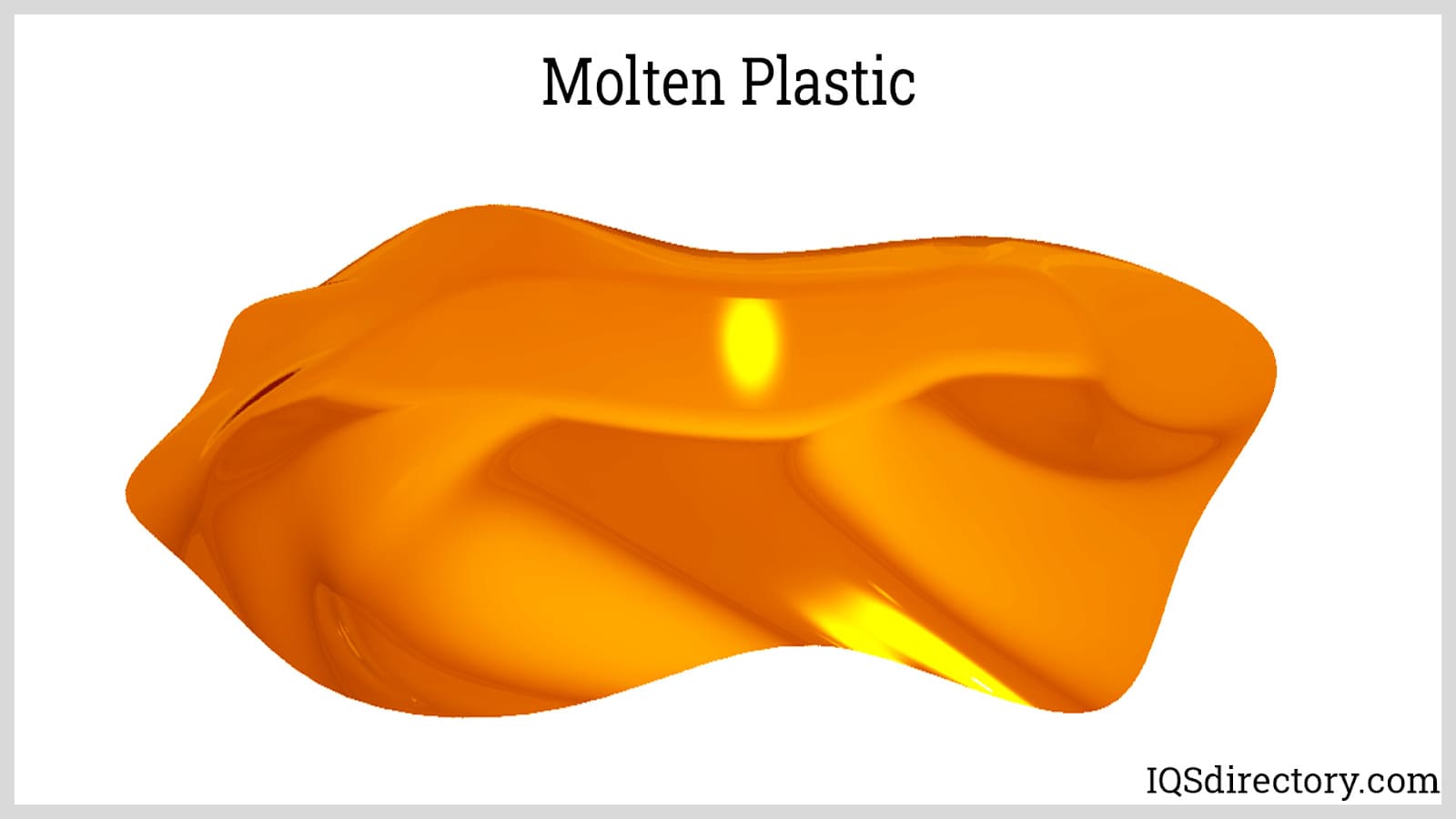
Molten plastic at high temperature, ready for molding or processing.
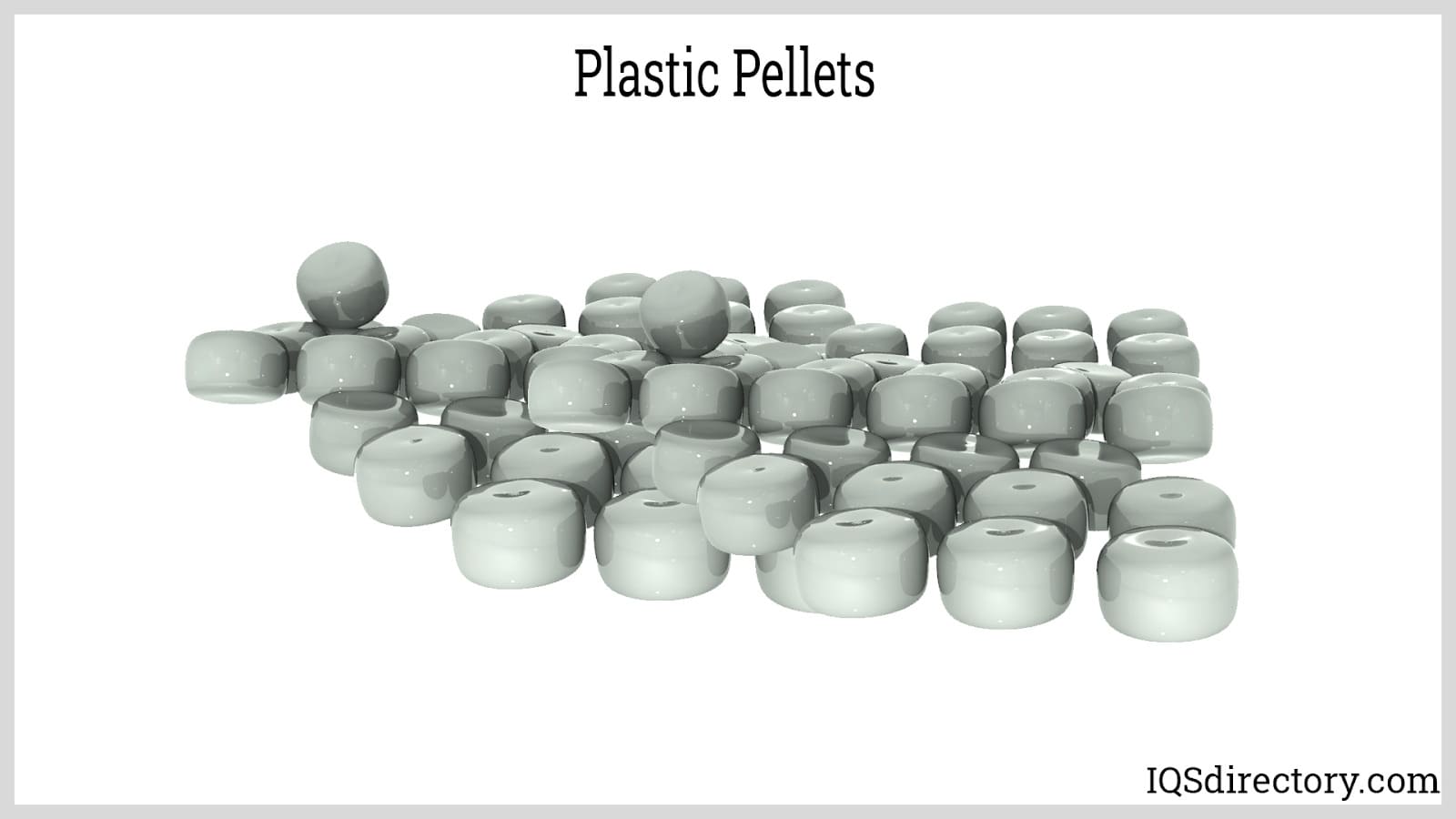
Plastic pellets in raw form, used in manufacturing to produce finished goods.
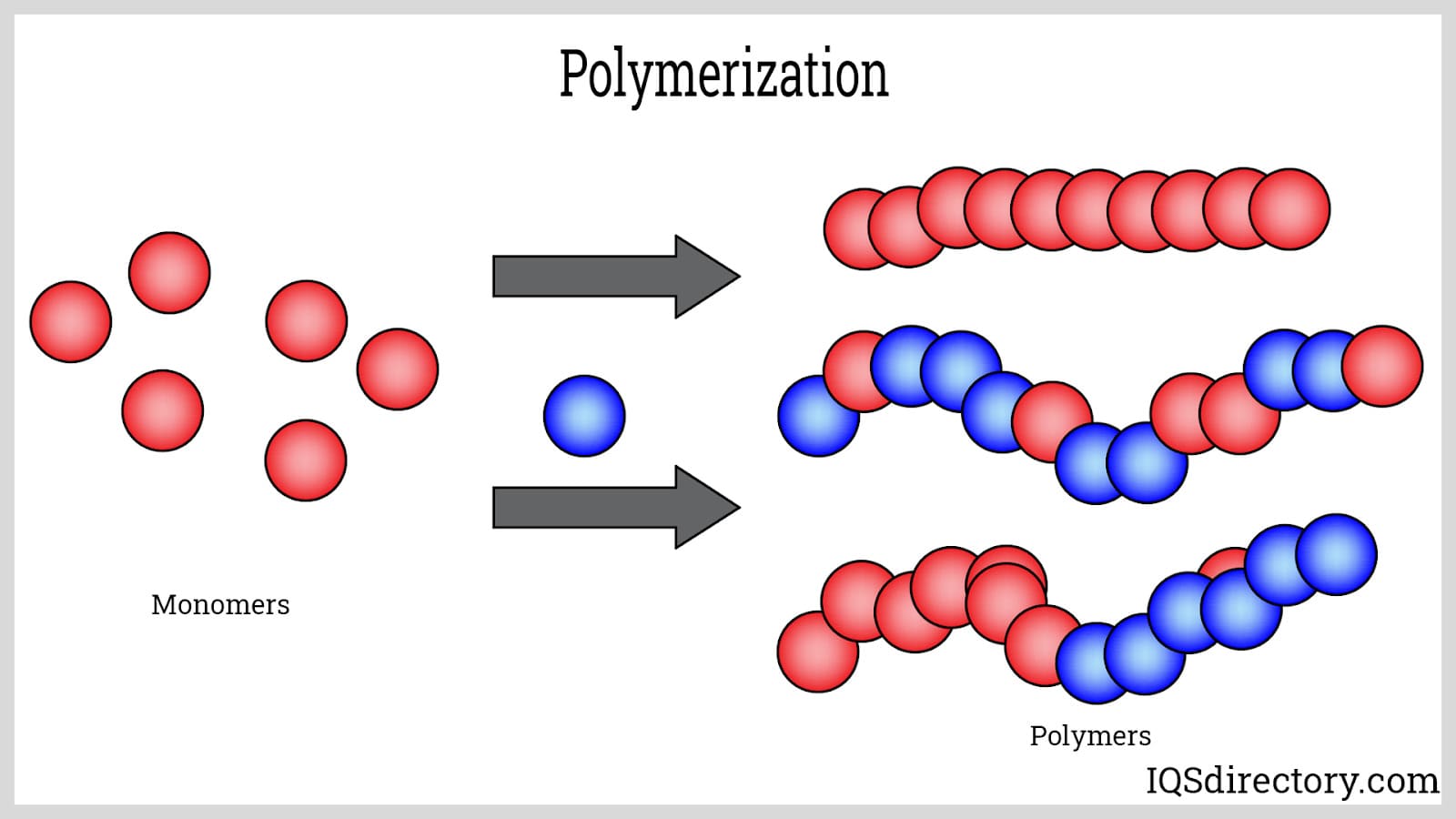
Polymerization bonds monomers together to create polymer chains for plastic production.
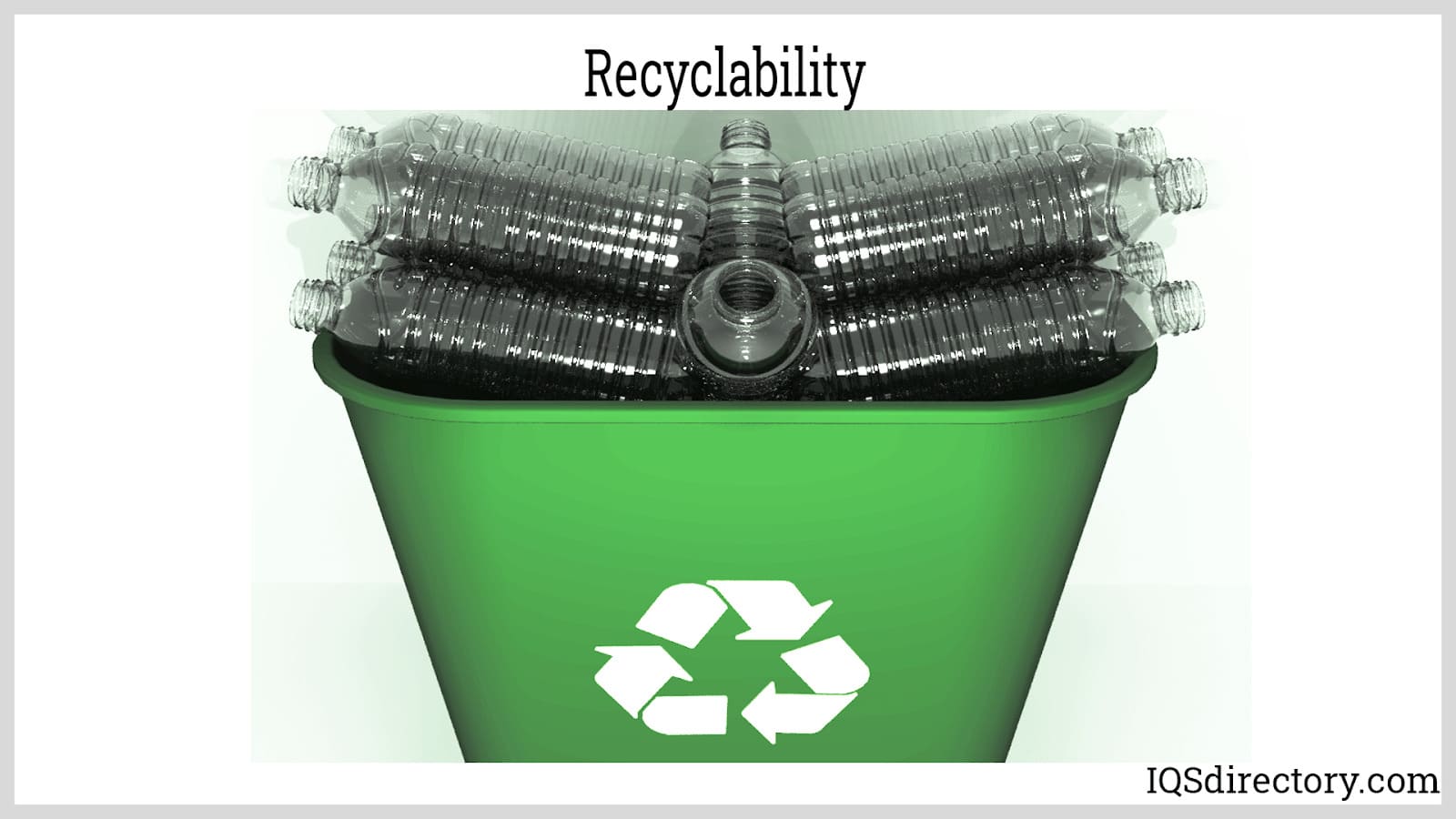
Plastics that can be recycled are melted and reshaped into new products, supporting sustainability efforts.
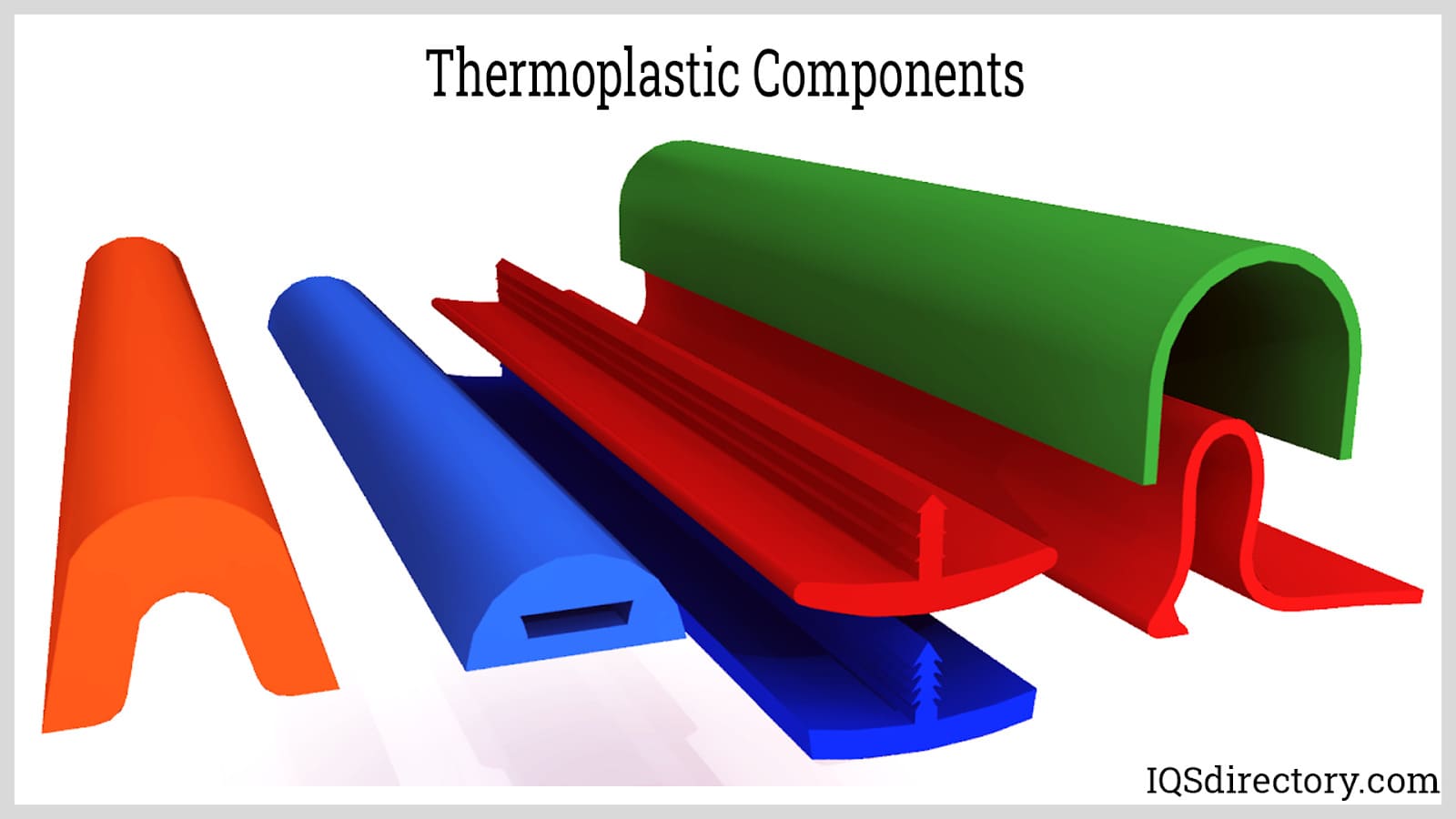
Thermoplastics are known for their durability and resistance to chemical damage.
Types of Plastic Produced
The plastics industry produces a wide variety of materials, including polyethylene, polystyrene, high-density polyethylene (HDPE), low-density polyethylene (LDPE), polyoxymethylene, polyvinyl chloride (PVC), and others.
Polyethylene
Polyethylene is a widely used plastic found in products such as artificial joints, shampoo bottles, and milk cartons.
Polystyrene
Polystyrene, often known by the trade name Styrofoam™, is essential for insulation but is not recyclable.
High-Density Polyethylene (HDPE)
HDPE is a petroleum-based thermoplastic valued for its strength, lightness, and solvent resistance. It's used in bottle caps, swimming pool parts, automotive fuel tanks, and food containers.
Low-Density Polyethylene (LDPE)
LDPE, the first mass-produced polyethylene, continues to be used for its chemical resistance, flexibility, and toughness. It is commonly seen in containers, snap-on lids, plastic wrap, and packaging materials.
Polyoxymethylene
Polyoxymethylene, also called acetal or Delrin, is often used as a substitute for metal in automotive and construction applications due to its strength and machinability.
Polyvinyl Chloride (PVC)
Polyvinyl chloride (PVC or vinyl) is available in rigid and flexible forms and is the world’s third-most produced polymer. It is used in building materials, packaging, cards, plumbing, insulation, inflatable products, and more.
ABS (Acrylonitrile-Butadiene-Styrene)
ABS resins offer high strength and resistance to most chemicals and stains, created from the polymerization of acrylonitrile, styrene, and butadiene.
Acrylic
Acrylic plastics are manufactured from transparent, thermoplastic resins derived from acrylic acid and petrochemical sources.
Fluoroplastic
Fluoroplastics, such as Teflon, resist heat, moisture, and abrasion, making them suitable for valves, gaskets, and bearings. They are also known for their flexibility.
Phenolic Plastic
Phenolic plastics, in the same group as polyester and vinyl ester, are made from phenol and formaldehyde. They are strong, comparable to iso-polyester, and provide high fire safety performance.
Polycarbonate
Polycarbonate is prized for excellent light transmission and dimensional stability, making it a leading transparent thermoplastic for electronic housings, machine guards, and aircraft windows.
Polypropylene (PP)
Polypropylene offers flexibility at low temperatures and strong chemical resistance. It is commonly used in banners and a variety of commercial products.
Polyurethane
Polyurethane is a tough plastic with high abrasion resistance and flexibility, used to make bumpers, gears, gaskets, and roller covers.
Applications of Plastics
Plastics are used in a broad spectrum of industries and sectors, including industrial, commercial, and residential settings. Sectors such as chemical and food processing, water treatment, oil and gas, healthcare, pharmaceuticals, aerospace, automotive, construction, and more depend on plastic components and solutions.
Plastic Products Produced
Plastics are available in a variety of stock forms such as plastic rods, plastic sheets, and plastic films. These materials can be further processed through fabrication or machining to create countless products. Examples include tubing, packaging, containers, plates, gears, insulators, medical instruments, toys, instruments, shielding, wraps, panels, bottles, and pipes.
Things to Consider When Purchasing Plastic
When purchasing plastics or plastic products, evaluate the unique properties of each type. Important considerations include thermal resistance, flexibility, environmental impact, durability, sterility, and corrosion resistance. Ensure the materials meet all necessary quality and performance standards.
After selecting the right type or specifications, contact a reputable plastic supplier or manufacturer. At the top of this page, you’ll find a list of trusted plastic companies. Review their profiles or visit their websites for more details. Narrow your choices, then discuss your project requirements, design, budget, timeline, and delivery needs with the companies you shortlist. Assess their communication to judge customer service. After thorough evaluation, select the supplier that best fits your needs.
Global Plastics Market
The global plastics market is highly competitive and rapidly growing. While sourcing plastics internationally, such as from China, can reduce costs, consider these key points before moving production overseas:
Plastic Sustainability
Growing environmental awareness has increased the demand for sustainable plastic production and use. When working with international manufacturers, confirm their commitment to eco-friendly practices and advanced technologies.
Clarity of Costs
Buying plastics globally involves complex logistics, including warehousing, currency exchange, customs, and freight. Make sure you understand all related costs before committing.
Regulations and Tariffs
Stay informed about new regulations that affect your materials or products, and ensure your international suppliers comply with standards recognized in your region. Be aware of applicable tariffs and import fees.
Possible Miscommunication
Working with overseas companies may introduce communication challenges, such as language barriers, time zone differences, and cultural misunderstandings. Even with clear communication, errors can occur, leading to costly mistakes and delays. Returning or exchanging products internationally can be complex, involving paperwork, fees, and lengthy wait times.
Overall, the risks and difficulties of international sourcing often outweigh the benefits. Building trust and maintaining strong relationships is more challenging across borders. Therefore, we recommend working with one of the regional companies listed above.
Plastic Terms
Additive
A material incorporated into a resin to enhance or impart specific properties.
Aging
The process of chemical and physical changes that occur in a material over time due to environmental exposure, which may degrade or improve its properties.
Alloys
Mixtures of polymers or copolymers blended with other elastomers or polymers.
Binder
A resin or substance that binds particles together, providing mechanical strength and ensuring the solidification, uniformity, or adhesion of a coating.
Clarity
The degree to which a plastic material is free from cloudiness or haze.
Composite
A structural plastic material made from a combination of different components.
Compressive Strength
The ability of a plastic to resist forces that would crush or compress it.
Copolymer
A polymer formed when two or more different monomers chemically react to create a compound.
Cure
The process by which polymers are chemically transformed to achieve greater stability and usability, often through heat, radiation, or chemical additives.
Cure Cycle
The duration and specific conditions under which a thermosetting material is cured.
Discoloration
A change in the original color of a plastic caused by exposure to light, chemicals, or environmental conditions.
Forming
The process of reshaping an existing piece of plastic into a new configuration.
Hygroscopic
The tendency of certain plastics to absorb moisture from the environment.
Masterbatch
A concentrated mixture of additives, pigments, or fillers within a base polymer.
Opaque
Plastic materials that do not allow light to pass through.
Plasticizer
A high-boiling liquid or low-melting solid added to hard plastics to increase flexibility by reducing intermolecular forces. Plasticizers vary in their ability to soften and modify plastics.
Plastisol
A mixture of resins and plasticizers that can be converted into continuous films through heat treatment.
Polymer
A natural or synthetic compound with high molecular weight, made up of long chains of repeating units, such as polyethylene or elastomers.
Reinforced Plastics
Plastics strengthened by incorporating high-strength fillers to improve mechanical properties.
Resin
An organic material, usually solid or semi-solid, with high molecular weight, that flows under stress and softens or melts at certain temperatures.
Surfactants
Chemicals that help mix or emulsify incompatible substances by altering surface properties and improving the flow and wetting of liquids.
Thermosets
Plastics or resins that, once cured, become insoluble and infusible and cannot be softened by reheating.
Virgin Material
Plastic material, such as pellets, granules, floc, or liquid, that has not been processed except for initial manufacturing steps.