Pneumatic Conveyors
A pneumatic conveying system is designed to transfer bulk materials from one location to another using air or gas flow as the medium. Air is the most commonly used gas, but other gases such as nitrogen can also be used. An efficient, practical, and economical pneumatic conveying system is essential for transporting bulk materials to a single or multiple destinations.
Pneumatic conveying is primarily used for moving dry bulk and powdered materials through a fully enclosed pipeline. The movement is driven by a combination of pressure differential and the flow of gases, which facilitates the transfer process. Key components of the system include a feeder, air mover, dust collection system, termination vessel, and belt conveyor, among others.
This system is ideal for transferring a variety of materials, including cement, flour, sand, minerals, and food products. However, it is essential that the materials being transported are dry, as paste or slurry materials can cause issues within the system.
Applications of Pneumatic Conveying Systems
Pneumatic conveying systems are essential to a wide range of industries, serving as a critical backbone for operations in many organizations. These systems are designed to meet diverse application needs, providing reliable transport solutions for various materials.
The food packaging industry heavily relies on pneumatic conveying equipment to meet its rigorous hygiene standards. These systems are used to transport a variety of food products, including rice, cereals, sugar, salt, and both animal and pet foods.
In the pharmaceutical industry, pneumatic conveying systems play a crucial role in transferring products while maintaining contamination control. Vacuum conveying systems, in particular, are widely used due to their suction capabilities, ensuring safe and clean product transfer. The chemical industry, which often handles hazardous materials, also benefits from pneumatic conveying systems. These systems help meet environmental protection standards while preventing cross-contamination.
Other industries, such as those dealing with minerals, cement, plastics, and polymers, also utilize pneumatic conveying systems for efficient material handling.
History of Pneumatic Conveying Systems
Pneumatic conveying systems were first introduced in Germany around the 1950s, with their development credited to a man named Gasterstadt. He created the first pressure drop flow meter and conducted experiments using 100 pipes, which laid the foundation for the technology.
In the 1960s, significant advancements occurred when students at Nagoya University in Japan were tasked with developing a solution for reliable material transport in multi-level facilities. Their work led to substantial improvements in pneumatic conveying technology, with some of these students eventually becoming lecturers themselves.
In the United States, industries dedicated considerable resources to further advancing pneumatic conveying systems. This effort ultimately led to the identification of the three primary types of pneumatic conveying systems that are commonly used today.
How Pneumatic Conveying Systems Work
In pneumatic conveying systems, the air pressure within the conveying line is controlled by the air mover, which generates either pressure or a vacuum. The position of the air mover determines whether the system operates under pressure or vacuum. When the air mover is located at the beginning of the system, it pushes air through the line, causing the system to function under pressure. Conversely, when the air mover is positioned at the end of the system, it draws air through the equipment, creating a vacuum. The efficient transfer of material in the pneumatic conveying system relies on properly maintaining the vacuum or positive pressure, as well as the airflow within the equipment.
Categories of Pneumatic Conveying Systems
Pneumatic conveying systems are typically classified into three main categories based on their operating principles: dilute phase, dense phase, and lean phase. These systems can function under either pressure or vacuum.
Dilute Phase
Also referred to as streamflow pneumatic conveying, this is the most commonly used method for transporting materials. Dilute phase conveying utilizes a large volume of air to carry materials at lower pressures compared to dense phase systems. The materials are transported at higher velocities and remain suspended in the air stream. To ensure efficient operation, it is crucial to maintain an appropriate air conveying velocity.
Dense Phase
In dense phase conveying, materials are pushed through the pipe under sufficient pressure to move them in one continuous mass along the entire length of the tube. This method is not ideal for dry bulk solids, as they can cause high friction within the system. Instead, the material and air flow in the pipe in multiple patterns. Dense phase operates under low velocity and a very high-pressure differential. Additionally, there is a variant known as lean phase pneumatic conveying, which operates under a pressure of around one bar. This technique is versatile and effective for conveying a wide range of materials in both pressure and vacuum systems
Alternative Conveying Systems
Screw conveyors are widely used in various industrial applications for efficiently transporting a broad range of bulk materials. They are cost-effective and require minimal maintenance to operate, with their primary function being the transfer of materials between different processes.
Conveyor belt systems provide an affordable and practical solution for moving products from one location to another. They can handle a variety of shapes, weights, and sizes of products, efficiently covering long distances with the use of a single drive.
Components of Pneumatic Conveying Systems
A pneumatic conveyor system consists of the following components:
- A feed system designed to introduce solids into the gas stream while preventing the gas from entering the storage systems.
- A conveyor line, which serves as the main conduit for carrying the material, along with the necessary accessories.
- Equipment responsible for generating the gas flow.
- Solid-gas separation equipment, typically including advanced reverse jet, bag, or centrifugal separators.
Advantages of Pneumatic Conveyors Systems
Pneumatic conveyor systems offer several advantages over traditional equipment like vibrating belts and trays.
Unlike most mechanical conveyors, which are open and allow impurities to escape into the atmosphere, pneumatic systems are fully enclosed and highly flexible. Additional benefits of pneumatic conveying systems include:
- High Transfer Rates: Pneumatic conveyors can transport materials at very high speeds, depending on the particle size of the materials being moved.
- Long-Distance Transfer: These systems are capable of transferring bulk materials over long distances in a short period of time.
- Lower Maintenance: Despite higher initial setup costs, pneumatic conveyors require less maintenance due to their fewer moving parts.
- Reduced Spillage and Dust: With the system being fully enclosed, the risk of spillage is minimized, and dust is rarely an issue.
- Improved Sanitation: Since the bulk material is contained within the system, the likelihood of contamination is significantly reduced.
Increased Safety: The enclosed nature of pneumatic conveying systems reduces operational risks, making them safer to operate.
How to Use a Pneumatic Conveying System
Pneumatic conveyor systems function by using differential air pressure to efficiently move bulk materials from one location to another. Essentially, material introduced at one point of the system is transported to another point through the system.
Pneumatic systems are primarily classified into two types: negative pressure systems, which use a vacuum to pull bulk solids through the pipeline, and positive pressure systems, which use air pressure to push the bulk material along. The application of pressure transforms the bulk materials into an air-like state, allowing them to flow freely within the tube.
Design Aspects of the Pneumatic Conveying System
To ensure the efficiency and reliability of pneumatic conveying equipment, several factors must be carefully considered during the design process. Some of the key considerations include:
Determining Material Bulk Density
Identifying the material’s bulk density is essential for sizing system components such as air sources and vacuum conveyor receivers. The bulk density also helps calculate the amount of compressed air required for the system. Materials with low bulk densities are easier to convey, while materials with high bulk densities require more power and larger vacuum receivers.
Conveying Distance
The distance over which materials must be conveyed is another critical factor. Longer conveying distances necessitate more powerful vacuum pumps to maintain the desired material flow.
Material Characteristics
The properties of the material being conveyed are vital in determining whether it is suitable for pneumatic transport. It is important that materials are dry, as pneumatic systems are not designed to handle paste or slurry-like substances. The material’s specific characteristics guide the design of a customized pneumatic conveyor system. Engineers will ensure the system meets the unique requirements of the materials being transferred while prioritizing accuracy, reliability, and efficiency. Custom options are often developed to minimize maintenance and provide optimal process solutions tailored to specific industrial needs.
Safety and Compliance Issues for Pneumatic Conveyors
Pneumatic conveyor systems are fully enclosed to effectively transport bulk materials while maintaining health and safety standards. Several safety features of the system include:
The enclosed design ensures that pressure is consistently maintained throughout the system, allowing bulk materials to be efficiently moved to their destination. This also prevents contamination of the surrounding environment, as no dust or particles are released into the air, ensuring cleaner air quality.
Additionally, the system is designed to prevent mixing of the bulk materials during transport, ensuring that the materials remain pure and unaffected by other substances.
Overall, pneumatic conveyor systems are safer than traditional transport methods, as they reduce the risk of contamination and ensure that the materials are transported securely to their destination.
Factors to Consider When Selecting a Pneumatic Conveying System
Selecting the right pneumatic conveying system involves several key considerations. The first factor to evaluate is the material's characteristics, as these play a significant role in determining whether a dense or dilute phase pneumatic conveyor system is appropriate. Material properties such as particle shape and size, bulk density, moisture content, friability, hygroscopic nature, and toxicity must all be taken into account.
Next, it's important to assess whether the system will fit in the designated space within the facility. One must consider any potential physical constraints in the area and determine how the system can be configured for optimal performance within those limits.
Another crucial factor is the required transfer rate, which should meet the specific needs of the materials being conveyed. High transfer rates are especially important for perishable materials that require fast and efficient handling.
In summary, pneumatic conveying systems are primarily used for transferring dry solid materials. Proper attention to material characteristics, system suitability for the location, and transfer rate requirements will help in choosing the best system. The right pneumatic conveying system can support the growth of industries like food and chemicals by ensuring efficient, uncontaminated transport of materials while maintaining a clean environment. These systems are recognized for their speed, efficiency, and reliability.
Pneumatic Conveyors Images, Diagrams and Visual Concepts
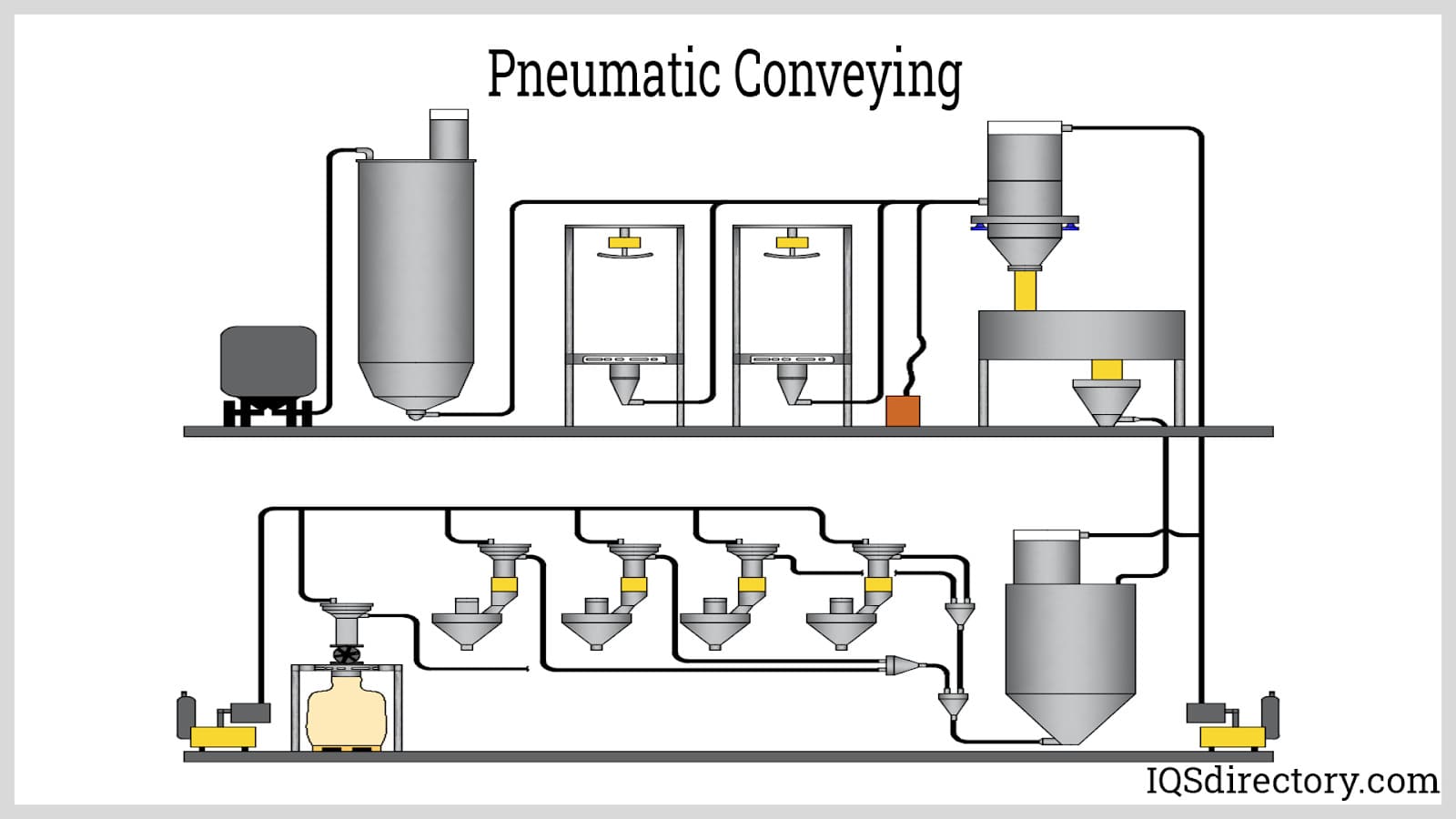
A method for transferring bulk materials, like powders and granules using air or gas to different processing centers.
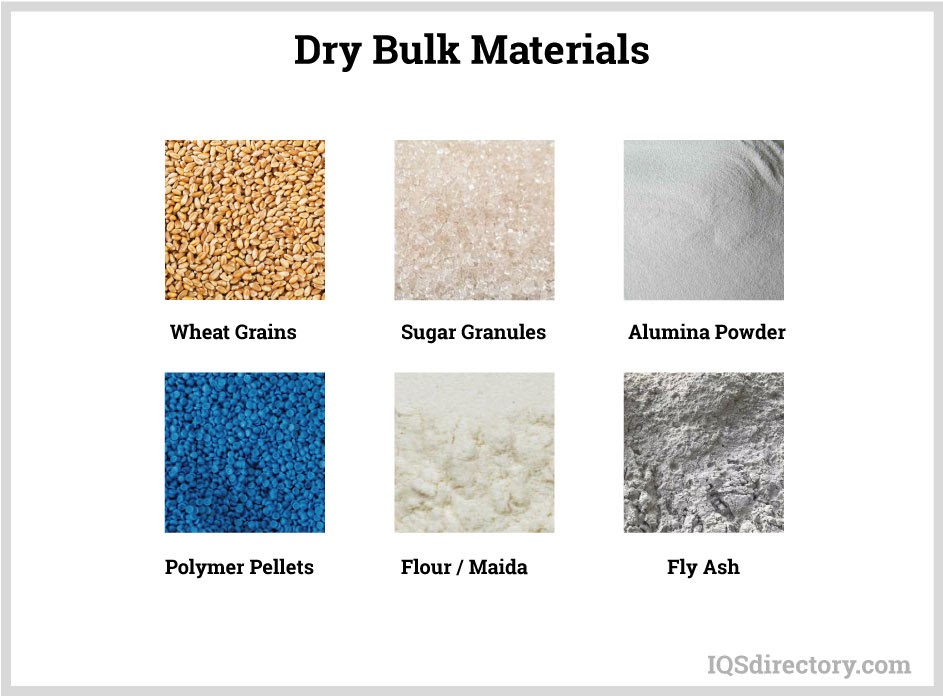
Examples of different materials that uses pneumatic conveying.
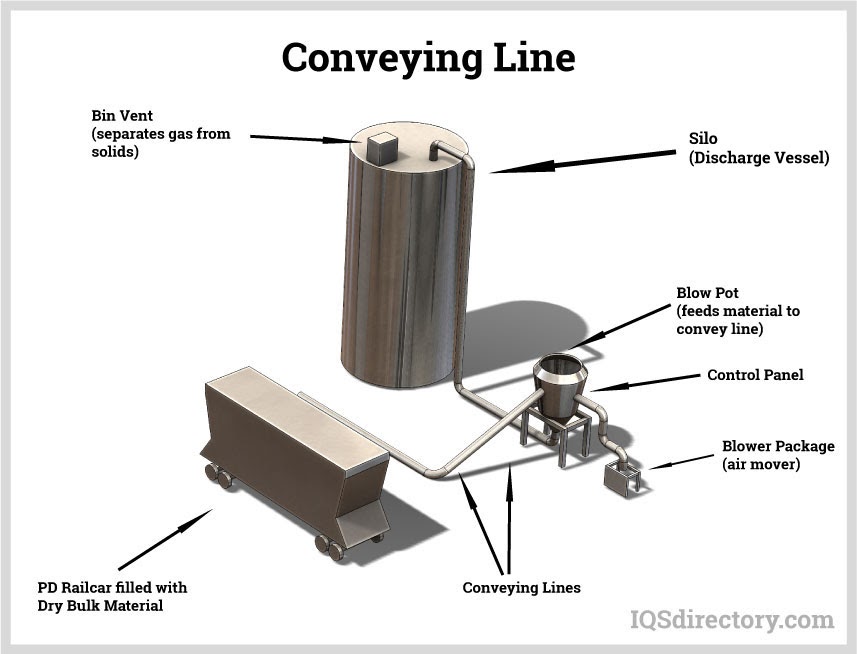
A Conveying lines is the method of transport.
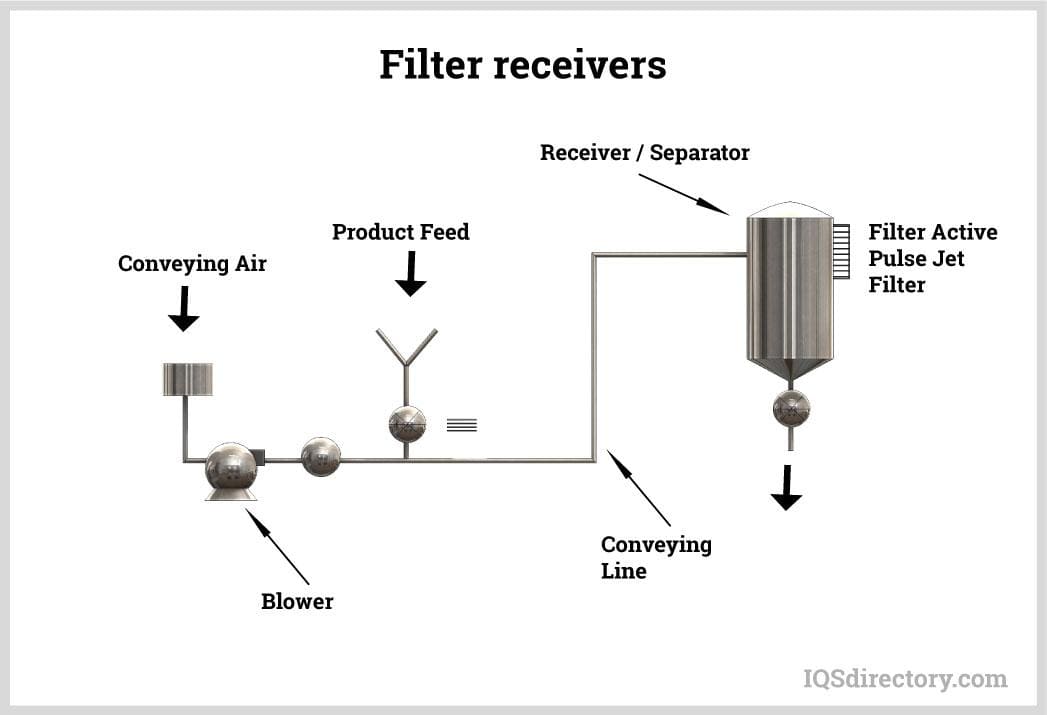
The Filter receivers separates airborne material from the material in the pneumatic conveying system.
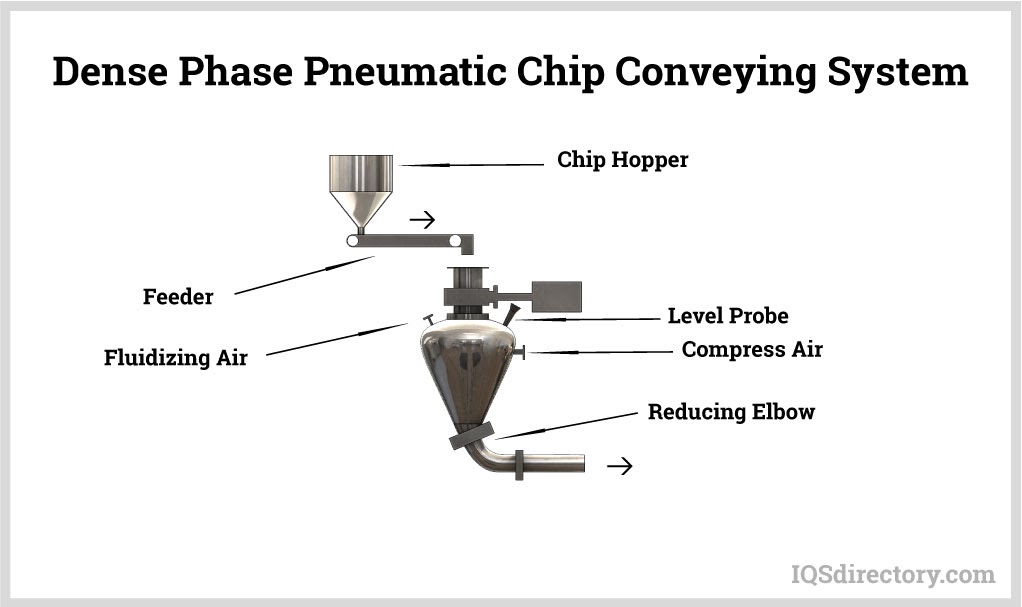
The Dense phase is the transfering of the material at a low velocity to prevent less damage to the machine parts.
Pneumatic Conveyors Types
Abrasive Materials Conveyors
These conveyors are designed to transport coarse, rough materials at a slower pace. Typically, they utilize compressed air to efficiently move the material through the system.
Air Conveyors
Air conveyors rely on pneumatic power to move materials from one point to another.
Bulk Bag Unloaders
These devices allow for the efficient discharge of powders or other dry bulk materials from bags, which are typically used for storage or transport of materials that are otherwise difficult to handle.
Bulk Conveyors
Used to handle a wide range of materials across various industries, bulk conveyors transport materials and often fill bags with bulk items for transport.
Dense Phase Conveying
This method is employed for transporting abrasive, friable, or heavy materials such as sands, soils, minerals, and rocks. Dense phase conveyors use air compressors to create high pressure, enabling materials to be moved slowly through the system.
Dilute Phase Conveying
A method for moving non-abrasive, lightweight materials like powders and grains. Dilute phase conveyors operate at lower pressure, facilitating quick transportation of materials through the system.
Enclosed Conveyors
These fully covered conveyor systems are used to prevent product contamination. They are essential in industries where the products being conveyed must be protected from exposure, such as pharmaceuticals, chemicals, and medical products.
Food Handling Conveyors
Used in the food processing industry, these conveyors handle a variety of food products, including beans, nuts, powders, and formulas. Given that these conveyors deal with materials that will be consumed, cleanliness and sanitation are crucial to avoid contamination.
Mobile Conveyors
These conveyors can be moved and positioned at various discharge points. They can draw material from a container, feedbin, or a pickup adapter under a bin or process vessel.
Pneumatic Conveying
A process that uses forced gas to transport solid goods through a system.
Pneumatic Conveying Systems
This term refers to all components of a system that use air-powered conveyors to move materials.
Powder Conveyors
These conveyors are used to carefully and efficiently transport powders, including potentially hazardous materials like sodium sulfate.
Powder Bulk Handling
The process involves the industrial mixing, conveying, measuring, or packaging of delicate, friable, sticky, or free-flowing powdered solids.
Railcar Unloading
This method transfers materials or products from railcars to storage systems such as silos or bins.
Vacuum Conveyors
These systems use compressed air-driven vacuum pumps, which are controlled automatically. When the material container is full, the vacuum pump is stopped, and the bottom valve opens, allowing the material to be discharged.
Pneumatic Conveyors Terms
Air Compressor
The equipment responsible for generating pressurized air above atmospheric levels within a dense-phase pneumatic conveyor system.
Air Receiver
A tank used to store compressed air generated by the system's air compressor in a dense-phase pneumatic conveyor system.
Arching
A no-flow condition where material forms a stable arch (bridge) across the bin, blocking the flow of materials.
Atmospheric Pressure
The force exerted by the atmosphere on the Earth's surface. Air in a pneumatic conveyor system that is pressurized above 14.7 psi is considered compressed, while air under 14.7 psi is a vacuum.
Attrition
The generation of fines or dust when handling solids, often caused by the friction or impact of materials against one another during transport. Materials like granules, food products, and plastic pellets are particularly prone to attrition.
Bin
A container designed to store bulk solids, equipped with one or more outlets for material withdrawal, which can be done by gravity or flow-promoting devices.
Bin Vent Filter
A component in pneumatic conveying systems used to remove or filter dust from the system, particularly from silos or storage bins.
Bridging
A no-flow condition similar to arching, where material becomes blocked in the bin and prevents further flow.
Bulk Bag Equipment
Process equipment designed for the handling, storage, and transport of bulk bags, which are large fabric containers for dry, flowable materials.
Bunker
A type of bin, often used for storing materials like coal, particularly in bulk handling applications.
Casters
Wheels attached to pneumatic conveyors that allow them to be easily moved to different locations.
Chute
A device for collecting and directing a material stream. Unlike a hopper, it does not operate full at all times.
Cylinder
The vertical section of a bin with a constant cross-section; its shape can vary but generally refers to a cylindrical container.
Dense Phase Conveying
A conveying method in which materials are transported at low velocities with high-pressure differentials. The material flows slowly through the system, often used for heavy or abrasive materials like sands and minerals.
Dilute Phase Conveying
A method where materials are transported at higher velocities using lower air pressures. This phase is commonly used for lighter, non-abrasive materials such as powders.
Discharger
A device that aids in material flow from a bin but does not control the rate of material withdrawal.
Diverter Valve
A component used to redirect material flow within a pneumatic conveying system, changing the direction of transport.
Effective Head
A term used to describe consolidating pressure in relation to bulk density, often used in calculating system performance.
Elevator
Similar to a bin, often used in the context of grain storage or transportation.
End Receiver
The mechanism at the end of a pneumatic system that receives and transfers the conveyed material into the designated receiving container.
Expanded Flow
A flow pattern combining mass flow and funnel flow, resulting in material movement that differs from typical flow models.
Feeder
A device used to control the rate at which bulk solids are withdrawn from a bin, regulating the flow into the pneumatic conveyor system.
Flooding, Flushing
A condition in which an aerated bulk solid behaves like a liquid, flowing uncontrollably through an outlet or feeder.
Flow Channel
The designated space within a bin where material actually flows during the withdrawal process.
Flow Properties Test Report (FPTR)
A report that includes results on a material’s characteristics like cohesive strength, bulk density, friction, moisture content, particle size, and permeability, crucial for designing mass flow bins and feeders.
Fluidization
The process of aerating a fine bulk solid using air or gas to make it behave like a fluid.
Footprint
The amount of space a pneumatic conveying system occupies on the production floor.
Funnel Flow
A flow pattern in which material moves in a channel surrounded by stagnant material, often leading to inefficient transport.
Hopper
The tapered or converging section of a bin, where bulk material is funneled into the pneumatic conveyor system.
Horsepower (HP)
A unit used to measure the rate at which work is done, often applied to the energy requirements of pneumatic conveyors.
Mass Flow
A flow pattern in which all the material in the bin is in motion at the same time whenever any material is withdrawn.
P-Factor
The ratio of applied solids compaction pressure to the pressure of the material during steady gravity flow.
Pickup Velocity
The gas velocity at the point where material is introduced into the gas stream of the pneumatic conveyor system.
Piping
The network of tubes through which conveyed materials travel in a pneumatic system, often designed to navigate obstacles within the facility.
Pneumatic Piping System
The complete system of pneumatic conduits used to transport air or other gases between different components of the pneumatic conveyor system, including pumps, valves, and actuators.
Pressure
The force exerted per unit area within the pneumatic system, typically measured in psi.
Psi (Pounds per Square Inch)
A unit of pressure used to quantify the amount of pressure applied within pneumatic systems.
Powder Handling
The process of managing, mixing, conveying, measuring, or packaging delicate and free-flowing powdered solids in industrial applications.
Ratholing
A no-flow condition in which material forms a stable, vertical hole in a bin, preventing the material from flowing properly.
Receiving Bin
The container that receives conveyed material at the end of a pneumatic conveyor system.
Relief Valve
A safety device attached to pneumatic components to relieve excess pressure buildup.
Rotary Valve
A mechanism that releases material from a pneumatic conveyor under gravitational pressure, often used in the discharge process.
Saltation Velocity
The velocity at which particles begin to settle out of suspension in a conveying line, resulting in decreased flow efficiency.
Sifting Segregation
The separation of bulk solids based on differences in particle size, shape, or density.
Silo
A large storage container used to hold bulk material before it is conveyed to its next location.
State Diagram
A graphical representation of pressure drop as a function of gas velocity, which defines the conveying modes of dilute and dense phase transport.
Tubing Bend
Curved sections of tubing used to navigate obstacles and direct the flow of materials in a pneumatic system.
Transporter
A container in a pneumatic conveyor system that holds materials to be conveyed at a specific rate. Dense phase transporters often use compressed air to move the material under pressure.
More Pneumatic Conveyor Information