Mass Flow Meters
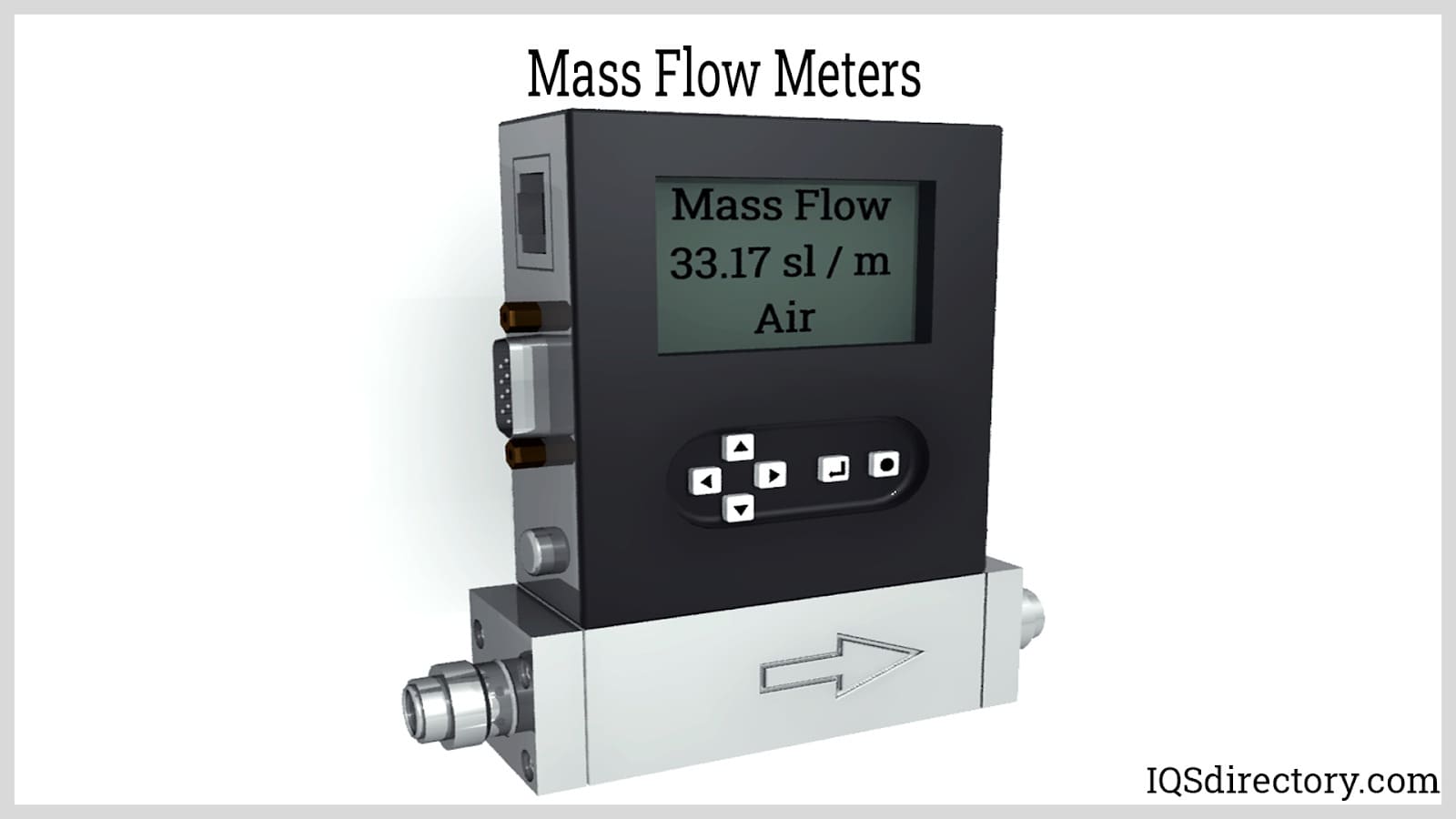
The measuring and controlling of pressure are an essential part of industrial operations. Getting accurate and meaningful data assists in determining the quality and stability of a final product. Pressure measuring devices supply a wide array of data such as levels, volume, flow, and density.
Though we may use pressure as a general term, there are various types of pressure. The meaning of pressure is force being applied to a unit of area. When pressure is applied to a surface, it spreads equally over the entire surface. Fluid pressure can be a liquid or gas with absolute pressure being the force applied by a fluid on a surface. When pressure is applied by air, it is referred to as atmospheric pressure.
Since pressure is such an important aspect of manufacturing processes, there are several devices used to measure and monitor it. Included in the group of tools are flow meters, leak detectors, pressure gauges, pressure switches, level switches, and pressure transducers. Each of these technical instruments offers data and information to assist producers in the manufacture of their products.
The term flow meter is a generic term that describes a variety of instruments used to measure the flow and movement of fluids and gases. After being fitted into a pipe, a flow meter provides data on the movement of a gas or liquid. The types of things that flow meters measure can include the pressure, rate, volume, and mass of the material. This information is used to control the various factors of an application.
A very critical and necessary instrument, especially where gas is present, is a leak detector, which is designed to identify any leaks in a system, provide data regarding the amount, and composition. Leak detection is used for determining gas and water leaks as well as other liquids. There are a variety of methods used to detect leaks, which include visible indicators, flame ionization, ultrasound, and sound. The purpose of a leak detector is to identify changes in pressure and flow rate.
Level switches are used in storage tanks to monitor the level of the material in the tank. They can be used for the measurement of levels as well as being able to control levels. To determine the level of a substance, a level switch has an electrical switch that activates when the level in the container reaches a critical point.
Pressure gauges are sometimes confused with flow meters since they are used to monitor liquids and gases in a pipeline. The use of pressure gauges goes beyond measuring the pressure in a pipe and includes measuring and displaying the pressure in an enclosed space or container. Pressure gauges are designed and manufactured to monitor specific substances or a general range of substances depending on the application.
A less complex form of pressure measuring device is a pressure switch that is designed to activate when the pressure in a material reaches a critical level. At that moment, the switch is programmed to trigger an alarm, emergency signal, or light to advise controllers of the danger. When a pressure switch is placed in the substance to be monitored, it is supplied with the pressure level that indicates unsafe or critical conditions.
An essential part of any form of pressure sensor is a pressure transducer, which converts physical force into electrical energy. Pressure transducers are a critical part in the manufacture of pressure sensors since they activate the sensor to supply data. The energy from the transducer produces an analog electrical signal.
The measure and monitoring of pressure is important for the protection of industrial operations and workers. By being able to observe flow rates, volume, pressure, and other factors, industrial managers are better able to control production processes and operations.
Flow meters are instruments used to measure and monitor the flow rate of liquids, gases, and vapors in a system. They are widely used in various industries, including oil and gas, chemical processing, water treatment, and manufacturing, to control and regulate the flow rate in a system.
There are different types of flow meters, including differential pressure flow meters, positive displacement flow meters, electromagnetic flow meters, ultrasonic flow meters, and turbine flow meters. Differential pressure flow meters use the pressure drop across an orifice plate to measure flow rate, while positive displacement flow meters use the movement of fluid through a chamber to measure flow rate. Electromagnetic flow meters use Faraday's Law of electromagnetic induction to measure the flow rate of conductive fluids, and ultrasonic flow meters use sound waves to measure the flow rate of fluids. Turbine flow meters use the rotation of a turbine in the fluid stream to measure flow rate.
Flow meters are used in many applications, including monitoring the flow rate of liquids in pipelines, measuring the flow rate of gases in combustion engines, and monitoring the flow rate of water in irrigation systems. Flow meters are also used in manufacturing processes to measure the flow rate of raw materials and finished products.
Learn more about flow meters.
Leak detectors are devices used to identify and locate leaks in various systems. They play a crucial role in ensuring the safety and efficiency of many industries, including oil and gas, chemical processing, and water management. These detectors work by sensing changes in pressure, temperature, or gas concentration in the surrounding environment, allowing users to pinpoint the source of the leak and take appropriate action.
In the oil and gas industry, leak detectors are used to detect leaks in pipelines, tanks, and valves, preventing oil spills and gas explosions. These detectors can also identify leaks in underground storage tanks, which can lead to groundwater contamination. Leak detectors are used in chemical processing plants to identify leaks in tanks and pipes, preventing hazardous chemicals from leaking into the environment and posing a risk to human health.
Leak detectors are also used in homes and commercial buildings to detect leaks in plumbing systems or gas lines. In the event of a gas leak, detectors can quickly alert occupants and emergency responders, minimizing the risk of injury or property damage. In addition, leak detectors can identify leaks in water supply systems, preventing water waste and damage to building structures.
Leak detectors come in various types, including electronic sensors, ultrasonic detectors, and infrared cameras. Electronic sensors are commonly used to detect leaks in pipelines and tanks, while ultrasonic detectors are effective for detecting leaks in pressurized systems. Infrared cameras are used to identify leaks in electrical systems and building structures.
Learn more about leak detectors.
Level switches are devices that are used to detect the level of liquid or bulk solids in tanks, containers, and pipelines. They work by sensing the changes in the level of the liquid or bulk solid and then activating a switch that sends a signal to the control system. The control system then takes appropriate action, such as turning on or off a pump, or activating an alarm.
Level switches are used in many industries, including chemical processing, oil and gas, food and beverage, and wastewater management. They play a critical role in controlling the level of liquids and solids in tanks, preventing overfilling and spillage, which can lead to environmental damage, equipment failure, and loss of valuable resources.
There are several types of level switches, including float switches, capacitance switches, ultrasonic switches, and optical switches. Float switches are the most commonly used type of level switch, and they work by using a buoyant float to detect the level of liquid in the tank. Capacitance switches use electrical capacitance to measure the level of liquid, while ultrasonic switches use sound waves to detect the level of liquid. Optical switches use light to detect the level of liquid or bulk solids.
Learn more about level switches.
Pressure gauges are instruments used to measure and display the pressure of liquids, gases, and vapors in a system. They are widely used in various industries, including oil and gas, chemical processing, water treatment, and manufacturing, to monitor and control pressure levels. Pressure gauges are critical tools for ensuring the safety and efficiency of many industrial processes.
There are different types of pressure gauges, including mechanical gauges, digital gauges, and differential pressure gauges. Mechanical gauges use a Bourdon tube or diaphragm to measure the pressure of a fluid, while digital gauges use electronic sensors to measure pressure. Differential pressure gauges measure the difference in pressure between two points in a system.
Pressure gauges are used in many applications, including monitoring the pressure in pipelines, tanks, and vessels. They can also be used to monitor the pressure of gases in combustion engines, compressors, and turbines. Pressure gauges are also commonly used in hydraulic and pneumatic systems to monitor the pressure of the fluid or gas.
In addition to measuring pressure levels, pressure gauges can also be used to diagnose problems in a system. For example, a sudden drop in pressure can indicate a leak or a malfunctioning valve.
To accommodate their many different applications, manufacturers make many different types of pressure gauges. Some are designed to measure specific substances or conditions. Examples of these include: water pressure gauges, air pressure gauges, oil pressure gauges, temperature gauges, gas pressure gauges, fuel pressure gauges, differential pressure gauges, and vacuum pressure gauges. Some of the uses of these gauges are more obvious than others. Water pressure gauges, of course, monitor the pressure of any water-based system. Learn more about pressure gauges.
Pressure switches are instruments used to monitor the pressure of liquids, gases, and vapors in a system and to activate or deactivate electrical or mechanical devices when a certain pressure threshold is reached. They are widely used in various industries, including oil and gas, chemical processing, water treatment, and manufacturing, to control and regulate the pressure levels in a system.
There are different types of pressure switches, including electromechanical switches, solid-state switches, and smart switches. Electromechanical switches use a mechanical contact to complete or break a circuit when a specific pressure is reached, while solid-state switches use a semiconductor to detect and signal pressure changes. Smart switches use microprocessors and sensors to provide more advanced control and monitoring capabilities.
Pressure switches are used in many applications, including monitoring the pressure in pipelines, tanks, and vessels. They can also be used to control the operation of pumps, compressors, and motors by activating or deactivating them when a certain pressure level is reached. In addition, pressure switches are used in safety systems to activate alarms or shut down equipment when the pressure exceeds a safe level.
Learn more about pressure switches.
Pressure transducers are devices used to measure and convert pressure into an electrical signal. They are commonly used in industrial applications to monitor and control the pressure of gases and liquids in a system. Pressure transducers play a critical role in ensuring the safety and efficiency of many industrial processes.
There are different types of pressure transducers, including piezoelectric, strain gauge, and capacitive transducers. Piezoelectric transducers use the piezoelectric effect to generate an electrical signal when pressure is applied to a crystal or ceramic element. Strain gauge transducers use a thin metal foil that is bonded to a diaphragm to detect changes in pressure. Capacitive transducers use changes in capacitance to detect changes in pressure.
Pressure transducers are used in many applications, including monitoring the pressure in pipelines, tanks, and vessels. They can also be used to monitor the pressure of gases in combustion engines, compressors, and turbines. Pressure transducers are also commonly used in hydraulic and pneumatic systems to monitor the pressure of the fluid or gas.
In addition to measuring pressure levels, pressure transducers can also be used to diagnose problems in a system. For example, a sudden drop in pressure can indicate a leak or a malfunctioning valve.
Learn more about pressure transducers.