Pressure Vessels
Pressure vessels, commonly known as air pressure tanks, are engineered to store and contain fluids, vapors, or gases at pressures exceeding atmospheric levels. Designed to operate above 15 psi, these vessels are constructed from a range of materials, including high-strength metals, plastic, and fiberglass. Typically cylindrical in shape, they can be oriented horizontally or vertically, depending on the application.
The History of Pressure Vessels
The concept of pressure vessels dates back to the 15th century when Leonardo da Vinci first documented the idea of pressurized containers in Codex Madrid I, envisioning their use for lifting weights underwater. However, it wasn’t until the 1800s that pressure vessels saw widespread use in steam generation. Early models, made from inferior materials and lacking safety regulations, were prone to catastrophic failures. Explosions of boilers and pressure vessels were alarmingly common, prompting local governments to draft construction laws.
By 1914, the American Society of Mechanical Engineers (ASME) introduced the first Boiler and Pressure Vessel Code, laying the foundation for safer designs. Engineers quickly adopted new technologies, reinforcing vessels with steel wire and improving structural integrity through longitudinal reinforcements. By the 1920s and 1930s, welding replaced riveted construction, establishing a stronger, more durable industry standard that remains in place today.
Modern advancements, including non-destructive examination techniques, radiography, phased ultrasonic testing, and explosion welding, have significantly enhanced the reliability and safety of pressure vessels. New material grades and innovative joining methods continue to push the limits of performance, ensuring these critical components operate safely under extreme conditions.
Pressure Vessels Benefits
Designed to contain gases and liquids at pressures far beyond atmospheric levels, pressure vessels are indispensable across various industries. While standard models endure pressures above 15 psi, specialized vessels can be built to withstand up to 10,000 psi, ensuring safe and efficient operation in high-pressure environments.
How Pressure Vessels Work
Pressure vessels maintain controlled internal pressure either through a direct source or indirectly via heat transfer. Typically, this process is managed using a network of valves and release gauges, allowing operators to regulate pressure levels according to specific application needs. Whether it's supplying water to a building or ensuring breathable air in diving cylinders, these components enable precise pressurization to support various critical functions.
Pressure Vessels Images, Diagrams and Visual Concepts
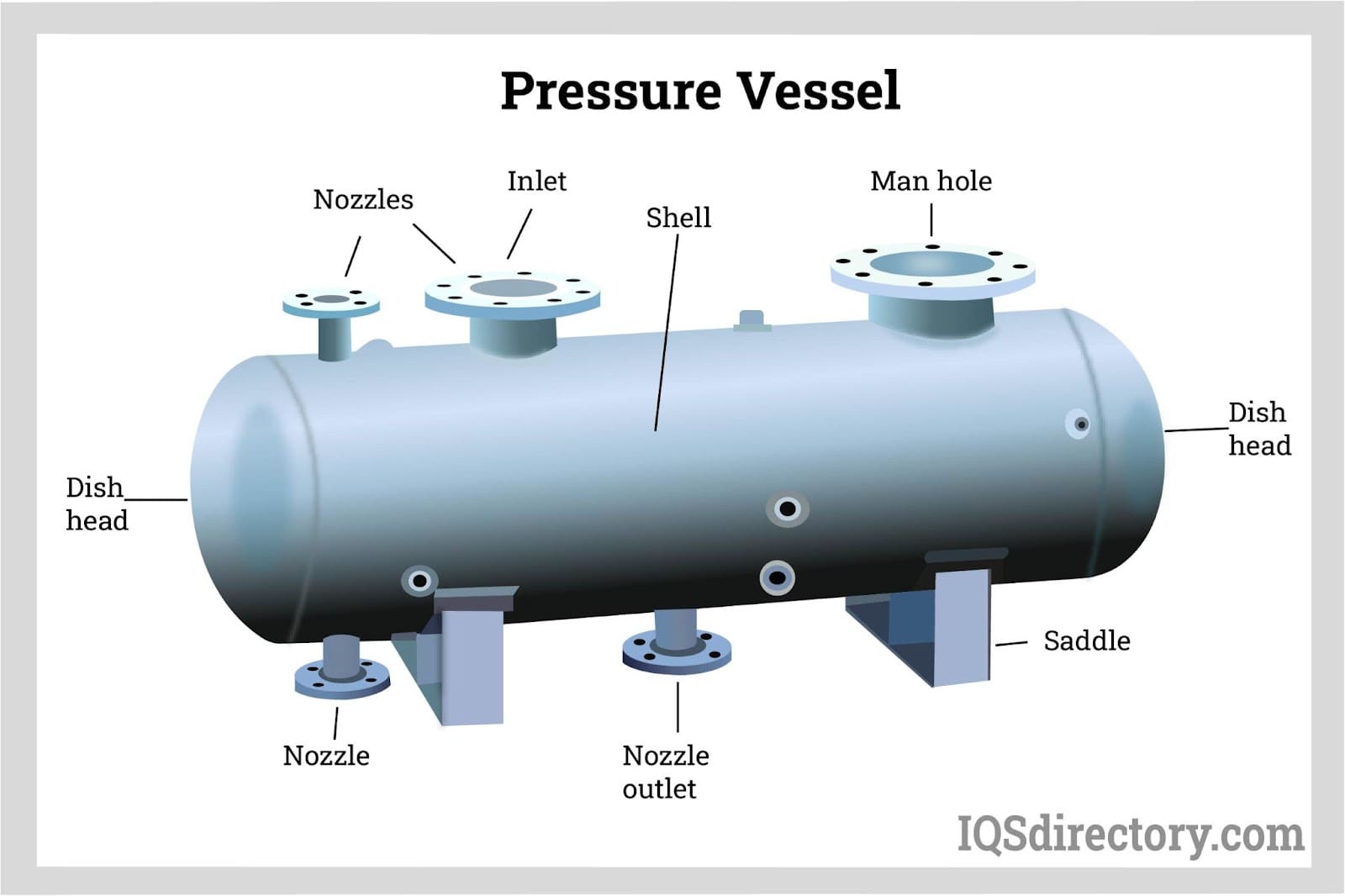
Pressure vessels are sealed containers used to store liquids, vapors, or gasses at greater pressure or less pressure than the surrounding atmosphere.
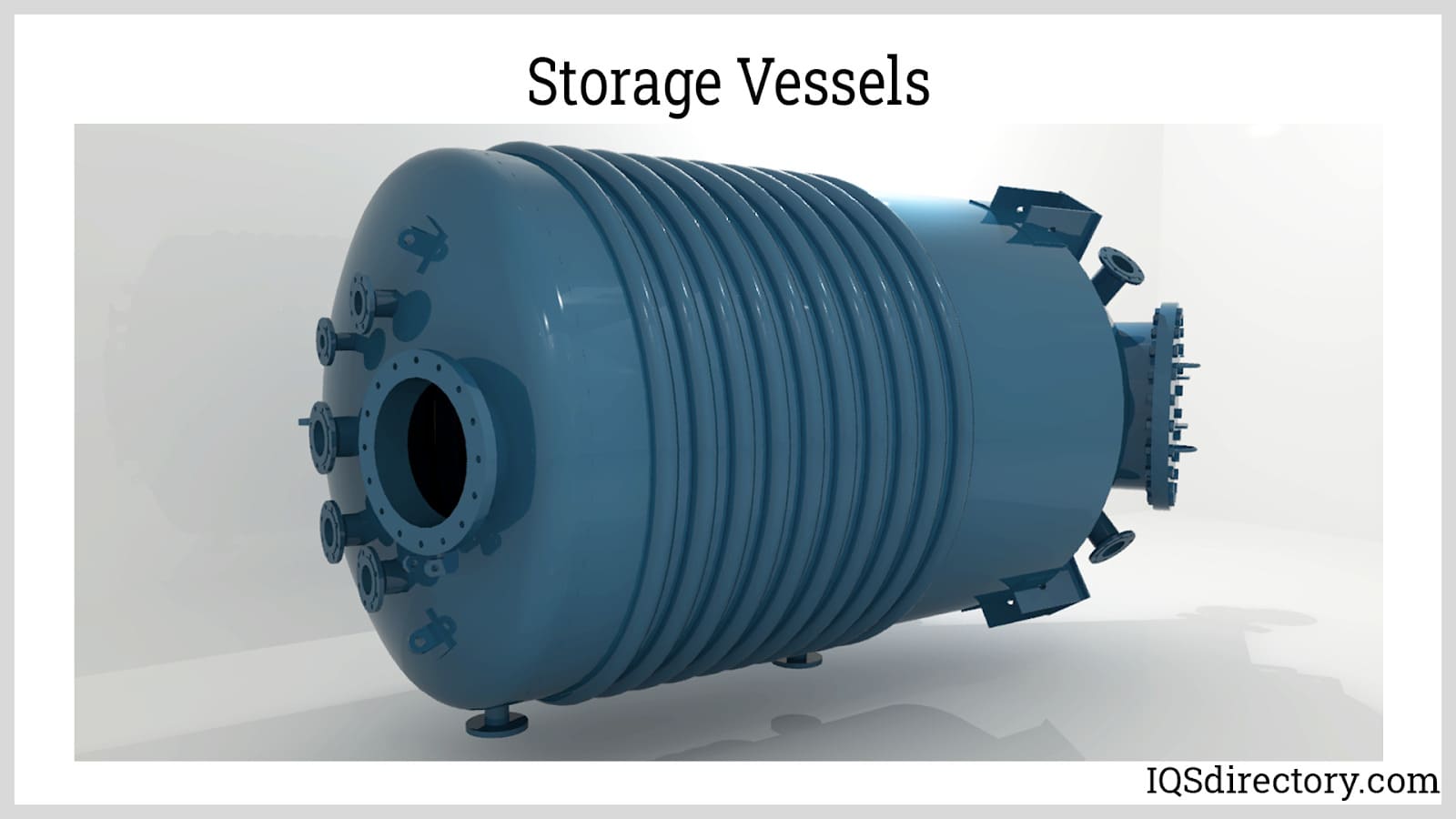
An example of pressure vessels are storage vessels which holds liquids, vapors, or gases as either a finsihed product or for later processing.
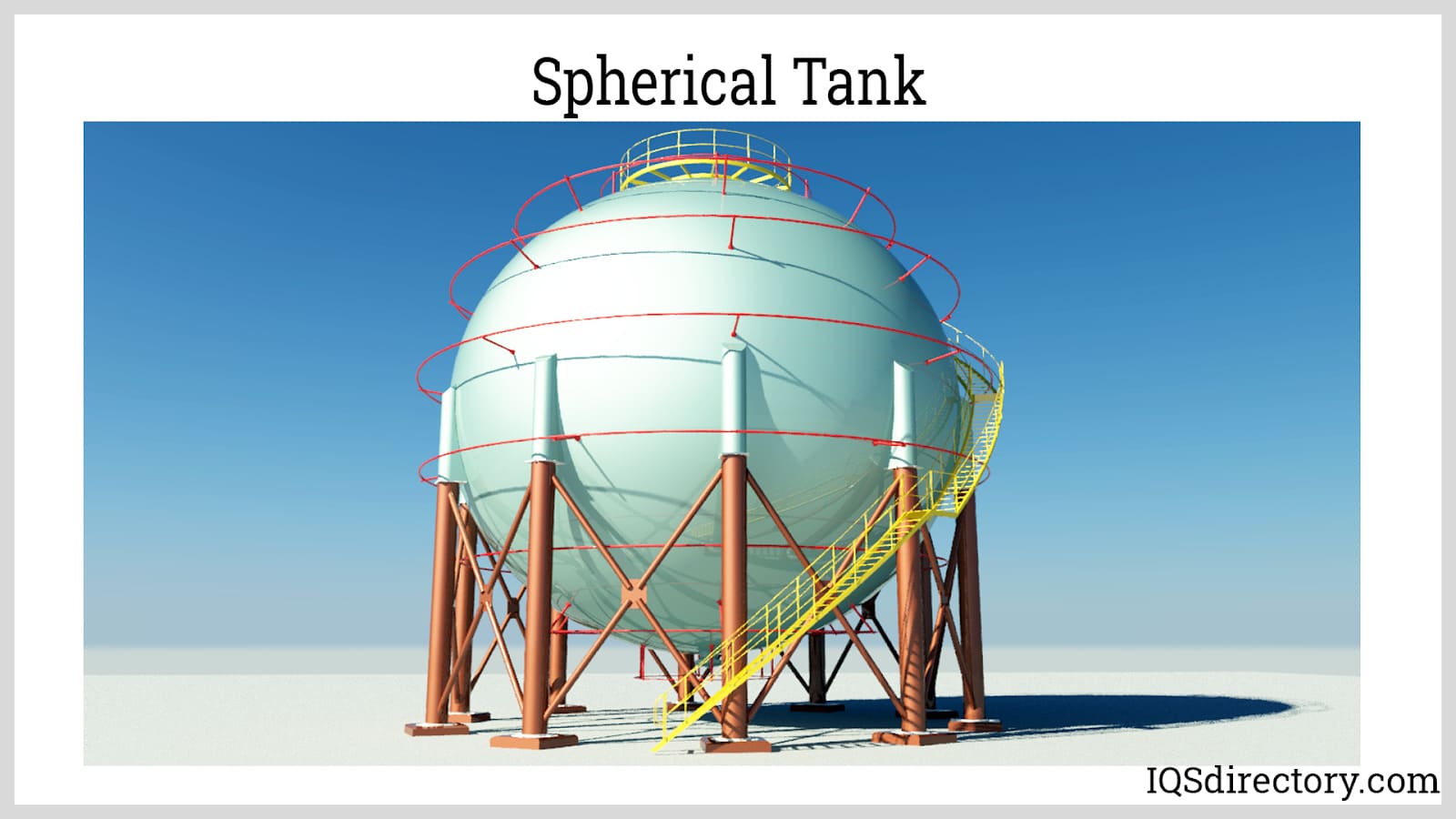
Spherical pressure vessels evenly distributes pressure both internally and externally in the sphere.
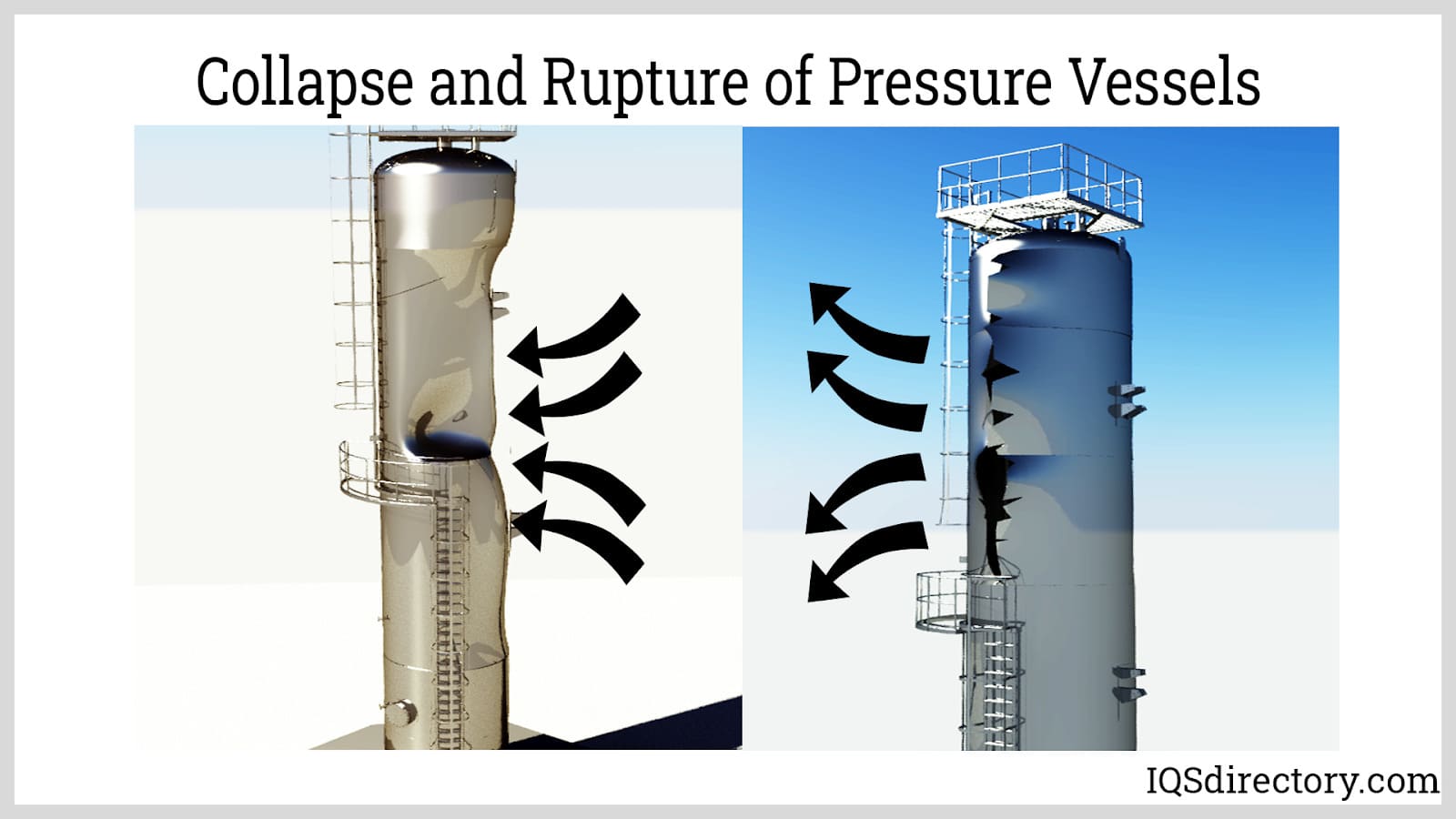
When the pressure exceeds the maximum tolerance safety concerns and damage to the vessels are more likely to occur.
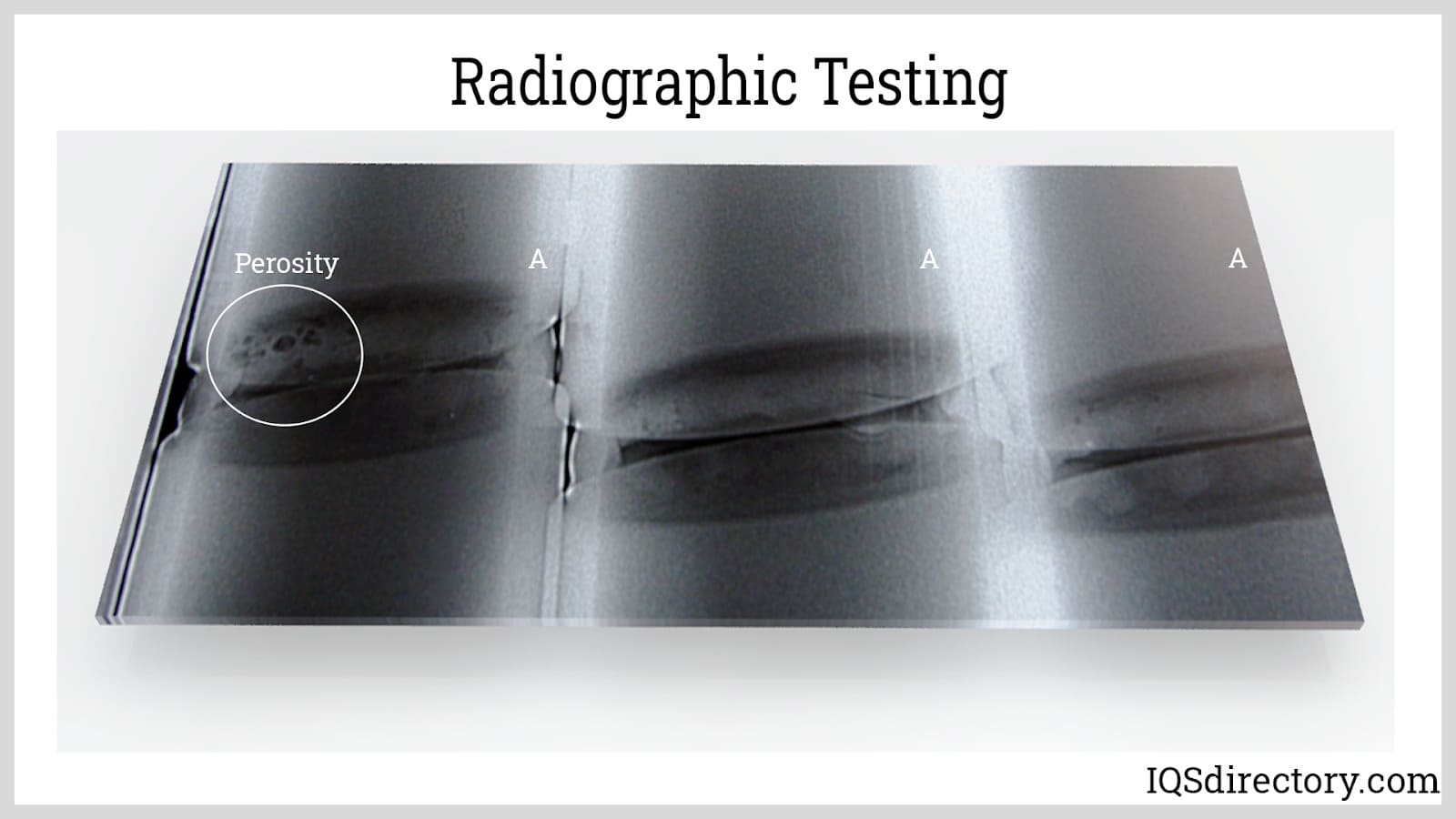
Utilizes x-rays to produce an image of a pressure vessel‘s surface and subsurface, which can detect discontinuities, holes, and difference in density of the vessel.
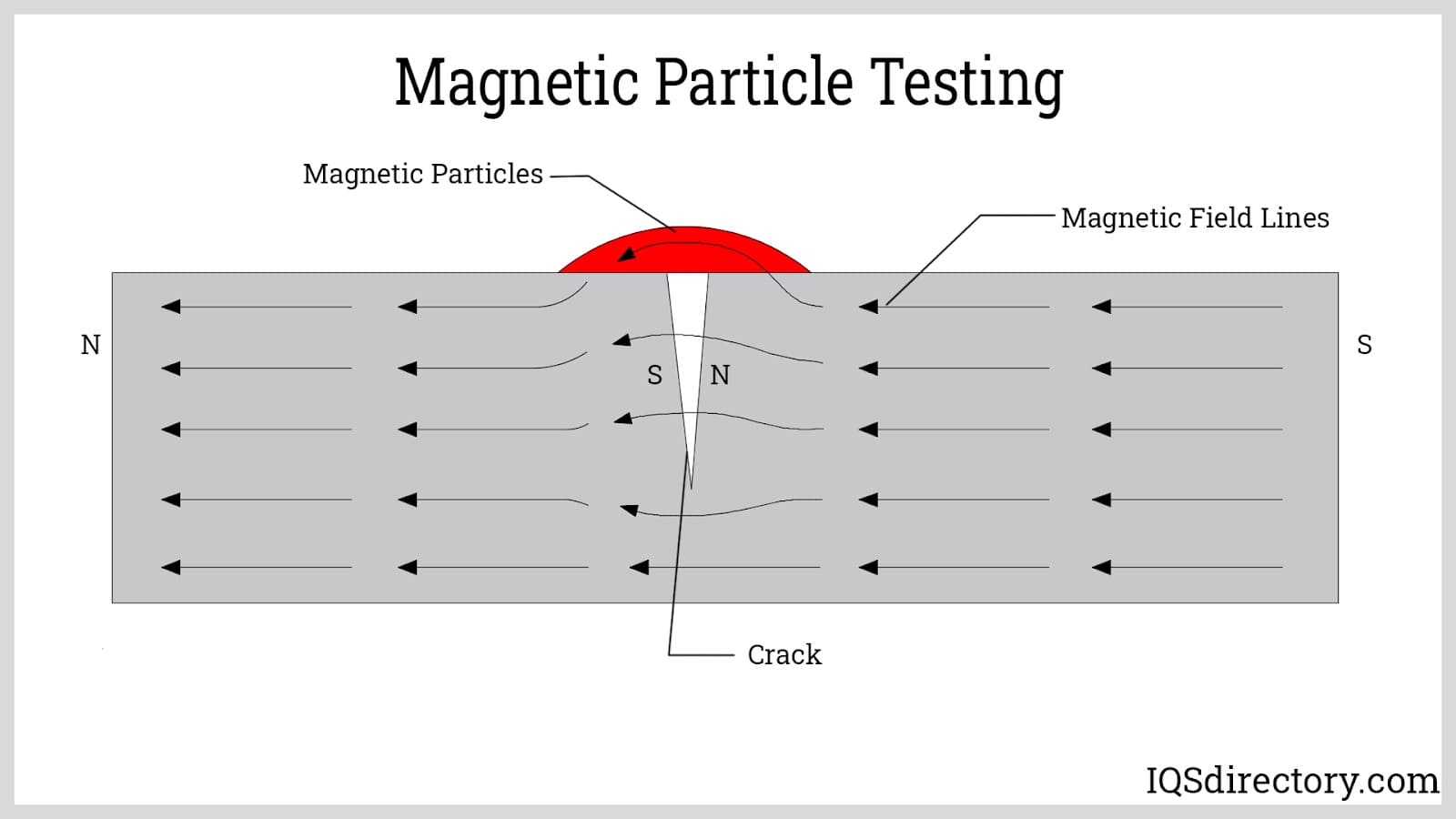
A magnetic current detect any discontinuities on the surface if any imperfections are present, the magnetic instability leaks out of the material.
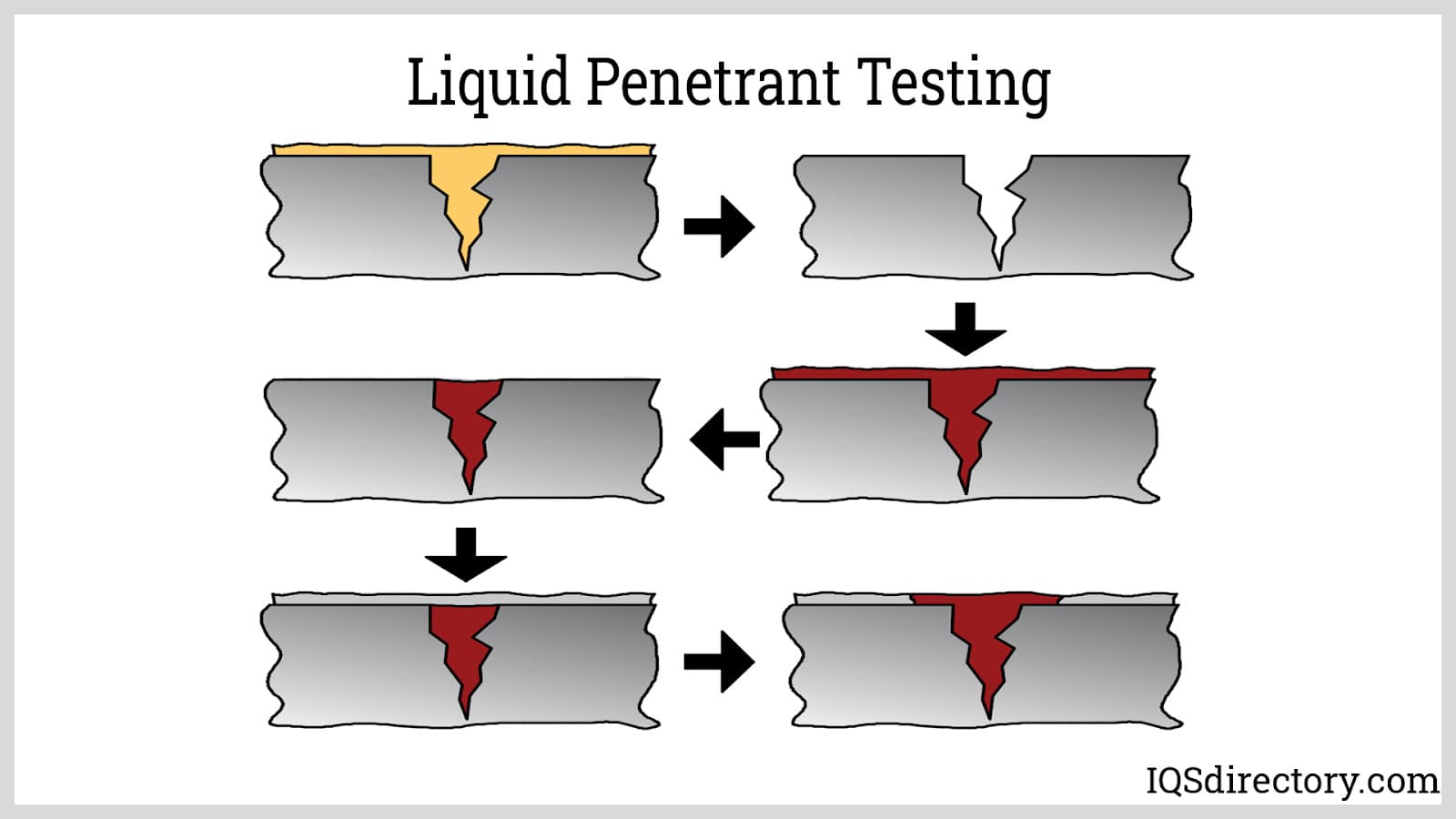
A small amount of liquid, called the penetrant, to an area with a possible flaw, then allowed to settle after spraying and then wiped to clean on the surface, if the penetrant has seeped into the cracks, which revels the imperfection.
Types of Pressure Vessels
Autoclave
Similar to grease kettles, autoclaves utilize steam and pressure to drive chemical reactions, producing a variety of substances, including food, lubricants, and chemicals. Process tanks, designed for holding and storing liquids, often function alongside autoclaves in industrial settings.
High Pressure Vessel
Built to withstand extreme psi levels, these vessels offer the highest strength among pressure tanks. Typically constructed from stainless steel, they provide superior resistance to pressure, temperature fluctuations, and corrosion, making them essential in high-stress applications.
Many pressure vessels play a vital role in manufacturing, facilitating chemical and material processing. Others serve diverse applications, such as expansion tanks and heat exchangers in residential water heating systems, water pressure tanks in wells, and vacuum tanks in sewage systems. These vessels are primarily used for short-term storage.
Spherical Pressure Vessel
Designed for maximum strength, spherical vessels can endure nearly twice the pressure of cylindrical alternatives. However, their intricate construction limits their production, as manufacturing costs are significantly higher than other vessel types.
Thin-Walled Pressure Vessel
A pressure vessel falls into this category when its wall thickness is 10% or less of its diameter. This design is common in applications where high internal pressure must be contained without excessive material usage.
Unfired Pressure Vessel
Instead, they transfer heat through electric heating elements, steam, or internal chemical reactions. Examples include air tanks, digesters, steam-jacketed kettles, and vulcanizers.
ASME Boiler/ASME Pressure Vessel
Vessels meeting the rigorous standards of the American Society of Mechanical Engineers (ASME) bear an official ASME stamp. This marking not only verifies compliance with industry regulations but also provides traceability to the manufacturer.
Cookers
These vessels facilitate physical transformations in their contents through controlled pressure and heat. Common examples include digesters, vulcanizers, and rendering tanks.
Fired Pressure Vessels
Powered by fuel combustion, fired pressure vessels generate heat for various industrial and residential applications. Boilers, furnaces, gas water heaters, and autoclaves fall under this category.
Heat Exchangers
These vessels enable efficient thermal energy transfer, either heating or cooling substances as they move through separate chambers. Heat exchangers are integral to industrial processes, power plants, and HVAC systems.
Kettles
Steam-powered vessels that heat fluids, kettles are widely used in food production, chemical processing, and pharmaceutical applications.
Pressure Tanks
Designed to maintain internal pressure above atmospheric levels, pressure tanks serve critical functions in water supply systems, compressed air storage, and industrial processing.
Rotating Pressure Vessels
These vessels, often containing steam, facilitate drying processes for materials such as paper, textiles, and plastics. Rollers pass materials over the rotating vessel, ensuring direct exposure to the emitted steam.
Steam Jacketed Vessels
By distributing steam between an inner and outer shell, these vessels provide moderate and uniform heating. They are commonly used in commercial food production, including candy-making and sauce preparation.
Storage Vessels
Designed to hold pressurized substances, storage vessels include air tanks, hot water tanks, and propane or gas tanks, ensuring reliable containment until contents are needed.
Thick Walled Pressure
Less common than their thin-walled counterparts, thick-walled pressure vessels have a wall thickness exceeding 10% of their internal diameter, allowing them to withstand extreme internal pressures.
Thin Walled Pressure Vessels
Are one of the most common of the vessels. They are any cylinder [shell] ratio which is 10% or less of the ratio of the thickness to the diameter, or a pressure vessel is thin walled if the diameter is 10-times or more of the thickness.
Transportable Vessels
Unlike stationary vessels, transportable vessels are designed for mobility, often used in road and rail tankers. Propane and gas tanks fall into this category, ensuring safe transport of pressurized substances.
Equipment Components
Pressure vessels incorporate various components to enhance functionality, accessibility, and operational efficiency. Ladders, stairs, and removable or detachable lids provide access, while sight glasses allow for internal observation. Heating and cooling systems regulate temperature conditions, and agitation mechanisms, such as propellers, facilitate mixing applications.
In addition to these features, all pressure vessels are equipped with safety valve fittings that prevent pressure from exceeding a designated threshold. Typically utilizing pressure relief valves, these systems activate automatically when limits are surpassed, releasing excess material to maintain safe conditions. This critical safety feature has proven invaluable in protecting both equipment and personnel, enabling pressure vessels to operate safely in roles such as water pressure tanks, mixers, air pressure tanks, vacuum tanks, storage tanks, and heat exchangers.
Applications of Pressure Vessels
Designed to contain a wide range of substances, pressure vessels serve essential functions across multiple industries, including chemical, petrochemical, aerospace, laboratory, pharmaceutical, food and beverage, oil and fuel, and plastics manufacturing. Their applications span compressed gas storage for substances like oxygen and nitrogen, laboratory autoclaves, hydro-pneumatic tanks, and refrigerant vessels.
These vessels are integral to operations in oil refineries, petrochemical plants, mining sites, submarines, and nuclear reactors. A particularly unique application is found in aviation, where an aircraft’s entire structure functions as a pressure vessel, maintaining cabin pressure while withstanding the dynamic forces of flight.
Vessel Materials and Customization
Pressure vessels must be constructed from materials that offer exceptional strength and durability, maintaining their structural integrity under high pressure. Common choices include carbon alloy steel, stainless steel, titanium, zirconium, aluminum, nickel alloys, and niobium. In some cases, composite materials or even concrete are used for specialized applications.
To bring their designs to life before manufacturing, engineers rely on computer-aided design (CAD) programs to meticulously map out every detail. Whether using CAD software or drafting plans by hand, manufacturers take into account key factors such as vessel material, lining material, wall thickness, shape, and manufacturing process—all of which are tailored to the vessel’s intended application and the substances it will contain.
Steel in Vessels
Carbon steel is the go-to material for most pressure vessels due to its strength and reliability. However, demanding applications call for enhanced variations, such as hardened steel or stainless steel. In cold environments, steel with high impact resistance is essential, while corrosive settings require stainless steel to prevent degradation and ensure longevity.
Composite Materials
For applications that do not require extreme pressure resistance, manufacturers turn to composite materials like carbon fiber. These vessels are fabricated using a filament winding process, where filaments are wound around a metal liner, resulting in lightweight yet high-tensile-strength structures. Though this method enhances performance, it is complex and can be costly. Polymers like polyethylene terephthalate (PET) are also used in specific applications, such as carbonated beverage containers.
Concrete in Pressure Vessels
While concrete is inherently weak in tension, it can still be used in pressure vessel construction when reinforced properly. Polished concrete veneers, for instance, gain strength through wound cables integrated within the vessel’s walls, increasing their ability to withstand internal pressure.
Lining Material
The lining of a pressure vessel plays a crucial role in pressure distribution and leak prevention. Depending on the application, manufacturers may use polymers, ceramics, or metals to provide additional protection against corrosion and pressure fluctuations.
Wall Thickness
A pressure vessel’s wall thickness is directly proportional to its radius and operating pressure, ensuring the structure can endure high-stress conditions. Thickness is also inversely proportional to the material’s normal stress capacity, meaning stronger materials require less thickness. These calculations are essential to maintaining tensile strength, as the vessel’s dimensions directly affect gas containment efficiency. Vessel shape also influences these factors, with spherical, cylindrical, and conical designs each requiring specific calculations for mass, density, and shear stress limitations.
Pressure Vessel Shapes
While pressure vessels can be fabricated in various shapes, cylinders, cones, and spheres are the most common due to their superior ability to withstand internal pressure. The most widely used design consists of a cylindrical body with hemispherical end caps. Another popular variation features torispherical head domes.
Cylindrical pressure vessels with end caps are often made from seamless pipes, particularly for large-diameter applications (e.g., 600 mm). Seamless construction enhances strength, reduces inspection frequency, and improves overall safety, though it comes at a higher cost.
Each vessel shape requires specific formulas for calculating mass and structural integrity. Additional considerations include pressure capacity, material density, shear stress limitations, and volume containment.
Manufacturing Processes
Pressure vessels are typically manufactured using one of three primary processes: forging, welding, or brazing.
- Forging involves shaping metal under heat and pressure, producing exceptionally strong components.
- Welding fuses metals by heating their edges to the melting point, creating a seamless bond.
- Brazing joins metals by filling gaps with non-ferrous filler material, ensuring structural cohesion.
Many pressure vessel components are formed from cold-rolled metal, as cold rolling produces a stronger, more resilient structure than hot rolling. To further enhance durability, vessels are often galvanized, quenched, or tempered, improving their resistance to temperature fluctuations and mechanical stress.
Customization of Vessels
Manufacturers tailor pressure vessels to meet specific operational requirements, considering factors such as shape, size, material composition, pressure capacity, temperature tolerance, corrosion resistance, and abrasion potential. Pressure vessels can range from a few hundred psi to extreme ratings of up to 150,000 psi, ensuring reliable performance across diverse industrial applications.
Safety and Compliance Standards for Pressure Vessels
Many tanks must be registered as ASME pressure vessels and comply with the stringent safety and quality standards established by the American Society of Mechanical Engineers (ASME). This includes adherence to ASME Section VIII, commonly known as the Boiler and Pressure Vessel Code (BPVC), which serves as the foundation for pressure vessel design in the United States. Certification under ASME standards is critical, as even the slightest structural weakness or leak in a pressure vessel can lead to catastrophic failure, including explosions and shrapnel damage.
To enhance safety, pressure vessels are engineered according to the “leak before burst” principle. This design philosophy ensures that under excessive stress, a vessel will develop cracks that allow gases or fluids to escape gradually rather than failing violently. This approach has significantly reduced the risk of fatal pressure vessel explosions. Compliance with ASME and other standardizing agency codes ensures that all pressure vessels are built to release pressure in a controlled manner rather than rupture unpredictably.
While ASME codes are the most widely recognized, engineers also adhere to other industry standards, including those set by the American Petroleum Institute (API), the National Board of Boiler and Pressure Vessel Inspectors (NBIC), and the American Institute of Aeronautics and Astronautics (AIAA). In cases where standard design rules do not suffice, engineers rely on advanced mathematical and scientific analyses to ensure that complex pressure vessel designs meet rigorous safety and performance requirements.
Around the world, various regulatory bodies oversee the manufacturing, design, operation, and inspection of pressure vessels. Because different regions have unique legal and safety requirements, it is essential to ensure that any pressure vessel complies with the specific codes and regulations applicable in its intended location.
Testing and certification confirm that a pressure vessel meets initial design and safety standards, but ongoing inspection is equally important. Regular post-purchase evaluations help verify that the vessel continues to operate within industry safety parameters. Manufacturers can conduct a variety of safety inspections, including leak and strength tests such as hydrostatic, pneumatic, vacuum, radiographic, ultrasonic wave, and magnetic particle testing, to ensure structural integrity over time.
Things to Consider When Purchasing Pressure Vessels
Given the high-risk nature of pressure vessels, selecting the right one is crucial for both operational success and personnel safety. Partnering with a reputable manufacturer is key to obtaining a vessel that meets your specific requirements. When evaluating suppliers, consider their technical expertise, willingness to perform necessary inspections, and commitment to customer service. Discuss your specifications, timeline, budget, and compliance needs to ensure they can deliver a solution that aligns with your expectations. By choosing a skilled manufacturer that prioritizes safety and quality, you can confidently invest in a pressure vessel that will perform reliably for years to come.
Pressure Vessel Terms
Agitator
A mechanical device used to stir or mix the contents of a pressure vessel, enhancing uniformity and process efficiency.
Atmospheric Pressure
The natural force exerted by the Earth's atmosphere, measured at 14.7 psi at sea level.
Baffle
An internal component designed to direct fluid flow and increase mixing efficiency, commonly found in vessels equipped with agitators.
Boiler
A specialized pressure vessel that heats water to generate steam or hot water using combustible fuels or electrical energy.
Brittle Fracture
A sudden, catastrophic failure of steel due to exposure to extremely low temperatures, even when stress levels remain below the material’s yield strength.
Corrosion Allowance
Additional material thickness incorporated into a vessel’s design to counteract potential wear from corrosion and abrasion. Protective coatings or linings may also be applied to extend vessel lifespan.
Creep
The slow, permanent deformation of steel caused by prolonged exposure to high temperatures, leading to structural changes over time.
Cryogenic Temperatures
Extremely low temperatures ranging from -250°C to -100°C (-418°F to -148°F), requiring specialized pressure vessels for containment.
Design Pressure
The maximum pressure a vessel is engineered to withstand, typically set at 110% of its normal operating pressure.
Design Temperature
The temperature at which a pressure vessel’s material must maintain structural integrity while operating at its design pressure.
Dewar
A specialized pressure vessel designed to store and maintain cryogenic substances at ultra-low temperatures.
Ferrule
A sanitary, low-pressure nozzle featuring an inset gasket surface, designed for clamp connections rather than bolted fittings.
Fluid
Any substance—liquid, gas, or vapor—that flows freely and adapts to the shape of its container, exhibiting minimal resistance to pressure.
Fusible Plugs
Safety devices that melt at a predetermined temperature, providing emergency pressure relief in the event of a fire.
Heat Transfer Surface (HTS)
A component or system within a pressure vessel designed to regulate temperature, ensuring optimal process conditions.
Hydropneumatic Tanks
Vessels designed to store both liquid and gas, balancing system pressure in applications such as water supply and air compression.
Hydrostatic Test
A critical safety test where a vessel is pressurized to 150% of its design pressure using liquid to detect leaks or structural weaknesses.
ID (Inside Diameter)
The internal measurement of a pressure vessel, excluding material thickness.
Lifting Lugs
Reinforced attachments on a pressure vessel’s exterior, engineered to facilitate safe lifting and transportation.
Manway
An access opening in a pressure vessel, allowing personnel entry for inspection, maintenance, or cleaning.
Megapascal (MPa)
A unit of pressure measurement, equivalent to 1,000,000 pascals, commonly used to express tensile and yield strength.
National Board Inspection Code (NBIC)
An internationally recognized standard governing the inspection, modification, and repair of pressure vessels.
Newton
A unit of force, where one Newton accelerates a one-kilogram mass at a rate of one meter per second squared.
Nozzle
An inlet or outlet port on a pressure vessel, controlling the introduction or release of fluids.
Operating Pressure
The actual pressure at which a vessel functions under normal operating conditions.
Pascal (Pa)
A unit of pressure measurement, where one Pascal equals one Newton per square meter.
Psi (Pounds per Square Inch)
A unit measuring pressure, representing the force applied per square inch of surface area.
Relief Valve
A safety mechanism that automatically releases excess fluid from a vessel when pressure exceeds a preset limit, closing once normal conditions are restored.
Rupture Disks
Single-use pressure relief devices designed to rupture instantly at a predetermined pressure, often used alongside other safety mechanisms.
Safety Relief Valve
A hybrid pressure relief device capable of discharging both liquid and vapor streams when pressure exceeds safe levels.
Safety Valve
A specialized relief mechanism that automatically vents excess gas or vapor to prevent vessel overpressure.
Set Pressure
The specific pressure level at which a relief valve or rupture disk activates to release excess pressure.
Straight Flange
A cylindrical vessel component featuring a bolted rim, designed to secure connections and maintain structural integrity.
Strain
The measurable deformation of a material resulting from applied force.
Stress
The internal force within a material caused by external loads, influencing its shape and structural integrity.
Stress Corrosion Cracking
A failure mode in which metal fractures due to the combined effects of tensile stress and corrosive environments.
Tensile Strength
The maximum stress a material can endure before breaking under tension.
Tensile Stress
The force applied to a material to create elongation or strain.
Vessel Heads
The shaped end sections of a pressure vessel, which may be flanged and dished, ellipsoidal, flat, conical, or hemispherical.
Vessel Shell
The primary body of a pressure vessel, enclosing and containing its contents under pressure.
Yield Strength
The stress level at which a material undergoes permanent deformation, beyond which it will not return to its original shape.
More Pressure Vessels Information