Learn About Pipe Cutting Techniques
Pipe Fabrication, also known as tube fabrication, is a broad category of industrial processes that manufacturers use to cut and shape pipes. Tube Fabrication covers cutting and sawing processes such as circular, band, friction, and more.
Pipe cutting is a large subcategory of pipe fabrication. Manufacturers usually precede it with fabrication processes like Tube Bending. Manufacturers use many techniques and a variety of Tube Forming Machines to create cut pipe products.

Pipe Cutting Techniques
Some of the most common tube cutting techniques include: abrasive cutting, band saw cutting, cold sawing, shearing, laser cutting and lathe cutting. Each operation has its benefits.
To decide which one(s) to use, manufacturers consider application requirements like: pipe thickness, pipe hardness, pipe toughness, pipe texture and requested product quantity.
Abrasive Cutting
Abrasive cutting is a manual cutting technique that works well for small product orders. Manufacturers perform it using an abrasive saw, also known as a chop saw or cut-off saw. Abrasive saws feature an abrasive disc that cuts or grinds through material.
Abrasives saws are effective at cutting tough materials like tile, metals, and concrete. The cut dimension depends on the abrasive machine. Some, for example, can cut materials as thick as 4 inches in outside diameter (OD), while others can handle only the thinnest materials.
Abrasive cutting machines are simple to operate and need little or no plan. Also, the method is cheap and fast. However, abrasive cutting is not heat tolerant, it does not allow for tight tolerances and it usually causes heavy burring and kerf (slit or notch left behind by cutting tool). Furthermore, it is not does not work well on thick materials.
Band Saw Cutting
Band saw cutting is an electronic process used for voluminous cutting. The most general process for cutting pipe and tubes, band saw cutting handles a wide range of pipe and tube materials. They cut these raw tube materials into an equally wide range of shapes.
Band saws feature an unending band blade that has various tooth contours. Depending on the model, band saws usually rotate vertically or horizontally on two wheels. They also usually feature shuttles, which range in length between 20 inches and 24 inches. The shuttles allow them to cut their materials to virtually any length. Band saw cutting is generally fully automatic, and it often receives help from CNC technology.
The big advantage of band sawing is the fact that it allows manufacturers to cut such a wide range of shapes (I-beams, squares, channels, extrusions, rectangles, etc.). Band sawing does not, however, work well when paired with thin-walled pipes. It also creates burring and struggles to create tight tolerances.

Cold Saw Cutting
Cold saw cutting, or cold sawing, is a cutting method that involves the automated use of a cold saw. A cold saw features a circular blade kept well functioning with cutting lubricant. The blade is fixed in place and operates without heat.
Manufacturers use cold saws to cut small breathe (diameter) or lean walled pipes that require close tolerances. They also use it to cut several materials at once. Note that cold saws only create perpendicular and square cuts.
Because it does not use heat, cold sawing does not leave heat affected zones. This is a great benefit, because it means that any products cut via cold sawing will require fewer successive finishing touches (i.e. deburring)
Shearing
Tube shearing is a cutting technique that manufacturers carry out using a high-speed computerized shearing machine called a tube shear. The tube shear uses two shear plates and ID punches under intense tension.
Regardless of size or wall thickness, tube shear machines cut all material with maximum brink, or maximum limits. In this way, shearing is unique.
Two of the biggest benefits of tube shearing are agility and production volume. Shearing can achieve high tolerances, and it is capable of an extremely high production rate. With shearing, the shorter the cut the higher the production rate. Usually, during an 8 hour run, tube shearing can produce up to 7,000 parts an hour. The main disadvantages of tube shearing are the fact that it is not expensive when used for small volume runs, and it has high tooling costs.
Laser Cutting
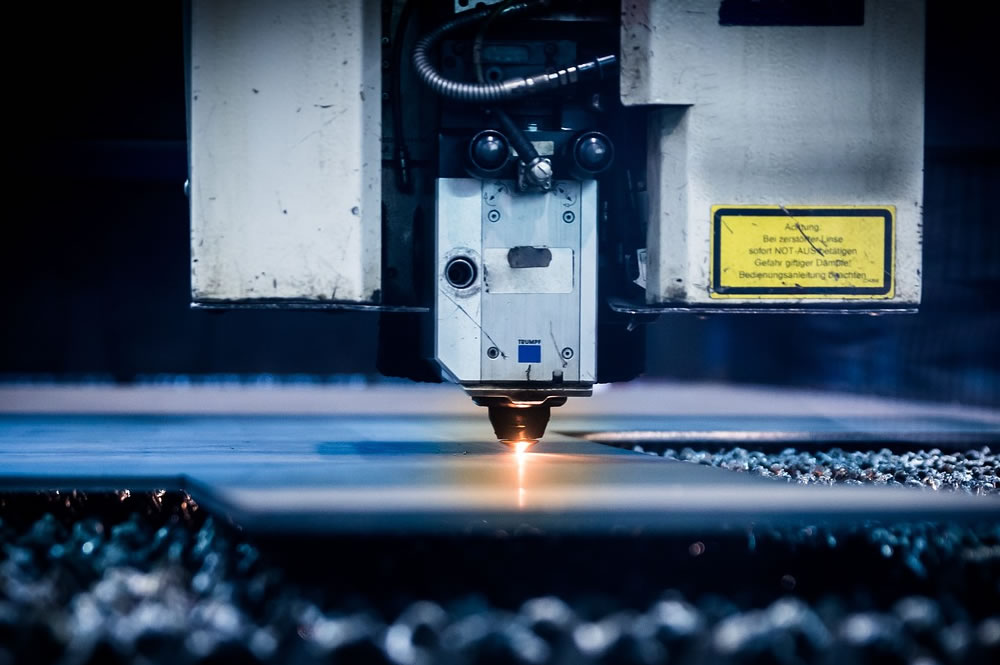
During laser cutting, manufacturers use CNC controlled laser beams to cut materials with extreme precision. Lasers don’t cut the material with force, but with heat. Thus, they creates very little distortion, narrow kerf and very few burrs. If they do leave any burrs, laser cutters can get rid of them.
Manufacturers use lasers to cut hard materials, like titanium. Operators can set lasers to run continuously while they do other work, so they can get more done at once. Because they offer such precision, operators can set them to cut out intricate markings, like number etchings and hole patterns.
Laser cutting does involve a costly investment. However, the results are always so excellent that it usually pays for itself.
Lathe Cutting
Lathe cutting is an older semi-automated pipe cutting technique. It works best with round, thin diameter tubing. Manufacturers perform lathe cutting using single spindle lathe machines. To begin the process, operators send hollow or solid pipe stock through the spindle, where at the end, a collet holds and rotates the stock. As the pipe rotates, tools from the lathe cut at it until it has all the right dimensions.
To add on secondary processes like deburring, grooving, boring or chamfering, manufacturers can attach tools or slides to the lathe machine. In this way, lathe cutting is diverse.
Lathe cutting takes a fairly long time to set up (between half an hour and hour) and lathe machines can only process one product at a time, but once the process gets going, production volume is high.

Equipment for Tube Fabrication
- Mazak lasers
- 3D Mazak SpearGear laser
- SOCO CNC Tube bender with 360 degrees rotating mandrel
- Amada Press Break
- Amada Corner Notcher
- Autoset Programmable Hardware insertion Press
- Rondo Tube and Angle Rolls
- 60 Bliss OBI Press
- Production Drill Press
- MIG, TIG or Robotic Welding
- Powder Coating
Who Uses Pipe Cutting and Why?
Pipe cutting techniques are most popular with engineers and manufacturers of industrial products made from alloy, brass or titanium. Industrial manufacturers use these techniques to cut the pipe and tube into different shapes and sizes for according to the customer’s specifications. They use these technologies because of their benefits in cutting precision in large scales, notwithstanding their disadvantages. For more detailed information on tube fabrication and cutting technologies, visit our list of Tube Fabrication Manufacturers.