Manufacturing Technology Trends That Will Change Your Life
As technology continues to take leaps and bounds in all areas of business, manufacturing is also benefiting from these improvements. Although it may not initially seem this way, these technological improvements have the potential to transform your life.
In this article, we’re going to take a deep dive into the latest manufacturing trends and explain how these might just change your life.
The Latest Manufacturing Processes
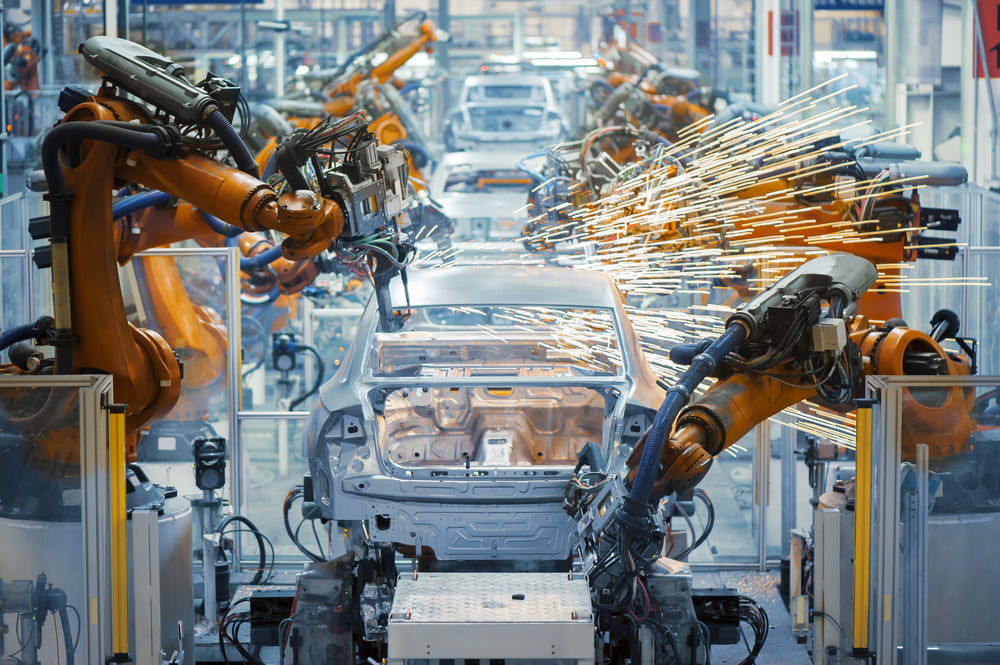
There are many new manufacturing processes that have the potential to rejuvenate lagging U.S. manufacturing. New processing models can double net energy productivity, thus supporting rapid manufacturing of high-quality, energy efficient merchandise at a competitive cost.
Four process technology areas are expected to generate large energy, carbon, and economic benefits across the manufacturing sector.
Reactions and Separations
The following is a list of new technologies that can provide high energy efficiency and process intensification, as well as yield dramatic energy and cost savings in a range of industries including, oil refining, food processing, and chemical production:
- Advanced Water Removal via Membrane Solvent-Extraction Technology
- New Design Methods and Algorithms for Multi-component Distillation Processes
- Process Intensification with Integrated Water-Gas-Shift Membrane Reactor
- Real-Time Remote Detection of HR-VOC Content in Flares - SBIR Phase II Recovery Act
- Ultra-High-Efficiency Aluminum Production Cells
- Grand Challenge Portfolio: Driving Innovation in Industrial Efficiency
- SBIR Phase III Xlerator Program
High-Temperature Processing
Non-thermal or lower energy alternatives to high-temperature processing technologies will allow more efficient production or recovery of critical materials (metallic and non-metallic). These technologies may enable or enhance water-based, selective mining of critical materials from low-grade ores; recovery of high-value resources in archaic electronic equipment and waste; and low-temperature, high-efficiency chemical or electrochemical processes.
Waste Heat Minimization and Recovery
Advances in high efficiency steam production, high-performance furnaces, and pioneering waste-heat recovery will help to improve sustainability, reduce water usage, and reduce the energy waste of U.S. manufacturing.
Sustainable Manufacturing
New manufacturing technologies can reduce production steps, material consumption, or part counts, and will reduce the energy of the manufacturing value chain and decrease the use of raw materials. The same is true of technologies that allow the production of materials or components that increase recyclability. New design and process tools could enable a manufacturing process to meet specific cost, time, energy, and life-cycle energy requirements.
The Latest Manufacturing Technology Trends
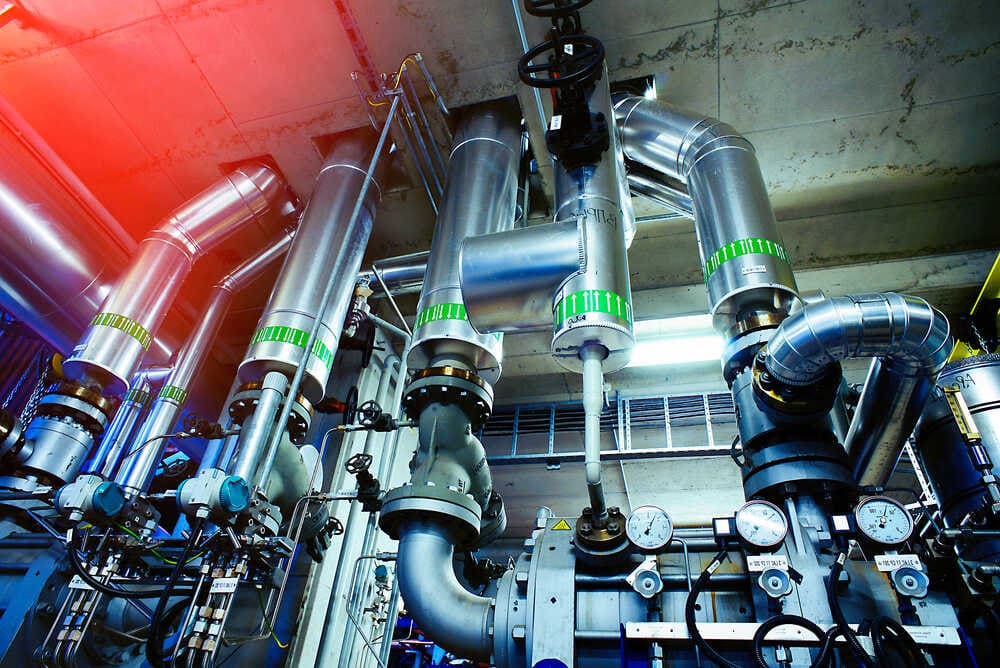
Beyond the physical aspects of manufacturing, there are advances in digitalization that will allow industrial manufacturers create new operating models, aggressive hiring, smart collaborations, and directed investments.
Leveraged Data and Analytics
By upgrading their technical capabilities, industrial manufacturers can bundle services enabled by connectivity and data, replacing the outdated model of selling one big complex machine under warranty and a service agreement for maintenance and repair.
These new services can include condition-based maintenance, which involves ongoing real-time monitoring of equipment to determine its maintenance needs; collaboration with customers on a day-to-day basis; and predictive performance management for large and small projects and equipment.
Innovative Pricing
The traditional pricing model for service contracts will be changed as technology begins to alter the relationship between manufacturers and their customers. We should expect to see a move from pay-for-product to pay-for-performance contracts. Condition-based maintenance, driven by predictive and consistent industrial technology, will become routine. This should translate into fewer visits from repair technicians.
Carefully Developed Strategic Partnerships
Industrial manufacturers must become more active players in technology environment, seeking expertise outside the industry in order to develop equipment connectivity, data analysis, and software. One industrial company has aligned with a wide range of technology firms to create a dedicated cloud-based platform that can run industrial workplaces. But these collaborations are not without risk. Leaders have to balance the practice of close collaboration with strategic partners against the need to stay flexible in contracting and partner selection, all while maintaining a hold on their markets.
Operational Data Mining
If connected machines are to be the backbone of industry in the near future, manufacturers will have to find out how to manage data coming from an avalanche of sensors, integrated equipment and platforms, and faster information processing systems. There is a critical need to hire people who can mine this information and work closely with customers to use the data to improve equipment performance and open new revenue streams.
Talent Development and Retention Strategies
In the digital world, industrial manufacturers often find themselves at a disadvantage when trying to attract and retain IT talent. The majority of talent is geographically centered in Silicon Valley, where many companies move in order to have access to the proper IT talent.
Industrial manufacturers must purposefully map out a technology strategy with specific benchmarks and achievements anticipated for the next 18 to 36 months — then communicate this plan clearly to job candidates. In developing this recruitment program, companies can’t just advertise for someone who can read data; candidates must have a balance between manufacturing savvy and technological skills.
Specific Examples of Manufacturing Technology
Just like the Industrial Revolution completely revolutionized manufacturing, digital transformation is changing the industry. Not since Henry Ford introduced mass production has there been a revolution of this importance. Now, manufacturing companies are using technology to move from mass production to customized production through automation equipment like automated guided vehicles and conveyors.
Consumer expectations and the introduction of connected devices and platforms are driving the digitization of manufacturing. The industry continues to evolve in response to the challenge of ensuring the right products are delivered at the right price to the correct person through a process of improved digitalization.
IoT and Industry 4.0
At the center of industrial transformation is the Internet of Things (IoT), accounting for more than $178 billion in 2016. The manufacturing industry is leading the way in the IoT because of the ways this connected technology has streamlined and simplified many manufacturing processes.
IoT can provide real-time feedback and alerts regarding defects or damaged goods. These implementations reduce cost and waste. The trend of mass customization has allowed manufacturers to more efficiently react to consumer demand. Customers expect the products they use to be intuitive and easy to interact with; therefore, mobilization and connected-ness continue to motivate manufacturers to modernize faster and create software-enabled products. IoT capabilities also offers immediate and consistent online support post-sale.
AI And Machine Learning
A machine’s ability to learn and adopt intelligent human behavior is not a new idea, but it is rapidly progressing. Today, advanced algorithms are transforming the way the manufacturing industry collects information, performs skilled labor, and predicts consumer behavior.
Smart factories with integrated IT systems provide relevant data to both sides of the industrial supply chain more easily, sometimes leading to a 20% increase in production. Quality is no longer a victim of efficiency; machine learning algorithms determine which factors impact service and production quality.
Sensors have replaced human hands, resulting in efficiency, reduced materials waste, and improved accuracy and workflow. Digitizing the industry means lower production costs, quicker turnarounds, and efficiently meeting marketplace demand.
Robots
Traditionally, robots have been used to perform tedious, repetitive tasks on the assembly line. Today’s robots are capable of mimicking more human traits, like dexterity and memory, which makes them more useful in manufacturing. Highly trainable and collaborative, robots are also providing safer working environments for humans by switching places with them in dangerous or hazardous situations.
Manufacturing and the Future
Manufacturing technology is not what it was a decade ago. Today’s increasingly automated and software driven industries have reduced human intervention to pressing only a few buttons.
The application of advanced technologies such as nanotechnology, cloud computing, and the Internet of Things (IoT) are changing the face of manufacturing in astonishing ways.
Here are some of the specific advanced technologies that are driving growth.
3D Printing
One of the biggest news items in the manufacturing technology sector in the last few years is 3D printing technology. It has captured the imagination of the general public and the manufacturing community.
Within just a few years, the technology has evolved so much that it is now possible to produce almost any component using metal, plastic, mixed materials, and even human tissue. It has allowed engineers and designers to think very differently when considering product development. As more manufacturers adopt and use 3D printing technology, there is little doubt that 3D printing will change the face of manufacturing.
Nanotechnology
Nanotechnology seems to be the technology of the future, but the first generation of the technology is already here. It involves the manipulation of matter on atomic, molecular, and supra molecular scales, thus, bringing with it, super-precision manufacturing. It is going to play an indispensable role in every manufacturing industry in the future. In many ways, it has already changed the world:
- Faster computer processing
- Smaller memory cards that have more memory space
- Clothes that last longer and keep the wearer cool in the summer
- Bandages that heal wounds faster
- Tennis and bowling balls that last longer
The space technology and biotechnology that is already in use with nanotechnology are just the beginning of how technology can change all industries.
The Internet of Things (IoT)
The Internet of Things (IoT) allows electronic devices connected to each other, within the existing Internet infrastructure, to communicate with one another without human direction.
An IoT device connects to the internet and is capable of generating and receiving signals. IoT enables connected devices to “talk” to each other, sending and receiving critical notifications.
For example, when a device detects a failure, the IoT connected device sends a notification to another device or a user. This type of small, but critical, application of IoT in manufacturing results in reduced downtime, increased quality, reduced waste and less overall costs.
Cloud Computing
Cloud computing is using a network of Internet-connected remote services along various points to store, manage, and process data. Many companies are already using cloud computing, although the manufacturing industry is still uncertain about the technology due to connectivity and security concerns.
Though sketchy at first, cloud computing is growing more stable and reliable as time passes. Manufacturers are using cloud computing software to connect manufacturing plants spread out over various geographic areas to share data quickly and efficiently. With cloud computing, manufacturers reduce costs, gain greater quality control, and increase the speed of production.
Big Data and Predictive Maintenance Technology
Manufacturing industries will significantly increase their efficiency and productivity with technologies that allow them to collect, process, and measure big data in real time. These technologies include electronic devices that connect factories through the internet and web pages that double as dashboards for controlling the processes. Predictive maintenance technology helps predict snags and defects and thus cuts downtime and costs.
Augmented Reality
Despite the failure of Google Glass, the concept of augmented reality eye wear is practical enough to survive. In manufacturing, the technology has widespread potential including:
- Real-time instructions/guidance
● Real-time notifications
● Real-time monitoring of worker tasks
● Improved safety warnings
● More effective training
● Data retrieval
● Reduce necessity for on-site maintenance/technical support
Like other technologies discussed here, augmented reality is still a young technology, and it will be exciting to watch it grow and evolve in the next few years.
Are Manufacturers Ready for New Technologies?
As we move into the future, it is critical that manufacturers with outmoded techniques and processes look to invest in upgrading. Not only should they consider upgrading in terms of their digital infrastructure, but they need to upgrade their equipment, hire up- and- coming talent with a balance of manufacturing and digital skills, and prepare to collaborate with companies whose digital resources far outstrip their own.