Rotational Molding
Rotational molding, or rotomolding, is a specialized plastic fabrication process used to create hollow plastic products. This method relies on a rotating mold and high heat to produce durable, seamless parts with uniform wall thickness.
The History Rotational Molding
The origins of rotational molding trace back to 1855 when British inventor R. Peters used biaxial rotation and heat to form metal shells for artillery and other hollow vessels. His goal was to achieve consistent wall thickness and density, but it took nearly 50 years for engineers to apply his discovery on a larger scale.
In 1905, American innovator Fred A. Voelke advanced the process by using it to create hollow wax objects. Five years later, G.S. Baker and G.W. Perks applied the method to produce the first hollow chocolate eggs. The technique gained further traction in the 1920s when R.J. Powell used it to mold plaster of Paris.
The 1940s and early 1950s marked a turning point as plastic rotational molding emerged, particularly in the toy industry. Manufacturers adapted rudimentary molding machines using automobile parts, electric motors, and gas burners. Nickel and copper molds shaped PVC materials, while cold water baths provided cooling. Hollow plastic toys, such as doll heads, became widely produced, leading to broader industrial applications, including traffic safety equipment, armrests, and buoys.
As more manufacturers adopted rotational molding, machine designs evolved, incorporating indirect heating systems for greater efficiency. A major breakthrough came in Europe with the shift from direct gas jets to high-velocity air heating. In the 1960s, the Engel process introduced low-density polyethylene as a new raw material, along with an improved cooling system that allowed molds to harden while still in motion.
By 1976, the industry had grown enough to establish the Association of Rotational Moulders (ARM) in Chicago. The 1980s saw further advancements with the introduction of materials like nylon and polycarbonate, enabling the production of fuel tanks, water tanks, and industrial molds. Researchers at Queen’s University Belfast made strides in refining cooling systems, improving process precision and efficiency.
Today, rotational molding continues to evolve, driven by new materials and innovations that enhance efficiency and expand its applications. Engineers and scientists push the boundaries of what’s possible, ensuring that rotomolding remains a critical manufacturing method across diverse industries.
Benefits of Rotational Molding
Rotational molding offers distinct advantages over other forming processes, making it a preferred choice for manufacturers. One key benefit is the ability to switch between colored plastics without the need for extensive line cleanings or die purging, saving both time and operational costs. Unlike other molding techniques, rotomolding does not rely on pressure, which helps reduce tooling and energy expenses. Additionally, the equipment required is more cost-effective, as the cast or welded molds used in the process are significantly less expensive than alternative options. Another advantage is its sustainability—most excess material generated during production can be recycled, making it an economical and environmentally friendly solution.
Rotomolding also ensures a seamless, uniform coating, creating strong exterior corners without stress points. This makes it particularly beneficial for manufacturing pressure vessels and tanks, where even the smallest seams or cracks could lead to failure. Furthermore, the process allows for in-mold assembly of products or prefinished parts, eliminating the need for additional tooling. Unlike other methods that require new dies for even minor design adjustments, rotational molding offers exceptional flexibility, reducing design and production timelines.
Materials in Molded Products
Manufacturers primarily use powdered polymer resins for rotational molding, with over 80% sourced from the polyethylene family. Common plastics used include LDPE (low-density polyethylene), LLDPE, PEX, and HDPE. Other frequently used materials include polypropylene, PVC, nylon, and polycarbonate, each offering unique properties suited to different applications.
- Polyethylene (PE) – Known for its hardness, rigidity, and high ductility, this material provides excellent impact strength, low friction, superior chemical resistance, low permeability, and good electrical insulation.
- Polypropylene (PP) – Similar to polyethylene but with enhanced thermal resistance and mechanical properties. When uncolored, it can also be made translucent.
- Polyvinyl Chloride (PVC) – Available in both rigid and flexible forms, PVC offers high hardness, good elasticity, strong chemical resistance, and good insulation properties, though it does not insulate as well as polyethylene or polypropylene.
- Nylon – A family of synthetic polymers valued for their high melting points, superior abrasion resistance, durability, and excellent chemical, thermal, and UV resistance.
- Polycarbonate – Naturally transparent, polycarbonate is strong, tough, and heat-resistant, with excellent dimensional stability and color retention.
Rotational molding relies on molds made from either stainless steel or aluminum, which are either welded together or die-cast.
- Stainless Steel – Offers exceptional durability, along with resistance to corrosion, rust, and stains.
- Aluminum – A lightweight metal with high corrosion resistance, making it ideal for mold fabrication.
By combining these materials with the inherent advantages of rotational molding, manufacturers can create durable, cost-effective, and customizable products tailored to a wide range of applications.
Rotomolding Manufacturing Process
Rotational molding, or rotomolding, begins with a specialized machine equipped with arms called spindles that support the molds containing raw plastic material. The machine moves the molds through a carefully controlled sequence—starting from the loading area, passing through a heating chamber, and finally entering a cooling chamber. This entire process unfolds in four distinct stages, typically lasting between 15 and 90 minutes.
Charging Phase
The process starts with the charging phase, where a precise amount of raw plastic material is loaded into a metal mold, which is then securely sealed. The method of loading can vary depending on the type of machine used.
Heating Stage
Next, the mold enters a heating chamber—often an oven—where it slowly rotates on both vertical and horizontal axes. This controlled movement ensures that the plastic powder melts and evenly coats the interior walls of the mold, preventing material buildup in any single area.
The duration of this heating phase is critical. Excessive heating can degrade the plastic, reducing its durability and impact resistance. On the other hand, insufficient heating prevents the material from fully melting and adhering to the mold walls, potentially leading to large air bubbles that weaken the final product. Manufacturers use fine plastic powders in this process because rotomolding relies on low pressure, making it essential for the material to distribute evenly. Additives can be incorporated into the plastic to enhance properties such as corrosion resistance and static dissipation, ensuring the finished product meets specific performance requirements.
Cooling Stage
Once the plastic has completely coated the mold, the cooling stage begins. Fans or water jets are used to gradually cool and solidify the plastic. This stage is crucial because rapid cooling can cause warping or defects in the final shape.
As the material cools, it naturally shrinks, which helps with product removal. In earlier days, operators determined the cooling duration manually, but modern machines now feature sensors that monitor mold temperatures, ensuring precise and consistent cooling cycles.
Removal Phase
After the plastic has fully hardened, the mold is carefully opened, and the finished part is manually removed. Shrinkage can sometimes make this step challenging, requiring careful handling. If a product needs additional structural reinforcement, features like ribs can be incorporated directly into the mold design..
Designing Rotationally Molded Parts
Effective design is crucial in rotational molding. Manufacturers consider key factors such as material selection, additive requirements, and mold type. The size, shape, color, and mechanical properties of the final product—such as strength, flexibility, and thermal resistance—all influence design decisions.
Custom molds allow for tailored solutions, including unique textures, colors, and finishes. Logos, graphics, and labels can be embedded directly into the molded part, ensuring durability. If reinforced joints or structural enhancements are needed, they can be seamlessly integrated into the design.
For specialized rotational molding solutions, consulting with an experienced manufacturer can help optimize materials, design, and production methods to achieve the best possible results.
Rotationally Molded Plastics Images, Diagrams and Visual Concepts
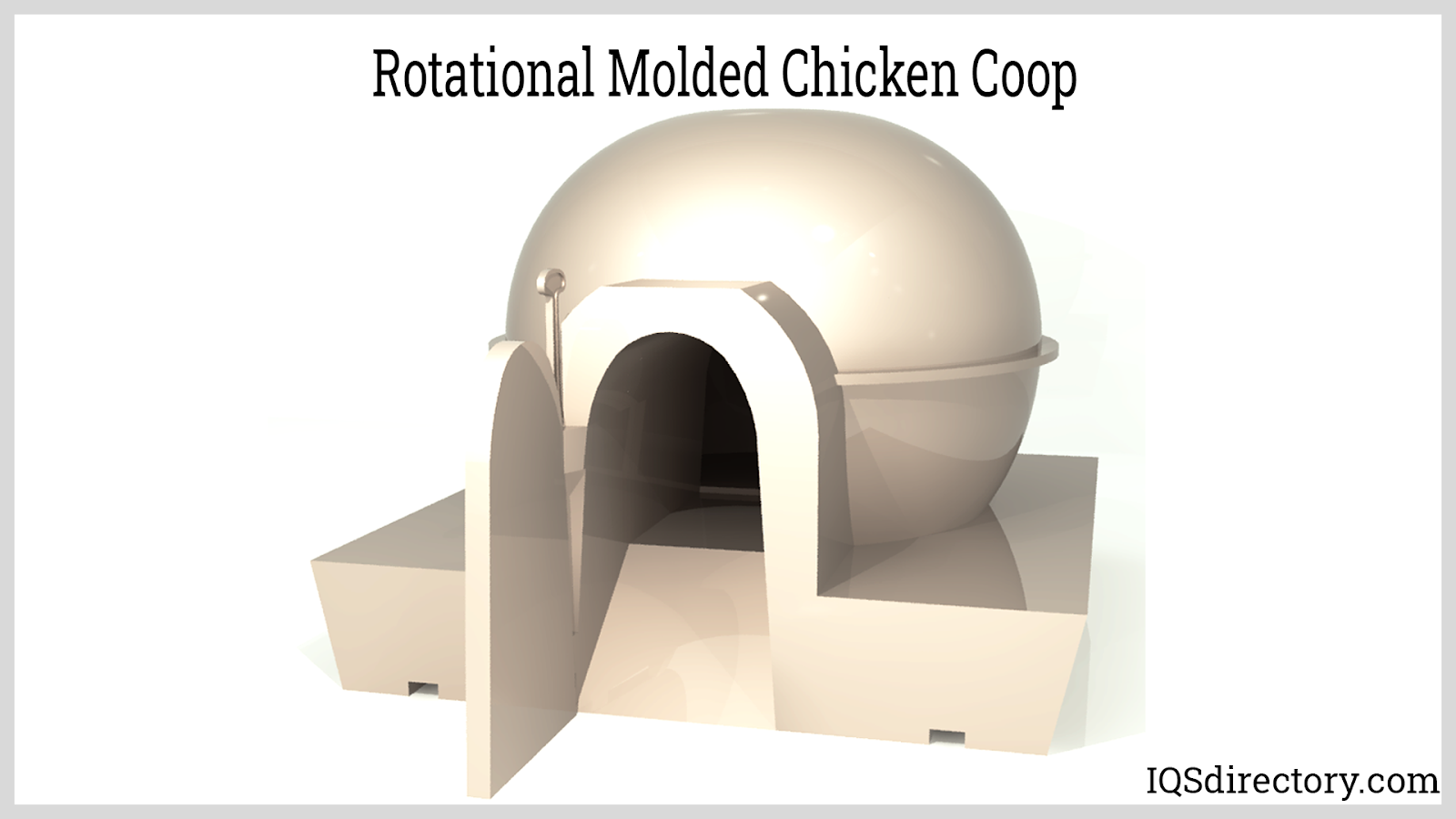
An example of the products that can be produced using rotational molding.
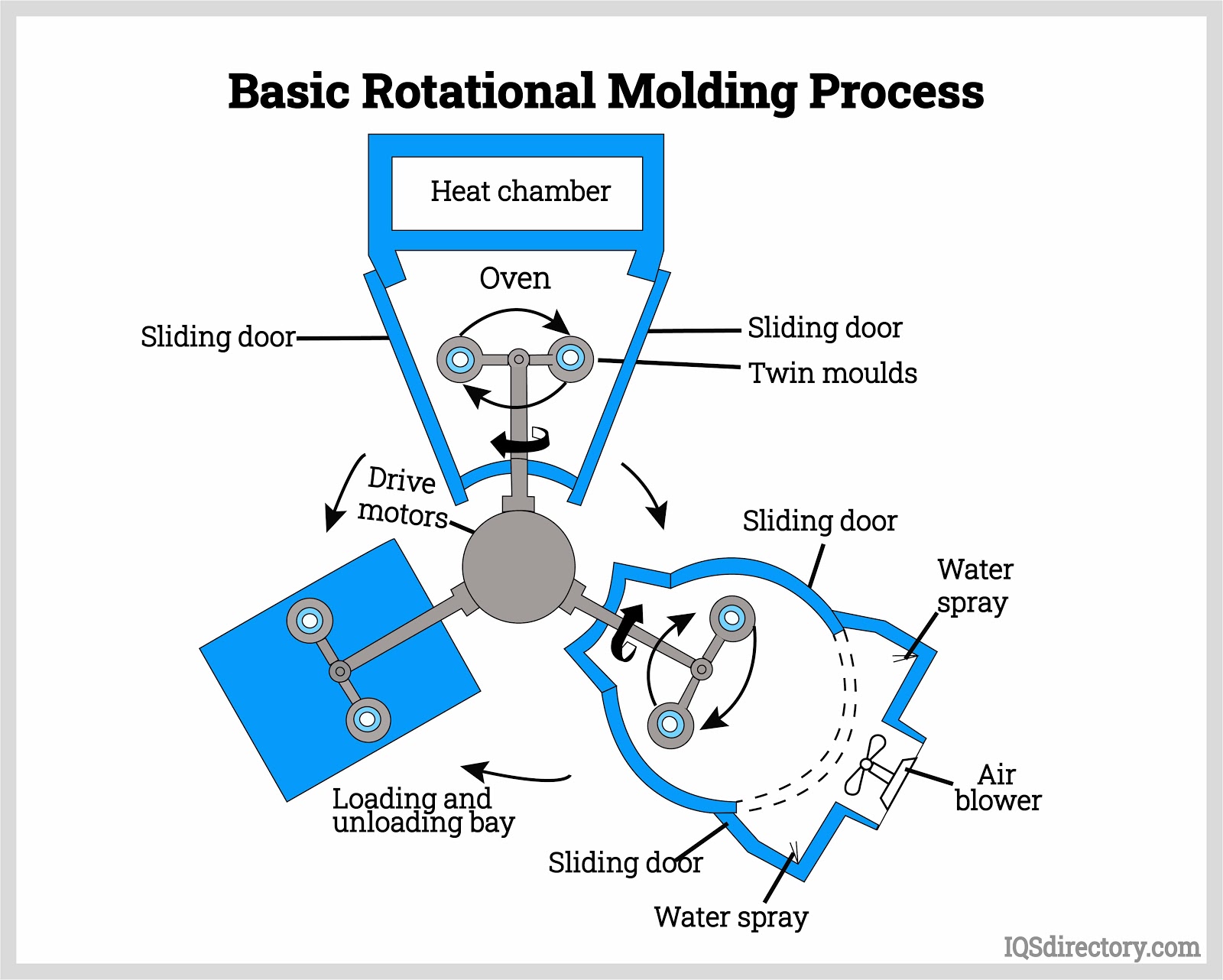
The basic process of rotational molding.
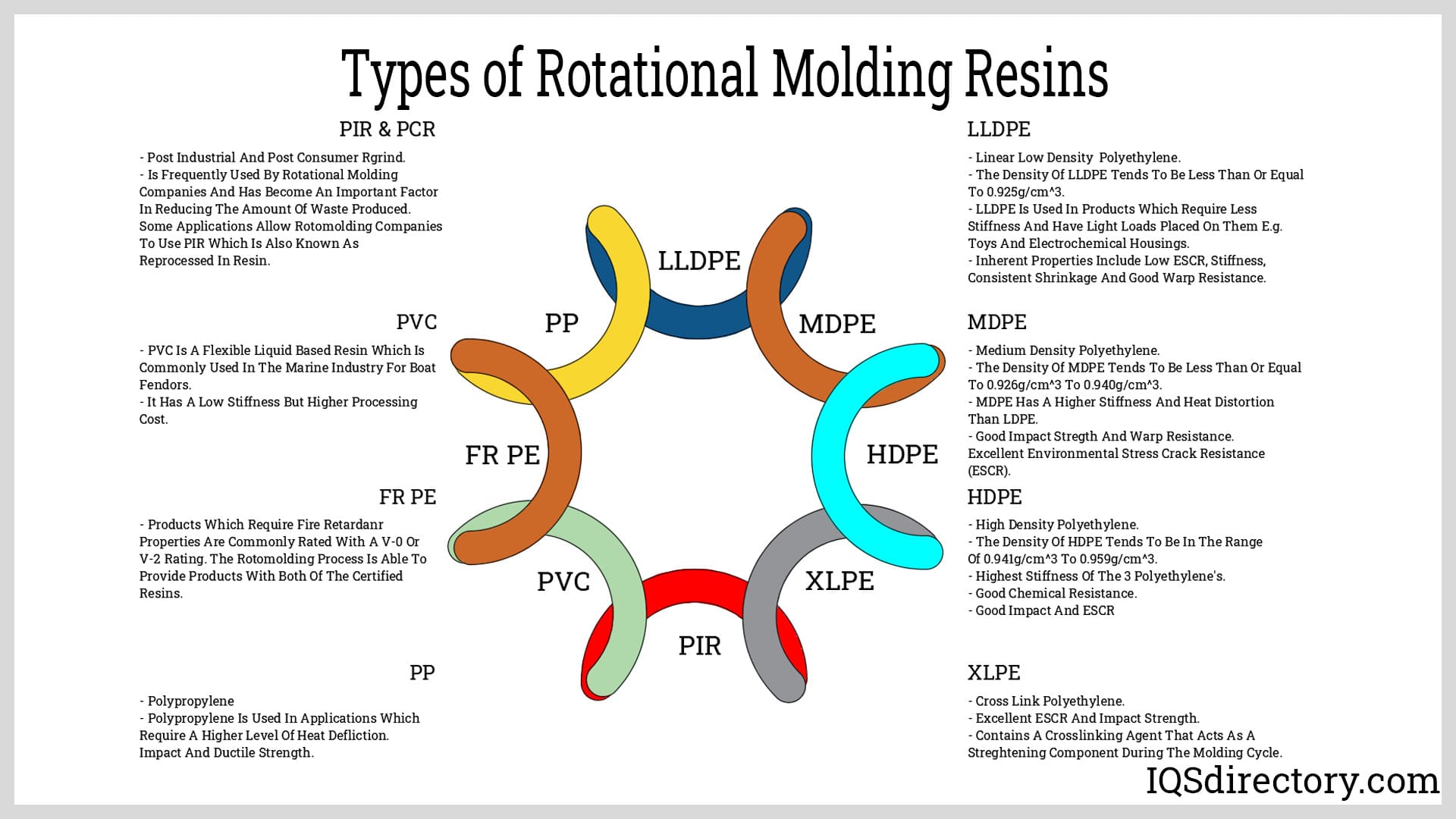
The different materials that are used in the rotational molding process.
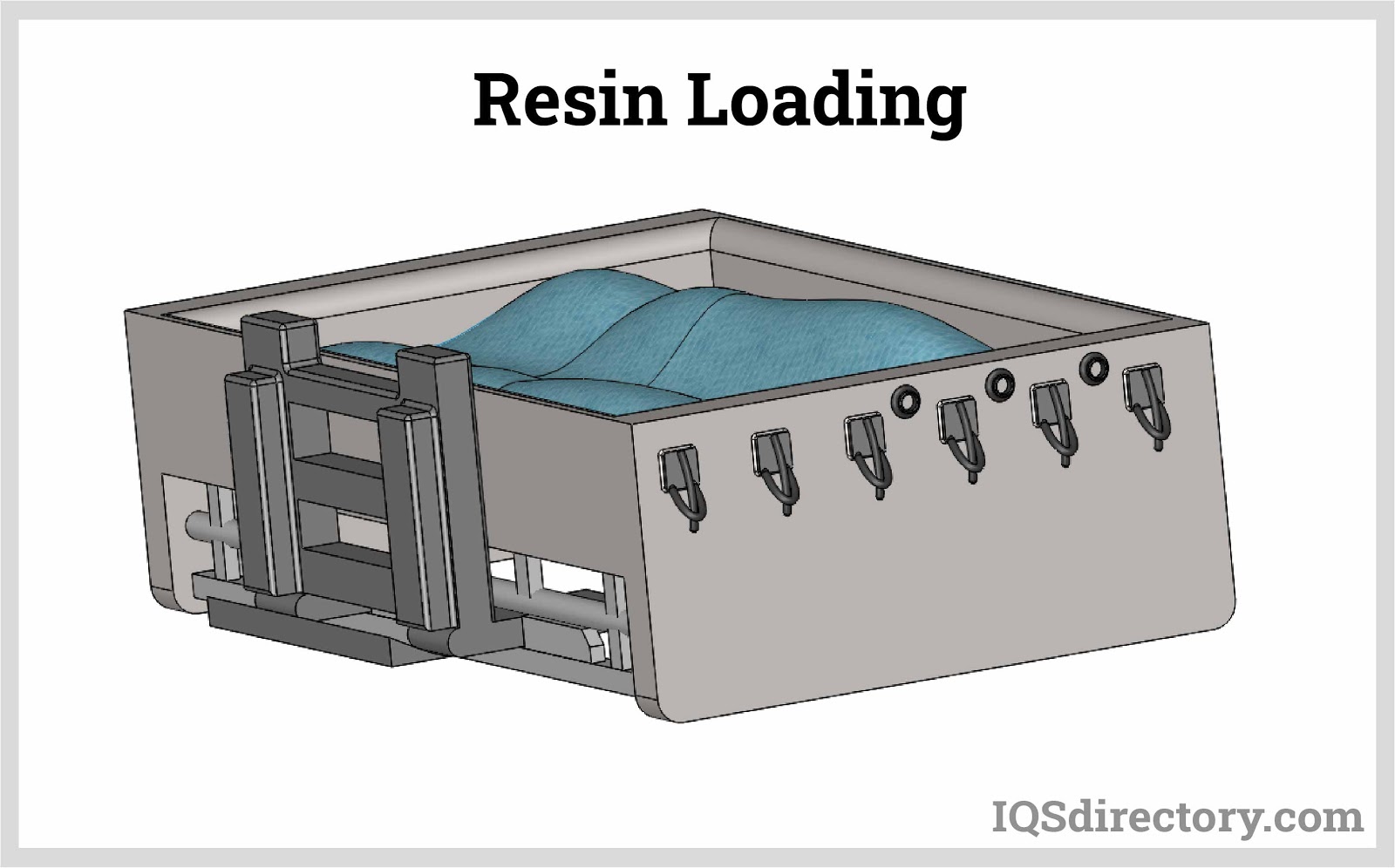
Measuring the quantity of the polymer, which is in powdered resin form which must be fine sizes, homogeneous, and dried.
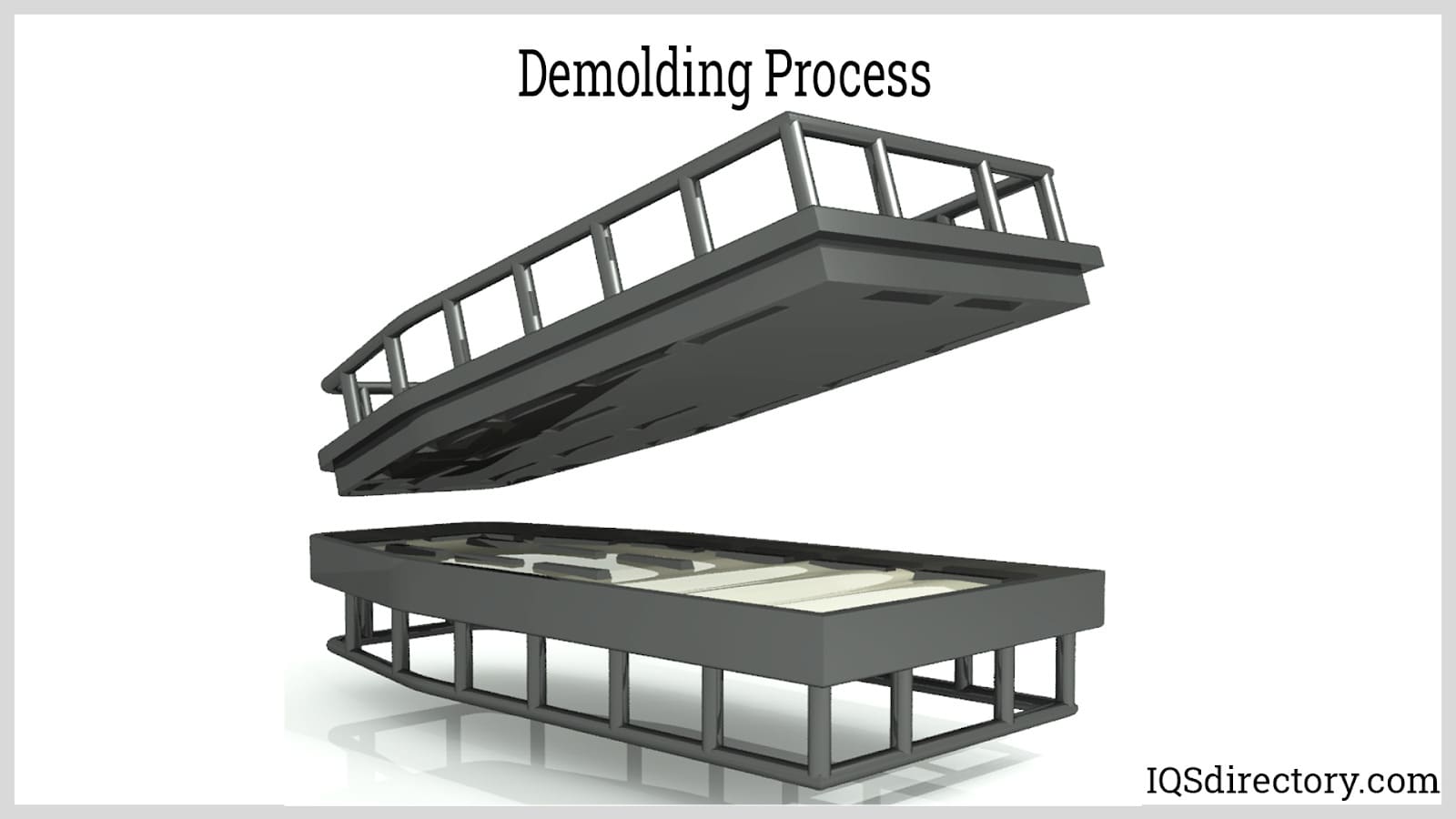
The cooling process to remove the mold which ejects airs to life the part out of the tool.
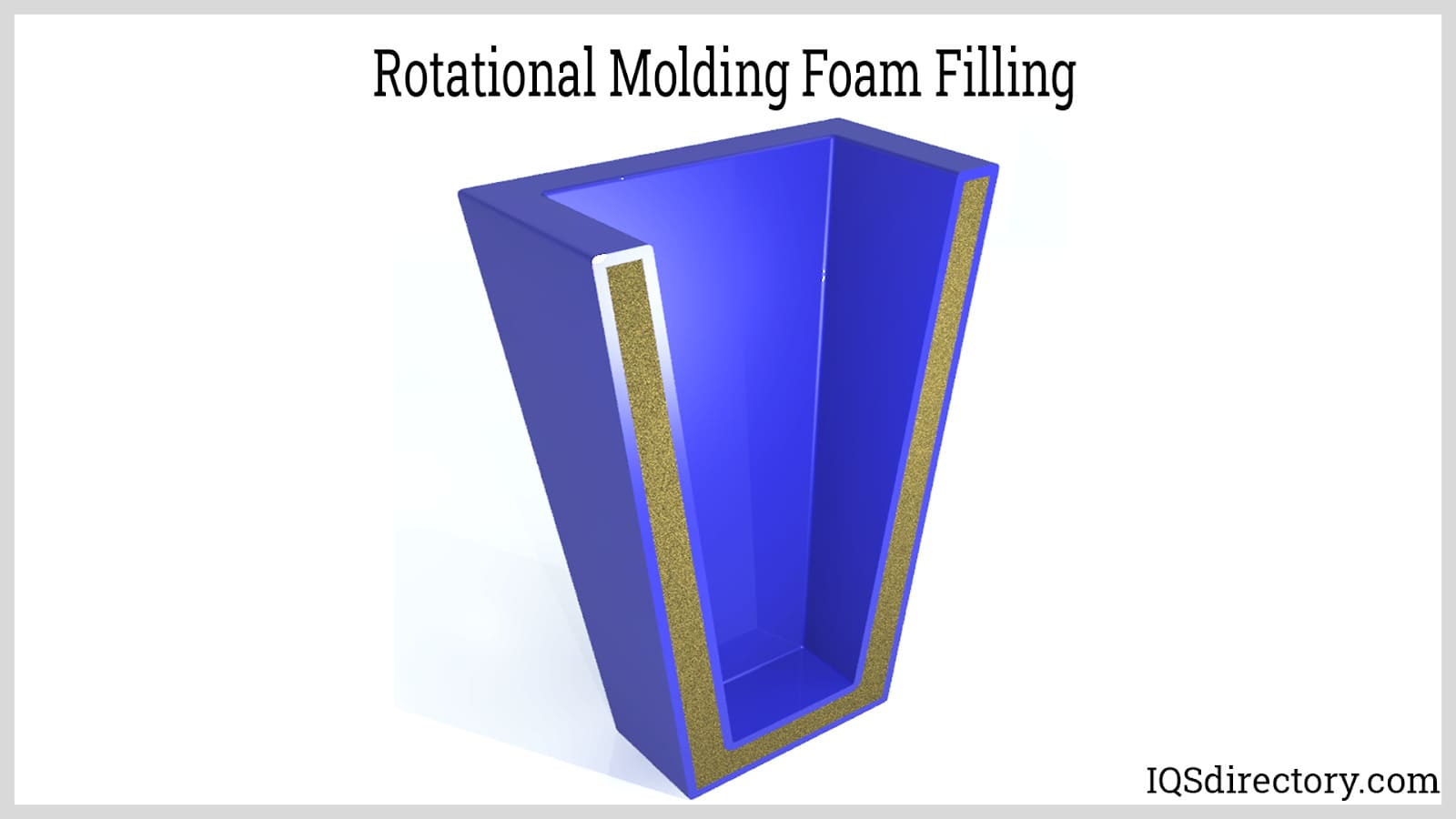
An example of secondary processes depending on the finished product.
Types of Rotationally Molded Plastics and Processes
Cross-Linked Polyethylene
This material is ideal for rotomolded products exposed to extreme cold, offering enhanced durability and impact resistance.
Custom Rotational Molding
Our custom services allow for the design and production of rotomolded products tailored to specific needs, ensuring optimal performance and precision.
High-Density Polyethylene
Known for high-flow molding and exceptional molecular weight performance, HDPE delivers interior gloss development, ductile cold temperature impact resistance, and a distinct off-gas odor indicating proper chemical cross-linking.
Linear Low Density Polyethylene
Offering superior fit and finish, LLDPE provides high impact strength, excellent tensile properties, and reliable dielectric strength in rotomolded products.
Plastic Rotational Molding
A process where molten plastic rotates within a mold, shaping it into durable, seamless products.
Polyethylene
A lightweight material with a low modulus of elasticity, polyethylene ensures thick-walled sections where needed while maintaining impressive impact resistance.
Polyvinyl Chloride
Commonly known as vinyl, PVC offers outstanding transparency, chemical resistance, long-term stability, and excellent weatherability. Available in rigid or flexible forms, it suits diverse applications.
Rotational Molders
Also called roto molders, these machines fabricate hollow plastic components using controlled rotation and heat.
Rotational Moulding
A low-pressure process that creates seamless, hollow plastic parts with consistent wall thickness.
Rotationally Molded Fuel Tanks
Constructed from seamless polyethylene, these tanks withstand saltwater, UV exposure, solvents, and extreme temperatures while retaining molded-in graphics, logos, and warnings.
Rotationally Molded Plastics
One-piece plastic components produced through a rotational molding machine, designed for durability and structural integrity.
Rotomolds
Machines engineered for producing hollow, single-piece plastic parts through rotational molding.
Rotomolded Products
Hollow plastic parts manufactured via rotational molding, ensuring strength and longevity.
Rotomolded Tanks
Seamless plastic containers designed for bulk material storage, offering durability and leak resistance.
Rotomolding
Also known as rotomoulding, this four-step process creates robust, hollow plastic components.
Types of Rotomolder Machines
Rotomolders, the machines powering rotational molding, typically include four key components: an oven, molds, mold spindles, and a cooling chamber. Molds define the shape of plastic products and are either welded or cast. The oven heats the molds, while the spindles ensure even coating by rotating along multiple axes. The cooling chamber rapidly hardens the plastic by lowering the mold’s temperature.
Rotomolders come in various configurations to accommodate both simple and complex designs:
Carousel Type
The most common bi-axial rotomolding machine, featuring either four or six stations. These machines allow continuous operation, with one arm in the heating station, another in cooling, and a third handling loading and unloading.
Clamshell
Designed with a mechanical arm for multi-axis rotation, these machines integrate heating and cooling in the same chamber, making them compact and cost-effective.
Rock and Roll
Built for producing long, narrow parts, these machines rotate molds 360 degrees on one axis while simultaneously rocking them 45 degrees on another. Their efficient heating chambers make them ideal for high-volume production.
Vertical Machines
Also called over-rotating machines, these feature separate heating and cooling zones with front-loading capability. Their compact chambers maximize energy efficiency while maintaining exceptional performance.
Shuttle Type
These machines shuttle molds between heating and cooling chambers while allowing bi-axial rotation. Their cost-effectiveness and ability to produce large-sized products make them a versatile choice.
Each machine type is designed for specific manufacturing needs, ensuring efficiency, precision, and high-quality results in rotational molding.
Applications of Rotational Molding
Customers trust the rotomolding process because it produces durable, single-piece components with uniform wall thickness and high tensile strength. These qualities ensure exceptional product performance while keeping tooling costs low and minimizing the need for additional fabrication.
Rotational molding is widely used across industries, including food and beverage processing, pharmaceuticals, wastewater management, agriculture, plumbing, sporting goods, packaging, material handling, chemicals, fuel and oil, marine, road construction, automotive, and toy manufacturing.
Typical rotomolded products, such as storage and fuel tanks, are hollow with large capacities and maintain consistent thickness and density for superior durability. Other common applications include outdoor furniture, kayaks and canoes, playground slides, safety cones, footballs, sports helmets, plastic tanks, beverage bottles, large trash containers, and various types of hollow bins.
Things to Consider When Choosing Rotational Molding
Selecting a quality rotomolded product starts with finding the right manufacturing partner. With countless options online, it can be overwhelming to navigate the choices. That’s where IQS comes in—we streamline the search process by connecting you with reputable molding service providers.
To make an informed decision, explore the manufacturers listed at the top of this page. Visit their websites, identify a few that align with your needs, and reach out with your specifications. Be sure to communicate details such as function, industry requirements, dimensions, shape, color, strength, and any other key product characteristics. Additionally, clarify your budget and timeline. As you gather information, compare not just technical capabilities but also customer service. The right manufacturer will combine expertise with responsiveness to deliver the best results for your project.
Variations and Similar Processes to Rotational Molding
While rotational molding is an excellent solution for many applications, other molding techniques offer distinct advantages depending on the project’s requirements.
Extrusion
Extrusion is ideal for creating products with a fixed cross-sectional profile. Unlike molding, this process forces material through a die rather than shaping it within a mold. Extrusion excels at producing complex cross-sections and works well with brittle materials, as it only applies compressive and shear stresses. The process also yields high-quality surface finishes.
Injection Molding
Injection molding utilizes a hopper, heated barrel, nozzle, and mold. During this process, molten material is injected under pressure into a cold mold, allowing it to solidify rapidly. Compared to rotational molding, injection molding is faster and better suited for producing metal components or sharp, threaded parts.
Blow Molding
Blow molding is specifically designed for manufacturing hollow plastic parts. This method begins with melting plastic and forming it into a parison—a tube-like shape with an open end. The parison is then placed in a mold, where compressed air expands it against the mold’s walls. Once cooled, the mold opens, and the finished part is released. Blow molding is primarily used for producing bottles and other hollow containers.
Rotational Molding Terms
Blow Molding
A widely used process for shaping hollow thermoplastic products like bottles and containers. This method primarily falls into two categories: extrusion blow molding and injection blow molding.
Chemical Cross Linking
A process in which individual polymer particles bond together at a molecular level, enhancing the strength and durability of the material.
Chemical Resistance
The ability of a material to withstand exposure to various chemicals without degrading. Plastics excel in this area, making them ideal for applications like holding tanks and industrial containers.
Corrosion
The deterioration of a material, often due to oxidation or chemical reactions, such as the rusting of iron.
Cycle Time
The total duration required for a rotational molding process, from loading raw plastic into the mold to the final removal of the fully formed product.
Deflashing
The removal of excess material from a molded part, particularly along seam lines where excess plastic may form during molding.
Density
A key characteristic of polyethylene (PE) that influences stiffness, impact resistance, and overall product performance.
Elasticity
A material's ability to return to its original shape after being stretched or compressed.
Fusion Temperature
The critical temperature at which plastic resin melts and begins adhering to the mold’s surface, ensuring proper formation.
Grindability
The ease with which plastic can be ground into a fine powder. Most plastics undergo grinding before being used in the rotational molding process.
Impact Resistance
A material’s ability to absorb energy and resist fracturing when subjected to sudden force or impact.
Plastic
A broad term for synthetic or semi-synthetic materials that can be molded or extruded into various forms. Plastics are commonly used for products, coatings, and adhesives.
Polymer
A long-chain molecular structure formed by linking repeating monomer units, giving materials their unique properties.
Pourability
The rate at which plastic powder flows through a funnel. For rotomolding, a material must have a minimum flow rate of 185 grams per minute to ensure proper molding.
Resin
A solid or semi-solid organic material, often translucent or transparent, used in plastics, adhesives, and coatings.
Spindles
The rotating arms of a rotational molding machine, responsible for moving molds between different processing stages. These spindles spin along multiple axes to evenly distribute material within the mold.
Thermal Stability
A resin’s ability to endure high temperatures without degrading. Some materials require precise temperature control to ensure successful rotomolding.
Thermoplastic
A type of plastic that softens when heated and hardens when cooled, allowing it to be reshaped multiple times. Common examples include polyethylene (PE), polypropylene (PP), vinyl, and nylon.
More Rotational Molding Information