Rubber Injection Molding
Since the inception of Injection molding techniques, the production of a wide range of products has become possible. Items such as bottles, lids, automotive parts, and a wide range of rubber products with complex part designs and geometries are the outcome of injection molding technology.
Compared to other production techniques such as compression molding or rubber transfer molding, injection molding can have a higher level of automation. Injection molding is an ideal manufacturing method for many components due to strict control over flash, waste, and faster rubber cure periods.
Quick links to Rubber Injection Molding Information
Why Use Rubber Injection Molding?
Rubber Injection Molding is a process that differentiates from the conventional injection molding process by using unvulcanized rubber as raw material. It not only produces rubber products with quick cycle time as compared to compression molding, but this technique allows you to manufacture custom-shaped rubber products with minimal wastage.
These are some of the abundantly used raw materials for rubber injection molding:
- Silicone
- Neoprene
- Ethylene Propylene Diene Monomer (Commonly Known as EPDM Rubber)
- Nitrile
All of these materials provide rubber products that are of exceptional quality and finish.
Types of Rubber Injection Molding
Since the 1960s, the process of rubber injection molding has developed three particular branches based on the type of raw material injected.
Thermoplastic Rubber Injection
In this type of rubber injection molding, the raw material used are elastomers. Elastomers are unique in the sense that they are processed as plastic but they show behavior or performance similar to rubber. The vulcanization process usually needs to take place in order to process the uncured rubber. But elastomers are polymers, and the vulcanization process is not required in this case. The only disadvantage associated with this process is that it is only plausible for high-temperature applications.
Organic Rubber Injection
It is the standard rubber injection molding technique that involves mixing raw material and stripping it into the screw. The amount of the raw material being fed to the barrel of the machine is in fixed quantities. As the material is preheated so due to the low viscosity it easily flows to the cavity of the mold.
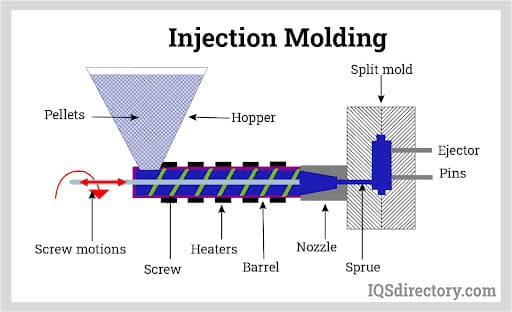
Liquid Injection Molding
Liquid Injection Molding (LIM) involves the use of silicone for the production of usable rubber products. The process is similar to the standard rubber injection molding process. The two-part compound of liquid silicone is first cured and afterward fed to the injection unit. One of the many benefits of this process is that the usage of closed systems restricts contamination.
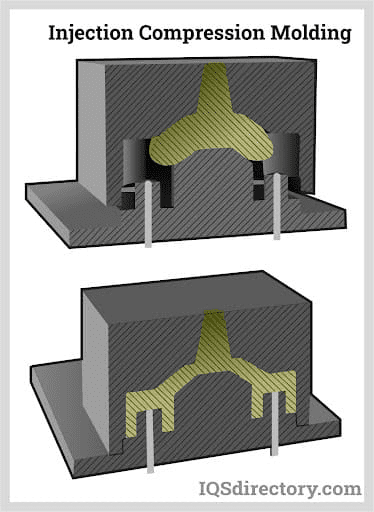
Benefits of Rubber Injection Molding Technique
Following are some of the valuable benefits of using the Rubber Injection Molding Technique:
- The percentage of waste produced using this method is extremely low.
- Complex geometric shapes and part designs can be produced through this method.
- The average cycle time is reduced as the raw material is preheated, and due to the low viscosity, it easily flows into the mold cavity.
- Frequent repeatability allows for mass production.
Applications of Rubber Injection Molding
The end products of injection molding are long-lasting and can be made in a wide range of shore values, making them suitable for a wide range of industries. Electrical overmolding, seals, stoppers, soft-touch grips, infant bottles, and other pliable parts are some of the applications for rubber injection molded parts.