Rubber Tubing
Rubber tubing consists of hollow channels crafted from a diverse range of natural and synthetic rubber materials, designed for the transmission of liquids and gases. This versatility has earned it various names, including hoses, tubes, and pipes.
The History of Rubber Tubing
Early rubber tubing originated from natural rubber, specifically pure gum rubber extracted from the latex of the Pará rubber tree and other latex-producing plants. While latex rubber tubing proved effective for many years, its widespread use declined due to the increasing recognition of latex allergies among users. Additionally, rising latex costs and advancements in synthetic rubber development contributed to the shift away from natural rubber.
In 1909, scientists at Bayer synthesized the first synthetic rubber in response to the growing demand for durable, high-performance materials, particularly for tire manufacturing. This breakthrough spurred rapid advancements in synthetic rubber production, leading to the creation of new rubber formulations like butyl rubber, which played a crucial role during both World Wars.
Innovation in rubber science has continued, with researchers developing new rubber tubing materials tailored to specialized applications. In 1957, the introduction of Viton fluoroelastomer revolutionized the aerospace industry by offering exceptional corrosion resistance and high-performance capabilities. Today, advancements in rubber technology persist, driving the evolution of rubber tubing to meet the demands of ever-changing industries.
Advantages of Rubber Tubing
Portability and Storability
One of the greatest advantages of rubber tubing is its ease of portability and storage. Despite their strength and durability, rubber tubes remain highly flexible, allowing them to be folded or rolled for convenient storage. Their compact nature ensures they take up minimal space, regardless of their weight, making them ideal for environments where storage efficiency is key.
Affordability
Rubber tubing offers a more economical alternative to metal or plastic tubing. Unlike metal pipes, which are priced by weight, rubber tubes are generally more affordable, with pricing starting below $10. Factors such as durability, protective coatings, and customization options can influence cost, but even premium rubber tubing remains an accessible and cost-efficient solution.
Easy Maintenance
Maintaining rubber tubing is straightforward. If blockages occur, they can typically be resolved without the need for specialized assistance, provided proper safety and operational guidelines are followed. This ease of maintenance reduces downtime and ensures continued performance with minimal effort.
Flexibility
Rubber tubing enables the creation of highly flexible fluid distribution systems that can accommodate twists and turns without compromising flow. Whether for home or industrial use, rubber tubing can be arranged and adjusted to meet specific requirements, ensuring optimal performance in any setup.
Versatility
Rubber tubing is available in a wide range of designs to suit various applications. Manufacturers offer options with weather-resistant coatings, explosion-proof capabilities, and aesthetic customizations to fit different environments. Whether for industrial, medical, or commercial use, rubber tubing can be tailored to meet specific needs.
Rubber Tubing Design
Rubber tubing is produced through extrusion, where uncured rubber is shaped into its final form before undergoing vulcanization for added strength and resilience. Manufacturers utilize both natural and synthetic elastomers, including neoprene, PVC, silicone, Viton, EPDM, nitrile, and more.
Customization options extend beyond size and shape, encompassing chemical resistance, abrasion resistance, temperature tolerance, and color. By incorporating specialized additives during the extrusion process, manufacturers can fine-tune tubing properties to meet precise application requirements.
Rubber Tubing Images, Diagrams and Visual Concepts
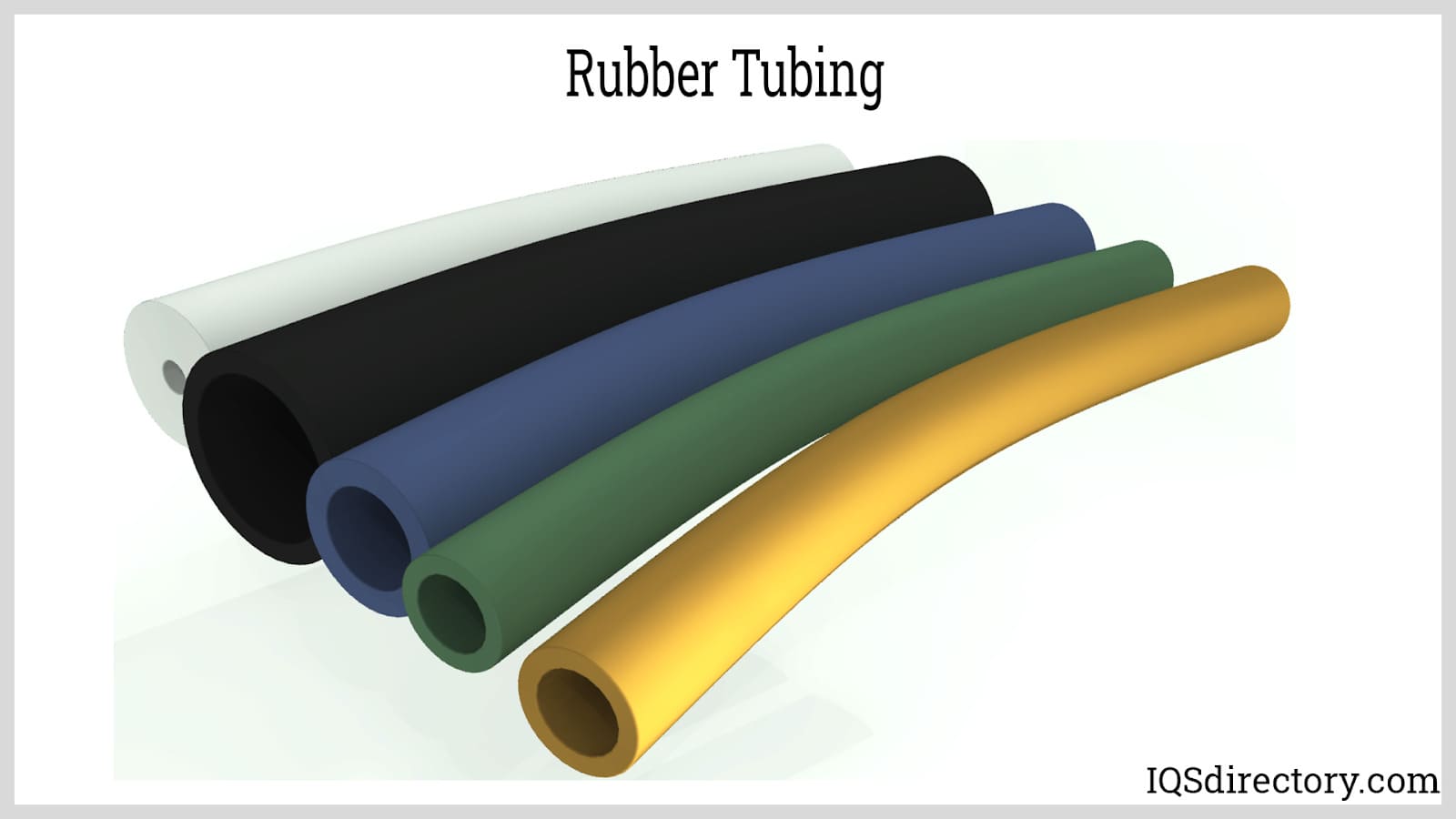
Rubber tubing is made of natural and synthetic rubber and is used to circulate and transport liquids and gases.
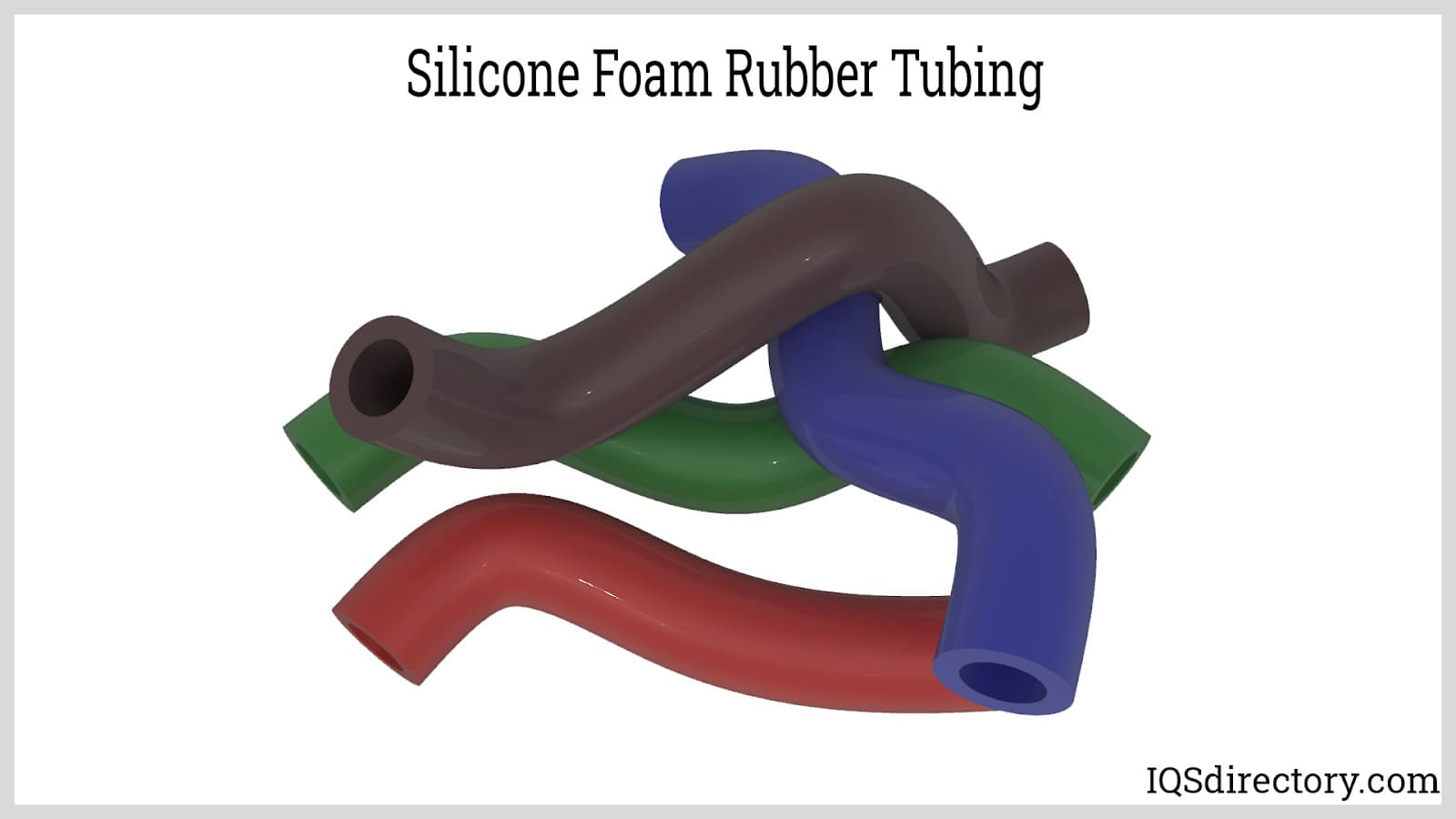
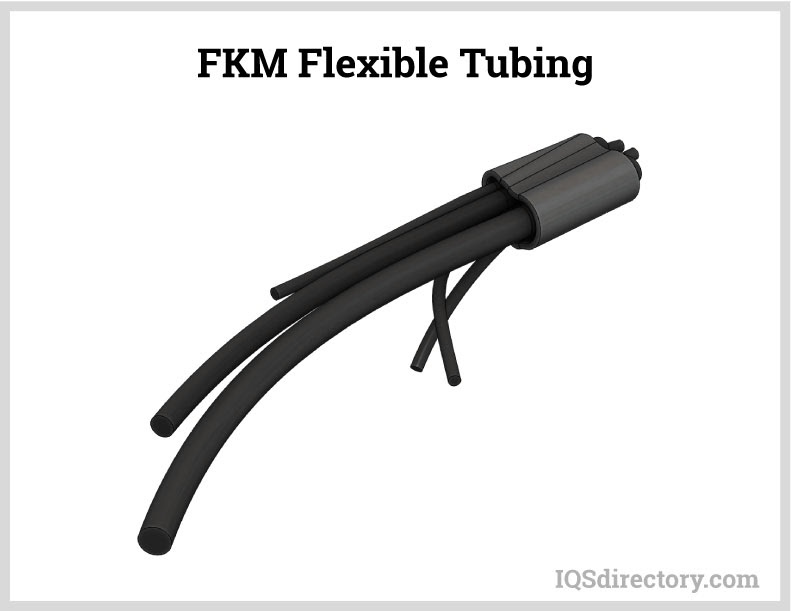
Fluoroelastomer rubber tubing is used for high temperature environments and is resistant to chemicals, oil, and heat above 200°C.
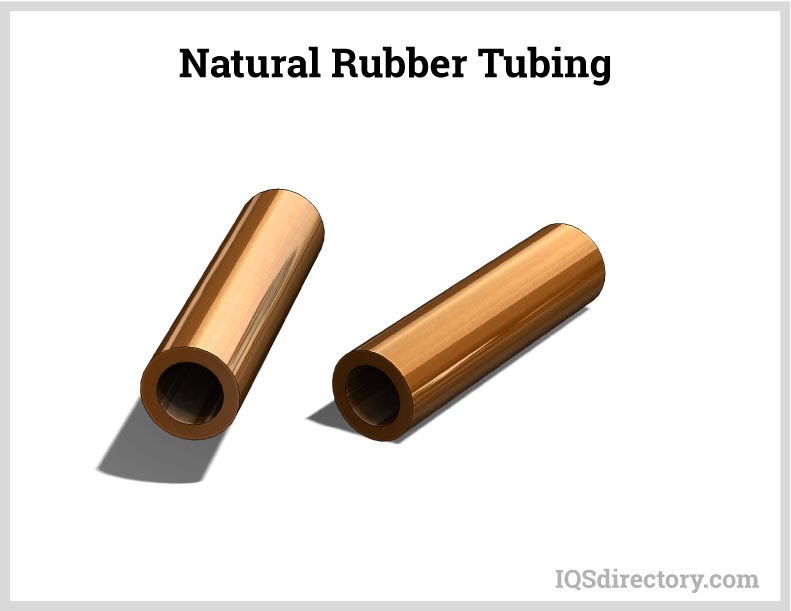
Natural rubber is very durable and flexible, which makes it usable in environments that require high strength, elongation, and tear strength.
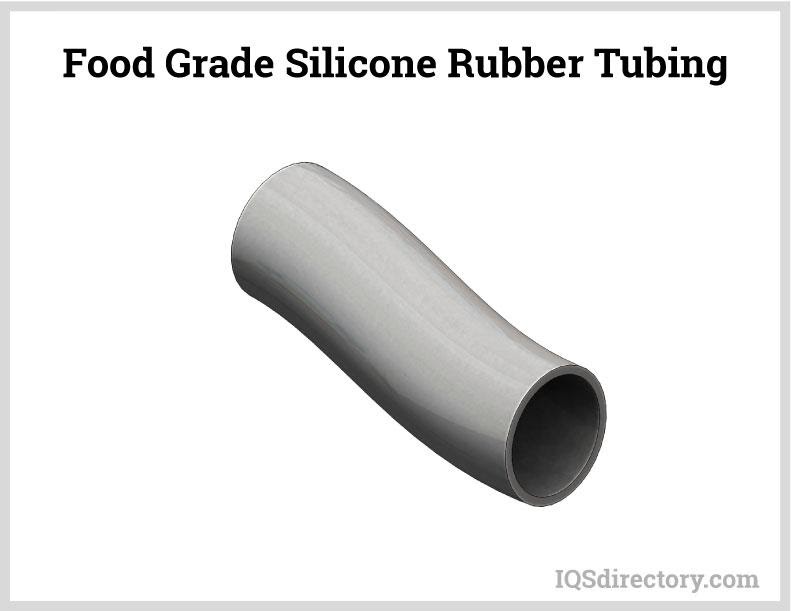
Rubber tubing for food processing is extremely critical and has to be manufactured to meet the rigorous standards set by the FDA.
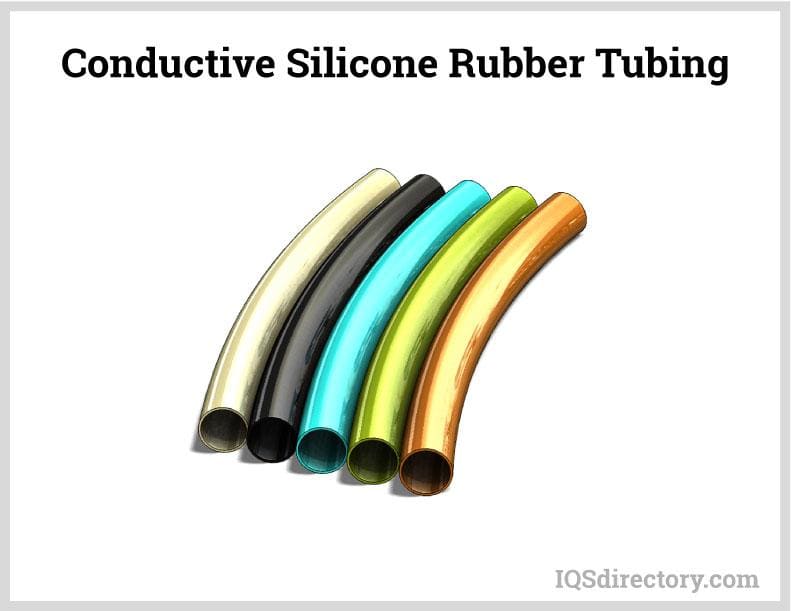
Conductive rubber tubing is used to control the static in electromagnetic interference (EMI) or radio frequency interference (RFI) shielding.
Types of Rubber Tubing
Latex Rubber Tubing
A naturally derived material known for its flexibility and chemical inertness, latex rubber tubing is commonly used in medical and laboratory settings. It serves as surgical tubing, rubber hose, and conductive tubing. However, due to latex allergies, alternative materials may be required for sensitive applications.
Thermoplastic Rubber Tubing
This material is highly durable, abrasion-resistant, and recyclable. It stretches without losing its shape, offering stiffness and flexibility for industrial and commercial uses.
Neoprene Tubing
Lightweight, stretchable, and resistant to chemicals, abrasion, and water, neoprene tubing is an excellent choice for applications requiring buoyancy and durability. It is also hypoallergenic, making it a safe alternative to latex.
PVC Tubing
One of the most versatile tubing options, PVC tubing is available in rigid or flexible forms. It can be transparent or colored and resists acids, alkalis, and various solvents, making it suitable for applications ranging from fluid transport to protective insulation.
Silicone Rubber Tubing
Derived from synthetic rubber, silicone tubing is smooth, pliable, and highly resistant to heat, water, and environmental factors. It remains flexible under extreme conditions and is commonly used in medical, food-grade, and industrial applications.
Viton Rubber Tubing
Made from a high-performance fluoroelastomer, Viton tubing withstands harsh chemicals and extreme temperatures better than most rubber materials, making it ideal for demanding industrial environments.
EPDM Tubing
A synthetic rubber composed of ethylene propylene diene monomers, EPDM tubing is frequently used in automotive and industrial applications due to its weather and chemical resistance.
Conductive Rubber Tubing
Designed to prevent static electricity buildup, conductive rubber tubing shields sensitive electronic equipment from electromagnetic or radio frequency interference. It is available in materials such as conductive latex and silicone.
Flexible Rubber Tubing
Ideal for applications requiring bending and contouring, flexible rubber tubing resists kinking and maintains its integrity even under repeated stretching or movement.
Surgical Tubing
A sterile, chemically inert material used in medical applications, surgical tubing has thin walls that allow for the free flow of liquids and gases.
Black Nitrile Rubber Tubing
Made from nitrile, this black rubber tubing absorbs heat efficiently while also providing insulation. It is resistant to acids, mineral oils, and vegetable oils, making it well-suited for automotive and industrial applications.
Hose Rubber Tubing
Often reinforced with thin metal wires or stiff rubber, hose rubber tubing retains its shape even when no fluid is flowing through it. It is widely used for industrial fluid and air transfer
Foam Tubing
Instead of transporting fluids, foam tubing provides cushioning, insulation, and improved grip for solid objects like tool handles. It comes in various colors and textures for comfort and durability.
Microbore Tubing
Designed for intravenous lines and delicate medical procedures, microbore tubing has strong walls that support fluid movement while minimizing patient discomfort. It is sterile, smooth, and chemically inert.
Gum Rubber Tubing
A naturally derived alternative to synthetic rubber, gum rubber tubing is flexible and provides a pathway for liquids and gases. It typically appears tan or white but can be colorized for specific applications.
Metal Rubber Tubing
An advanced material composed of polymers with metal ions, metal rubber tubing is flexible, self-assembling, and capable of withstanding extreme conditions. It is commonly used in aerospace and specialized industrial applications.
Things to Consider When Purchasing Rubber Tubing
Selecting the right rubber tubing is essential for ensuring system efficiency and longevity. With a wide range of options available, it’s important to consult an experienced supplier who can meet your specific requirements. Beyond product capabilities, consider the manufacturer's commitment to customer service. A supplier that fails to align with your timeline, budget, or operational needs may not be the best fit. Rather than making compromises, seek out a partner who can fully support your application.
Proper Care for Rubber Tubing
To maintain performance and prevent issues like leaks or contamination, rubber tubing requires proper care and handling.
Careful Handling
Rubber tubing is flexible but can be susceptible to damage if not handled properly. Even reinforced tubing with protective layers requires careful usage. Store tubing in a clean, dry environment, away from sharp objects or excessive heat, which could compromise its integrity. During use, only connect it with approved fittings and avoid applying pressure beyond its recommended capacity. Dragging tubing over rough surfaces, tying knots, or placing heavy objects on it can degrade its durability and lead to premature failure
Use the pipe for its purpose only
Always use rubber tubing for the specific application it was designed for. Exposing tubing to incompatible substances, such as using water tubing for chemical transport, can weaken its structure, cause leaks, or result in chemical contamination. If you need tubing for an alternative use, consult with the manufacturer to ensure you have the correct material for the job.
Routine Cleaning and Inspection
Establish a regular cleaning schedule to keep tubing in optimal condition. Clean it at least every six months or as recommended by the supplier. Use lukewarm, soapy water, rinse thoroughly, and allow it to dry completely before use. During cleaning, inspect the tubing for any leaks, cracks, or signs of wear. If significant damage is found, replace the tubing or use a properly sized connector to join sections. Don’t overlook fittings and grommets, as they also require regular maintenance.
Applications of Rubber Tubing
Rubber tubing is widely used in flow management systems for transporting liquids and gases. It plays a critical role in various industries, including construction, medical and healthcare, food and beverage processing, HVAC, petrochemical applications, and wastewater management. Whether for irrigation, industrial processes, or consumer applications, rubber tubing ensures efficient fluid movement and system performance.
Rubber Tubing Accessories
For proper functionality, rubber tubing requires compatible accessories such as fittings, industrial hose barbs, and rubber grommets. These components ensure secure connections to tools, instruments, or additional tubing, optimizing performance and reliability in any application.
Rubber Tubing Terms
Butyl
A highly flexible rubber known for its exceptional air retention, originally popularized in tire inner tubes.
Neoprene
A synthetic rubber prized for its versatility, offering resistance to sunlight, ozone, weather, oil, and chemicals. With a broad temperature tolerance and strong physical durability, it withstands burning, flexing, and twisting.
Nitrile
A durable rubber widely used in industrial and automotive applications. Known for its resistance to oil, fuel, and chemicals, it is commonly found in fuel and oil handling hoses, seals, and grommets.
Polysulfide
A synthetic rubber compound recognized for its superior resistance to water, oils, and various organic solvents.
SBR
Developed during World War II as an alternative to natural rubber, this synthetic rubber offers enhanced hardness and chemical resistance while maintaining the ability to be vulcanized..
More Rubber Tubing Information