Screw Machining
Screw machining, also known as Swiss screw machining, is a widely used manufacturing process for producing high-precision metal components. It utilizes screw machines, a specialized type of automatic lathe, known for their efficiency and ability to achieve high production volumes with exceptional accuracy.
The History of Screw Machining
Originating in Switzerland during the 1800s, screw machines were developed in response to the increasing demand for interchangeable, precision-engineered parts driven by industrialization. Switzerland, a hub for precision manufacturing at the time, was renowned for producing optical instruments, microscopes, measuring tools, and other finely crafted equipment. Swiss watchmakers played a key role in the early development of automated metalworking lathes, using rotary slides to manufacture intricate components with remarkable precision.
By the 1870s, innovations such as the collet chuck, which facilitated the use of bar stock, and advancements in headstock movement further refined screw machining capabilities. The mid-20th century saw the introduction of computer numerical control (CNC) screw machines, revolutionizing the process with enhanced automation and precision. Swiss-type CNC screw machines emerged in the 1970s, initially gaining traction in the semiconductor and electronics industries throughout the 1980s. As the technology advanced, its application expanded into medical, aerospace, and industrial sectors, solidifying its role as a cornerstone of modern precision manufacturing by the 1990s.
Advantages and Disadvantages of Screw Machining
Advantages of Screw Machining
Screw machining stands out as one of the fastest and most cost-effective methods for manufacturing small rotary parts. Its efficiency comes from CNC machining and turning equipment, which can machine multiple parts simultaneously—some machines handle up to six parts at once, with tooling areas capable of holding as many as 20 tools. This high level of productivity reduces cycle times, allowing manufacturers to produce large volumes of precision-machined parts quickly. By enabling a single operator to oversee multiple screw machines while also performing secondary operations, labor costs are significantly reduced. Without Swiss screw machining, many of today’s high-quality metal parts would be prohibitively expensive to produce on a large scale.
Beyond speed and efficiency, screw machining delivers design flexibility and structural precision unmatched by other metal fabrication methods. Few processes can rival its ability to meet tight tolerances, making it the preferred choice for intricate components such as specialty fasteners. While some metal stamping techniques can approach the precision of screw machining, applications that demand extreme accuracy—such as minute medical instruments—require the capabilities of Swiss screw machining.
Screw Machining Disadvantages
Despite its advantages, screw machining presents some challenges. One of the primary drawbacks is the setup time. Unlike manual lathes or non-CNC machines, multi-spindle CNC screw machines require extensive preparation, including part design and system programming with CAD software. Setting up a Swiss screw machine can take one to two hours, making it more cost-effective for long production runs. However, since screw machining does not require custom dies or hardware, even short runs remain a viable and economical option.
Another challenge is material waste. The process generates a significant amount of scrap—sometimes as much as a foot of leftover material per bar. While this is an inherent part of the process, manufacturers often implement material recovery and recycling strategies to minimize waste and optimize cost efficiency.
Overview of Screw Machining
Screw machining works with a wide range of materials, including steel, stainless steel, brass, aluminum, and titanium, which is commonly used for medical and sanitary applications. Even non-metal materials such as PTFE and nylon can be screw-machined. However, the final quality of any machined part ultimately depends on the integrity of the raw material.
A defining feature of Swiss screw machines is their ability to move the headstock, distinguishing them from traditional lathes. These machines shape parts by shaving down metal workpieces while disc cams rotate machining tools into position. The workpiece, held in place by a chucking collet, undergoes cutting, drilling, and finishing operations with remarkable precision. The machine motor
CNC Swiss machines take precision even further, often incorporating more tooling than their automatic counterparts. With more than eight spindles operating simultaneously—each programmed at different speeds—they process round, square, or hexagonal bar stock with extreme efficiency. A guide bushing stabilizes the stock as it enters the work bay, minimizing deflection and ensuring consistent accuracy throughout the machining process.
Applications and Products of Screw Machining
Screw machining produces an array of precision-turned components, commonly referred to as CNC turned parts. Specialty fasteners such as button machine screws, hex machine screws, and truss machine screws are widely manufactured using this method. Military applications also rely on screw-machined parts, including components for combat helmets and firearms.
Beyond fasteners, screw machining plays a crucial role in producing metal knobs, miniature medical instruments, bio-implants, tire gauges, threaded rods, splines, spindles, and custom metal parts requiring high precision. This process excels at manufacturing products that are either long and slender or small and complex, making it indispensable across multiple industries.
Once a screw machine has completed the tooling process, the resulting parts find applications in fields such as medical, automotive, laboratory, electronics, and military sectors. The ability to work with both common and exotic metals—as well as non-metal materials—underscores the versatility of Swiss screw machining and its critical role in modern manufacturing.
Screw Machining Images, Diagrams and Visual Concepts
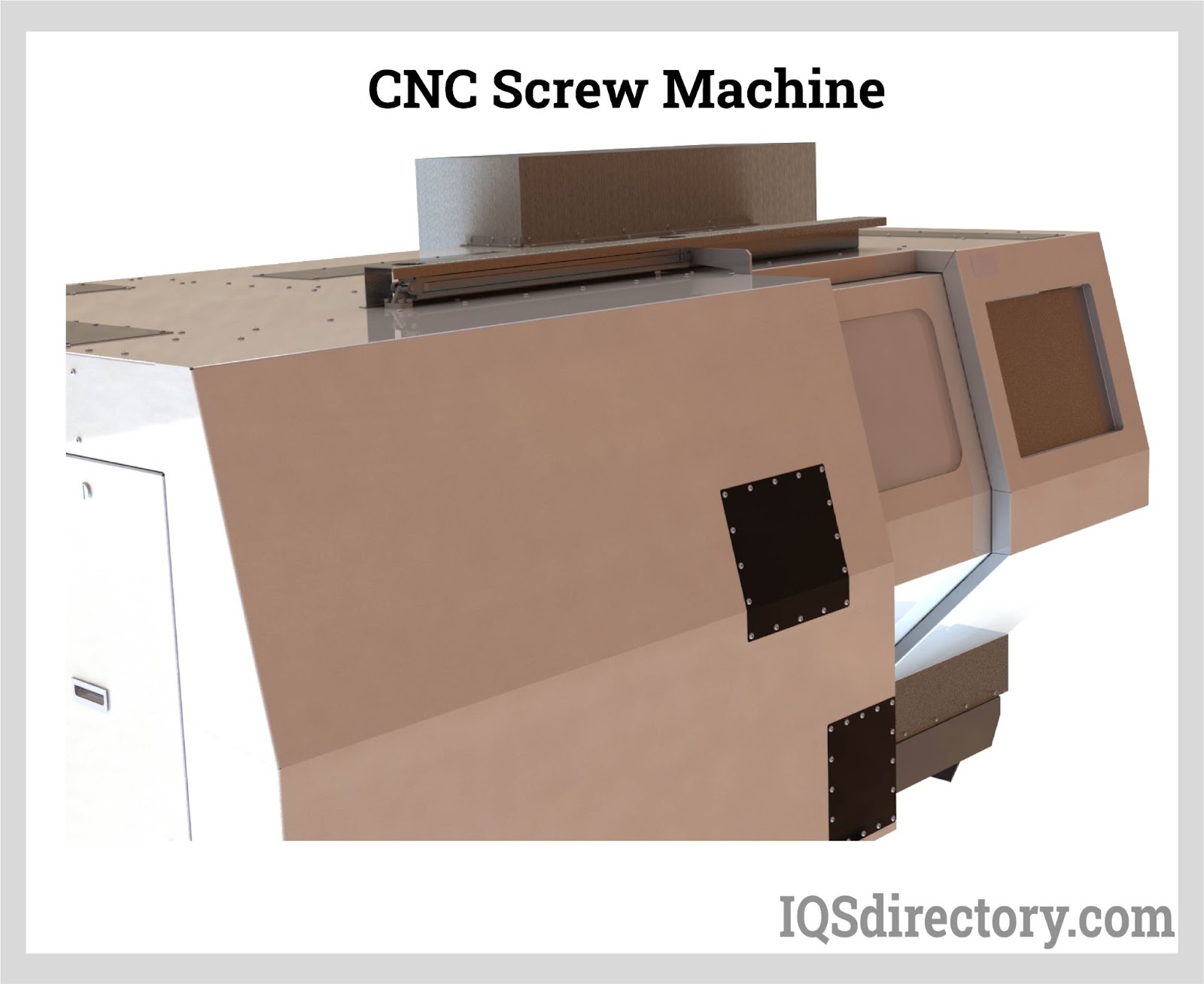
Carrying multiple spindles simultaneously and can manufacture up to six pieces at once for more consistent, intricate, and exact parts.
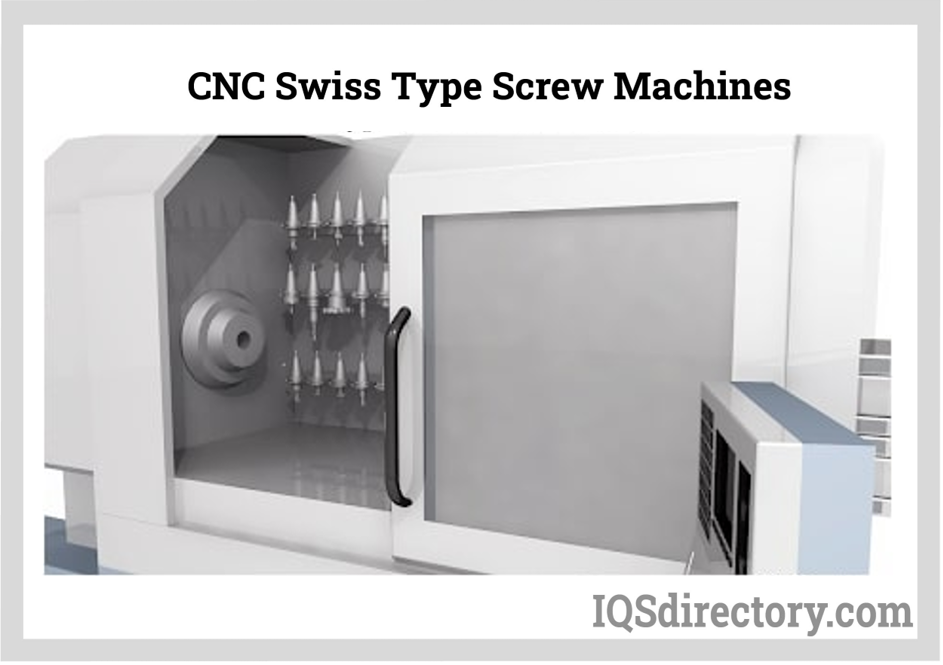
Swiss type screw machines effectively mass-produced screw machined goods because the metal bars stock moves using rotary slides.
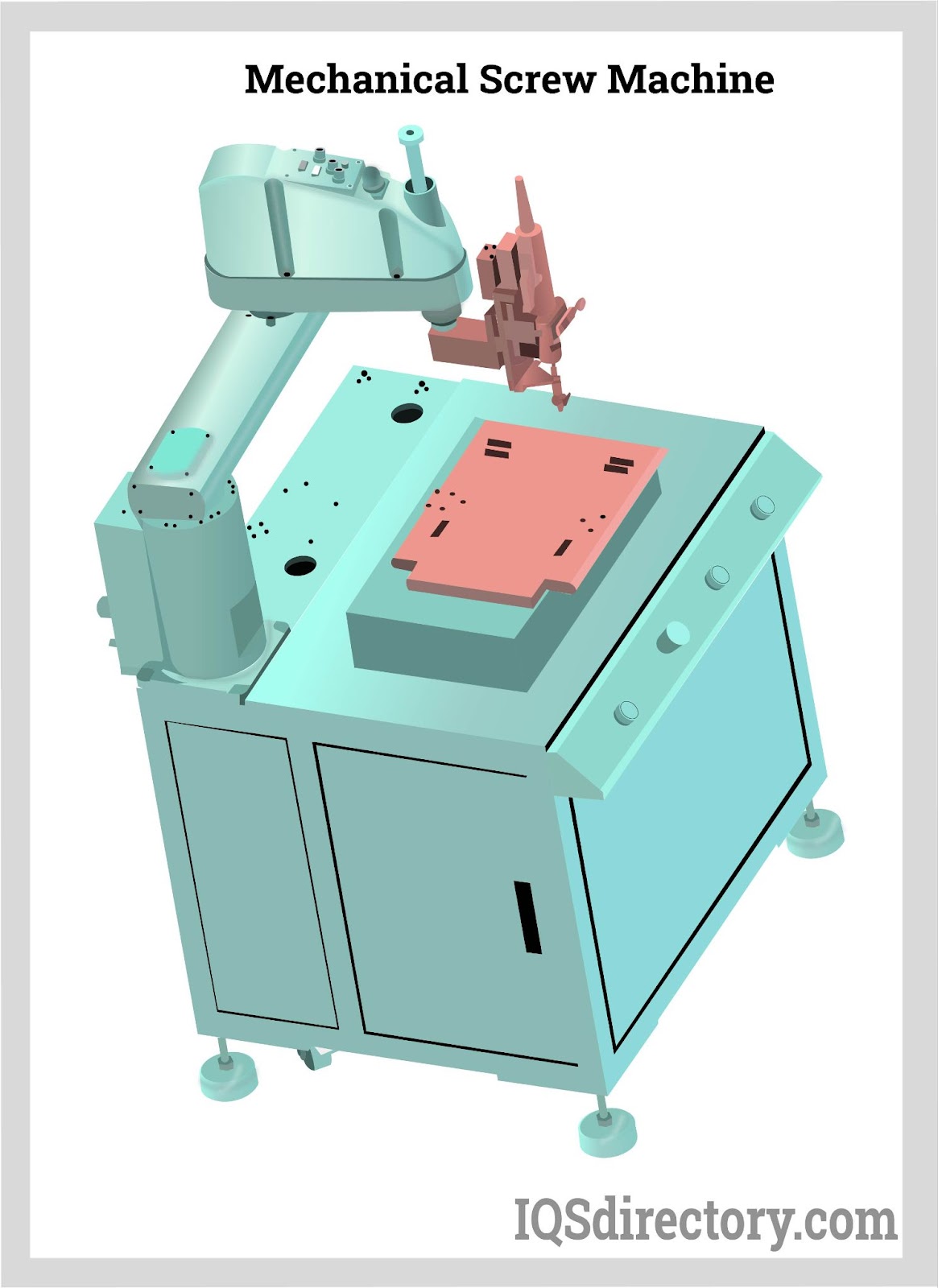
A screw machine which specializes in the creation precise medical components.
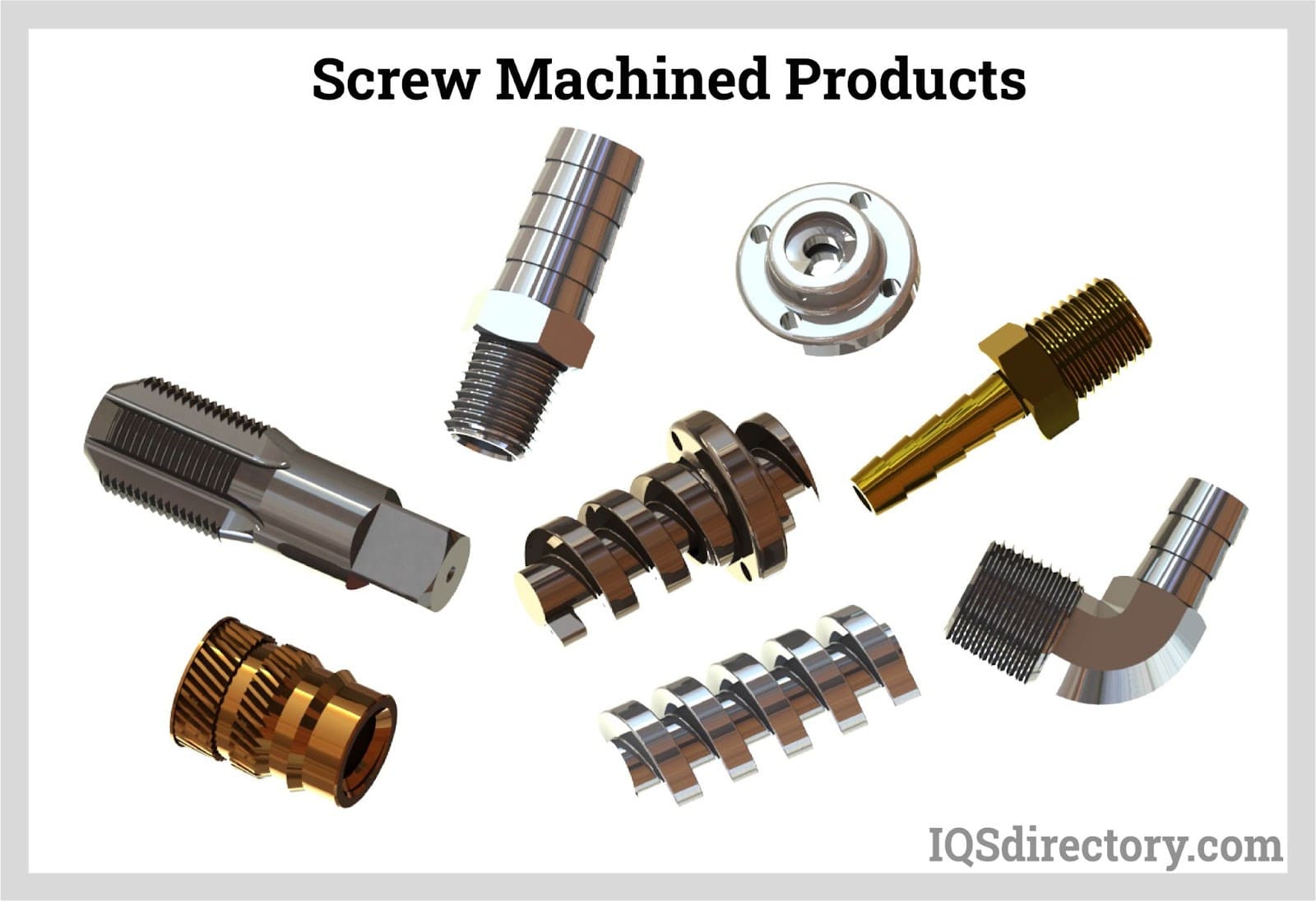
Screw machined products can be created a range of specialty fasteners and screws.
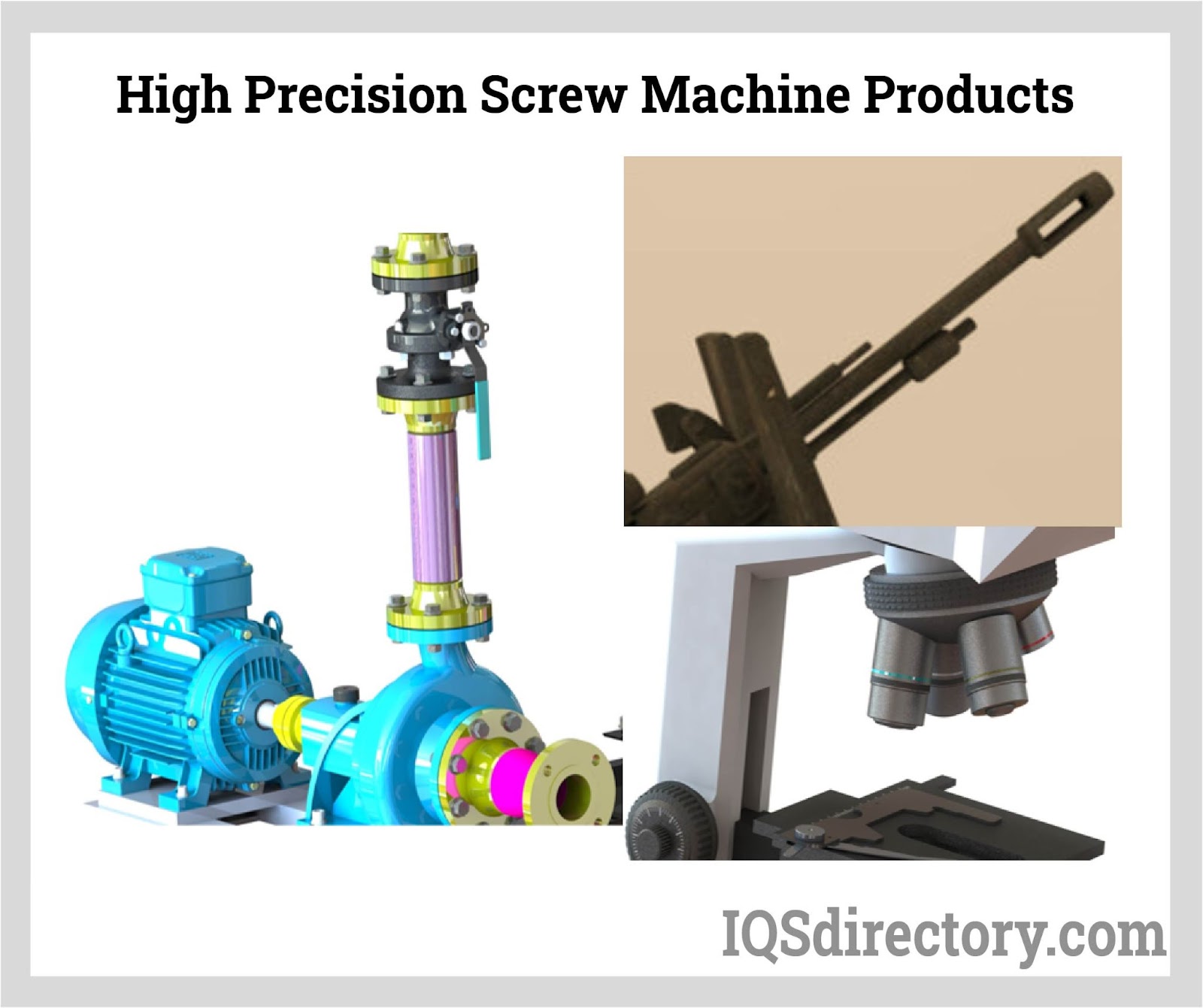
These are produced with incredibly tight tolerances, which is helpful for turning huge quantities of parts.
Screw Machining Processes
Different types of screw machines excel at various machining processes, each contributing to the precision and efficiency of metal component manufacturing. Among the most common processes are knurling, thread rolling, and surface finishing.
Knurling Process
Knurling creates a patterned texture on metal surfaces to enhance grip. This process is widely used for tool handles, metal flashlights, knurled nuts, and knobs. Using specialized CNC turning tools, precise knurled patterns are etched into the metal, ensuring consistency and durability.
Thread Rolling and Forming
Thread rolling and forming are essential for shaping screw heads and threading components. These cold-forming techniques press a shaped die against the workpiece to create threads without cutting into the material. Because these processes rely on compressive force at low temperatures, the metal must possess sufficient ductility to be formed without cracking.
Surfacing Metal Parts
Screw machining not only shapes metal parts but also enhances their surface quality. Turning operations can produce a smooth, near-polished finish or a knurled texture, depending on application needs. In advanced CNC Swiss screw machines with dual spindles, secondary operations can be performed automatically, reducing the need for manual intervention.
Equipment for Screw Machining
Screw machines are specialized, automated versions of metalworking lathes, designed to shape workpieces while they rotate around an axis. Unlike traditional lathes, screw machines often feature multiple spindles, making them ideal for high-volume production.
Screw machines are classified based on both physical orientation and control method.
Turret Type Machines
Turret screw machines use a vertical ram to feed the workpiece into the machine, making them well-suited for certain mass production applications.
Swiss Type Screw Machines
Swiss screw machines, originally distinguished by their rotary slides, offer superior precision and stability. They can be further categorized into automatic and CNC screw machines:
- Automatic Screw Machines – These early non-manual lathes operate mechanically using cams, levers, and clamps. While all screw machines are automated, the term "automatic screw machine" generally refers to these cam-driven systems.
- CNC Screw Machines – Controlled by pre-programmed computer systems, CNC screw machines offer advanced precision and repeatability, enabling complex machining sequences with minimal human oversight.
Modern screw machining continues to evolve, incorporating hybrid machines that blend the features of traditional automatic systems with CNC technology, further enhancing manufacturing capabilities
Screw Machine Products
High Precision Screw Machine Products
Designed to extremely tight tolerances, high-precision screw machined parts are ideal for large-scale production where consistency is critical. The use of high-grade metals and rigorous inspection processes ensures exceptional accuracy.
Medical Screw Machine Products
Precision screw machining plays a vital role in the medical, scientific, and pharmaceutical industries. These components include spinal implants, screws, and dental implants, all manufactured to meet stringent quality and safety standards.
Stainless Steel Screw Machine Parts
Known for their exceptional corrosion and chemical resistance, stainless steel screw machined parts are widely used in industrial applications exposed to extreme temperatures, moisture, and harsh chemicals.
With advancements in screw machining technology, manufacturers can produce highly precise, durable components for diverse industries, meeting the growing demand for efficiency and quality.
Things to Consider When Choosing Screw Machining
Selecting the right screw machining supplier requires careful evaluation to ensure they meet your specific needs. It's essential to invest time in finding a manufacturer with both the expertise and flexibility to provide tailored solutions. Key factors to assess include the origin and quality of screw-machined materials, the degree of product customization available, and the supplier’s ability to meet deadlines with reliable turnaround and shipping times.
For screw machining manufacturers, operational efficiency depends on strategic investments in machinery. Flexibility is often overlooked but remains critical in adapting to evolving technologies. As Swiss screw machining advances, investing in sophisticated CNC machines with multiple tooling options can provide long-term adaptability. This approach contrasts with a more rigid business strategy that ties growth to high production volumes. Generally, Swiss screw machines offer greater precision than turret screw machines, while CNC Swiss machines outperform automatic Swiss machines in both speed and accuracy.
Screw Machine Products Terms
- Acorn Die – A threading die with a cutting portion shaped like an acorn, used in screw machines.
- Broaching – A machining process that alters part surfaces by pushing or pulling a cutter (broach) through them, ideal for complex designs.
- Button Die – A small, adjustable die housed in a ring holder, used in screw machining.
- Cams – Components that control the automatic movement of slides and turrets to position cutting tools.
- Chuck – The lathe component that holds and rotates a workpiece for shaping.
- Collet – A specialized chuck that secures a turned part without causing surface defects.
- Cross Slide – A cam-driven slide that moves tools perpendicular to the spindle for precise feeding.
- Lathe – A tool used to rotate and shape a workpiece in screw machining.
- Mechanical Safety Clutch – A mechanism that disengages the main drive shaft to prevent damage in case of overload or jamming.
- Milling – A process that shaves layers from metal parts for precision machining.
- Precision Machine Screw – A slotted screw machined from bar stock, with cut threads and a machine-finished surface.
- Screw Stock – Free-machining alloy in wire or rod form, used for screw machine products.
- Spindle – A rotary shaft in a screw machine that rotates the workpiece.
- Turning – A machining process where a blank rotates against a stationary cutting tool to form parts.
- Turret – A cam-driven component that automatically positions tools for machining.
More Screw Machine Products Information