Springs
Springs are elastic components that store mechanical energy when at rest and resist forceful deformation. Spring manufacturers often use tempered steel, or stainless steel springs, made with chromium alloys, and are found in food service and medical applications as they are durable, contaminate resistant, and readily sterilized. Other metals, including copper, bronze, and titanium, as well as plastics may be used in the manufacture of custom springs.
Quick links to Springs Information
The History of Springs
Early History of Springs
For an item that is absolutely indispensable today, there is relatively little recorded history of springs. One of the earliest known uses was the Bronze Age invention of tweezers. They consisted of two strips of metal with a small plate brazed between them. Simple tongs and pincer pliers developed as metal forging techniques improved.
During the Iron Age, tensioned metal became more useful to man. King Tut used leaf springs on his carriages to smooth out the ride and increase their longevity.
Leonardo Da Vinci is credited with the design and manufacture of the first hammer spring for a gun in 1493. It allowed for a gun to be shot single handedly.
British physicist, Robert Hooke, discovered a principle of physics, in 1680, which states that the amount of force (F) required to extend or compress a spring by some distance (X) is linearly proportional to the distance, where the constant (k) represents its stiffness. When pressure is applied, the force developed is known as stress. Deformation as a result of the stress is known as strain. F = kX is the formula known as Hooke's Law.
Springs in the 18th Century and Beyond
The first coiled spring was invented by R. Tradwell in 1763. It was considered a great improvement over leaf springs because it required less maintenance. It took almost another century to develop steel coil springs, which found their use in chair seats.
In 1943, naval engineer Richard James accidentally discovered Slinky, the world's most famous coil spring. While working on the development of springs that could support ships' sensitive instruments and keep them stable in high seas, James knocked one of the coils off a shelf. He watched, fascinated, as it walked down a stack of books, across a table, onto the floor, then recoiled into a neat upright stack.
His wife, Betty, named it "Slinky" because of its smooth, graceful movement. It has been sold as an inexpensive child's toy for over six decades. Slinkys have been used as musical instruments, radio antennas, and in anti-gravity experiments. They are also used as teaching tools because of their ability to simulate waves.
Spring Design
Spring manufacturing begins with the designing process. Attention must be given to appropriate material with regard to shear modulus and tensile strength of the wire to be used. Working tolerances must be considered when placing springs into components as spring diameters change when loads are applied. Compression springs increase in diameter as compression is applied. Extension springs decrease in diameter when under force. Diameters of torsion springs will increase or decrease under force depending on the direction of winding versus direction of torsion.
Designing springs for manufacture should be based on physical dimension, spring rate, and expected loads of the finished product. Wire used for winding the spring helical should be the appropriate size and substance. The number of active coils must be calculated to achieve adequate load handling capabilities. Thought must also be given to any special tooling that may be necessary to complete the manufacture of the product. Coatings or surface treatments of the wire are options to be considered. They may offer colored outer surfaces, corrosion prevention, wear resistance, or surface hardening qualities to the wire spring metal. Special packaging requirements for long, thin, or slinky springs must be provided so they do not sustain damage in transport.
Spring Images, Diagrams and Visual Concepts
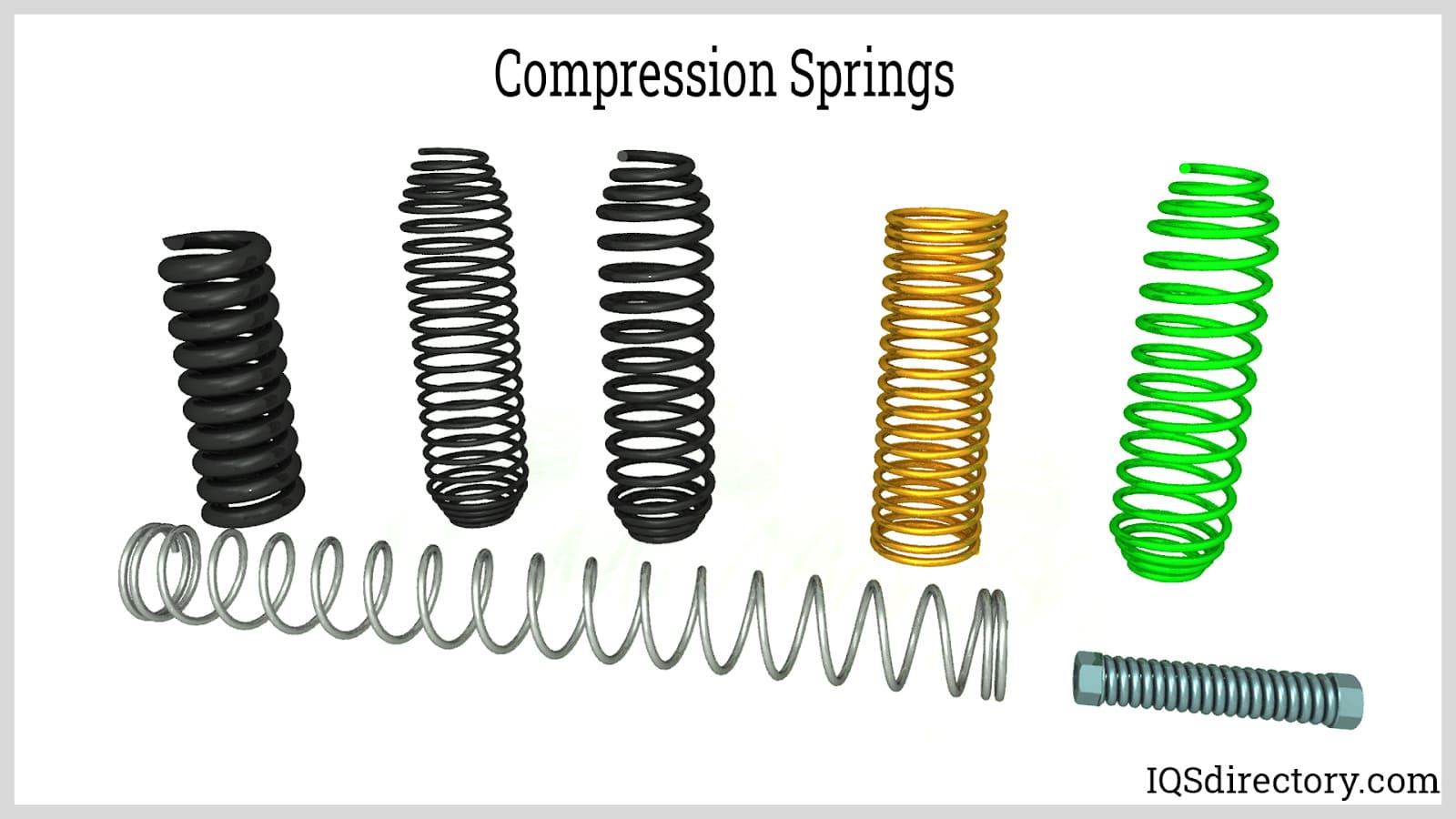
Springs are flexible machine elements which stores mechanical energy when subjected to tensile, compressive, bending, or torsional forces.
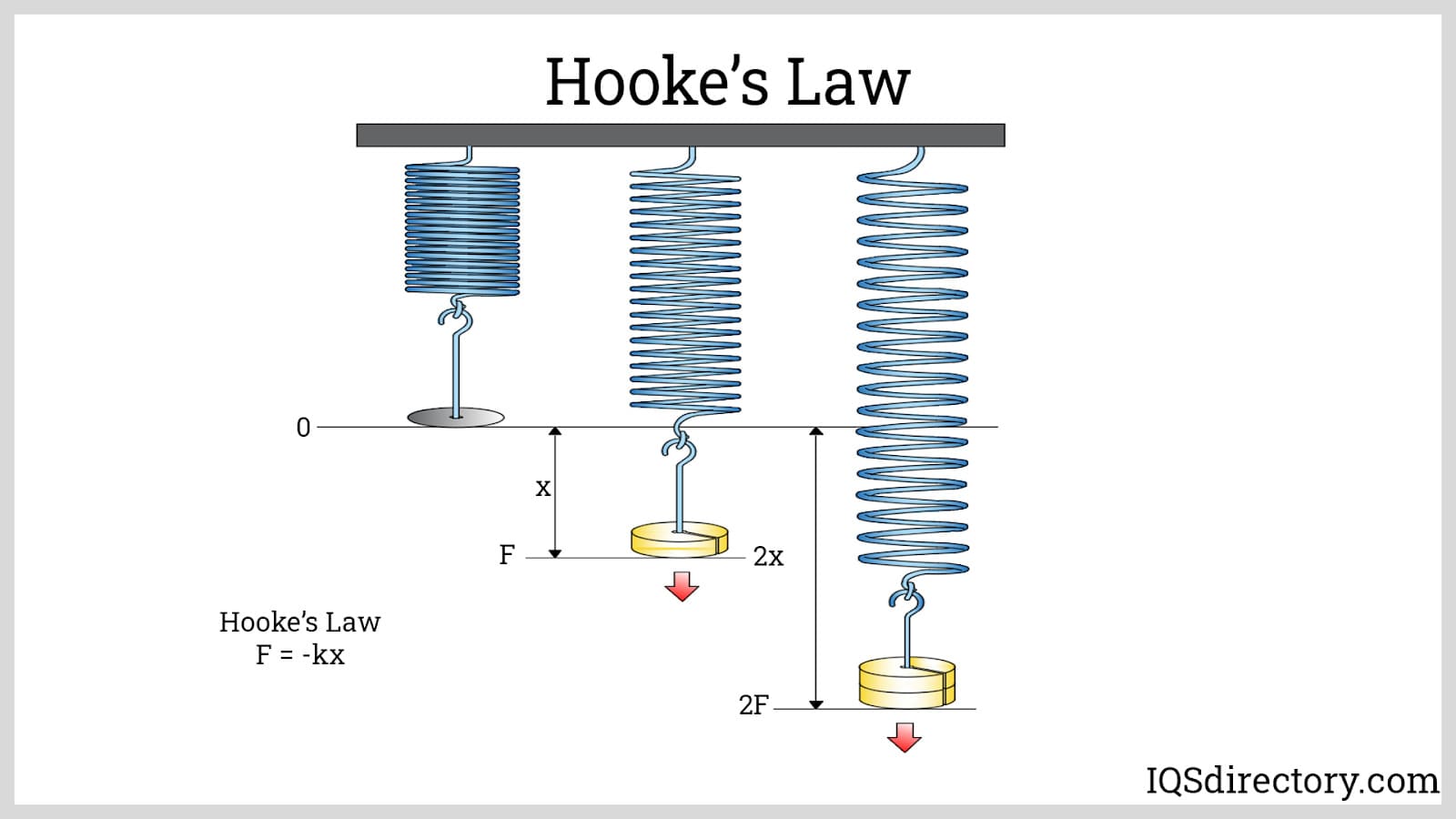
Hooke‘s law is a behavioral model for springs whichs states that force applied to a spring is directly proportional to its deflection, if within the elastic range of the spring.
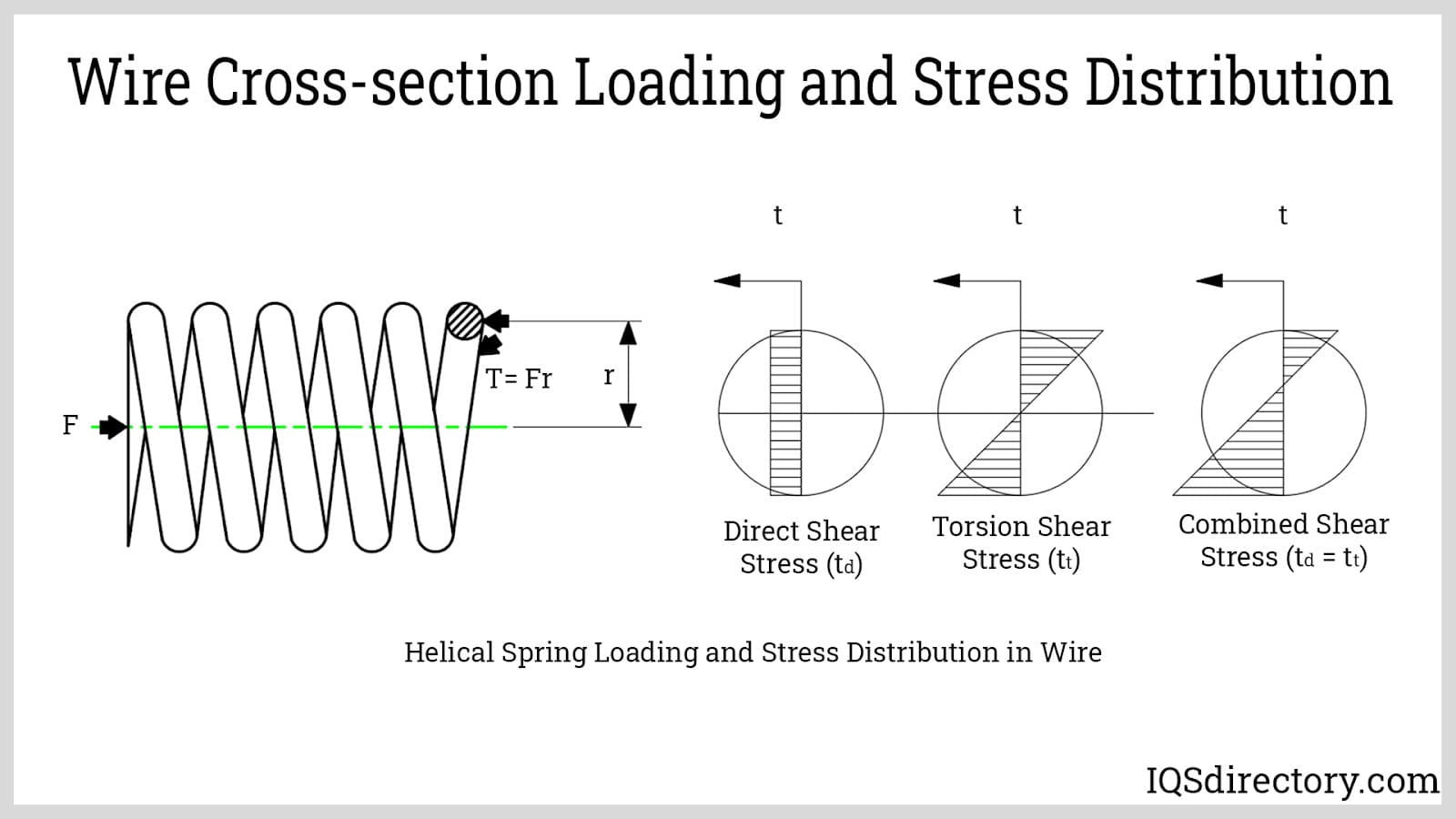
The design of springs usage must determine the maximum stress on the spring which calculated with the Wahl correction factor.
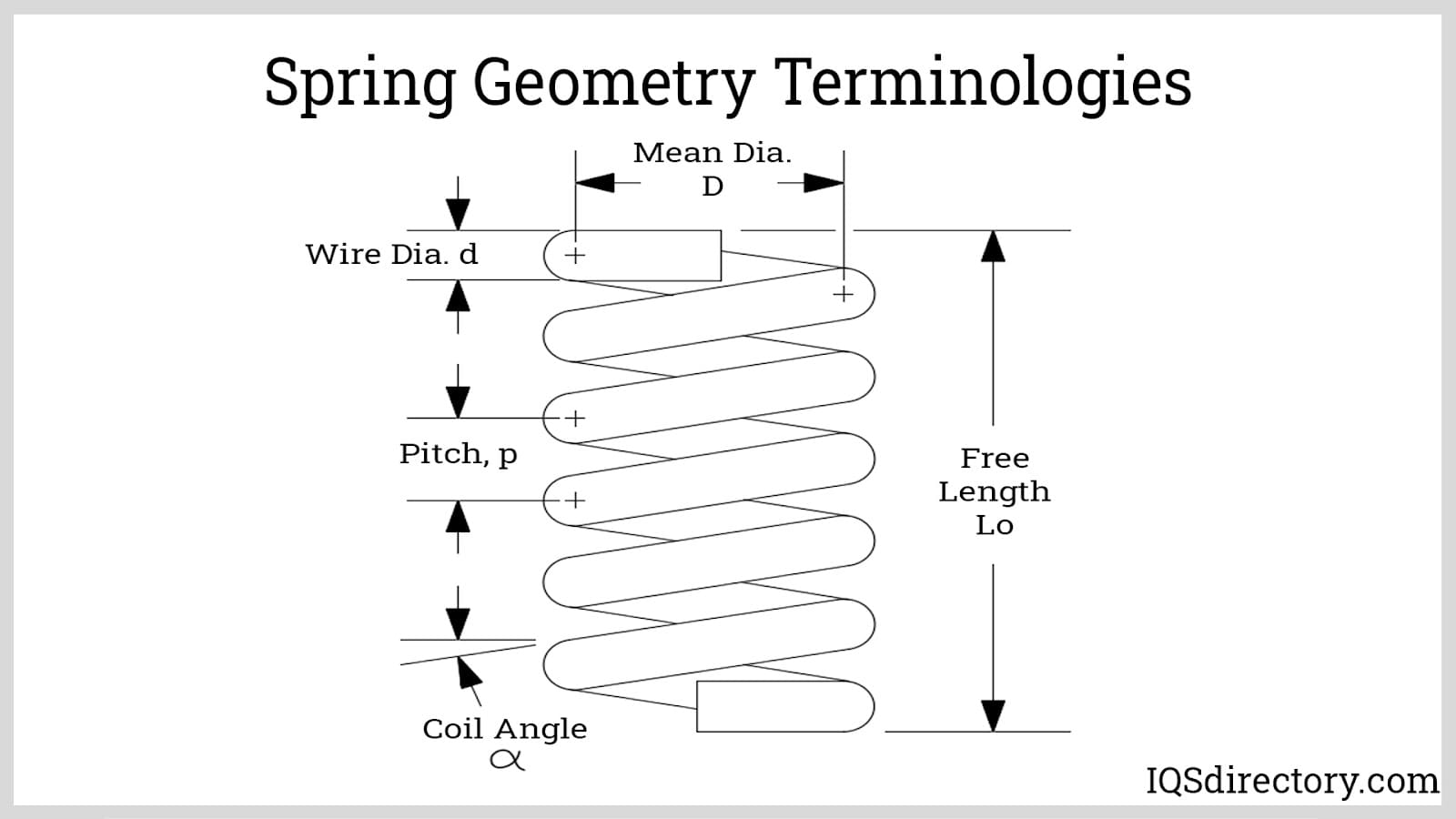
The design of the springs are determined by wire dimensions, coil length, coil pitch, and coil angle.
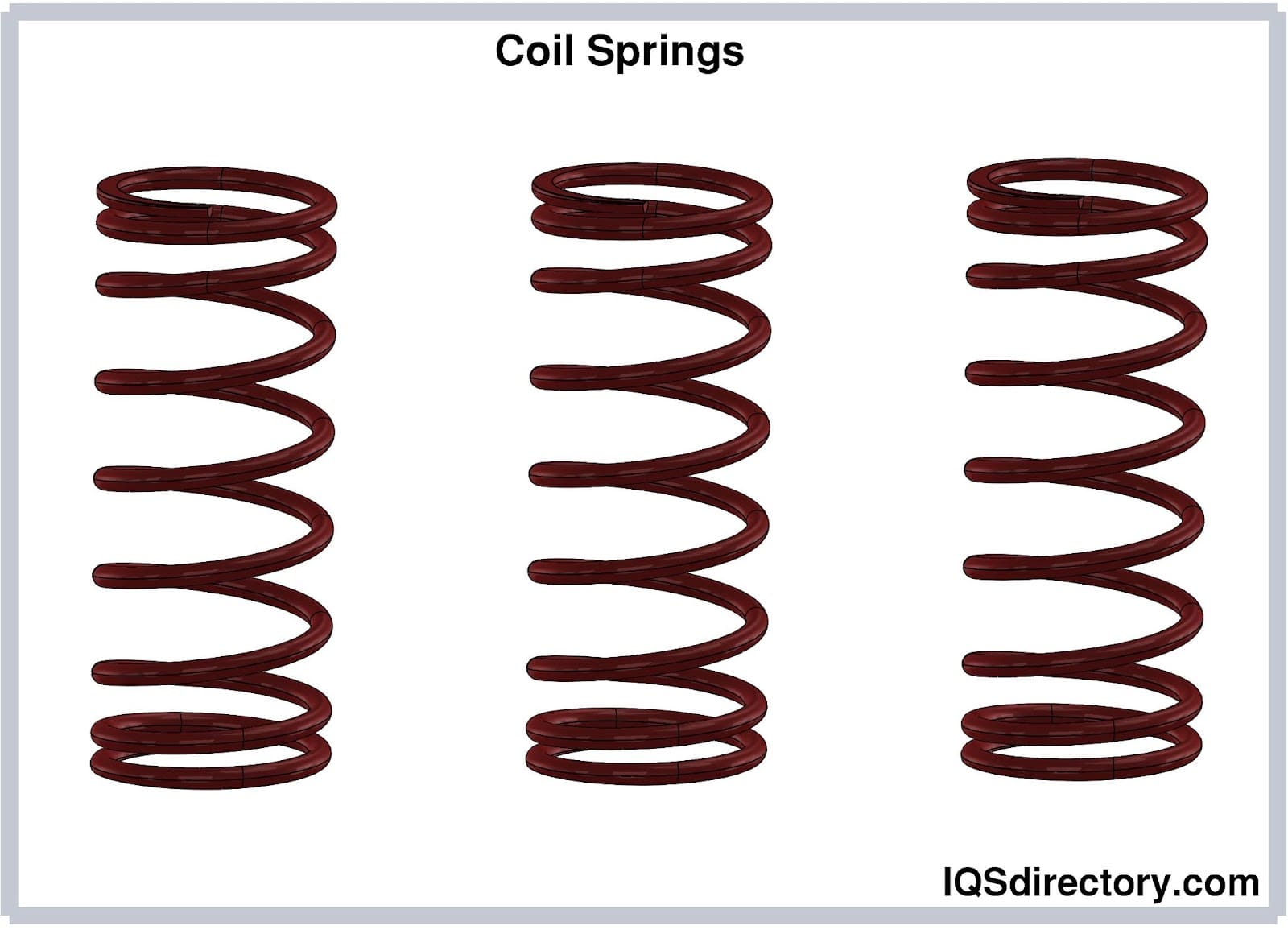
A coil spring is an elastic element in the form of curls made from round wire and wrapped around a cylinder.
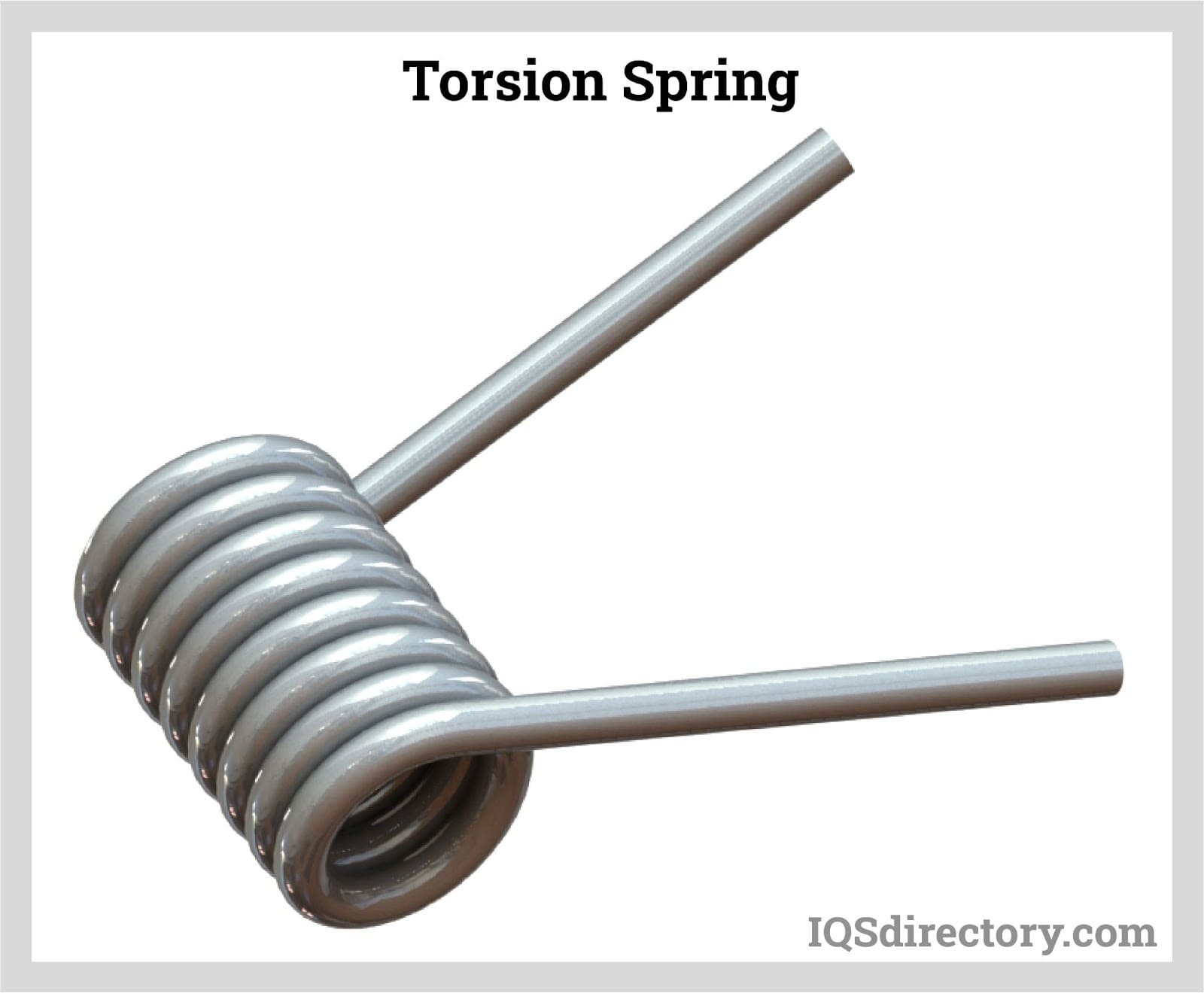
Torsion springs produce mechanical energy by storing the resistance and exerts torque opposite to the twisting force proportional to the twisted angle.
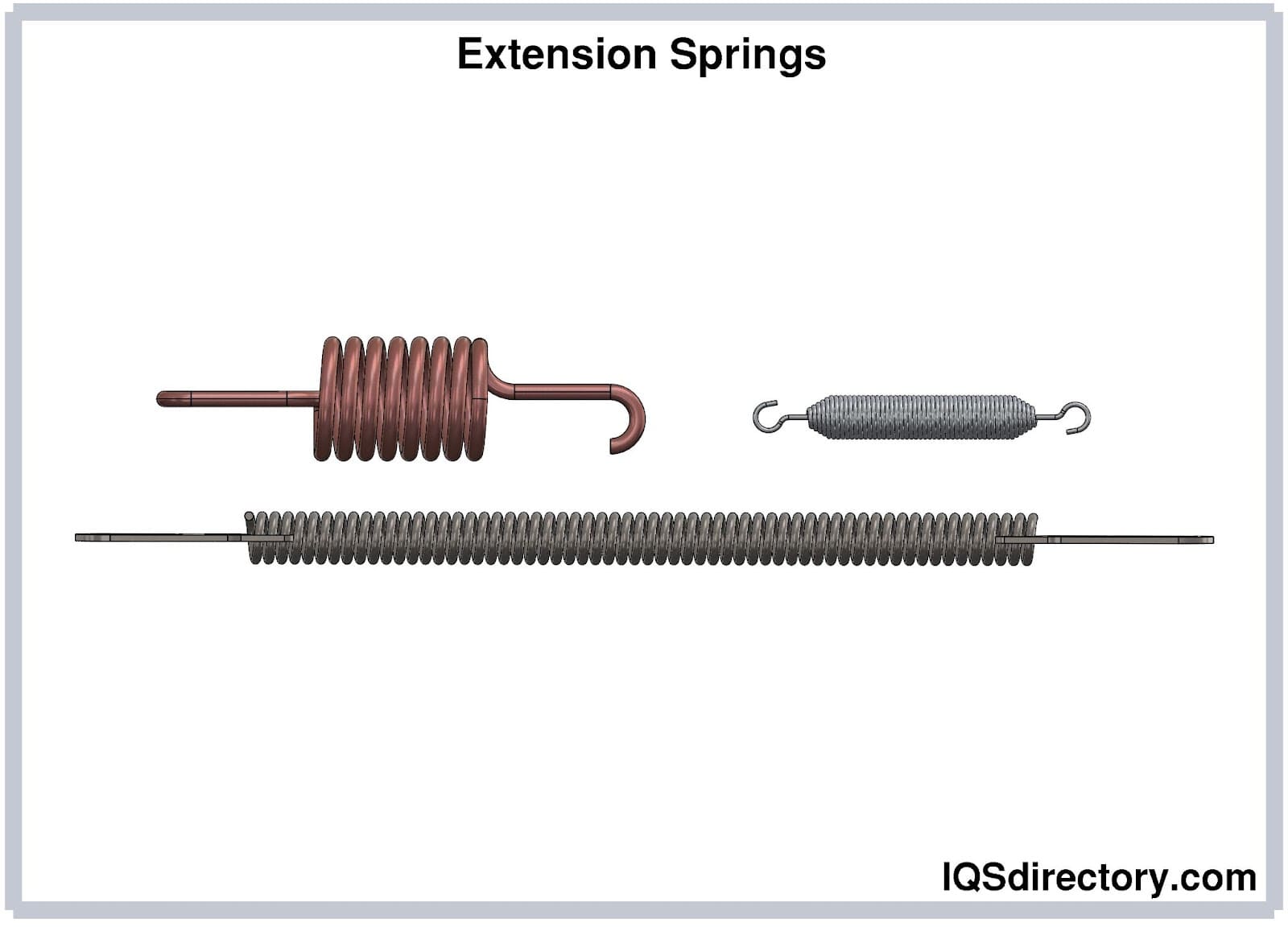
Extension springs are helical wound up so closely together to create initial tension in the coils, which can absorb and store energy.
Spring Types
Springs are manufactured in many shapes and all sizes. While springs can be made from a wide range of metals, cold rolled spring steel is often used to form the wire into springs. Spring steel is a medium carbon steel with high yield strength, known for its excellent elastic properties. It is specifically made for spring fabrication. Flat springs and coil springs are the two basic types of spring.
Small Springs
Components of machines and equipment that are made of very thin, tightly wound wire. They measure between 0.0036 and 0.187 inches thick, and smaller springs are always in development.
Spiral Springs
A unique type of flat spring that can be made out of various metal materials and is bent into loops that form a spiral. Unlike a coil spring where the loops gradually go upwards, creating a spring that exerts vertical force; the loops of a spiral spring are all flat and wrap around each other, generating horizontal force when they are compressed.
Steel Springs
Broadly references any type of spring made from any type of steel. In turn, the term "springs" references elastic members of machinery, devices and systems that exert a resisting force when their shape is changed.
Tension Springs
A tightly wound metal coil that is designed to operate with tension. The spring stretches to a particular length as force is applied to it. Imagine a screen door being opened and then slamming shut as soon as you take your hand off and stop applying force to it.
Trampoline Springs
Enable people to jump higher than they ever could on solid ground. This ability is even used on a professional level among gymnasts who need trampolines to help them perform incredible maneuvers in the air. The strong, elastic fabric of a trampoline, combined with the many springs that support it, make the creation of this kind of upward momentum possible.
Flat Springs
Made from metal that is flattened, curved, and tempered to offer resistance or shock absorbance, are used in many ways. They may be simple securing devices, clips, clamps, or tongs. Flat springs may be used as battery contacts. Layered and bound together as leaf springs, they provide shock absorption for transport vehicles.
Clock Springs
Or power springs, are helically wound springs that are naturally inclined to expand; the expansion generates torque, or circular movement. However, once the expansion occurs and the spiral length has run out, the clock spring must be rewound.
Leaf Spring
Are made from arc shaped lengths of spring steel, typically fitted with a loop or eye on each end for attaching to the chassis of a vehicle. The arcs may be elliptical or parabolic. The spring may be single leaf, but is usually stacked in multiple layers that decrease progressively in length. The layers are secured at the center and at strategic intervals along the length, to provide tension against the compression caused by bouncing on bumpy roads. The axle is located at the center of the arc, providing the maximum absorption of shock.
Coil Springs
Formed by helical winding spring wire around a cylinder, barrel, or core. The wire may be flat or square shaped in profile, but is normally round. Wire used in the manufacture of helical springs may be microscopically fine or have a thick diameter to offer stronger compression or torsion resistance. Music wire is high tensile, high carbon steel wire that has been cold drawn through a die and then heat tempered for strength. Music, or piano wire, has no twist and is able to take the stress and strain of repeated heavy loads without losing its consistency. The inherent qualities of the material used for the wire, in conjunction with the type of winding, will determine spring rate, the amount of force required to create specified deflection. Coil springs may be categorized as compression springs, extension springs, torsion springs, or constant force springs.
Compression Springs
Resistant to compressive forces. They are at rest when extended, so as compression force is applied, they will push back. Coils are counted from tip to tip of the helix. The number of active coils determines the amount of compression that may be deflected. The active coils of a spring are any portion of the spring that stores and releases energy. How the ends of the coil are finished determines whether the ends are fully active coils, half inactive coils, or inactive coils. This is important to know when designing springs to ensure correct compression resistance. Compression springs may be hourglass shaped, barrel shaped, or may be uniformly cylindrical, with or without reduced ends. Industrial stamping presses and spring hammers use compression of a giant spring to increase the power stroke of the hammer head. Firing pins for guns include a tiny compression spring. Compression springs are commonly found in electrical contacts, mattresses, seating, shock absorbers, and ballpoint pens.
Metal Springs
Can be constructed of a wide range of metals, depending on the particular application of the spring. Metal springs are ideal for use in marine, petrochemical, pharmaceutical, medical and in many other contexts. Metal springs can be involved in major or minor ways in alarms, aviation, circuit breakers, electronics, furniture, hardware, instruments and gauges, office/business machines, solenoid valves and writing instruments as well as a wide variety of other industrial, commercial and consumer products.
Conical Springs
Sometimes referred to as tapered springs because of their shape. The tapered, cone shape provides a nearly constant spring rate under compression. The tapered coils nest inside each other providing a flat profile when under maximum spring compression. They also offer less load deflection providing greater stability. Conical springs are commonly manufactured from stainless steel or copper for heat and corrosion resistance in electrical settings as they are often used as electrical contacts and in push buttons.
Extension Springs
Resistant to stretching forces. Initial tension refers to how tightly the wire coils are wound and represents the load necessary to start the spread of coils. They are at rest when retracted. As pulling force is applied, the initial tension is deformed and the spring will attempt to return to its zero-deflection state. Extension springs are normally cylindrical with hooks or loops at each end for interfacing with components. All coils in an extension spring are considered active coils. Spring extension refers to the distance a given spring will stretch under specified pulling force. Examples of extension springs are found in garage doors, door closers, vise grips, trampolines, automotive interiors, and carburetors.
Torsion Springs
Store rotational energy or torque. They are closely wound helical springs that store and release angular energy and resist torsion, or twisting force. The wire winding may be pitched to reduce friction. Torsion springs may be wound clockwise or counter-clockwise to suit the application. Loads should always be applied in the rotational direction of the winding. Torsion springs are generally used with a center shaft or mandrel for support. The ends are attached to components which rotate around the center point of the spring. As torque is applied, the spring resists creating spring torsion. Some examples of torsion springs are found in clipboards, mouse traps, clothespins, tailgate assemblies, industrial spring hinges, and ratchets. Often torsion springs are also referred to as spring springs or spiral torsion.
Constant Force Springs
Are actually hybrid springs. They are made by helical winding of a flat strip of spring steel that has been pre-stressed to retain its tension. The strips are wound around the core in constant radius coils. When the strip is extended, it resists the loading force and tries to recoil at a constant rate. Wind-up timers and some actuator dials are made with constant force springs that create double torsion when being wound up and then winding down. Some common examples of a constant force spring can be found in seat belts, thermostats, retractable tape measures, dog leashes, and hose reels.
Applications of Springs
From the paperclip to complex electronic lock systems, springs are found in a wide range of places around the home, in all industries, and in nearly all factors of transportation. A custom spring can be designed to suit any specific purpose, from precision springs in micro-electro-mechanical systems (MEMS), medical devices, and Nano-technology, to industrial springs that provide earthquake-proof foundations for high-rise buildings.
Although springs employ very simple, mechanical principles, their function within equipment and machinery across consumer and manufacturing industries is extensive and nuanced. Springs, such as constant force springs, can provide kinetic energy to other pieces of equipment without any external power source. Compression and leaf springs provide essential shock absorption in suspension transportation applications, while extension and torsion springs provide doors, windows and many types of equipment with necessary resistance. As metalworking and heat-treating technologies have improved, spring manufacturing has improved as well, turning out springs with more durable elasticity and greater load resistance. All springs are defined as devices that store potential energy by using an elastic material. The potential energy is at a minimum when the spring is at its relaxed length. Carefully pairing a spring with its intended application will help to ensure the spring's effectiveness and longevity.
Things to Consider When Purchasing Springs
Springs have such a vast array of purposes and styles, it is impossible to pinpoint what is the "best" design. The perfect design for the application is only limited by the imagination of the inventor. The benefits and advantages must be determined through consideration of materials and functional demands of the device. Any situation where mechanical forces need to be resisted mechanically can be addressed through the use of springs of some kind.
Concern should be given to issues regarding fatigue and stability, as metal under stress and strain will eventually wear out. Since springs are generally metal pieces designed to exist under stress, be sure to find the best metal or alloy to withstand those forces over time. Because springs are ruled by laws of physics, standardized formulas exist for manufacture of every spring type imaginable.
Good spring manufacturers will have trained design staff available to help design custom springs that meet ASTM, AISI, and SAE working and safety standards. A designer should be able to guide the client through the process to create the appropriate spring device for the intended purpose.
From children's bobble head toys to highly technical watches and clocks, complex systems of simple springs keep things ticking along.
Springs Terms
Active Coils
Coils that are free to deflect under load.
Arbor
Also called a "mandrel," it is the round, hardened shaft about which springs are wound.
Closed Ends
Ends of compression springs in which the pitch of the coil ends is reduced to the degree that the end coils touch.
Close-Wound
Referring to the coiling of a spring so that its adjacent coils are touching.
Coil
A round shape formed by a series of concentric circles.
Deflection (F)
Motion of spring ends or arms under the application or removal of an external load (P).
Free Angle
Angle between the arms of a torsion spring when the spring is not loaded.
Free Length (L)
The overall length of a spring in the unloaded position.
Frequency
The lowest inherent rate of free vibration of a spring itself, typically expressed in cycles per second, with ends restrained.
Helix
The spiral form (open or closed) of compression, extension and torsion springs.
Hooke's Law
Load is proportional to displacement. Most springs obey this law.
Hooks
Open loops or ends of extension springs.
Hysteresis
The loss of mechanical energy during the cyclic loading and unloading of a spring.
Lathe
A machine that rotates stock against which other tooling is brought to bear. Lathes are used to wind springs.
Load (P)
The force applied to a spring that causes a deflection (F).
Loops
Coil-like wire shapes at the ends of extension springs that provide for attachment and force application.
Pitch (p)
Also referred to as "coils per inch," it is the distance from center to center of the wire in adjacent active coils.
Rate (R)
Change in load per unit deflection, generally given in pounds per inch (N/mm).
Shot Peening
A cold-working process in which a metal surface is impacted with a high-velocity stream of metal shot or glass beads. Shot peening is used for cleaning or improving resistance to stress corrosion by producing a compressive stress.
Spring Index
Ratio of mean coil diameter (D) to wire diameter (d).
Stress Relieve
To heat treat springs under low temperatures in order to relieve residual stresses.
Torque (M)
A twisting action in torsion springs that tends to produce rotation, equal to the load multiplied by the distance (or moment arm) from the load to the axis of the spring body.
Torsion
A twisting force that can result in shear stresses and strains.
More Springs Information
Spring Informational Video