Vacuum Forming
Vacuum forming is a basic thermoforming process in which a plastic sheet is heated to a pliable temperature, shaped over a mold, and formed using vacuum pressure. Once the plastic conforms to the mold's surface, it is cooled and released using reverse pressure. This method is commonly employed to transform plastic sheets into various objects.
To facilitate easy removal of the formed plastic, draft angles are incorporated into the mold design. Additionally, mechanically or pneumatically pre-stretching the plastic sheet before vacuum application allows for adjustments in the depth of the formed parts. Typically, thermoplastics are the preferred materials for vacuum forming due to their moldable properties.
History of the Vacuum Forming Process
The origins of vacuum forming trace back to the 1860s when John Wesley Hyatt discovered celluloid, the first artificial plastic. Along with his brother, he patented this innovative material, which could be heated and molded into various shapes such as sheets and rods.
However, centuries earlier, the Romans were shaping tortoise shells containing keratin into utensils using hot oil. This process, involving heat forming, can be considered an early example of thermoforming.
In the 20th century, thermoforming as we know it began to take shape, evolving from heating plastics and forming them over molds. By the 1940s and 1950s, vacuum-formed plastics emerged, initially used for display and marketing tools. In 1950, a machine for molding articles from thin plastic sheets was patented. By 1964, this technology had been refined, and a machine specifically for plastic sheet vacuum forming was perfected and patented. The following decades saw continuous advancements in vacuum forming, culminating in the sophisticated methods we use today.
Benefits of Vacuum Forming
Vacuum forming has become widely popular due to its numerous advantages:
- Precision: Products created through vacuum forming are highly accurate to design specifications. The process ensures that a single heated sheet conforms exactly to the desired shape.
- Cost-Effectiveness: Vacuum forming is economical, as it requires inexpensive materials, low pressures, and less intricate tools. The ability to produce items from a single plastic sheet further reduces costs, and recycling materials enhances affordability.
- Versatility: The process accommodates a wide range of unique designs and shapes, offering great flexibility.
- Quick Turnaround Time: This allows businesses to save time for other operations, improving efficiency and profitability.
Steps of the Vacuum Forming Process
Vacuum forming involves several key steps:
1. Clamping
The plastic sheet is securely held in place by a robust frame, capable of accommodating even the thickest plastics.
2. Heating
Infrared heaters, typically mounted on aluminum plates, evenly heat the plastic sheet to its optimal forming temperature. Advanced systems may use quartz heaters for faster response times and pyrometers for precise temperature control.
3. Sheet Leveling
In some machines, a photo-electric beam ensures the plastic sheet remains level. If the sheet sags and breaks the beam, air is injected to lift it back into position.
4. Pre-Stretching (Bubble)
Pre-stretching occurs when the plastic reaches its forming temperature, creating an even wall thickness before vacuum application. Machines equipped with this feature ensure consistent results by controlling the bubble height.
5. Vacuum Application
The vacuum pumps removes air trapped between the mold and the plastic sheet, enabling the sheet to conform to the mold. Larger machines may utilize vacuum reservoirs and high-volume pumps for rapid and precise molding.
6. Plug-Assisted Vacuum Forming
For uneven distribution, a plug pushes the plastic sheet into the mold before vacuum application, ensuring uniform thickness, especially at the mold's base.
7. Cooling and Release
After forming, the plastic cools before being released. Premature release may cause deformation. Cooling is expedited with fans or mist sprays, and temperatures are carefully controlled to prevent defects.
Finally, trimming and finishing remove excess material. Finishing processes may include drilling holes, creating cutouts, decorating, printing, reinforcing, and assembling components.
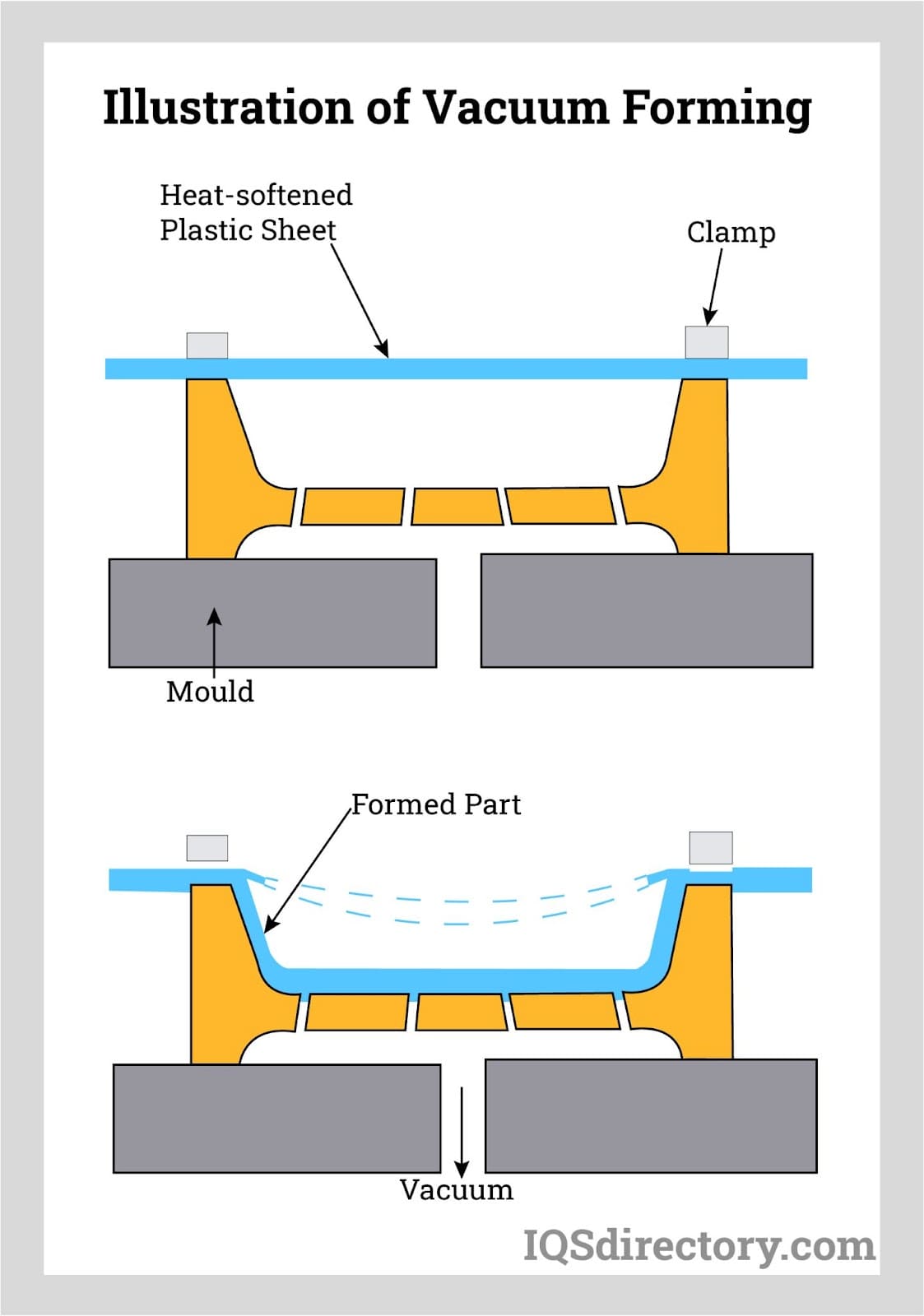
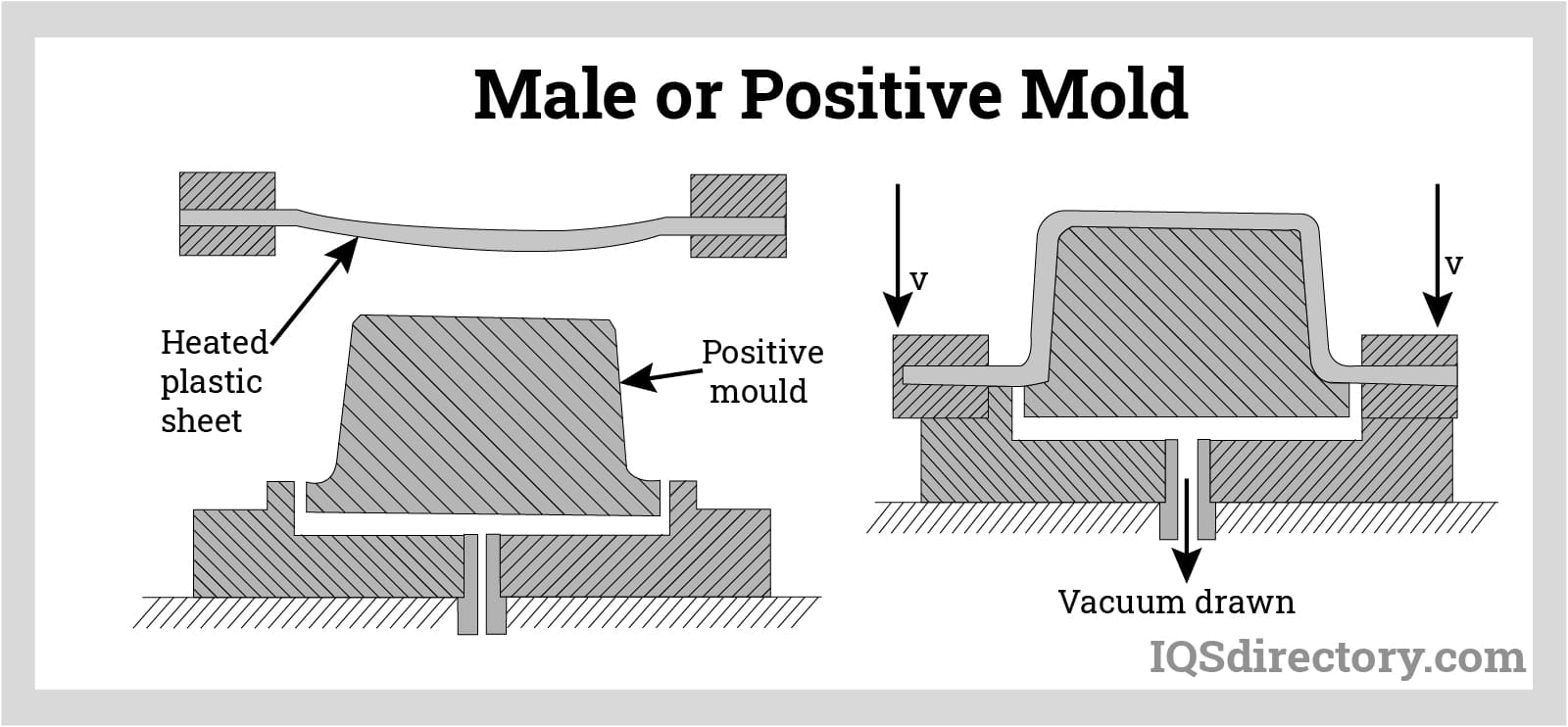
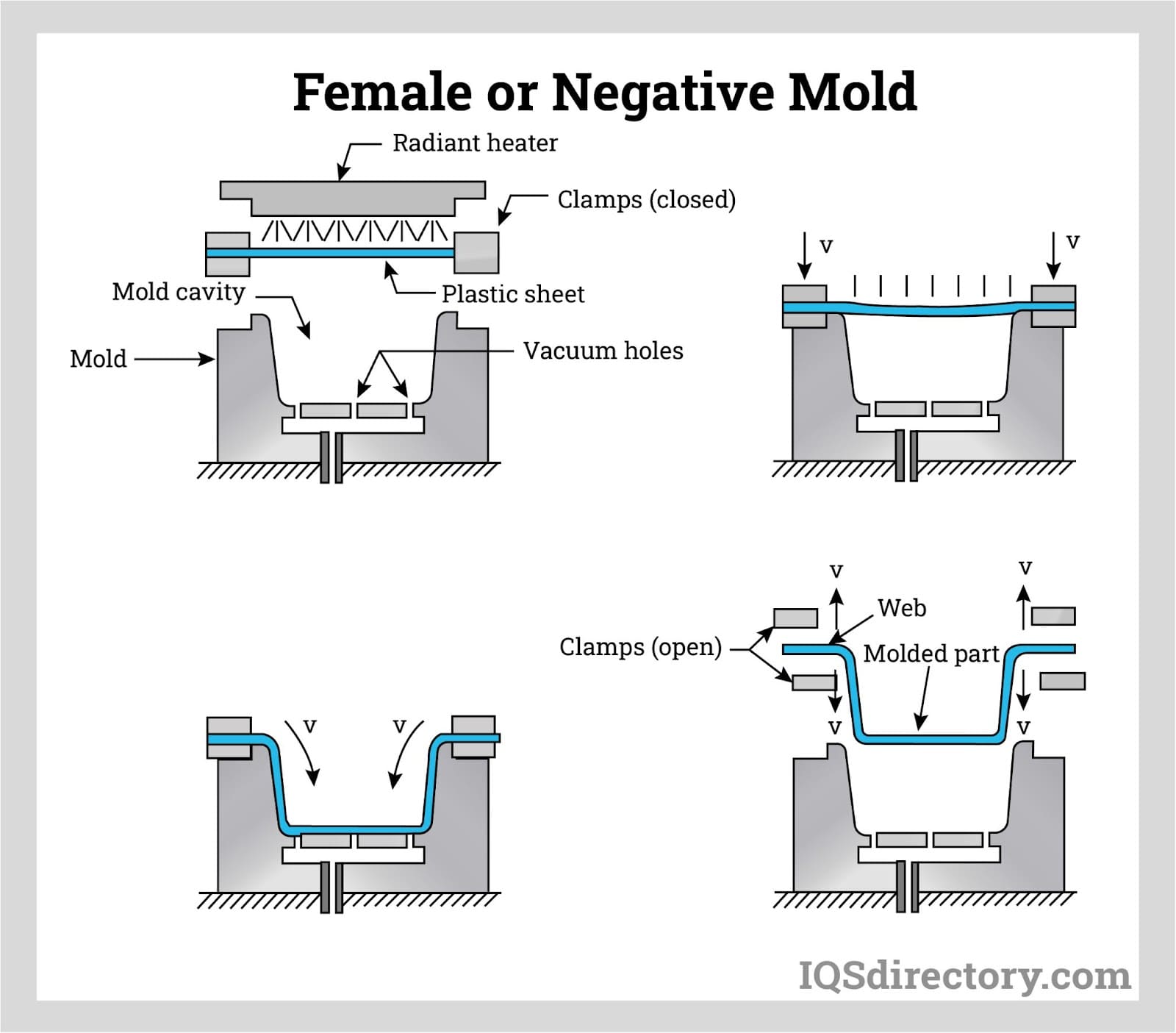
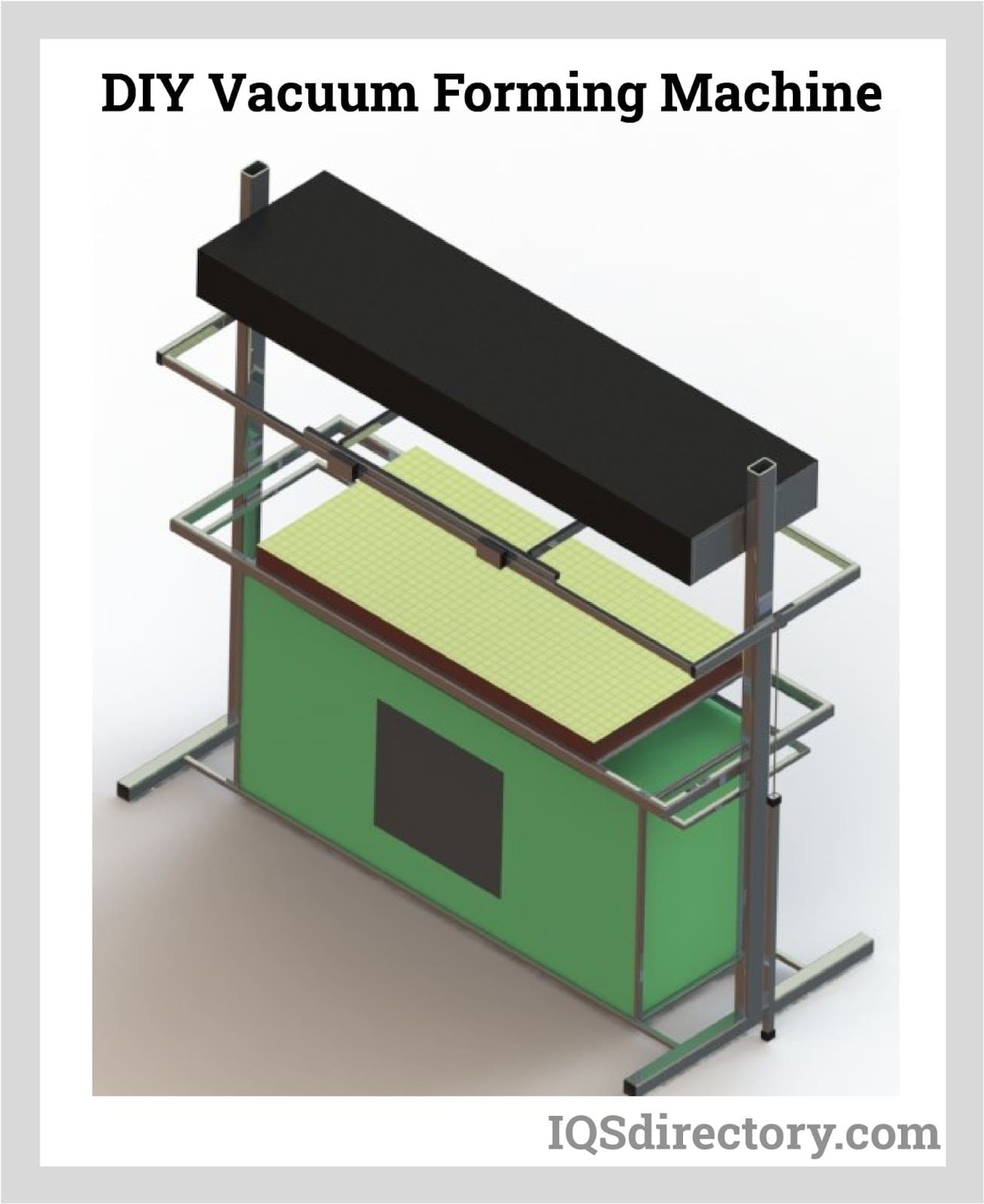
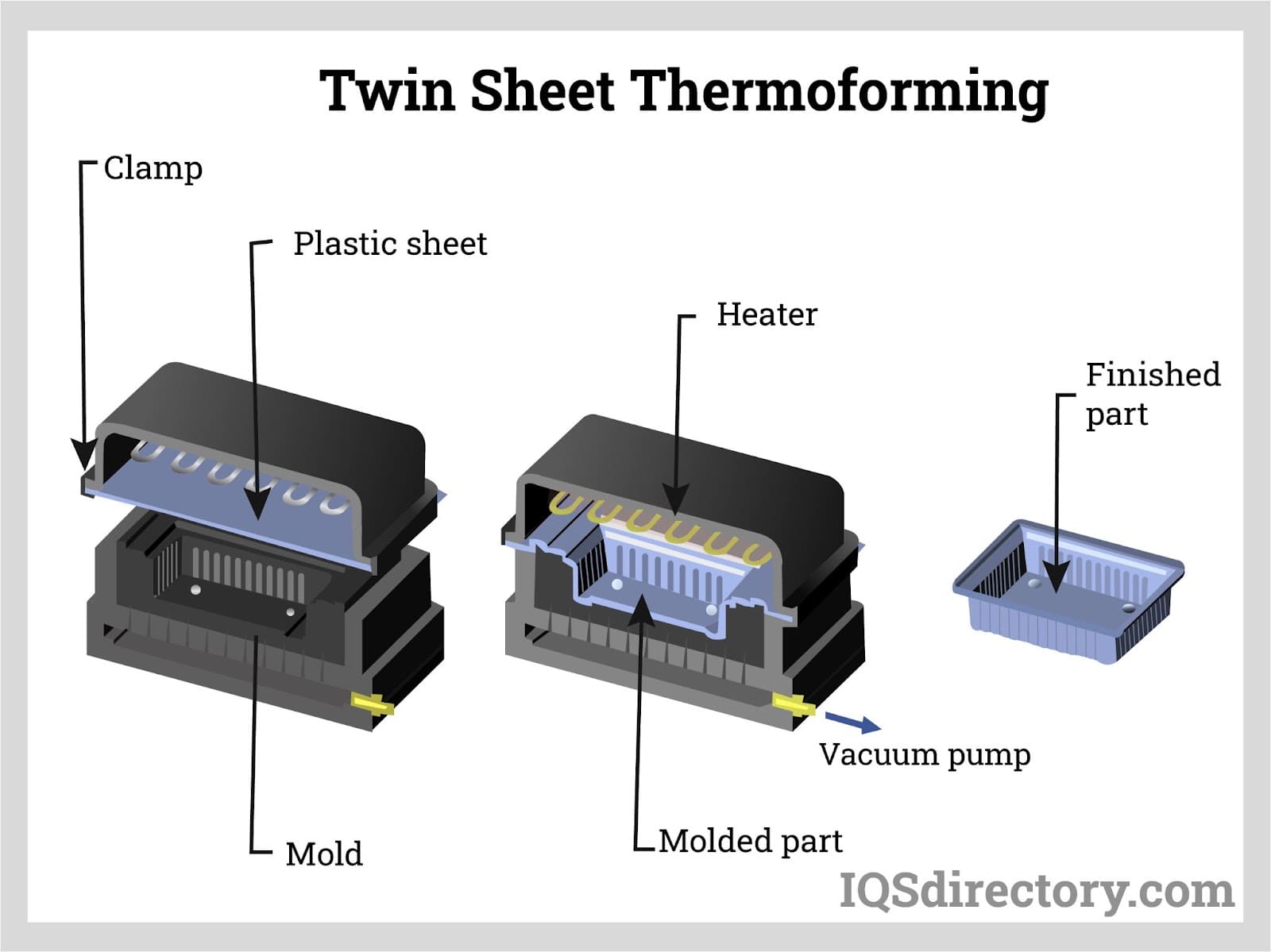
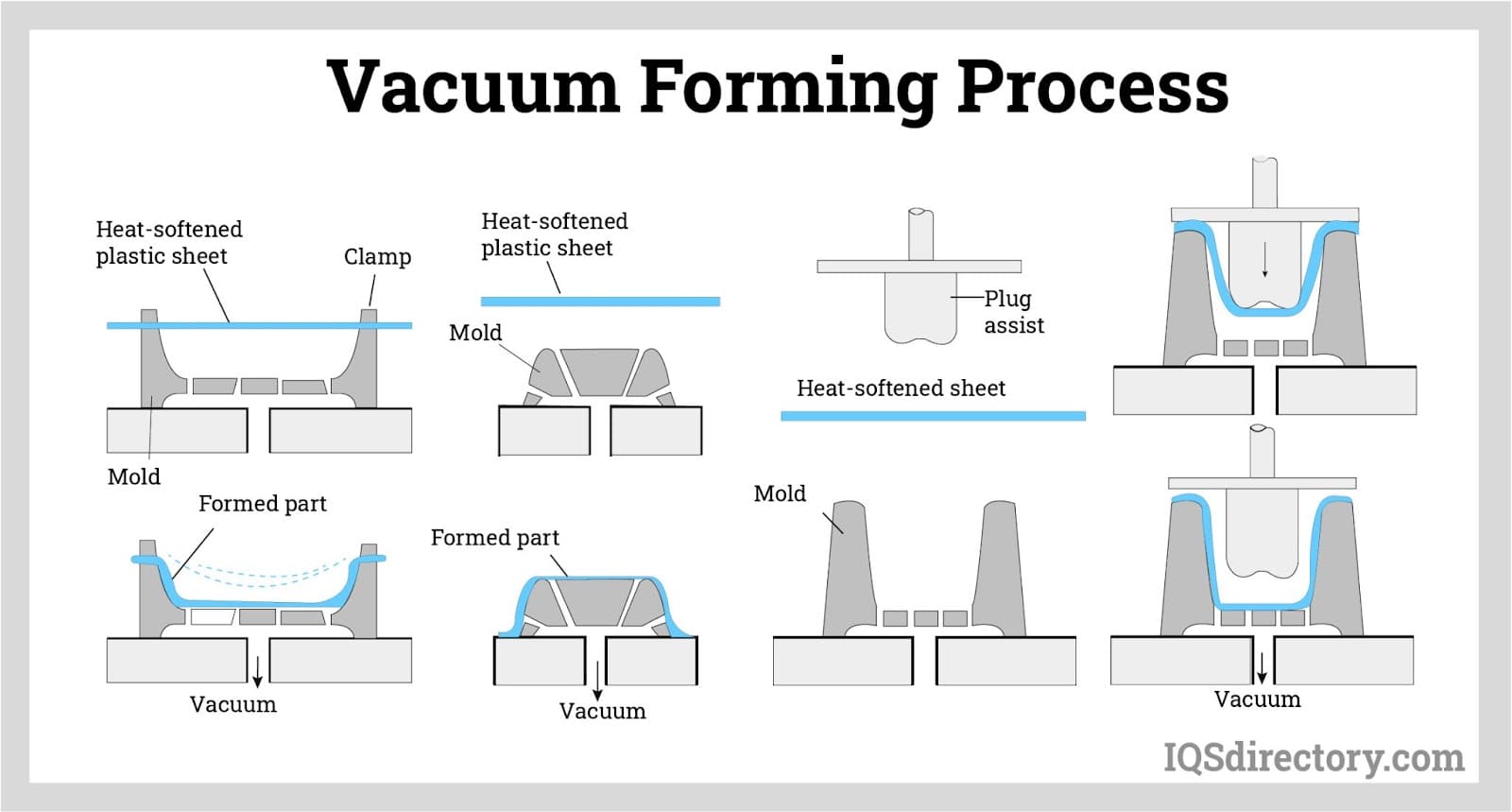
Vacuum Forming Types
Blister Packs
Clear, non-resealable plastic packaging designed to protect products from tampering.
Clamshells
Plastic packaging with hinges that allow it to open and close like a clam's shell.
Drape Vacuum Forming
A method similar to snapback forming, where the thermoplastic sheet is stretched to the base of the mold. Air is used to stretch the material before vacuum sealing it to the mold, ensuring uniform thinning of the plastic.
Plastic Covers
Vacuum-formed plastics designed to secure, protect, and contain objects from environmental factors such as weather, light, dust, water, or debris.
Plastic Forming
A category of manufacturing techniques that transform thermoplastics into a wide range of products for industrial, commercial, and domestic applications.
Plastic Packaging
All storage or containment solutions made by shaping various polymer resins.
Plastic Trays
Shallow platforms with raised edges, designed to prevent items from sliding or rolling off.
Plug Forming
A thermoforming technique where a plug or male mold presses heated plastic into a female mold before applying a vacuum. This ensures even distribution of material.
Pressure Forming
A thermoforming process where pressure is applied to the top of the plastic sheet while a vacuum pulls it downward. This method provides greater precision and allows the plastic to achieve more defined shapes.
Snapback Vacuum Forming
A process where a vacuum box pre-stretches the plastic sheet. A partial vacuum stretches the material, and the mold is pushed into it. The box is then vented to atmospheric pressure to complete the forming process.
Straight Vacuum Forming
A vacuum thermoforming method using only female molds, resulting in material distribution opposite to that of male molds.
Thermoforming
A process that involves heating and stretching thermoplastics into specific shapes.
Twin Sheet Thermoforming
A technique where two plastic sheets are vacuum-formed simultaneously and then fused to create hollow parts or products.
Vacuum Formed Plastics
Plastics created by using a vacuum to form heated sheets into molds during the thermoforming process.
Vacuum Molding
A manufacturing method that shapes thermoplastics through molding into a variety of products.
Vacuum Packaging
Refers to both packaging in reduced-oxygen containers and materials produced through vacuum forming.
Materials Used in Vacuum Forming
Vacuum forming utilizes a variety of materials, with thermoplastics being the most common. Ideal thermoplastics for this process possess properties such as low forming temperatures, good flow, thermal stability, minimal shrinkage during cooling, and high impact strength.
The most frequently used materials include polyester (PET), polyvinyl chloride (PVC), high-density polyethylene (HDPE), low-density polyethylene (LDPE), polypropylene (PP), polystyrene (PS), polycarbonate, acrylonitrile butadiene styrene (ABS), acrylics, and Kydex, a PVC-based thermoplastic.
- Polyester (PET): Forms easily at low temperatures, with fast cycles and excellent performance. Commonly used for packaging materials like food and beverage containers and processed meat packages.
- Polyvinyl Chloride (PVC): Known for its strength, toughness, transparency, and chemical resistance. Used in food wrappers, blister packaging, and vegetable oil bottles
- High-Density Polyethylene (HDPE): Although challenging to form, it is widely used for milk bottles, cereal box liners, plastic bags, and margarine tubs.
- Low-Density Polyethylene (LDPE): Also forms with difficulty but is suitable for garment bags, squeezable food bottles, plastic bags, and shrink wraps.
- Polystyrene (PS): A highly versatile thermoplastic that forms easily at low temperatures, enabling fast cycles without pre-drying. High-impact polystyrene is tough and cost-effective but unsuitable for outdoor use due to poor UV resistance. It is commonly used for fast food trays, disposable plastic cutlery, egg cartons, and CD jackets.
- Acrylonitrile Butadiene Styrene (ABS): A rigid, weather-resistant material with good impact strength due to its rubber content. It is used for luggage, vehicle parts, sanitary components, and electrical enclosures.
- Acrylic: Valued for its hardness, clarity, and high-quality finish. Applications include signage, baths, sanitary ware, and roof lights.
Applications of Vacuum Forming
The primary purpose of vacuum forming is to shape thermoplastics into various objects, ranging from simple packaging to complex, high-impact products like aircraft cockpit covers. This process is versatile and widely used across industries, enabling the transformation of thermoplastic materials into diverse shapes and designs.
Vacuum-formed products include permanent items like protective covers, road signs, and transparent components such as acrylic passenger cabin windows in aerospace. The process is a straightforward, low-technology method for molding that facilitates cost-effective production in numerous applications.
Industries That Use Vacuum Forming
Vacuum forming is a versatile process employed across various industries to create a wide range of products. Below is an overview of its applications in different sectors:
Aeronautical Industry
Aeronautical manufacturers use vacuum thermoforming to produce interior trim panels, covers, and cowlings. For example, NASA employs thermoforming technology to create interior components for space shuttles.
Agriculture
Agricultural suppliers manufacture numerous products from vacuum-formed plastic materials, such as animal containers, machine parts, flower tubs, seed trays, and clear growing domes.
Pharmaceuticals
Pharmaceutical manufacturers rely on vacuum thermoforming for blister packaging. A sheet of plastic is heated to form cavities, which are then sealed with plastic or aluminum foil to safely store and deliver unit doses of tablets, capsules, and lozenges.
Building and Construction
Vacuum forming plays a crucial role in creating various building components, such as PVC door panels, molds for concrete paving, molded ceiling features, drainpipes, roof lights, and internal door liners. Other applications include fireplaces, porches, and decorative architectural elements.
Automotive and Vehicular Industries
The automotive sector heavily utilizes vacuum forming for parts like wheel hub covers, bumpers, mudguards, liners, seat backs, storage racks, ski boxes, door interiors, windshields, protective panels, batteries, and electronic housings.
Medical Applications
Hospitals and medical facilities depend on vacuum forming for the production of prosthetics, pressure masks, radiotherapy masks, wheelchair components, and dental castings.
Other Industries
Vacuum forming is also widely used to produce furniture, packaging materials, bathtubs, shower surrounds, souvenirs, point-of-sale displays, cosmetic cases, and cutlery.
Customization in Vacuum Forming
Design Customization
While the basic vacuum thermoforming process is similar across machines, customizations ensure specific requirements are met. Mold types—male (protruding) or female (recessed)—are selected based on the product’s design.
Pressure forming is a variation that combines vacuum forming with additional air pressure to achieve greater detail and precision in the final product. This method is ideal for intricate designs.
Machinery and Customization
Specialized tools and equipment are integral to both the primary production and secondary customization of vacuum-formed products. The choice of machinery depends on factors like product size, thickness, and quantity.
Finishing and trimming tools include trimmers, scalpels, heated knives, vertical and horizontal band saws, roller presses, guillotines, punch presses, and handheld power routers. CNC machining offers high precision for drilling holes and adding detailed customizations, such as engraving or embossing specific marks and text.
Choosing the Right Manufacturer
There are many manufacturers in the vacuum forming plastic industry. Any good manufacturer can be found but it is essential for a customer to get the right manufacturer. The right manufacturer ensures that all needs of the client are met. When a custom plastic is needed, the right manufacturer will be able to deliver it.
Vacuum Forming Terms
Selecting the right vacuum forming manufacturer is essential to meet specific needs. A reliable manufacturer ensures high-quality results and accommodates custom requirements. For unique designs and specialized products, partnering with an experienced manufacturer guarantees the best outcomes.
Vacuum Forming Terms
Black Points
Dark particles that form in plastic film during thermoforming due to contamination.
Bleed
The tendency of some plastics to lose color when exposed to water or certain solvents. It also refers to the unwanted migration of materials to the surface of plastic or into adjacent materials.
Blister
Thermoformed semi-rigid plastic shells designed to conform to the shape of the packaged product.
Boss
A protrusion on a plastic part that adds strength, aids in alignment during assembly, or facilitates fastening.
Burn Holes
Openings in thermoformed plastic caused by vacuum and heat at weak or thin points.
Degradation
A structural change in plastic material.
Denest
The separation of thermoformed parts, such as blisters, for further processing in packaging.
Destaticization
The removal of static electricity from plastic to minimize dust adhesion.
Die Cutting
Using a steel rule to cut finished sheets of blisters or blister cards into individual pieces.
Draft Angle
The tapering of a blister or clamshell sidewall to facilitate removal from the thermoforming mold and ease denesting.
Embossing
Creating patterned depressions on plastic film or sheeting.
Environmental Stress Cracking
The tendency of thermoformed plastic to crack when exposed to specific chemicals.
Female Mold
A concave mold, also known as a negative or cavity mold.
Fold-Over Blister Card
A blister card that is scored and die-cut to allow the blister to be sealed between two card halves or between a card and a blister flange, commonly used for heavy items.
Gas-Flush
In vacuum packaging, a process where nitrogen flushes the chamber to prevent the plastic from clinging tightly to fragile products.
Heat-Sealing
Joining two or more plastics using heat and pressure.
Male Mold
A convex mold, also called a positive or protruded mold.
Pock Marks
Irregular indentations caused by trapped air, surface moisture, or low pressure, resulting in insufficient contact between plastic and the mold.
Prototype
A model representing the size and design of a final part.
Reprocessed Plastic
Thermoplastic material made from industrial plastic scrap generated by another processor.
Sag
The flow of heated plastic sheeting during thermoforming, where molten sheets sag. The sag distance, measured by an electric eye, indicates the material's readiness for forming.
Sandwich Heating
A method of heating thermoplastic sheets on both sides before forming.
Scrap
Plastic material not part of the final product, typically tip scrap, which can be reused.
Sheet Train
The production setup for creating plastic sheeting, including an extruder, die, polish rolls, conveyor, draw rolls, cutter, and stacker.
Thermal Expansion
The slight change in length or volume of material when exposed to heat.
Two-Piece Blister
A double blister design for displaying a product on both sides.
Undercut
An indentation or protrusion that complicates mold removal.
Unit Dose Packaging
Blister packaging designed for single-dose medicines to ensure clarity and convenience.
Vacuum Form Table
A machine used to produce vacuum-formed parts and products.
More Vacuum Forming