Vibratory Feeders
A vibratory feeder, also known as a bowl feeder, is one of the three primary types of parts feeders used in bulk material handling. The other two are centrifugal feeders and pneumatic feeders. Vibratory feeder systems utilize vibration to transport parts or bulk materials through various stages, such as finishing, packaging, or recycling.
- In contrast to methods like pneumatic, screw, or standard belt conveying, vibratory conveying provides an ideal solution for handling delicate or sticky food materials. Its gentle movement minimizes the risk of liquefying, shearing, or damaging materials during the process.
History of Vibratory Feeders
The first vibratory feeders were patented in the United States by Mario Thomas Sgriccia in 1950. Initially used primarily in the mining industry, these early machines were durable and straightforward but had notable drawbacks, including high energy consumption, substantial weight, and uneven material distribution. In the 1960s, engineers introduced the electromagnetic vibrating feeder, which was lighter, more energy-efficient, and provided more consistent material flow. However, these models were still loud and lacked durability.
Since then, manufacturers worldwide have refined vibratory feeders. Innovations such as sound enclosures have improved the usability of these machines, leading to today’s diverse range of feeder types. Modern vibratory feeders are quieter, highly durable, and efficient, catering to industries far beyond mining, including any sector requiring material sifting and sorting
Benefits of Vibratory Feeders
Vibratory feeders offer several advantages, including:
- Low Maintenance & Easy Material Handling: Minimal moving parts reduce upkeep.
- Cost-Effectiveness & Automation: Lower operational costs with automated functionality.
- Versatility: Adaptable for various materials, regardless of shape, size, or weight.
- Effectiveness & Accuracy: Precise feeding ensures efficient material handling.
- Ergonomic Design: Simplifies operations and improves user experience.
Additionally, feed rates can be easily adjusted to suit specific application needs, enhancing their versatility.
Design of Vibratory Feeders
When designing a vibratory feeder system, manufacturers consider factors like load volume, material feed rate, material size, texture, and vibration intensity or amplitude.
The standard vibratory feeder design is a bowl feeder, typically made of stainless steel, silicone, or plastic. These bowls are mounted on a base with a vibrating drive system beneath them. Customization options include:
- Sound Enclosures: Minimize noise during operation.
- Feed Rate Adjustments: Tailored to specific application requirements.
- Vibration Parameters: Custom intensity and amplitude settings.
How Vibratory Feeders Work
Though individual models vary, vibratory feeders generally move materials using a combination of gravity and vibrations:
- Gravity dictates the flow direction of materials, guiding them downward or sideways
- Vibrations, generated by a drive unit beneath the feeder bowl, move materials or parts along a predetermined path.
The bowl and drive unit create circular vibrations, propelling materials up a spiral ridge along the bowl’s edge. At the outfeed area, parts are aligned into a single-file line.
For loose materials, vibratory feeders often work alongside additional equipment like vibratory screens, conveyors, or trommels to sift and separate materials efficiently.
Vibratory Feeders Images, Diagrams and Visual Concepts
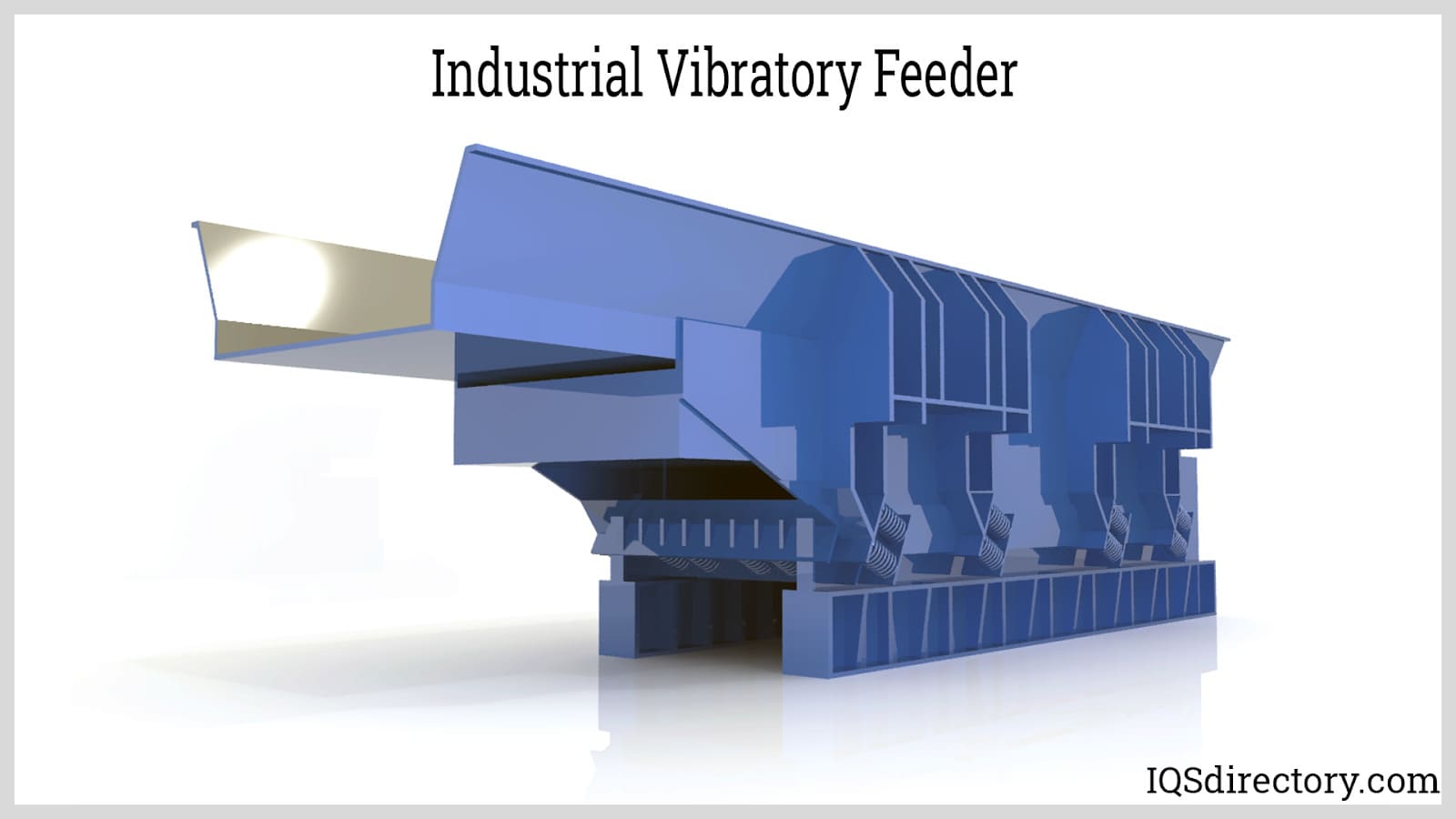
A vibratory feeder is a conveying system designed to feed components or materials to an assembly process using controlled vibratory forces, gravity, and guiding mechanisms to position materials.
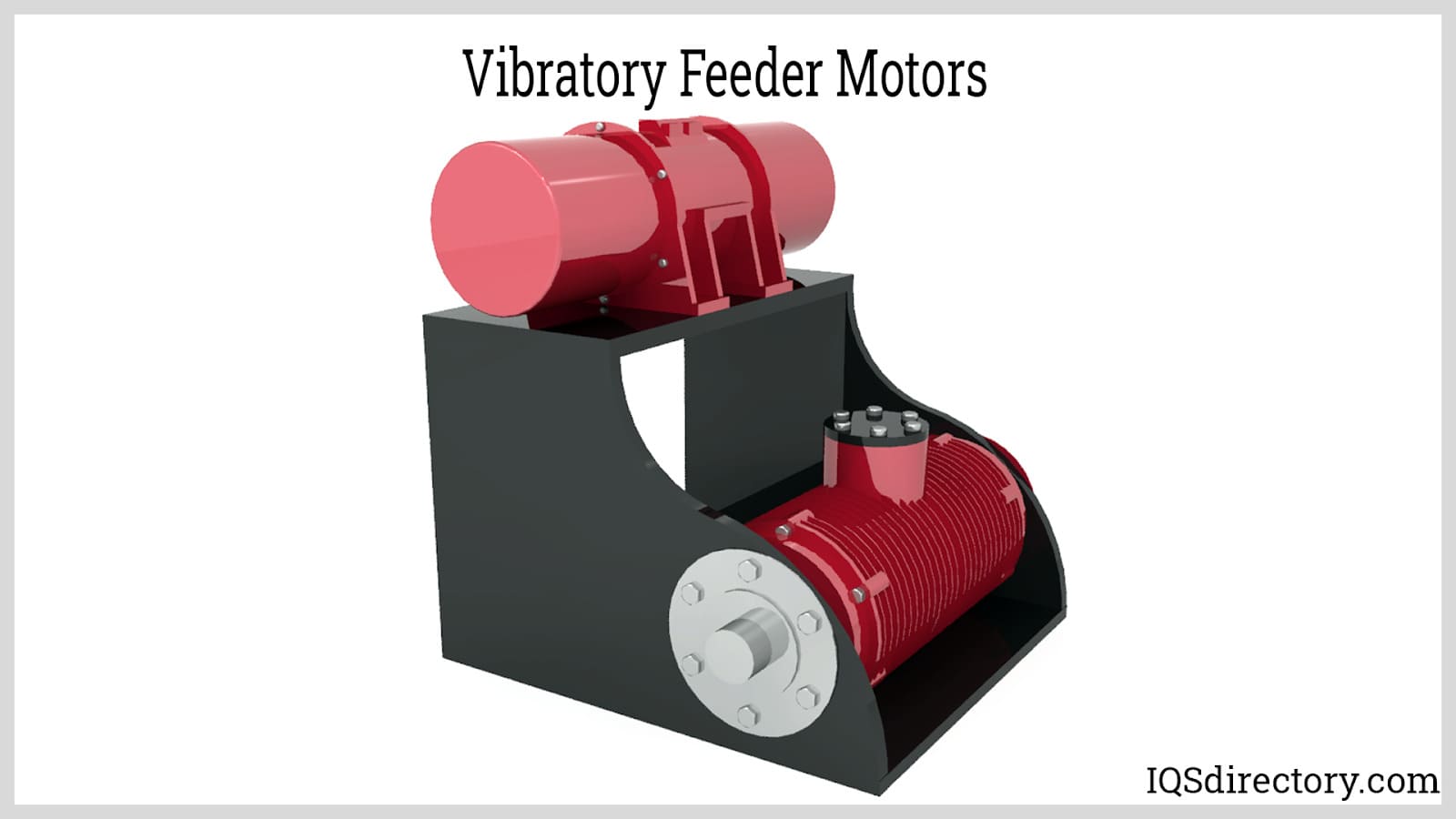
The motors causes vibrations with both horizontal and vertical.
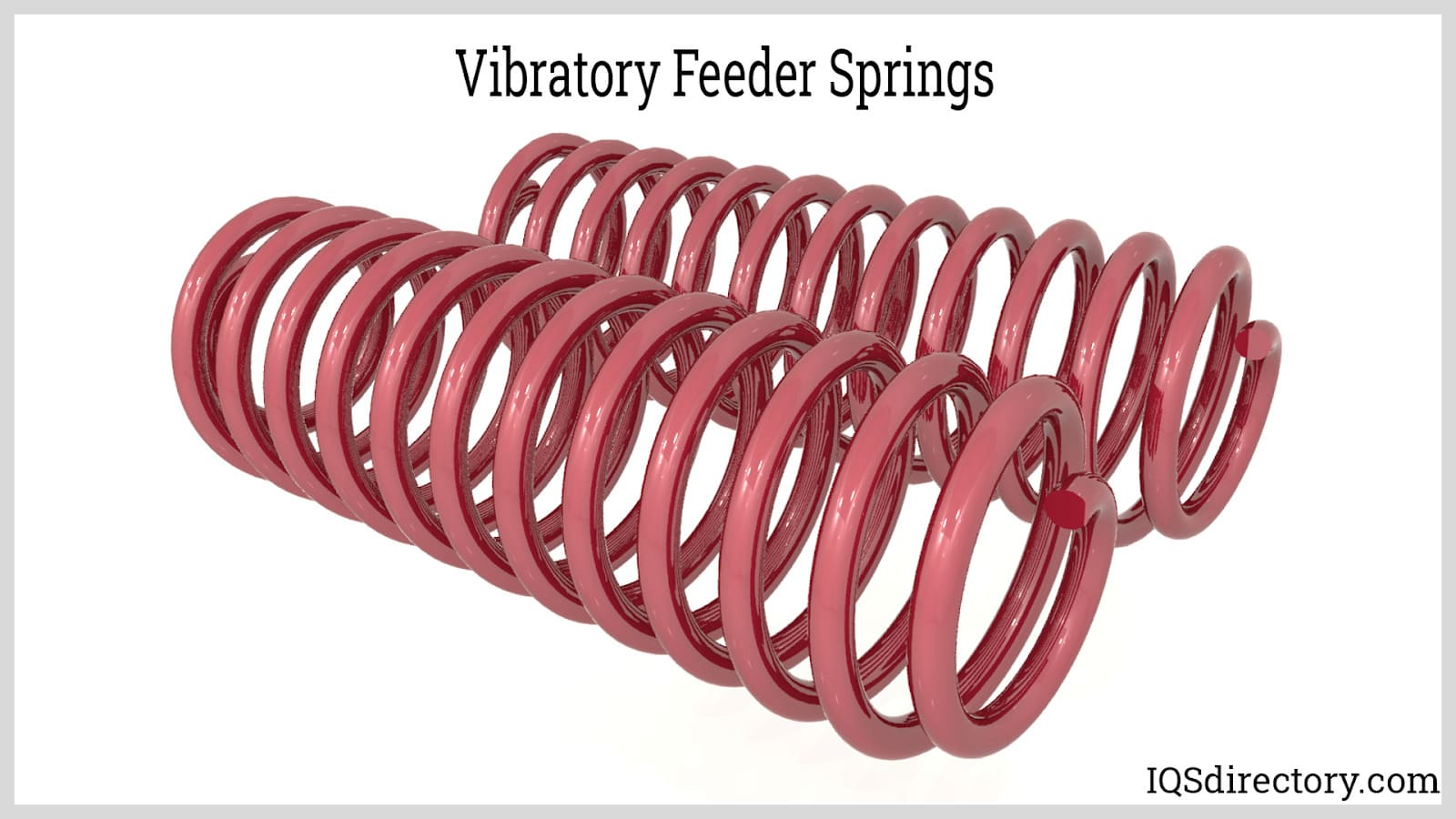
The primary springs continuously store and release energy during operation.
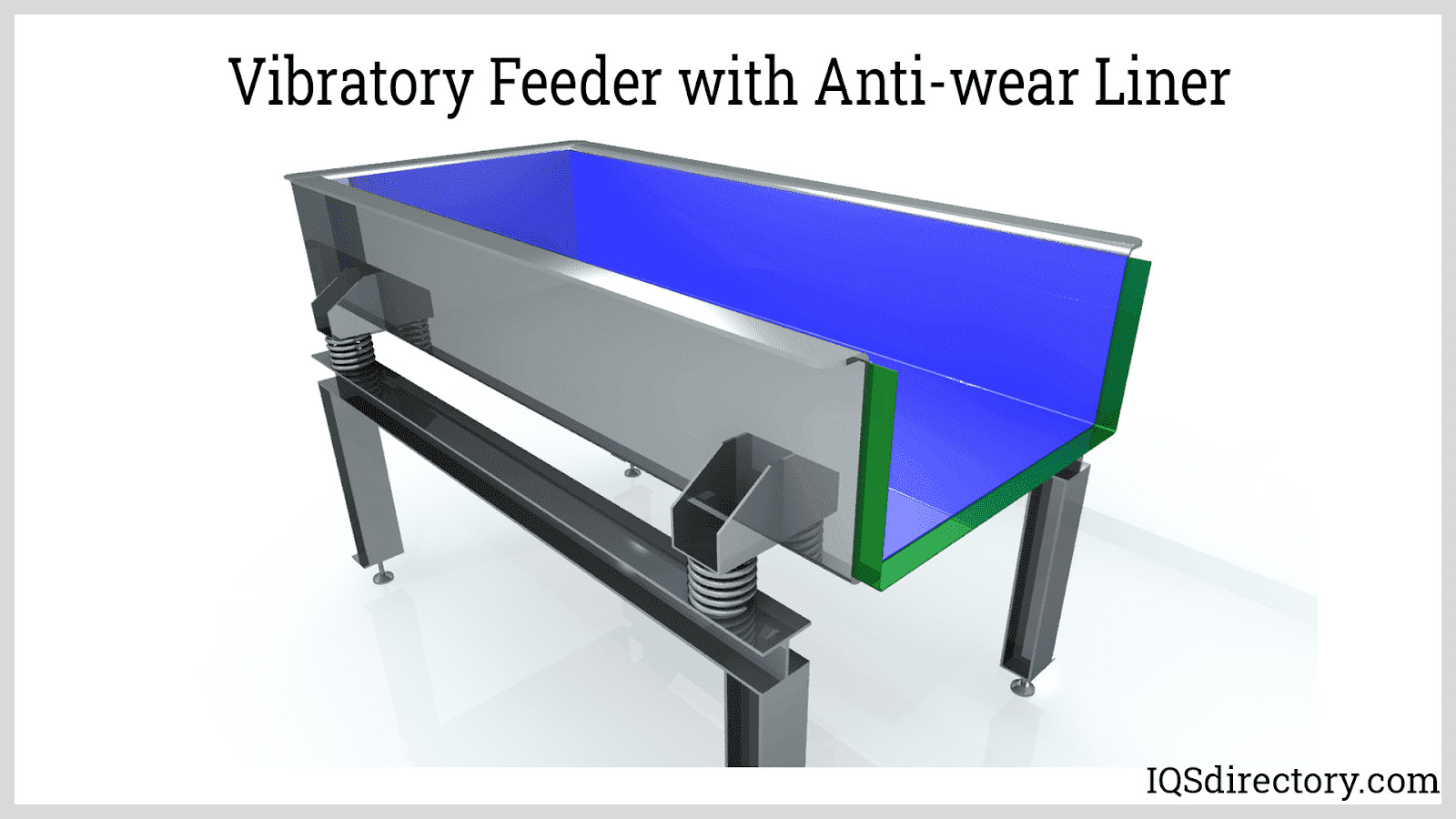
Material added to cover the surface of the trough to resist wear, temperature, reduce noise, reduce friction,and prevent material buildup in the trough.
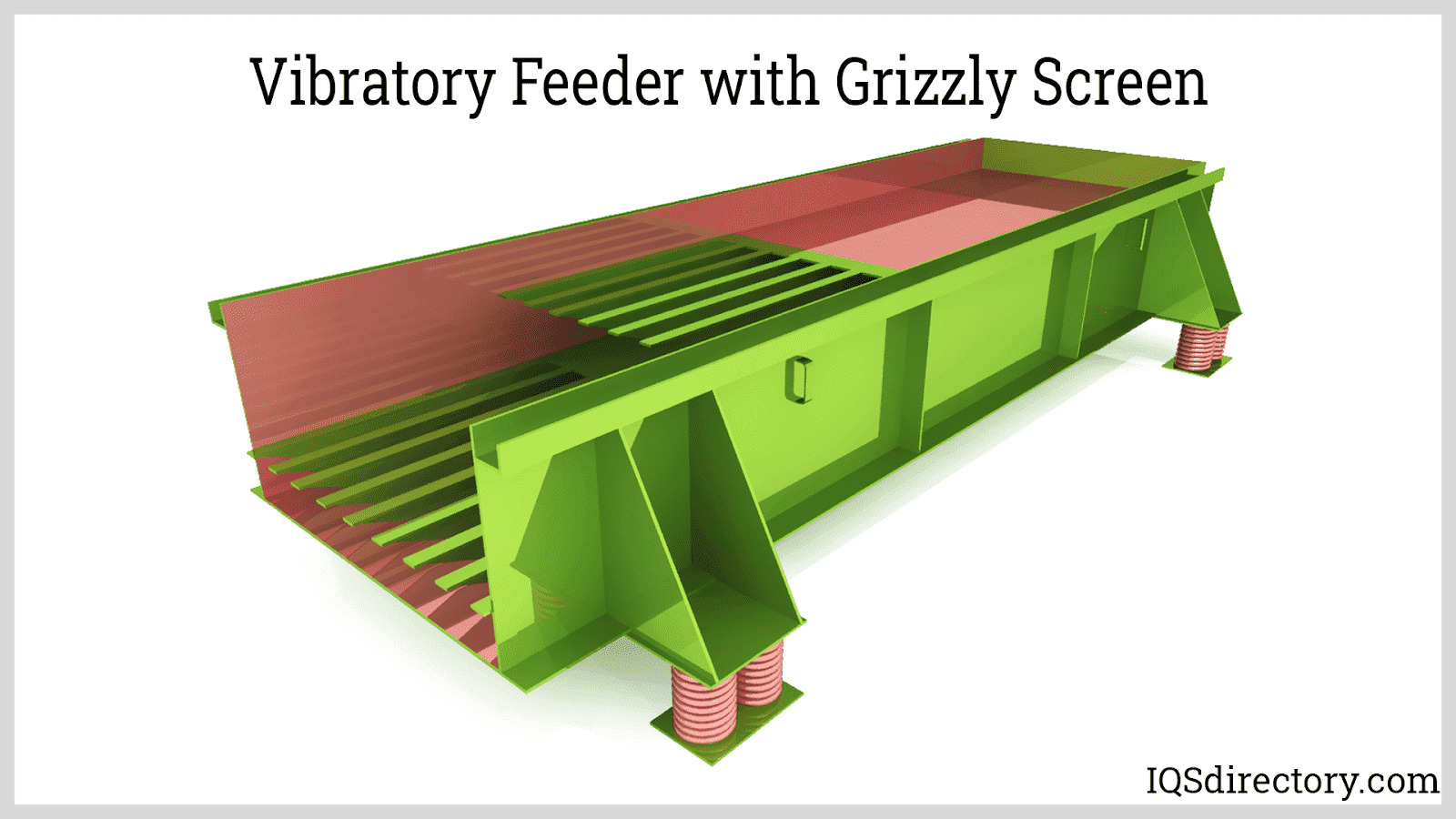
A Grizzly Screen heavy-duty screen consisting of rails or bars running in the direction of material flow and separtes fine particles form the material.

Vibratory bowl feeders have helical trough which uses vibrations to toss and shuffle materials along a slightly slanted surface of the helical trough.
Types of Vibratory Feeders
Vibratory Bowl Feeder
Also referred to as vibratory bowls, these feeders consist of a bowl-shaped top and an inclined spiral track that guides components. Parts move from the track to a line leading to the bottom of the bowl feeder. These feeders are widely used by small parts manufacturers to efficiently orient products for further processing or distribution. Initially designed by pharmaceutical companies for counting, sorting, and organizing pills, bowl feeders are now used for small parts such as fasteners, ammunition, O-rings, molded rubber components, and toothpaste caps.
Vibratory Conveyor
Also known as step feeders, these are metal troughs that vibrate in one direction to transport bulk powders or heterogeneous mixtures from one process to another. Some vibratory conveyors are specially designed with ultra-low vibrations for delicate or sticky materials, like gummy bears or lettuce. A major benefit of step feeders is that they prevent part jamming, a common issue with standard bowl feeders. This smooth operation reduces downtime and operational costs over time.
Grizzly Screen
A high-powered type of vibrating screen, the grizzly screen is most commonly used in the mining industry for separating materials.
Electromagnetic Vibratory Feeders
These feeders utilize a sub-resonance tuned two-mass system to generate vibrations. The basic mechanism involves an electromagnet attracting an armature bracket, which is connected to a secondary mass via a leaf spring set, creating linear vibrations. These vibrations move materials along the feeder pan. A controller adjusts the AC supply to regulate the feed rate. Electromagnetic feeders are known for their excellent control and are ideal for batching applications.
Electromechanical Vibratory Feeders
These feeders use rotary electric vibrators to provide fully adjustable and consistent volumetric flow. They are corrosion-resistant, rugged, and require minimal maintenance. Electromechanical feeders are equipped with controls for vibration intensity, force, and frequency, making them versatile for use across various industries. They can be outfitted with single, dual, or multiple drives to function as vibrating conveyors, offering unique flexibility compared to other vibratory equipment
Trommel
Trommels, or trommel screens, are vibrating screens used to sort smaller particles from larger ones. They significantly reduce the labor needed to sort recyclable materials, streamlining the recycling process and making it a more cost-effective aspect of manufacturing.
Rotary Trommel
This large tumbler design aids in gravel processing and recycling. Trommel magnets are often incorporated into metal recycling rotary trommels to separate ferrous materials from non-ferrous ones.
Continuous Flatbed Trommel
Equipped with screens or filtering devices, these trommels sort particles by size, allowing larger particles to be conveyed for further processing or containment.
Pneumatic Feeder
Specialized for laboratory use, pneumatic feeders are both water- and explosion-proof, meeting laboratory standards. They operate with a pneumatic drive unit featuring a piston engine to create vibrations. Designed to maintain a constant speed regardless of load, they are ideal for lab environments. Additionally, they are known for being environmentally friendly, reliable, and low maintenance.
Types of Non-Vibratory Feeders
Screw Feeder
Screw feeders are specifically designed for use with screw conveyors. They are ideal for volumetrically metering materials at a controlled rate, providing precise control over the feed process.
Belt Feeder
A belt feeder consists of a conveyor belt and rollers that allow the belt to move. This type of feeder is typically used to transport materials that do not require pre-sifting before being fed into bulk handling machines.
Storage Hopper
Storage hoppers are containers used to collect granular materials and dispense them onto a conveyor or other material handling systems using gravity.
Linear Feeder
Also known as inline feeders, linear feeders are a non-vibratory alternative to vibratory feeders. They feature horizontal conveying components and are designed for handling oily or irregular parts that vary in size and shape. Linear feeders require minimal maintenance and are easy to set up, providing long-term reliability.
Centrifugal Feeder
Centrifugal (or rotary) feeders work alongside screw conveyors or vibratory conveyors to provide air-tight bulk material feeding. These feeders use a rotating disk powered by an electric motor to generate centrifugal forces that move components to the outer edge of the bowl. Specialized tools then orient the parts before they are fed into the processing line. These feeders are ideal for high-speed, gentle handling, particularly for components that do not tend to tangle, such as caps and medical devices. Centrifugal feeders are commonly used in applications like powder bulk material conveying or dust collection systems, operating without electromagnetic vibrations or gravity.
Vertical Mast-Step Feeder
Vertical mast-step feeders save floor space by collecting components from a hopper and using elevated plates or conveyors to achieve the necessary height. They operate quietly and without vibration, leading to lower maintenance requirements.
Applications of Vibratory Feeders
Vibratory feeders are widely used for feeding, sifting, and sorting delicate materials like powders. They handle materials such as plastic, wood, crushed cement, metals, gravel, and sand, and can also align small parts like washers, O-rings, Legos, and coins. These feeders are essential in industries like recycling (for material reclamation), fertilizing, sand and gravel, pharmaceuticals, agriculture, food processing, mining, and pulp production.
Things to Consider When Purchasing Vibratory Feeders
When purchasing a vibratory feeder, it’s essential to evaluate both your application needs and the reliability of the manufacturer. Key factors to consider include: the type of material you need to handle (e.g., loose, compact, small parts), the material's weight, the required speed of movement, whether sanitary conditions are necessary, and how frequently you’ll need to change materials.
Once you have answers to these questions, take them to a trusted manufacturer. How do you find one? The best approach is to use a directory, like the one provided by IQS. We’ve already done the research for you by identifying the top manufacturers across the USA and Canada. To explore our recommendations, check out the list at the top of the page. Review their websites, select three or four companies that seem to meet your needs, and contact them to discuss your specifications. Compare their responses, keeping in mind that the right choice will be the manufacturer capable of delivering high-quality results that align with your budget and timeline.
Vibratory Feeder Equipment Components
Vibratory feeders consist of several key components: an electromagnetic or electromechanical system, springs, a bowl, a spiral track, and, often, a control box.
In an electromagnetic system, springs connected to the system convert electromagnetic vibrations into wavy movements within the bowl. In an electromechanical system, rotary electric vibrator drives generate the movement. The spiral track helps move parts through the feeder, while the control box, or cycle controller, adjusts the intensity and amplitude of the vibrations.
Vibratory Feeders Terms
Approach
The location in the parts feeder bowl where parts begin to ascend the feeder track.
Backpressure
The force exerted when parts emerge from the vibratory feeder.
Cascade Bowl
A type of bowl feeder featuring basic tooling on its inner track. Cascade bowls are ideal for orienting larger, standard parts.
Depth of Bed
Also known as "material depth (mat. depth)," this is the thickness of the material layer carried on the conveyor or vibratory feeder surface.
Discharge End
The exit point of the vibratory feeder where parts emerge from the system.
Drive Unit
Also called the "drive base unit," this device powers the vibratory feeder system.
Explosion Proof
Equipment designed to meet operational standards in hazardous environments, as defined by organizations such as Underwriters Laboratories (UL).
Feed End
The entrance through which parts enter the vibratory feeder system.
Grizzly
A durable screen used for sizing bulk materials.
Hanger
Also referred to as "suspension assembly" or "bail assembly," this device supports the vibratory feeder.
Head Load
The weight of the material supported by the vibratory feeder, located in the trough and hopper/bin.
Hopper
A large, bulk container that stores material and regulates its flow into the vibratory feeder system.
Isolation
Also known as a "vibration absorber," this device separates vibrations between the machine and the supporting structure. Examples include coil springs and rubber isolators.
Load Sensitivity
The variation in vibratory feeder performance as its material load decreases.
Orientation
The process of arranging parts in a specific position from random orientations. Vibratory feeders generally support three levels of orientation: simple, moderately complex, and complex.
Outside Track Bowl
A bowl feeder with intricate tooling designed for parts with complex configurations.
Rotation
The directional movement (clockwise or counterclockwise) of the drive base unit that shifts the bowl feeder and parts.
Singulation
The separation of a group of parts into individual components.
Sound Enclosure
A foam-lined structure designed to absorb noise generated by the vibratory feeder.
Spring
A device that generates or isolates vibration between the machine and its supporting structure.
Trough
Also known as a "pan," this is the tray where materials are loaded into the vibratory feeder system.
Vibratory Separators
Devices used across various industries to separate materials or particles for different applications.
More Vibratory Feeders Information