Wire Rope
A wire rope is a cable made by intertwining multiple wire strands to form a single, cohesive structure. While the terms "wire," "rope," and "wire rope" are often used interchangeably, the technical definition specifies that a cable must be at least 9.52 mm thick to be classified as a wire rope. Known for its versatility and high load capacity, wire rope serves as a durable alternative to natural fiber ropes like hemp or manila. It is widely used for applications such as motion transmission at various angles, tie-downs, counterbalancing, guidance, control, and lifting.
The History of Wire Rope
Modern wire rope was invented by Wilhelm Albert, a German mining engineer, between 1831 and 1834. He developed wire rope for use in the mines of the Harz Mountains, replacing weaker natural fiber ropes like hemp and manila, as well as less durable metal ropes such as chains.
Albert’s design consisted of four three-stranded wires. In 1840, Robert Stirling Newall, a Scottish engineer, improved upon Albert’s model. Around the same time in the United States, John A. Roebling, an American manufacturer, began producing wire rope with the goal of constructing suspension bridges. Other American innovators, such as Erskine Hazard and Josiah White, adapted wire rope for railroad and coal mining applications. They also used wire rope to build lift systems for the Ashley Planes project, improving transportation and boosting tourism in the region.
In 1874, approximately 25 years later, the German engineering firm Adolf Bleichert & Co. was established. They utilized wire rope to construct bicable aerial tramways for mining operations in the Ruhr Valley. Over time, they expanded their work to include tramways for both the Wehrmacht and the German Imperial Army. Their wire rope systems gained popularity across Europe before reaching the United States, where they found a hub at Trenton Iron Works in New Jersey.
Over the decades, engineers and manufacturers have developed various materials to enhance the strength and durability of wire rope. These include stainless steel, plow steel, bright wire, galvanized steel and specialized wire rope steel. Today, wire rope is an essential component in heavy industrial operations, reliably facilitating tasks that require significant lifting power.
Advantages of Wire Rope
Wire rope is renowned for its strength, durability, and versatility. Its unique construction evenly distributes weight among its strands, allowing it to handle even the heaviest industrial loads with ease.
Wire Rope Design
Wire ropes consist of three primary components: wire filaments, strands, and cores. Manufacturers create wire rope by twisting or braiding filaments into strands, which are then helically wound around a core. Due to this multi-strand configuration, wire rope is also commonly known as stranded wire.
Rope Filaments
The first component, the filaments, are cold-drawn metal rods of varying but relatively small diameters. The second component, the strands, consist of multiple filaments—ranging from as few as two to several dozen. Lastly, the core serves as the central element around which the strands are wrapped. Wire rope cores enhance flexibility while increasing strength by at least 7.5% compared to fiber core ropes.
Lay of a Rope
The helical winding of strands around the core is referred to as the "lay." Ropes can be either right-hand lay, with strands twisted clockwise, or left-hand lay, with strands twisted counterclockwise.
In an ordinary lay, the individual strands are twisted in the opposite direction of the rope’s lay to increase tension and prevent unwinding. This is the most common configuration. In contrast, Lang’s lay twists both the strands and the rope in the same direction, while alternate lays combine ordinary and Lang styles. Despite the availability of alternative designs, the helical core configuration is often preferred for its combination of high load capacity and ductility.
Rope Customization
Wire rope manufacturers consider various design factors when creating custom assemblies. These include:
- Strand gauge: Adjusted based on strength, flexibility, and wear resistance requirements.
- Wire rope fittings: Used to connect cables to other components.
- Lay: Determines the direction and style of the rope’s twist.
- Splices and coatings: Enhance durability and performance.
Specialized wire ropes, such as push-pull cable assemblies for transferring motion, often use treated steel or plastic-coated cables tailored to specific applications.
Wire Rope Images, Diagrams and Visual Concepts
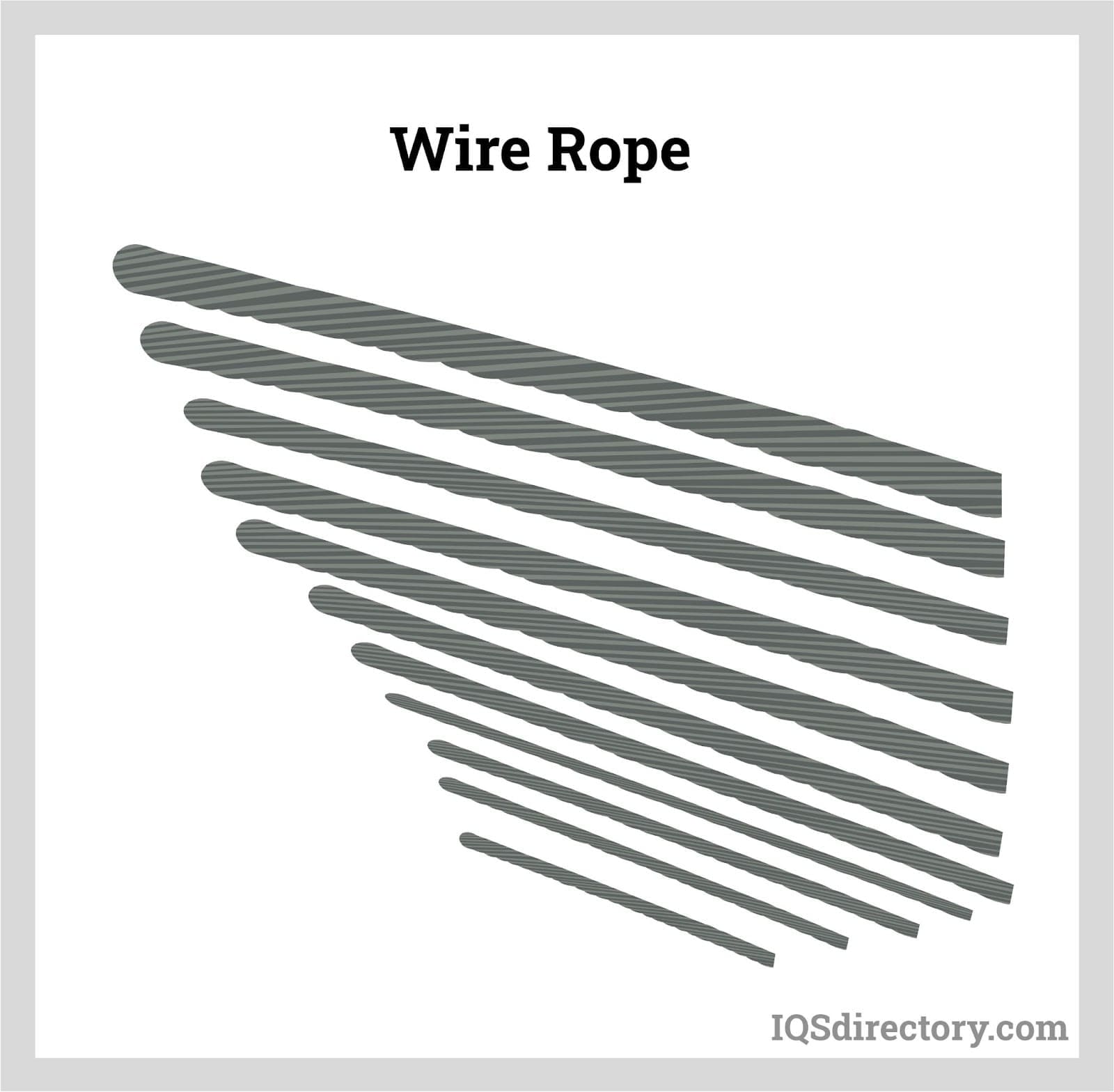
Wire rope is constructed of multiple wire strands that are braided together to form a spiral or helix design.
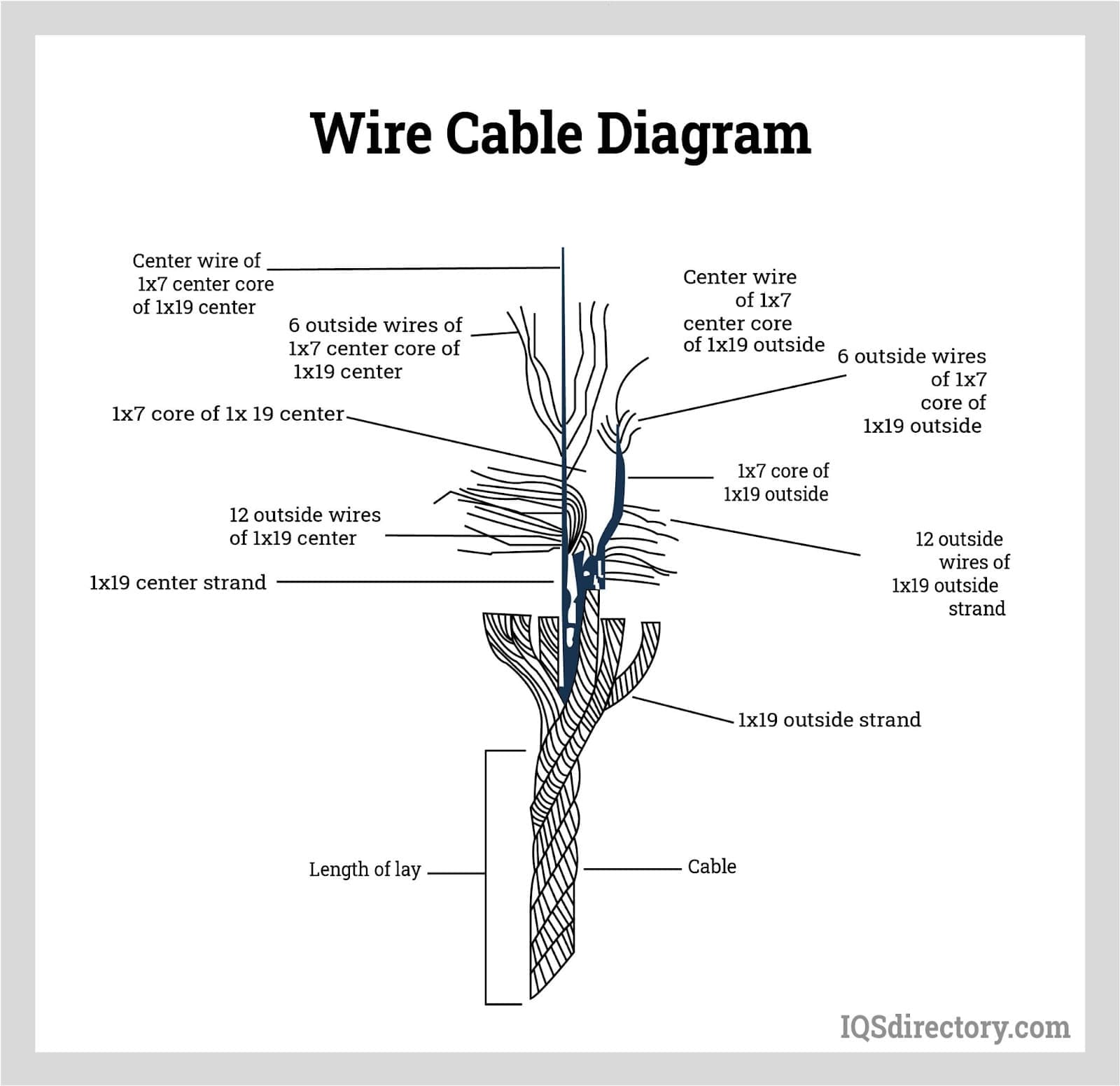
An overview of each step found in the manufacture of wire rope.
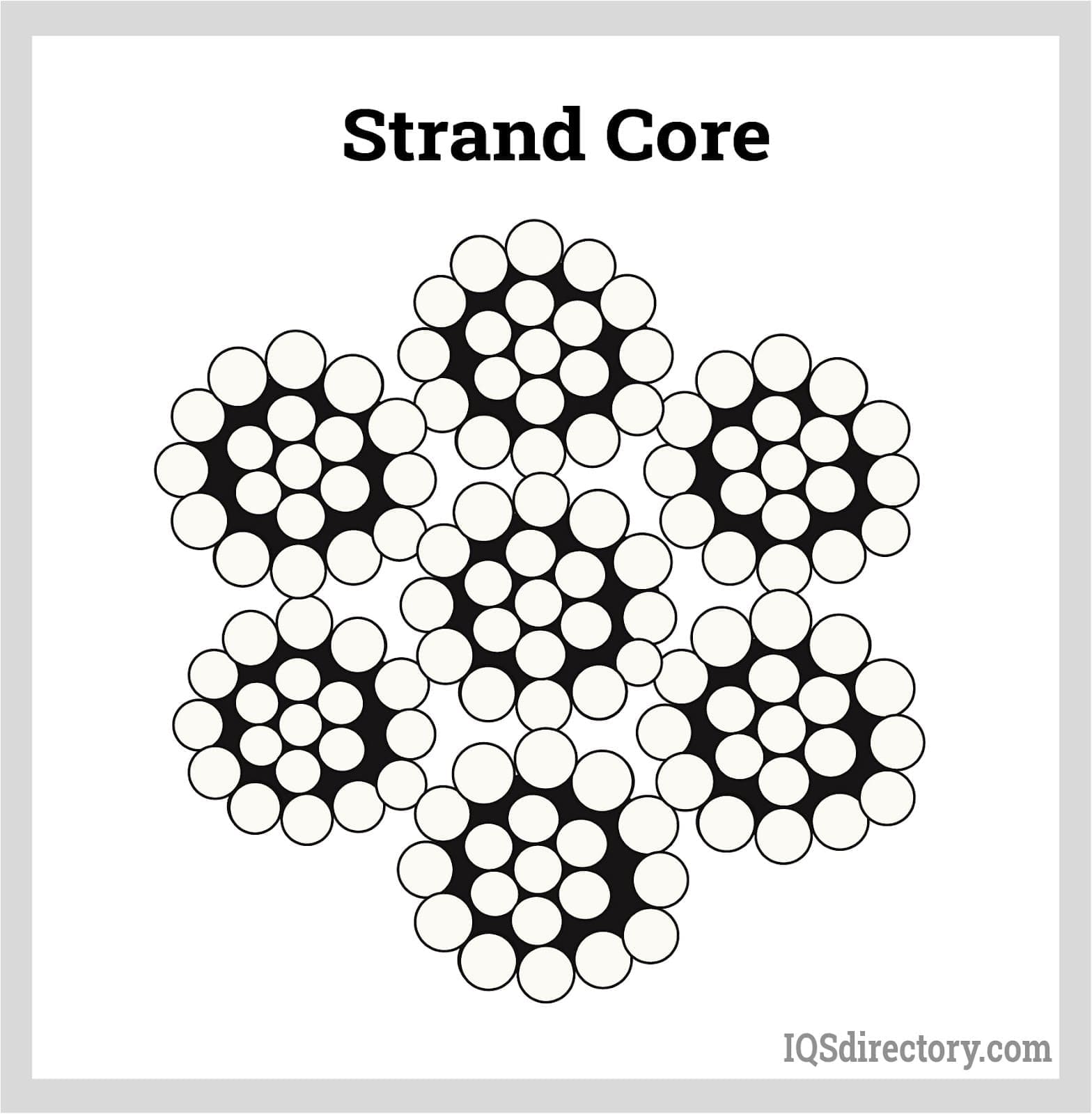
A wire strand core, is like the rest of the strands with wires of the same diameter as the other strands.
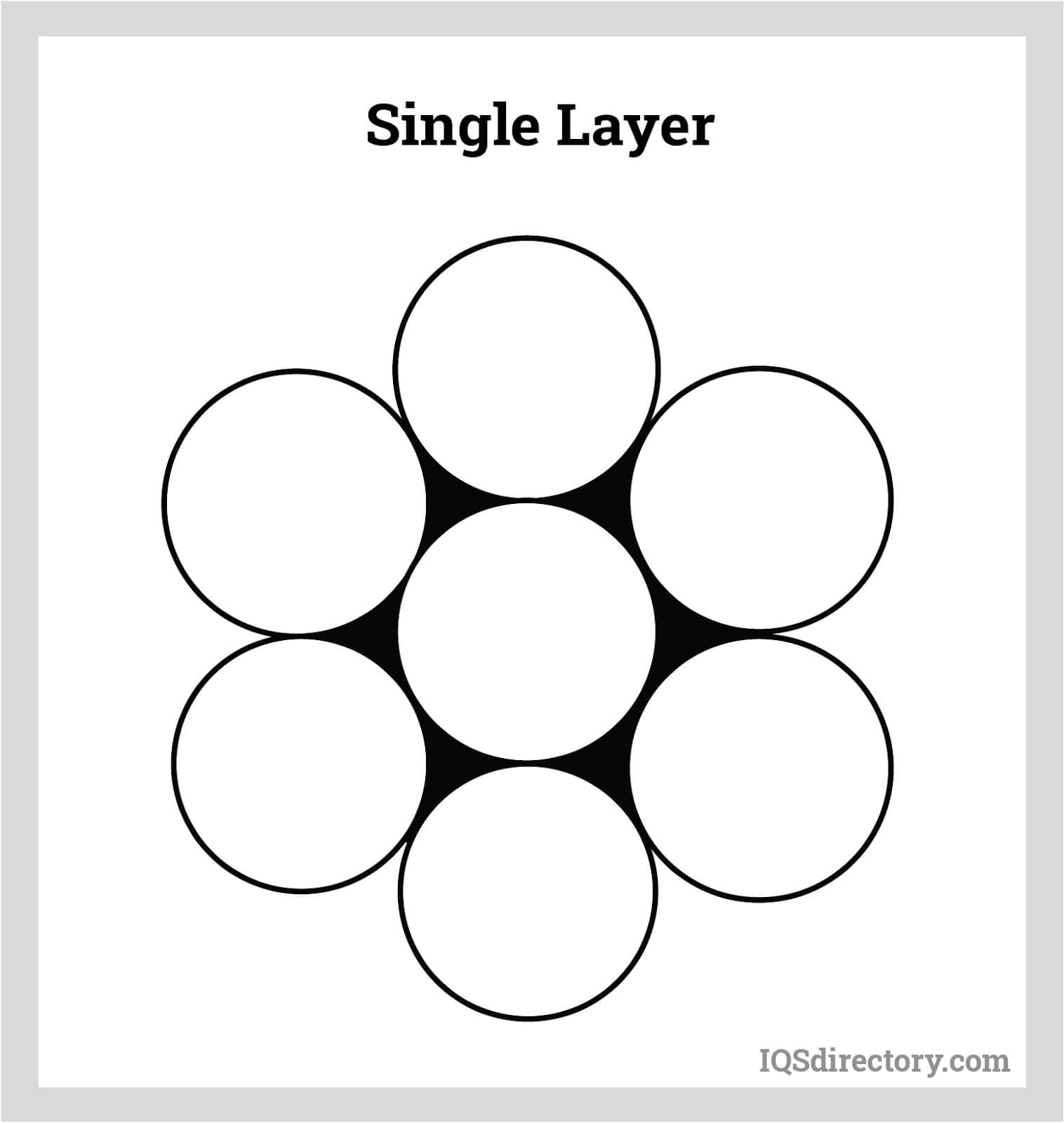
A single wire core with multiple wires wound around the circumference.
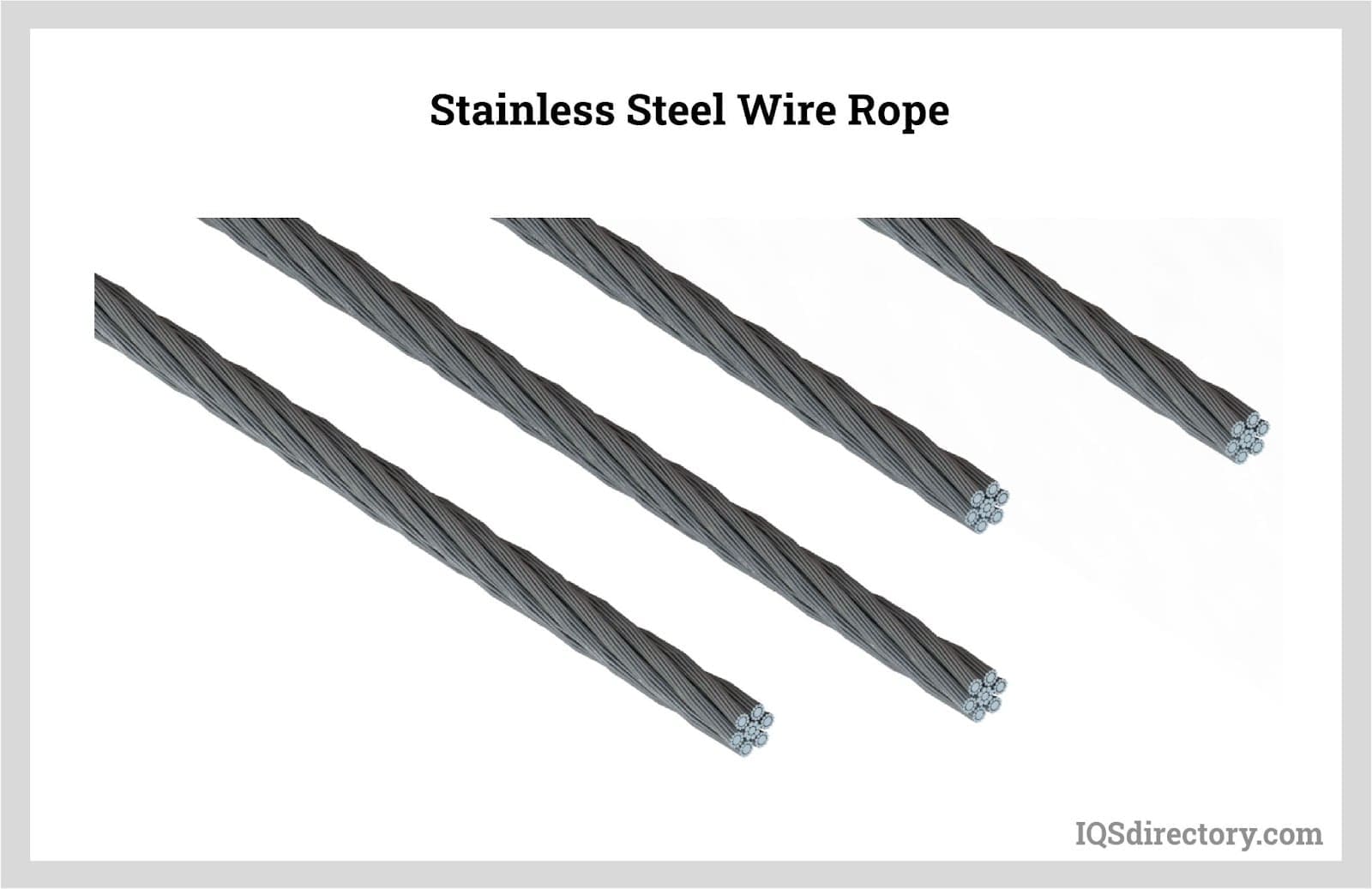
Metals used to make wire rope have a high degree of strength and resilience.
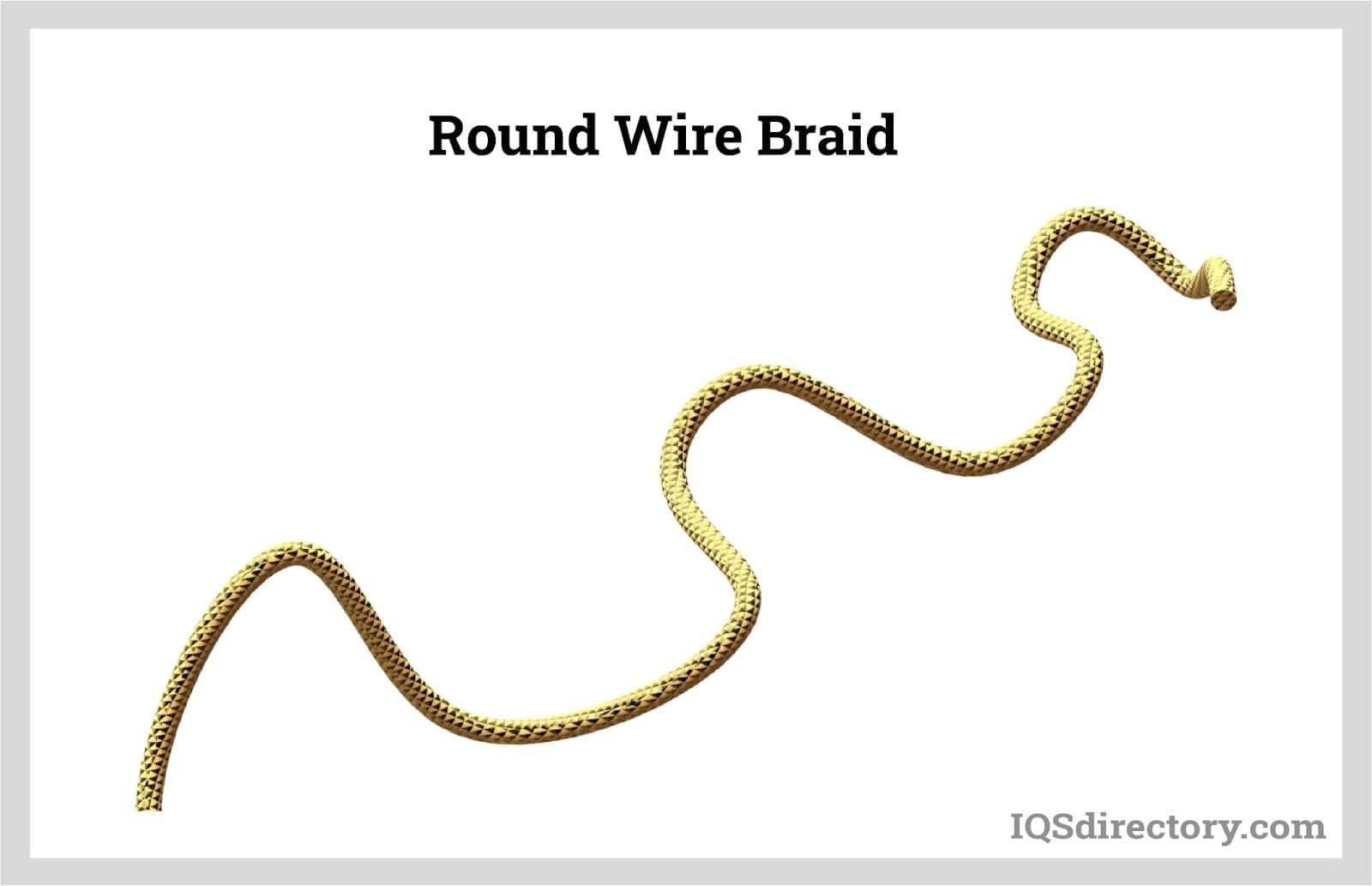
Braided wires are electrical conductors with small wires that are braided together to form a round tubular braid.
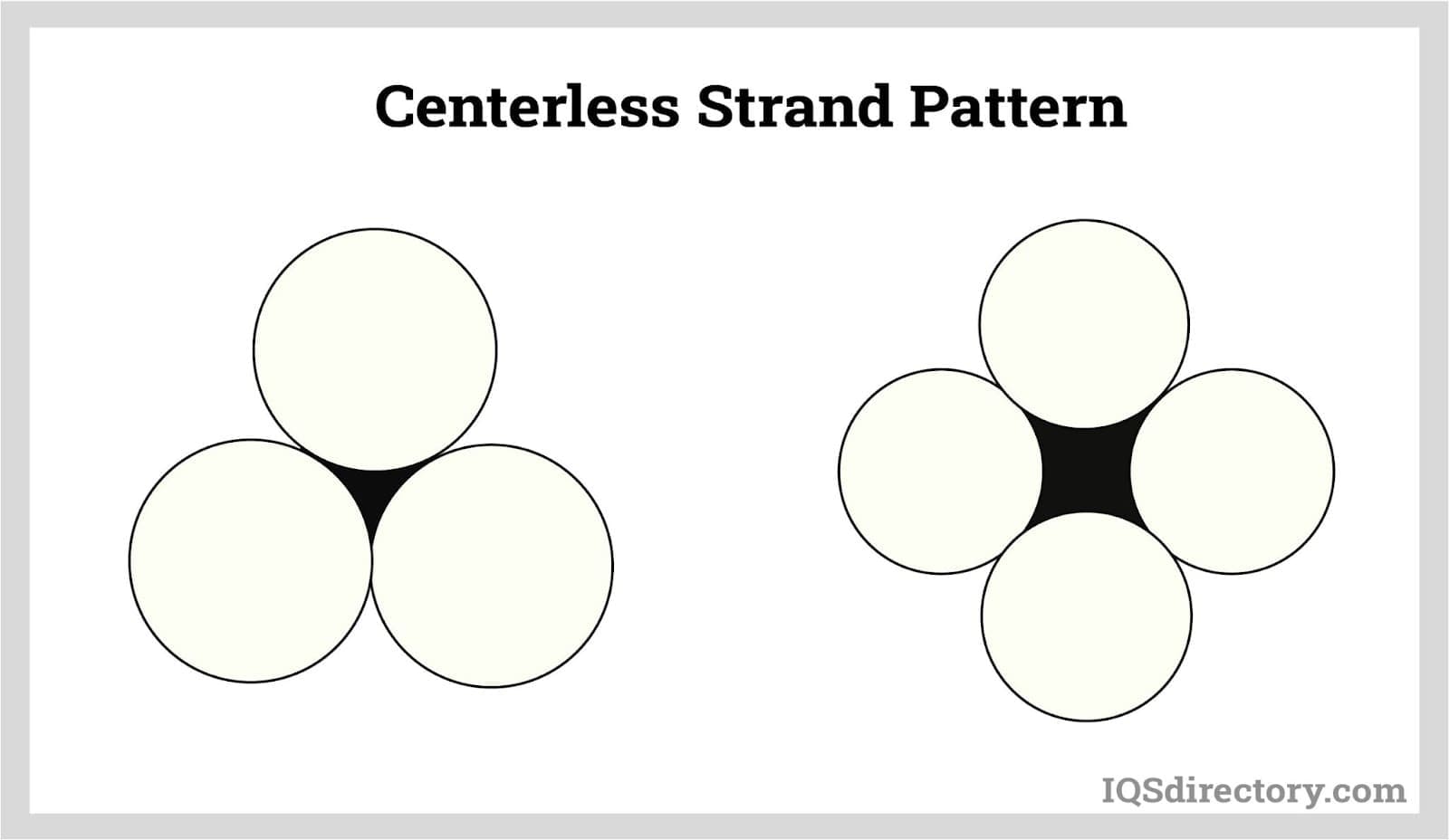
A centerless strand of wire are equal in size and are wound together in a helical shape.
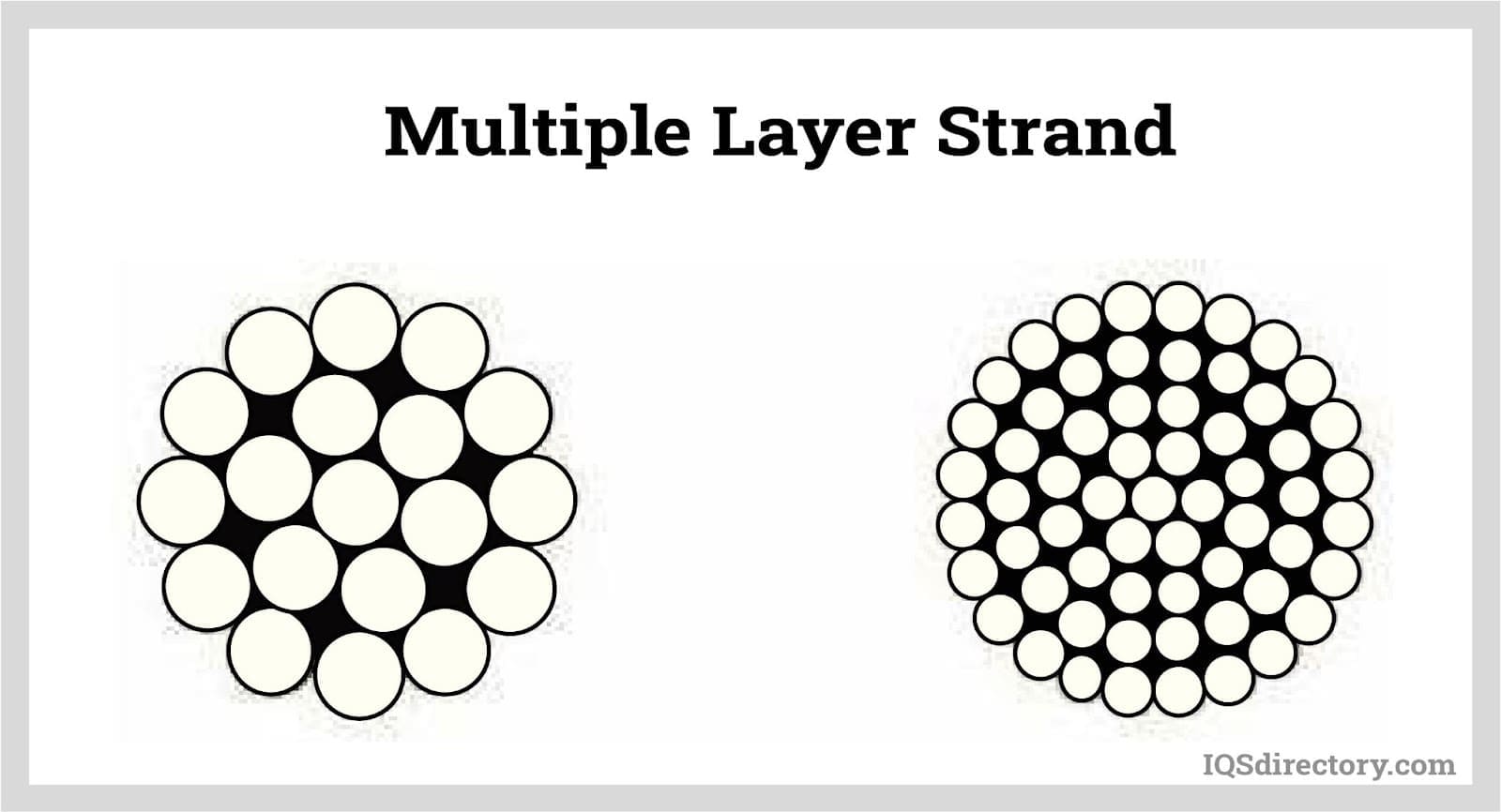
A multiple layer strand wire with wires placed over each another in successive order.
Types of Wire Rope
Wire ropes are typically identified by the number of strands and the number of wires per strand, though they may also be classified based on their lay, length, or pitch. For instance, a door-retaining lanyard wire rope is designated as 7 x 7, while wire ropes used for guying are identified as 1 x 19. Common configurations include 6 x 19, 6 x 25, 19 x 7, 7 x 7, 7 x 19, 6 x 26, and 6 x 36.
Identification codes may also include additional details, such as core type, workload limit, and other specifications. Below are specific types of wire rope cables not categorized by the standard numbering system:
Bright Wire Rope
This ungalvanized steel wire rope lacks a protective coating but may be designed to resist spinning or rotating under load. This variant is known as rotation-resistant bright wire rope.
Coiled Cable
Also referred to as coiled wire rope, this type consists of small metal wires bundled and twisted into a coil. Coiled cables offer easy storage and tidiness, eliminating the need for a spool. They automatically retract into a spring-like shape when not in use, making them highly convenient to handle.
Cable Wire Rope
A high-strength rope made by twisting individual filaments into strands, which are then helically wrapped around a core. Steel cable is one of the most common types of wire rope in this category.
Wire Rope Chain
Unlike solid wire ropes, wire rope chains consist of linked metal segments. While flexible and strong, they are more prone to mechanical failure compared to traditional wire ropes.
Push Pull Cable
Push-pull cables are specialized control cables designed for precise mechanical motion transmission in multiple directions. Their flexibility facilitates easy routing, making them popular in industrial and commercial applications.
Steel Wire Rope
Steel wire rope is made from non-alloy carbon steel, known for its high strength and stretch resistance. For added durability, manufacturers produce stainless steel and galvanized steel wire ropes, ideal for applications like rigging and hoisting.
Spiral Rope
Spiral ropes consist of curved or round strands with wires assembled in opposite directions between inner and outer layers. This design ensures pollutants, water, and moisture cannot penetrate, enhancing durability.
Stranded Rope
Stranded ropes are made by spiraling strands around a core. They come in three core types: fiber core, wire strand core, and wire rope core. These ropes feature overlapping layers for added strength and durability.
Other Categories of Wire Rope
Running Ropes
Used in systems with continuous motion, such as elevators or cable cars.
Hoist Wire Ropes
Specifically designed for lifting applications.
Stationary Ropes
Used in static applications, such as guy wires.
Track Ropes
Provide support in transport systems like aerial cableways.
Wire rope slings enhance safety and capacity in manufacturing applications. Made from improved plow steel wire ropes, they feature looped ends or terminations like hooks, chokers, or thimbles. These slings improve durability at connection points and offer superior performance in load-bearing applications.
Common Types of Slings
Permaloc Rope Sling
Permaloc rope slings are crafted using the Flemish Splice method to form the eye. These slings enhance safety by providing reverse strength, ensuring the uprightness of the eye is independent of metal or alloy sleeves. Additionally, Permaloc rope slings feature excellent abrasion resistance, making them durable and long-lasting.
Permaloc Bridle Sling
Permaloc bridle slings share many features with typical slings but offer notable advantages. They provide superior load control, resistance to wire rope crushing, and are equipped with robust hooks and links that enhance longevity and reduce maintenance requirements.
Grommets and Endless Slings
Manufacturers also offer grommets and endless slings with movable legs. These slings deliver unmatched load stability and balance, improving safety during operation.
Wire Rope Applications
Wire ropes serve a wide range of purposes, from cranes to playground swings, offering versatility across various industries. Common applications include:
- Hoisting, hauling, and rigging
- Cargo control, baling, and tie-downs
- Anchoring, mooring, and towing
- Guardrails, fencing, and cable railings
Industries utilizing wire ropes include:
- Industrial Manufacturing and Construction – for heavy machinery and infrastructure
- Marine, Gas, and Oil – for anchoring and mooring
- Mining and Transportation – for towing and rigging
- Fitness and Recreation – using plastic-coated cables for gym equipment and playgrounds
- Theater and Electronics – for stage rigging and miniature cables in communication devices
Wire Rope Materials
Wire ropes are primarily made from cold-drawn steel wire, stainless steel wire, or galvanized wire. Additional materials include aluminum, nickel alloy, bronze, copper, and titanium, though cold-drawn carbon steel wires remain the most common.
- Stainless Steel Rope and Cables – Ideal for corrosive environments.
- Galvanized Wire Rope – Known for its strength and durability, widely used in specialized applications like galvanized aircraft cables
Wire rope cores vary based on application needs:
- Metal Cores – Provide strength and durability.
- Fiber or Impregnated Fiber Cores – Offer flexibility for specific uses.
Independent Wire Rope Core (IWRC) – A core strand of wire used for added support and resilien
Standards and Specifications of Wire Rope
Wire rope standards vary depending on its application. Commonly referenced standards include those set by OSHA, ASTM International, and ISO. Depending on your industry and specific use case, additional standards may apply. To ensure compliance, consult your service provider for a comprehensive list of applicable standards.
Safety Factor for Wire Rope
The safety factor provides a margin of security against potential risks. Determining the safety factor starts with understanding the type of load the rope will bear, including shock loads and environmental factors like wind. Safety factors are expressed as ratios, such as 4:1 or 5:1. For example, a 5:1 safety factor means the wire rope’s tensile strength must be five times the expected load. In specialized applications, this ratio can increase to 10:1.
By carefully evaluating these factors, you can select a wire rope that ensures safety and longevity. For expert advice, work with a trusted supplier who prioritizes your needs and offers guidance tailored to your application.
Things to Consider When Purchasing Wire Rope
Wire ropes are critical to the safety of many operations, making it essential to evaluate their capabilities and specifications thoroughly. Key factors to consider include:
- Diameter
- Breaking strength
- Corrosion resistance
- Flattening or crushing resistance
- Bendability
- Lifespan
Ensure the chosen wire rope aligns with the specific application and operational environment. For example, environments with extreme temperatures or corrosive conditions may require specially coated ropes designed for enhanced durability.
Proper Care for Wire Rope
To maximize the lifespan and safety of your wire rope, follow these guidelines:
- Do not exceed the rope’s rated load or breaking strength.
- Inspect regularly for rust, kinks, fraying, or other signs of wear.
- Clean and lubricate the rope as needed.
- Store ropes in a dry, temperature-controlled area, and ensure they are properly coiled to prevent kinking.
By maintaining your wire ropes, you can ensure reliable performance and extend their working life.
Accessories for Wire Rope
Essential accessories for wire rope include connections, fasteners, fittings, and hardware such as wire rope clips and steel carabiners. Selecting the right accessories can further enhance the functionality and safety of your wire rope system.
Wire Rope Terms
Breaking Strength
The calculated load required to break a wire rope when subjected to tension.
Core
The central element of a wire rope around which strands are helically laid. Cores can be made from fiber (cloth), independent wire rope, or wire strands.
Drum
A flanged, cylindrical barrel, either tapered or uniform in diameter, used for winding and storing rope during operation.
Extra Improved Plow Steel
A steel grade offering superior safety features without increased diameter and exceptional resistance to abrasive wear. It is 15% stronger than Improved Plow Steel, with a tensile strength ranging from 280,000 to 340,000 psi.
Galvanize
The process of coating wire, strand, or rope with zinc to prevent corrosion.
Grade
Classification of wire ropes based on breaking strength.
Guy Line
A steel wire or strand, typically galvanized, used to brace or support structures.
Improved Plow Steel (IPS)
A high-carbon steel with a tensile strength of approximately 260,000 psi, about 15% stronger than Plow Steel. IPS is commonly used in commercial wires.
Independent Wire Rope Core (IWRC)
A wire rope used as the core for a larger rope.
Iron
A low-carbon steel wire with a tensile strength of about 10,000 psi. It is pliable and suited for applications involving repeated bending, such as tillers, guys, and sash ropes.
Lay/Laid
The helical arrangement of wires to form a rope. The "lay" refers to the direction of the helical path of the strands: right lay (right-hand twist) or left lay (left-hand twist).
Marine Rigging
Wire rope used on boats for securing masts, hoisting sails, docking, and stabilizing cargo.
Mechanical Cable Assemblies
Heavy-duty cables used in industrial equipment for pulling objects and bearing significant weight. They also serve smaller applications, such as bicycle brakes or car throttle pulleys.
Rope Grades
Classification of wire rope by breaking strength. Grades, in ascending order of strength, include Iron, Traction, Mild Plow Steel, Plow Steel, Improved Steel, and Extra Improved Steel.
Rigging Equipment
Used on sailboats for securing masts, adjusting sails, docking, and stabilizing cargo.
Sheave
A pulley wheel with a channel, mounted in a frame, to guide or change the direction of a rope or cable.
Strand
A group of wires helically wound around a core to form a symmetrical portion of a rope.
Strand Grades
Classification of strands by breaking strength, ranked as Common, Siemens Martin, High Strength, and Extra-High Strength. Utility-grade strands are available for specific applications.
Swage
The process of attaching a termination to a wire rope by deforming the termination around the rope using a hydraulic press or hammering. The resulting strength matches the wire rope's rating.
Swaged Fittings
Fittings designed to fasten wire rope ends through a cold flow process.
Traction Steel
A rope material grade with a tensile strength of 180,000 to 190,000 psi. It offers excellent bending fatigue resistance and minimal abrasive force, making it ideal for elevator applications.
Wire
A continuous span of metal drawn from a rod.
Wire Braids
Wire strands braided together to form a flexible structure. Unlike stranded wire, the strands in braids are intertwined rather than bundled.
Wire Rope Fittings
Components that secure spliced or swaged rope ends in assemblies, preventing unraveling and enhancing connection versatility.
Wire Rope Cable Assemblies
Metallic ropes made of twisted, spiraled, or bonded wires. While "wire rope" and "cable" are often used interchangeably, cables typically refer to smaller-diameter ropes (less than 3/8 inch), used for lighter-duty applications.
Wire Rope Lanyards
Cable assemblies made of spiraled wire bundles, used to support hanging objects, connect items, pull or lift loads, and secure equipment.
Wire Rope Wholesalers
Suppliers offering a wide range of wire ropes and accessories at affordable rates and in bulk. Accessories include swivel eye pulleys, eye nuts, eye bolts, hooks, shackle pins, turnbuckles, and more, enhancing the rope's functionality and preventing fraying.
More Wire Rope Information